- Published 16 Feb 2024
- Last Modified 16 Feb 2024
- 6 min
Industrial Equipment Lifecycle Management
Industrial equipment lifecycle management means managing the entire life of machinery from original purchase through to disposal. Read this guide to find out more.
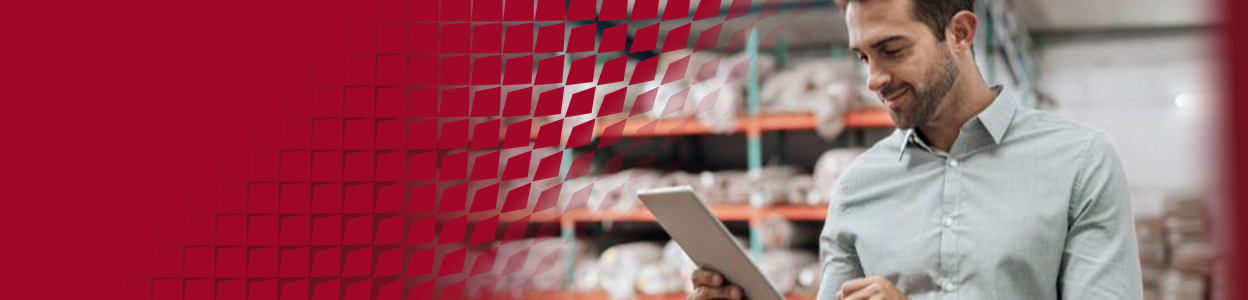
Reviewed by David Carmichael, Solution Engineer (February 2024)
Paying careful attention to each phase of the lifespan of a piece of machinery has numerous benefits in manufacturing. This guide explains how to approach each stage, from planning to purchase machinery to disposing of it at the end of its life without harming the environment.
What is Lifecycle Management?
The equipment lifecycle of industrial equipment should be managed from original purchase through to equipment end of life. Managing the equipment lifecycle starts with developing a plan to acquire industrial equipment and continues through its usage, industrial maintenance, and eventual disposal.
As well as enabling a manufacturer to be more sustainable, effective management of industrial equipment – which can be very expensive – also helps contribute to long-term growth and profitability.
Industrial Equipment Lifecycle
It’s helpful to break the equipment lifecycle down into four phases.
The first and second phases are planning to buy and procuring the new machinery. Correct planning considers what the manufacturer is hoping to achieve and how buying new industrial equipment fits into the business strategy. In the procurement phase, it’s necessary to budget for the equipment and determine the most cost-effective way of acquiring it.
The third phase sees the equipment used for manufacturing and maintained. Industrial maintenance can be reactive, preventative, or predictive, and should aim to minimise machinery downtime and extend the life of the asset. Running machinery efficiently in the production phase can make a significant difference to the overall sustainability of the operation – by reducing energy usage, for example.
The final phase of the equipment lifecycle is the disposal of the asset once it has reached the end of its useful life. At this point, it’s incumbent on the manufacturer to dispose of equipment according to environmental and health and safety regulations.
Planning to Buy Industrial Equipment
In the planning and procurement phases of purchasing industrial equipment, it’s important to start by thinking about the equipment you already have and how the new purchase will improve efficiency or be otherwise essential. You need to determine whether the capital investment will generate a good return. It’s also important to bear in mind the time it will take to obtain new manufacturing equipment – which can be months after placing the order.
It's important to consider any other costs. For example, do your employees need training in using the new equipment? If you are taking out a loan, what is the cost of the interest? What is the cost of industrial maintenance likely to be? Would a used option provide a greater ROI?
You also need to consider the physical footprint of the new equipment and whether you have enough space to site it.
Purchasing Industrial Equipment
When purchasing industrial equipment, look for a reliable and well-established supplier. The equipment manufacturer should take the time to understand your needs and have experience providing equipment to your sector. Bigger companies may have more prominent marketing, but are there less well-known options that provide a better deal? It’s vital you do your research.
