- Published 18 Sept 2023
- Last Modified 17 Oct 2023
- 7 min
Guide to Industrial Maintenance Tools
Maintenance tools come in all shapes and sizes, from screwdrivers to sophisticated predictive maintenance tools that plan and schedule maintenance, using sensors to predict failure before it happens. Read on to find out which tool to use for the job – and how to keep your engineers and technicians safe while they’re working.
Maintenance of industrial facilities is crucial for reducing machinery breakdowns, preventing costly downtime and lost productivity, and making a plant more reliable. Maintenance relies on a wide range of industrial tools and techniques, from the hand tools we’re all familiar with to advanced thermography and condition monitoring technologies. Safety is critical at all times. It’s vital that technicians and engineers are able to carry out repairs and modifications to machinery efficiently and with minimal risk.
There are several approaches to industrial maintenance. From reactive – where engineers respond to machinery breaking down – to preventative, in which maintenance is regularly scheduled to prevent breakdown by using preventive maintenance tools. To predictive maintenance, where machinery is continuously monitored and failures even forecasted in advance. It’s the latter that relies on some of the more sophisticated tool technologies such as ultrasonic detection and vibration monitoring.
Let’s take a closer look at some of the key technologies in the industrial tool armoury.
Hand Tools
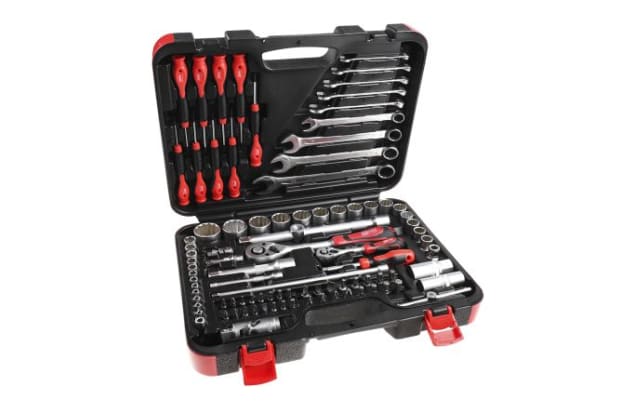
Some of the hand tools industrial maintenance engineers and technicians use are familiar from the domestic front and DIY. For example, a wide range of screwdrivers including flat, Torx and Philips types are essential. Technicians also use hammers, mallets, pliers and drills. Ratchet, socket and wrench sets are typically found in their toolboxes, along with saws.
Other hand tools industrial maintenance technicians commonly use include callipers, wire strippers, and feeler gauges, which engineers use to measure the distance between two components. Specialist hand tools for electrical engineers include multimeters and cable cutters. Engineers working with Heating, Venting, and Air Conditioning (HVAC) equipment may carry digital thermometers and specialist tools such as coil fin straighteners, which help clean and unclog air conditioning units.
All hand tools exploit ‘mechanical advantage’ – a measure of the ratio of output force to input force in a system. It is vital hand tools are used correctly and safely to prevent injury to the technician. Maintenance engineers should wear correct personal protective equipment (PPE) at all times such as gloves, safety goggles, hearing protection, and masks if needed.
Remote Inspection Tools
If machinery is dangerous or inaccessible for in-person inspection by the technician, remote visual inspection (using video, for example) can help determine if there are problems that must be addressed. Remote inspection tools include borescopes, tubes with cameras on one end and a display at the other, fibrescopes, flexible inspection tools using fibre optic technology, and videoscopes. These tools are particularly useful for assessing the health of hard-to-reach systems.
Condition Monitoring
Condition monitoring is a mainstay of predictive maintenance solutions, which assess the health of equipment in real time and attempt to diagnose failures before they happen. Condition monitoring is typically used on rotating equipment, pumps, electric motors, compressors and internal combustion engines.
Industrial Leak Detection
Industrial leak detection locates leaks in plant equipment using ultrasonic leak detectors and electronic leak detectors. But how do they work? Ultrasonic detectors detect leaks in pipes and valves using sound. They pick up high-frequency soundwaves produced by leaks in pressurised systems. An electronic leak detector, meanwhile, may detect refrigerants such as chlorine and fluorine in air. Many ultrasonic leak detectors feature LED displays to alert engineers to leaks and their seriousness. Leak detection tools such as these are used to detect leaks in pipes, compressed air and refrigeration systems, and vacuum-based systems.
