Getting Started
Most of the time, the pressurized gas used in pneumatics is simply air, which could be dry or could be lubricated. They work on end effectors which could be something such as a common cylinder, which is generally one of the first things people think about when it comes to pneumatics. However, it could also be something a bit more complex and specific to different types of applications. For example, it could be air springs, vacuum systems, grippers, and more.
One of the biggest uses of pneumatics is for the absorption of shock. This is partially because air is easy to compress and it can work well within a pneumatic system to absorb shock. Most of the time, the pneumatic systems are operating with a pressure around 100 psi, which is generally quite small, but works well for the various applications and tools that utilize it. Hydraulic systems are quite a bit more robust and operate at a much higher psi.
What is the Physical Concept of Pneumatics?
Most of the pneumatic systems use air compressors to help them reduce the air volume. While they reduce the volume, it is simultaneously increasing the pressure of the gas. The gas then travels through pneumatic hoses. You control the flow of the air on the way through the hoses and to the actuators via valves. It is important to have a system that can monitor and filter the air regularly in order to ensure proper operation and efficiency. This also helps to provide a longer life for the machine.
Over the past few years, the control that users have over pneumatic systems has become far better than it once was. The advancement of technology and the coupling of better components, better tools, and electronics with the pneumatic systems have helped with this. Pneumatic systems and tools today are actually comparable to many high-end electronic automation synn stems.
What is Pneumatics Used for?
Pneumatics is useful for many different fields today, and you can find pneumatic devices nearly everywhere. The technology is useful in the fields of material handling, robotics, medical science, entertainment, and much more. Pneumatic tubes can carry items long distances. Air brakes on buses and trucks, exercise machines, pressure regulators and sensors, pipe organs, chairs, vacuum pumps, pneumatic tires, power tools, and more use some form of pneumatics today.
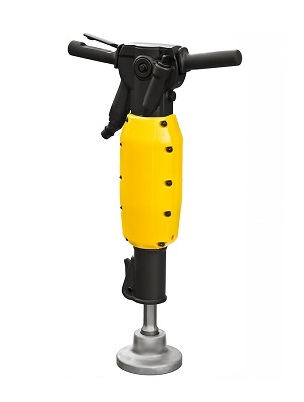

What is Hydraulics?
Hydraulics is an area of engineering that deals with liquids, and how to use liquids in order to create mechanical actions of some sort. Many people consider hydraulics to be a liquid form of pneumatics, but it is a bit more complicated than that. The engineering and science of hydraulics can be very complicated, as the properties of fluids are far different from the properties of a gas, such as air. Hydraulics utilizes far more psi, between 3,000 and 5,000 psi, typically. As mentioned, pneumatics only uses a fraction of this amount of psi. Even though it is a bit different from pneumatics, the concept is still relatively simply to grasp.
What is the Physical Concept of Hydraulics?
The concept behind hydraulics is that when applying force to one area, that force will transfer to another area via an incompressible fluid. One of the misconceptions some people have about hydraulics is that water and hydraulic fluid is the same thing, but the fluid is generally some sort of oil. The pressure added to Point A, and then an action or movement will occur at Point B.
With hydraulics, it is possible, and common, to utilize force multiplication. This simply means that the small amount of force you use at Point A is multiplied and is much greater by the time it reaches Point B. One of the ways this is possible is by trading force for distance.
Today, you will find hydraulics in use with many different types of machinery and systems. They are used in auto assembly lines, large machines and construction equipment, elevators, hoists, machine tools, flight simulators, amusement park rides and much more. Some theatrical stages even utilize hydraulics to raise or lower parts of the stage. Hydraulics is also a part of motor vehicles. Find it in the power steering, brake lines, and automatic transmissions. Hydraulic systems are a part of nearly every industry in some capacity or another today.
Comparison of Pneumatics and Hydraulics
Some people think these two things are synonymous with one another, but by now, it is easy to see that they are quite different. It is true that they utilize the same basic technique in order to manipulate some type of mechanical movement. They use the same type of actuators cylinders for linear force and motors for rotational force. However, the real difference comes from the type of medium they use to create that movement.
Pneumatics utilizes air, which is compressible. Hydraulics uses oil, which is not compressible, at least not as readily. Air can change consistency too, but fluids maintain their consistency. Pneumatics is generally faster as well. However, the upper limit for pneumatics is 150 psi, so they are not able to move the huge loads that hydraulics is capable of moving. At the upper end of the hydraulics spectrum, it is possible to utilize up to 10,000 psi.
One of the other major differences is in the area of cost. Pneumatic systems tend to be substantially cheaper than hydraulic systems are. It is easy to see just how many differences these different systems have. Even though there may be some overlap in the types of work that they do, as well as the things they can accomplish, each has different specialties. One is generally better suited to certain types of tasks than the other one will be.
What Are the Various Types of Hydraulics and Pneumatics?
- Electric Actuators: an electric actuator is an electrical machine capable of converting electrical energy into mechanical energy. People typically call this a motor. Other types of actuators include pneumatic actuators and hydraulic pistons.
- Hydraulic and Pneumatic Tools: many different sorts of pneumatic and hydraulic tools are on the market today, including jackhammers, sandblasters, airbrushes, air ratchets, drills, and nail guns. Hydraulic pumps and other devices are available too.