Take the opportunity to visit the manufacturer and test the equipment before you buy. When negotiating contracts, work out an arrangement that is mutually beneficial and that considers agreement on delivery dates and times, compensation if something goes wrong, and any other obligations and risks.
Maintaining Industrial Equipment
The most basic form of industrial maintenance is running equipment until it fails, sometimes known as reactive maintenance, or a ‘fix on fail’ approach. While this might make financial sense for certain low-value assets that aren’t critical to the business, many manufacturers instead adopt a preventative or predictive approach for all their industrial equipment. Preventative maintenance focuses on maintaining equipment according to a strict schedule to try and prevent problems occurring and costly machinery downtime. This schedule may be determined by the manufacturer of the equipment.
Manufacturing companies are also increasingly using predictive maintenance, in which networks of sensors on machinery relay its condition to the engineer, making it possible to determine when machinery is in danger of developing a fault or failing altogether. The Industrial Internet of Things, AI, and machine learning are used to analyse data and predict failure before it happens.
Precision maintenance goes a step further by working maintenance into a detailed system of all staff continually using set, planned techniques for operating, monitoring, cleaning, and maintaining a given machine, and documenting all this.
Maintenance Technologies
Key maintenance technologies include:
- CMMS: Computerised maintenance management systems function as repositories of data and documentation, and they allow companies to automate common maintenance activities. A CMMS helps create preventative schedules, manage parts, spares and inventory, generate work orders, and assign personnel
- Thermography: Thermography reveals temperature variations that may indicate overheating and electrical faults, or insulation problems. That makes thermography particularly well-suited for the maintenance of electrical systems and motors
- Condition monitoring / vibration monitoring: Condition-monitoring sensors – vibration monitoring is commonly used – enable predictive maintenance by relaying anomalies in machine performance that may indicate a fault
- Non-destructive testing: Non-destructive testing detects faults without damaging equipment. NDT methods include ultrasonic (acoustic) testing, X-ray inspection, and magnetic particle testing. Pipelines and storage tanks are often inspected using NDT to identify structural problems, fatigue, and corrosion
- Oil analysis: Oil analysis monitors lubricants and is used to detect problems such as wear of bearings or gears. Oil analysis takes samples of oil and analyses them for viscosity, acidity, and tiny particles of metal. Oil analysis optimises maintenance schedules and can reduce costs by identifying equipment that requires changes to lubricant
Equipment End of Life
At the end of the machinery’s useful life, it is removed from service. It may be reconditioned, sold at auction, or recycled, but should be disposed of responsibly in all cases.
End of Life Regulations
Responsible lifecycle management means disposing of a production asset correctly. Commercial waste regulations dictate that any waste that comes from industry must be reused, recycled, or otherwise recovered as far as possible. There are also regulations that impact particular types of equipment. For example, the Waste Electrical and Electronic Equipment (WEEE) regulations help make certain that electrical and electronic equipment is recycled responsibly. The end-user has ultimate responsibility for this.
The Environment
The volume of waste generated by industry is a major burden on the environment. Waste from electrical and electronic equipment in particular is a growing problem. Poor management of waste from machinery can cause air, water, or soil pollution and add to the strain posed by landfills. The best way to avoid these outcomes is to minimise waste from end-of-life equipment in the first instance.