Thermal Imaging Tools
If something is going wrong with a piece of machinery, its heat signature can be an early warning sign. That’s where thermal imaging tools come in. Thermal cameras detect equipment heat signatures and compare them to historical readings. Anomalies may indicate the need for further investigation by the maintenance engineer. For thermal imaging to work correctly, it’s important the system is operating at least around half of its load, and that the impact of ambient temperature and currents in the air is accounted for.
Using a CMMS
A computerised maintenance management system (CMMS) is essentially a database containing information about your machinery and all aspects of its maintenance. Central to the CMMS system is its asset register, which contains information such as equipment manufacturer, serial number, model and information about equipment performance and location, not to mention data on any Industrial Internet of Things instrumentation.
The CMMS also features a work order management system. A word order is a request for a technician to carry out a task. Work order management tracks the type of task required, when the work needs to be carried out, and where it should be performed.
The CMMS makes the maintenance technician’s job easier. It means no longer having to keep track of preventive maintenance schedules on spreadsheets or pieces of paper. Instead they can be automated in the system. The CMMS also allows resources to be allocated to a job, and helps maintenance managers prioritise which tasks are most important.
Ultimately, the CMMS system should help improve reliability and reduce downtime.
Vibration Monitoring
Vibration monitoring uses vibration sensors to detect anomalies in vibration speed, frequency and displacement which may indicate a fault is developing. Vibration analysis can be used to detect problems with a range of components, including rotors, bearings, gearboxes and motors.
Industrial Tool Training
If your engineers need to gain experience in using industrial maintenance tools, training can be beneficial. Courses available include everything from how to use hand tools to how to use a CMMS system. And a major part of investment in predictive maintenance is often training if engineers are unfamiliar with the technologies involved or used to a more traditional preventative regime.
Tool Safety
Safety is obviously paramount when it comes to carrying out maintenance. Hand tools and power tools can be hazardous if used incorrectly or if they are in poor condition. Typical health and safety risks from hand tools are blows to the hand, eye injuries from particles, and sprains.
Non-sparking hand tools may be necessary in some scenarios where there is a danger of a spark causing a fire or explosion. The correct PPE for maintenance tasks, such as safety glasses, gloves and safety boots must be used. If PPE isn’t being used, or used incorrectly, it is important that the situation is rectified immediately. Workers should also have successfully completed any tools training necessary to use tools safely.
Storing Tools
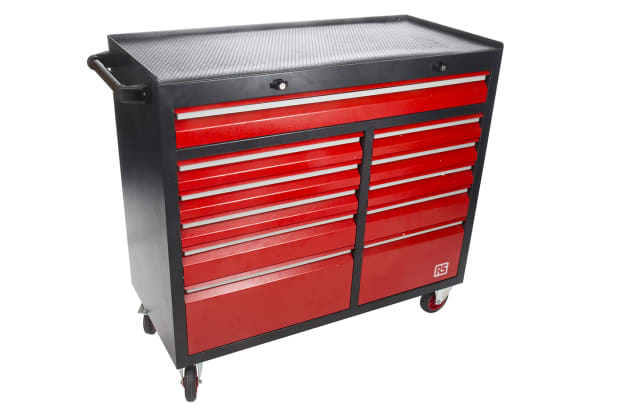
Tools that are cared for last longer and perform better. There is a wide range of tool storage solutions on the market, including boxes, chests, pouches and racks. If you’re looking for ways to store tools that protect them and keep them in top condition, RS can help.
Benefits of Choosing the Right Tools
Choosing the correct industrial maintenance tool for the job enables you to maintain equipment safely and efficiently, and makes your maintenance regime more productive, whether it’s preventative, predictive, or a mixture of both. If you’re considering which tool to use, think about the application and the outcome you want to achieve, whether it’s using hand tools for mechanical operations or the latest condition-monitoring vibration sensors to assess the condition of a machine tool. Getting the tools right benefits everyone, from the engineers using them, to the bottom line of the business when unscheduled downtime and lost productivity becomes a thing of the past.
Want to browse the latest in PPE? We’ve got you covered here.
Featured Articles
Related links
- Why are Industrial Lubricants Important?
- Augmented Reality for Maintenance
- Tool Management Strategies for Efficient Maintenance
- Maintenance and Automation
- A Complete Guide To Spanner Sets
- A Guide to Machine Safety Standards and Equipment
- Facom 96 Piece Industrial Maintenance Tools Tool Kit with Box
- What is Inventory Management?