- Published 25 Sept 2023
- Last Modified 18 Apr 2024
- 8 min
Proactive Maintenance to Optimise Machinery Lifespan
Proactive maintenance has the potential to extend manufacturing equipment lifespan while cutting costs and improving productivity. It will also help you keep your employees safe. Read on to learn more about the proactive maintenance meaning and approach, and the benefits of preventative and predictive maintenance types for your business.
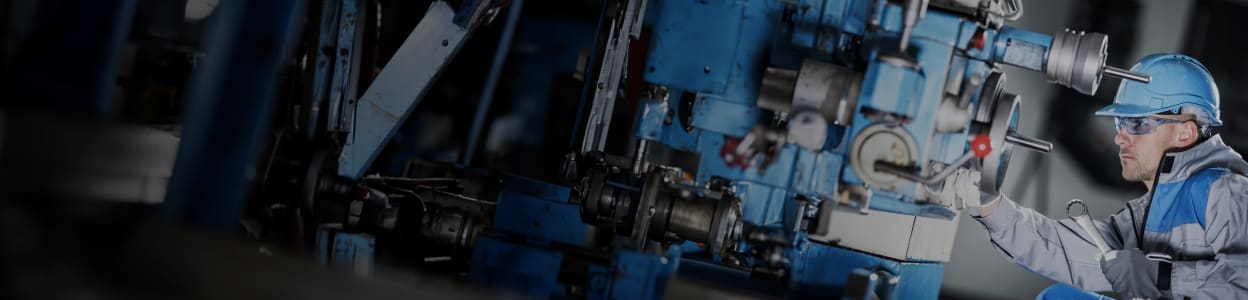
Simply put, proactive maintenance is a strategy for maintaining equipment that fixes problems before they become issues that result in the scenarios manufacturers don’t want: machinery breakdown, unplanned maintenance, equipment downtime, increased cost, and lost productivity. An example of proactive maintenance is regularly lubricating a machine or checking pipework for signs of corrosion.
One of the most important examples of proactive maintenance is predictive maintenance, which uses a network of condition monitoring sensors and sometimes AI or machine learning to predict machinery failure before it happens. This enables engineers to carry out planned maintenance works before a fault becomes critical and causes the breakdown of the machine. Predictive maintenance is thus a means of providing an early warning system about faults. Preventative maintenance is a more traditional approach to proactive maintenance, whereby machinery is maintained according to a strict schedule which may be determined by its manufacturer, or by the level of usage of the machine.
The most futuristic proactive maintenance approach is prescriptive maintenance, in which a machine uses sensors and analytics to diagnose faults itself and give engineers plans on how to deal with any problems.
So you’ll see that the reactive and proactive maintenance approaches are very different types of maintenance: the latter means waiting for machinery to fail – and then having to fix it. That not only entails the cost of repair, but can also disrupt production, putting further pressure on finances. In this guide, we explain how a proactive maintenance approach works, look at some of the technology involved, and discuss the difference between predictive and preventative maintenance. Let’s get started.
What is Proactive Maintenance?
If you’re using a proactive maintenance strategy, you maintain equipment to a schedule and look for the underlying causes of problems, fixing them before they become an issue. Proactive maintenance is often used interchangeably with ‘preventative maintenance’ but it also encompasses ‘predictive maintenance’ (condition monitoring – learn more about it here). Preventative maintenance may include regularly lubricating parts of a machine to reduce friction or regularly cleaning surfaces. Predictive maintenance might see a network of sensors installed on a machine to collect data on vibration and detect any underlying anomalies that indicate a fault is developing, Engineers will then use this information to carry out planned maintenance.
Advantages of Proactive Maintenance
There are a number of benefits to proactive maintenance, ranging from improved safety to extending the lifespan of machinery. Advantages of a proactive approach include:
- Reduced downtime. For manufacturers, time when equipment can’t be used translates into higher costs and diminished productivity. A proactive maintenance approach minimises breakdown. Proactive maintenance focuses on maintaining equipment at regular intervals or continuously monitoring its condition to minimise downtime (downtime usually means unplanned maintenance is needed). According to a report from Deloitte, unplanned maintenance costs manufacturers $50 billion each year; poor maintenance regimes can reduce a plant’s productivity by up to 20%.
- Improved safety. A very important aspect of proactive maintenance is a safer working environment. Ernst & Young says that up to a third of deaths in manufacturing environments are related to carrying out maintenance (injuries are caused by moving parts, burns, or shocks, for example). Keeping equipment in optimum condition minimises the need for maintenance interventions and therefore reduces hazards to employees.
- Minimised repair costs. It may seem the upfront investment in predictive maintenance technology is daunting. But the financial costs of not investing in maintenance can be much greater, including reduced profit margins and increased operational expenditure. Costs could come in the form of replacement components, or labour costs when technicians are called in. Some studies estimate, by contrast, that investment in a predictive maintenance regime can generate investments of 10 times the initial cost.
- Improved equipment availability and longevity. Proactive maintenance means machinery is available for more of the time, boosting the productivity of manufacturing facilities. And because machinery is well-maintained, its life is maximised. That means capital investment in new equipment may not be needed until much further down the line.