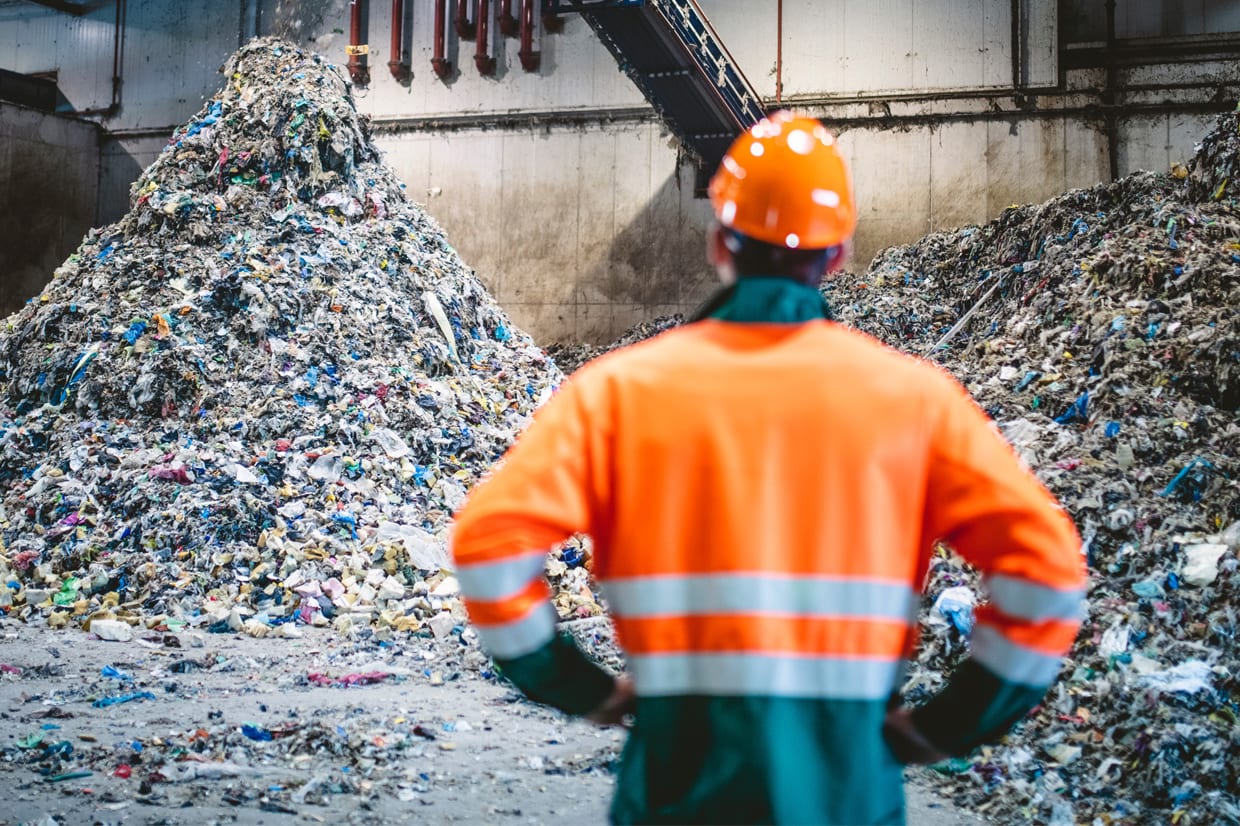
Lifecycle Optimisation
To sum up, product lifecycle management for Industrial equipment is essential to manufacturing. Lifecycle optimisation means consideration of all aspects of buying, using, and maintaining equipment, maintenance best practice, and careful disposal of machinery. Doing so enhances a business’ efficiency and profitability while cutting down on unwanted downtime and maximising asset life.
Not only that, get equipment lifecycle management right, and you’ll be helping avoid contaminating the environment.
Want more information? Learn more about optimising machinery lifespan.
Related Articles
Related links
- Remote Maintenance Advantages and Considerations
- A Guide to ESD Testing
- RS helps ACCIONA to digitise its management processes
- Banner, PSW Series Standard Power Supply for Use with Electrical and Industrial Equipment
- MikroElektronika Single Wire CAN Click NCV7356D1R2G Sensor Add-On Board for Industrial Equipment MIKROE-4225
- Banner 3m Cable Length for Use with industrial equipment, RoHS Compliant Standard
- Digital Twins and Maintenance
- Digital Transformation in Industrial Maintenance