PLCs, HMIs & Industrial Computing
What are PLCs and how do they work?
Programmable logic controllers (PLCs) are thought of as the digital brain of automated control systems. It is a solid state device that is able to receive input signals, process, analyse and transmit output data to control a large number of devices to apply logic to tasks to ensure they perform at optimum levels.
What are HMIs?
A Human Machine Interface (HMI) allows real-time process information to be presented to a human user, to be able to control and modify the process.
What is a SCADA system?
Supervisory control and data acquisition (SCADA), is the term used to describe a full industrial control system that uses a computer system to monitor and control a process. This is where PLCs and HMIs work together. A system will usually comprise:
- A HMI - To present data to a human operator
- Supervisory (computer) system - To gather data sending commands
- Remote Terminal Units (RTUs) - To connect sensors
- PLCs - To apply logic to devices in the process
- Communication infrastructure - To provide connectivity
What industries are both HMI and PLCs used in?
All automated systems can rely on and benefit from process control devices. Some key industries they are used in are:
- Food and beverage
- Automobile
- Manufacturing
- Bottling
How do you select a PLC?
They're usually available as a fixed configuration or in modular format. The specific model required is highly dependent on the application, the software package, the environment it will be used in and networking capabilities. There are some key points to consider such as the number of input and output points. A simple rule to follow is the larger the systems, the larger the memory, programming, and communication capabilities.
Guides & Articles
%20x%2080%20(h)/plc.jpg)
PLCs Guide
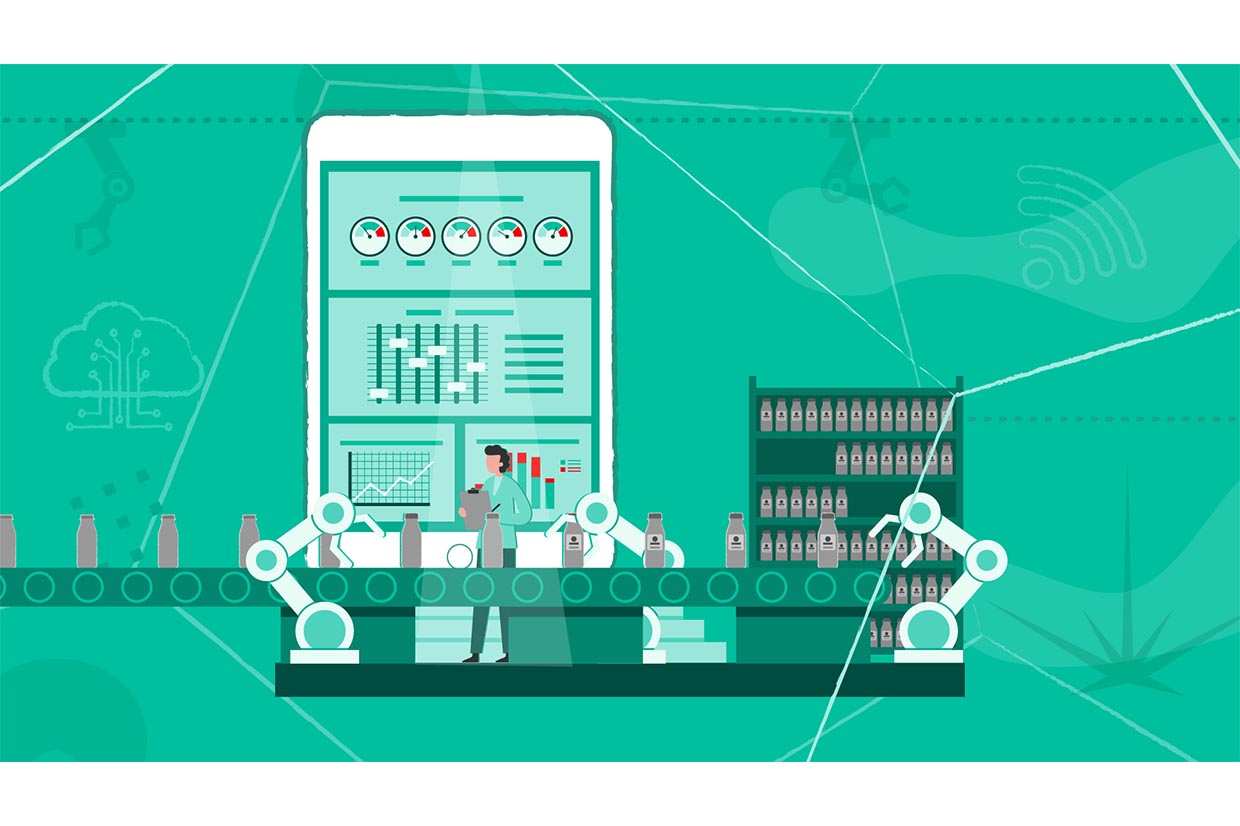
Discover with DesignSpark
Bring IoT to Legacy Industrial Technology - Part 2
Related links
- Data Acquisition
- Industrial Computers
- Data Acquisition Accessories
- Data Acquisition ICs
- Schneider Electric Twido Series Logic Module Relay Output Sink,...
- Mitsubishi FX3U Series Logic Module Relay Output Sink, Source Input
- Mitsubishi FX3U Series Logic Module Transistor Output Sink, Source Input
- Siemens Software for Use with SIMATIC HMI