- Hydraulic Adaptors, Fittings and Couplings: a number of different types of hydraulic couplings, fittings, and adaptors are available for hydraulic systems, including quick connect and quick release devices. Some of the options include flaring tools, bite rings, blanking caps and plugs, compression tube fittings, and threaded adaptors.
- Hydraulic Cylinders, Pumps and Power Units: you can find portable and fixed hydraulic cylinders and pumps, as well as pump flanges, gear pumps, and even seal kits for fixes. Replace the elements in the hydraulic system as needed, but make sure all of the parts and pieces work together before making a purchase.
- Hydraulic Fluids and Filtration: many different types of hydraulic filters and fluids are available for hydraulic systems. High quality fluid will ensure the system functions properly and you have enough power. The filtration devices will help to ensure there is no grit, grime, or dirt that makes its way into the system and the fluid. It is important to take proper care of the system, and watching the filtration and fluids is the first step.
- Hydraulic Instrumentation and Switches: the instrumentation and switches available for your hydraulic system can cover a variety of different needs. Hydraulic instrumentation and switches offer diagnostic testers, pressure kits, and monitors. Some of the options include circulation sights, flow meters, pressure sensors, and digital hydraulic pressure switches. They can help you to gain more control and understanding with your system.
- Hydraulic Tubing and Hose: the tubing and hoses for the hydraulic system are very important, and they need to be high quality. Hydraulic hoses and tubes come in a wide range of different sizes, styles, and colors. Because of the different types of hydraulic systems and their various uses, a variety of hoses and tubing are available. Always make sure the tubes and hoses you use are right for your particular system and needs.
- Hydraulic Valves and Manifolds: the hydraulic valves allow you to control the flow and pressure of the liquid as it goes through the system, and the manifolds consist of a number of valves. Changing the open and closed state of these valves will determine what is happening within the system. Always check the pressure and flow ratings for valves to make sure they will work well with the system you have.
- Pneumatic and Hydraulic Pressure Gauges: in pneumatics and hydraulics, it is often important to measure the pressure and flow readings. The only way to make this happen is with the right gauges and meters. Many different types and styles of gauges are available for these systems, and it is important to make sure to choose the gauges right for your particular type of system. Have a mounting system that works for the hydraulic and pneumatic gauges as well.
- Pneumatic Adaptors, Fittings and Couplings: these devices and items are needed to hook up the hoses to the pneumatic air system. The fittings and couplings can help to attach the air hoses. They come in various sizes, so getting items that fit is important. In addition, pneumatic adaptors can help to make changes to the pneumatic system without needing to use an entirely different system.
- Pneumatic Air Compressors, Boosters and Vacuum Pumps: the air compressor is the main unit, the heart of the pneumatic system. This device is what will compress the air, which you can then use to create some type of mechanical action. The booster can amplify the amount of pressure directly on the application, which can provide an increase in power. One of the common uses for vacuum pumps is to eliminate moisture from lines and even air conditioning systems.
- Pneumatic Air Preparation: to maintain the system in good working order, it is important to ensure proper air preparation regularly. Regulators and filters can help to ensure clean air is passing through the tubing and the hoses, and the filters can ensure grit and debris do not foul up the system. These devices come in different sizes, so it is important to make sure they work with the fitting and the hoses in use with the system.
- Pneumatic Counters, Logic Controllers and Timers: these devices can add a number of features and options to the pneumatic system. The pneumatic counters, for example, can count a pulse of compressed air. Some reset automatically and others will require a manual reset. These counters will generally have between two and eight digits. The logic controllers are able to control many different types of industrial processes. A pneumatic timer will create time delays by controlling how quickly air passes through the system.
- Pneumatic Cylinders and Actuators: the pneumatic cylinders and actuators are the part of the pneumatic system that moves and manipulates the mechanical motion. In fact, the actuator will generally consist of a cylinder. Some of the common types of pneumatic actuators include grippers, tie rod cylinders, vacuum generators, and rotary actuators.
- Pneumatic Instrumentation and Switches: a number of different types of pneumatic instrumentation and switches are available, including air switches and pressure sensor controllers. These devices are important for controlling the pneumatic system, especially complex systems.
- Pneumatic Tubing and Air Hose: pneumatic tubing and air hoses are available in a number of different types of material, including nylon, polyurethane, bonded polyurethane, and PTFE. They are available in straight versions as well as coiled versions. You can find the tubing and hoses in different sizes, colors, flexibility, and strength.
- Pneumatic Valves and Manifolds: the pneumatic valves and manifolds are the means by which one can control the flow of air through a pneumatic system. Some valves and manifolds may be able to handle more pressure than others will, so it is important to check the ratings and the max flow and pressure they can handle.
Product spotlights
Motion Sensor
An electronic device capable of converting the movements it senses into electrical signals.
Rocker Switch
One of the most common method of using a rocker switch is on a light switch, but they are in quite a few other devices and applications as well including surge protectors and appliances.
Strain Gauge
Stretching a strip of conductive metal will not only make it longer and thinner, it will result in an increase in electrical resistance from one end of the strip to another.
Screw Extractors
Screws have significant advantages over nails in certain applications.