Preventative Maintenance
Reactive maintenance may be unavoidable occasionally, but preventing problems from occurring in the first place is ideal.
Preventative maintenance is by definition regular. It’s maintenance that aims to keep equipment in top condition by scheduling work. The schedule is often determined by the machinery manufacturer. Preventative maintenance may also encompass maintenance of the facility in which the equipment is located (including heating, ventilation and air conditioning systems and lighting, for example). It’s important to set up the right type of work patterns in the schedule. For example, you would want to schedule maintenance for times when machinery is not in action. This is far more efficient than shutting equipment down for the sole purpose of maintenance. You will also want to save time by managing the number and duration of site visits by technicians carefully.
Benefits of preventative maintenance, as with other forms of maintenance regime, include increased machinery uptime, extended life of assets, improved productivity, and reduced cost. Preventative maintenance actions are usually based on time elapsed or level of equipment usage. Some machines will need more frequent preventative maintenance interventions than others.
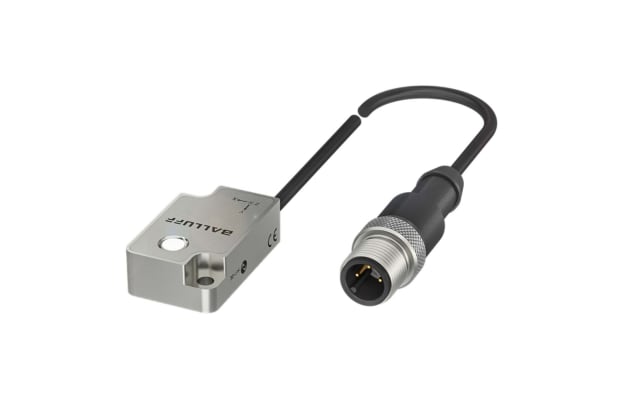
Predictive Maintenance
Predictive maintenance has grown in popularity in recent years and is now widely used throughout the manufacturing industry. It is a high-tech maintenance solution that employs technologies including vibration analysis, thermography, ultrasonics, oil and infrared analysis, and motor circuit analysis.
Predictive maintenance monitors the condition of a machine in real time and provides feedback to the engineer indicating whether a problem is developing. For example, ultrasonic technology can detect leaks in HVAC equipment and problems with machinery lubrication. Vibration monitoring picks up anomalies in vibration speeds and frequency to indicate problems with motors, bearings, gearboxes and motors. Oil analysis can reveal problems with machinery thanks to the detection of metal particles in the oil. Ultimately, the aim of predictive maintenance is always to detect potential problems and fix them before they become bigger.
Benefits of predictive maintenance include reducing the cost and frequency of asset failure. Machinery will enjoy more uptime and less downtime, which in turn raises productivity and boosts profitability. The in-depth assessment of assets under predictive maintenance also helps to prioritise maintenance activities and intervene where it is necessary. Machinery longevity can also be increased. When it does come time to replace a machine, the replacement process is often more efficient when predictive maintenance is being used.
Computerised Maintenance Management Systems
A computerised maintenance management system (CMMS) is essentially a database that contains all the information about the manufacturer’s maintenance activities. It removes the need to use spreadsheets or even paper-based systems to log maintenance. The CMMS helps schedule maintenance, raise and track maintenance work orders (where a job is defined, prioritised and a technician is allocated to the task), manage inventory and facilitate predictive maintenance by collecting and analysing data.
The CMMS will include a register of assets. Information on the asset register includes items such as manufacturer, model and serial number. The register will also contain information about the location and type of equipment. Any performance data will be recorded, along with documentation, instruction and repair manuals, safety information, and warranties. With predictive maintenance in mind, the CMMS can also provide information on the connectivity of machinery to the Industrial Internet of Things.
How Does Proactive Maintenance Work?
If you’re implementing proactive maintenance you need to start with listing assets that need to be maintained (and those assets that are defined as critical to business function). Also ask whether current maintenance procedures are working, and where they might be improved. If there are gaps in maintenance, identify them. Is your approach too reactive? Then consider types of maintenance strategies. Would preventative maintenance or predictive maintenance better serve your needs? Or a mixture of both?
People are often resistant to change, which means it’s important to lead from the front when it comes to any cultural or technological changes to maintenance. A project leader with extensive maintenance experience should oversee implementation and assist technicians with adopting new processes, and any other changes. For example, a 5S approach to maintenance requires that shopfloor operatives take ownership of maintenance of their equipment. If you have CMMS software, it can be used to identify any new maintenance tasks and their duration.
Optimising Machine Life
One of the benefits of introducing proactive maintenance is that machine life is extended (along with all the other advantages in terms of productivity, safety, and cost savings). For example, McKinsey & Company has found that predictive maintenance has the potential to extend asset life by up to 40%. Don’t forget that predictive maintenance and condition monitoring allow you to detect faults that could otherwise become much more serious.
You can even benefit the planet with proactive maintenance. A good maintenance regime not only optimises machine life, it also helps the environment: keeping equipment in good condition means it will use less energy.
Did you know RS stocks a wide range of lubricants? Explore our range of greases here.