- Published 17 Jan 2024
- Last Modified 29 Jan 2024
- 7 min
Tool Management Strategies for Efficient Maintenance
Tools are vital to maintenance but looking after those tools is an art in itself. This guide shows you how to manage, protect, store and maintain tools so they are available and up to the job in hand when it comes to maintenance. Read on to find out more about the best tool management strategies and most effective tool management systems for manufacturers.
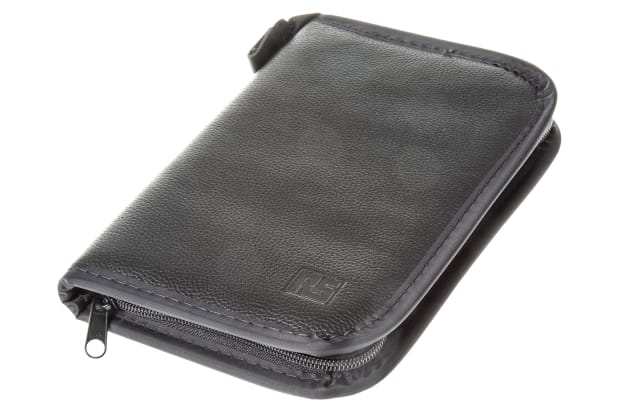
Reviewed by David Carmichael, Solution Engineer (December 2023)
A well-run plant depends on managing maintenance tools. Production efficiency and productivity rely on having the right tools available for maintenance and at the right time. That’s where an effective tool management regime comes in handy. This guide explains the benefits of tool management systems and how to calibrate, secure, store and track tools.
Benefits of Managing Tools
Managing maintenance tools effectively has a number of benefits, including boosting productivity, reducing cost, and increasing machinery uptime. Broadly, you need to know what tools you have on site, where they are, what the tool is used for when it comes to your maintenance regime, and any maintenance that the tool itself requires. A good tool management system or inventory considers all these factors to realise benefits such as reduced downtime.
Other benefits of managing maintenance tools include greater longevity of production machinery and improved tool lifespan. Electronic tool inventory control systems and tool tracking systems are capable of keeping track of maintenance tools in real-time, so engineers know where tools are located or whether they are in use. This can help make a plant much more efficient and assist technicians in carrying out maintenance.
Calibrating Tools
Accurate calibration of a tool determines its readiness for carrying out maintenance tasks. Tools work correctly when they are calibrated correctly. Some basic tools such as screwdrivers and hammers do not need calibrating, but other tools do. Equipment calibration ensures these tools are fit for purpose.
One example of a tool that needs calibration is an electrical tester or electrical metre measuring voltage. Torque wrenches and torque screwdrivers also need to be calibrated, as do measuring devices such as Vernier calipers and laser distance metres. Tools that help maintain health and safety such as gas detectors and insulation testers must of course also be calibrated and maintained correctly to ensure they work as required.
As part of tool inventory control, engineers should know which tools need to be calibrated. It’s important to maintain a list so these tools are calibrated correctly and to the required standards. For example, there are strict quality assurance standards that need to be maintained for some tools, while manufacturers of tools may specify calibration requirements.
Types of Calibration
Calibration is critical where measurement equipment is used to monitor the performance and safety of processes or machinery. Types of equipment calibration include calibrating pressure measurement tools, such as digital pressure gauges or monitors for applications where gas or hydraulic systems are used. Temperature is another variable where calibration may be required – for example, for thermal imaging equipment or tools for measuring infrared radiation.
Other instruments that measure the flow rate of liquid or gas such as flow meters also need calibration. Some hand tools such as torque wrenches need calibration to ensure they apply the torque specified by the manufacturer of machinery when technicians tighten fasteners, nuts or bolts. Electrical tools that measure voltage or current also need calibrating to ensure they are accurate.
Calibration Schedule
Equipment calibration schedules and calibration services vary depending on the type of tool, the amount it is used, the environment it’s used in, and what the manufacturer recommends. Tools that are used every day should be calibrated more frequently than tools that are seldom used. For example, a tool used every day might be calibrated every three months, and a tool only used once a year could be calibrated every three years.
Equipment calibration schedules are important parts of tool quality assurance and plant health and safety regimes. They provide engineers with peace of mind that tools are functioning as they should be, and in turn that assets are being maintained correctly.
Storing and Securing Tools
Good tool management means taking proper care of maintenance equipment and that’s where tool storage solutions come in. Storage ensures your tools are safe, secure, and ready to be used when required.
Tool Storage Solutions
Tool storage solutions come in a variety of shapes and sizes and include portable toolboxes, tool chests, tool cabinets, tool bags, and outdoor tool storage spaces. Tools should be stored in a dry and clean environment to prevent damage. That means it’s important tools are cleaned after usage for maintenance and before being stored. Tools also shouldn’t be stored on the floor. Instead, invest in shelving to accommodate the tool and keep it safe and secure.
Tools may also be stored in vending machines on the shop floor. This enables engineers to rapidly access the tools they need. These types of solutions also monitor usage and inventory levels so the optimum number and types of tools are always on hand.
Tool Security Practices
Tools are often valuable, which means tool storage solutions should be kept locked if there are concerns about theft or improper use. Some toolboxes are lockable and rugged to prevent theft of tools and feature bespoke locks and keys. If you are transporting tools, do not leave them unattended in the cab of a van, truck, or other vehicle. Lock them in the vehicle or protect them with a heavy-duty locked toolbox that cannot be moved.
Tracking Tools
Factories, warehouses, and other industrial facilities often contain hundreds or thousands of physical assets and that’s where inventory control comes in: a solution for how to keep track of tools and equipment. Tools are part of factory inventory and tool tracking can be invaluable if a maintenance engineer is trying to keep tabs on a lot of items of equipment. Tool tracking systems may be integrated with a company’s computerised maintenance management system (CMMS) and barcodes and tags can be fixed on tools so that maintenance equipment can be located easily and machinery serviced in a timely fashion. Again, this helps to boost productivity and cut downtime, reducing costs.
Tool Tracking System
Tool tracking systems typically include software that enables you to manage inventory while tracking asset location, records of tool deployment, and costs. A good tool tracking system will also allow you to record tool usage and return of the tool by a technician, provide an audit trail, and even help identify needs for future purchases of tools or equipment for preventive maintenance or predictive maintenance.
Barcode tool tracking is an effective system for tool management. Barcodes or RFID tags help track tool location and maintenance history. This helps to:
- Enhance teamwork. Providing tool tracking enables everyone on the team to see where tools are and who is using them, fostering collaboration
- Prevent tools from being lost. Perhaps the biggest benefit of barcode or RFID tracking is that you know where tools are at any given time
- Ensure tools are in the right place at the right time. Barcodes enable verifying tools to be located precisely where they are needed
- Reduce cost. Accurate tool tracking has benefits in terms of productivity and tool life, which cuts costs
- Improve health and safety. Safety-critical equipment is maintained correctly meaning it is always available and fit for purpose
Team Commitment
Commitment among team members is vital for good tool management for maintenance. As well as all the financial and efficiency advantages of managing maintenance tools, looking after tools is also vital for health and safety. Therefore, it’s really important that there is strong employee buy-in to tool management. That buy-in requires appreciation from your maintenance team for the need for tool management strategies and a commitment to make them work.
Although the latest technologies such as tool management systems integrated with CMMS are hugely beneficial, it is also important that there is a commitment to teamwork, quality, cleanliness, order, and safety when it comes to tools.
Need tool storage? RS has got you covered. Explore our range of toolboxes here.