- Published 25 Sept 2023
- Last Modified 12 Feb 2024
- 5 min
Safety Standards in Industrial Maintenance
Industrial plant maintenance standards help engineers develop systems for maintaining machinery that keep it running smoothly, and above all, safely. Find out more about how and why to implement effective and efficient preventive maintenance best practices and industrial predictive maintenance based on internationally recognised expertise.
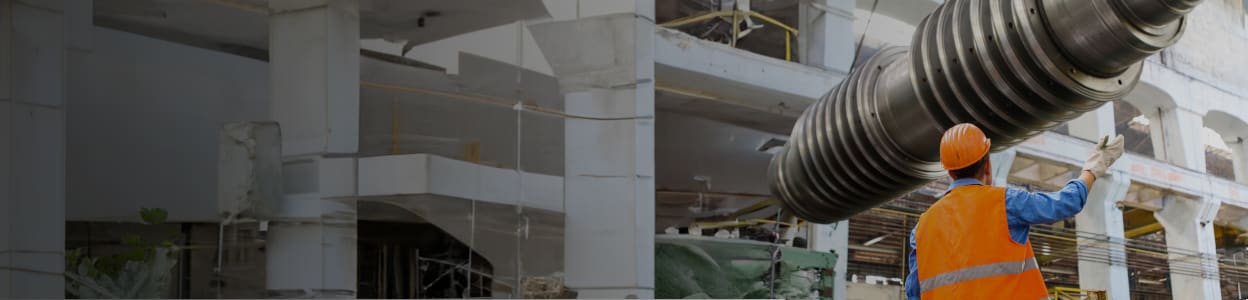
Without effective industrial equipment maintenance services, machinery can fail, safety may be compromised, and energy usage and costs may soar. Industrial maintenance standards help manufacturers establish best practice when it comes to maintenance tasks such as replacing components, lubrication, cleaning machinery, and making repairs.
Standards include international frameworks like ISO 55000, methodologies such as Total Productive Maintenance that aim to completely eliminate failure, and systems drawn from lean manufacturing, as well as a host of other techniques to enhance machinery care.
When combined with other strategies such as a predictive maintenance or preventative maintenance regime, these standards enable manufacturers to get the most out of their equipment while maintaining a safe and efficient working environment.
What is Industrial Maintenance?
Simply, industrial maintenance services ensure that assets in a manufacturing facility are kept in good condition. Industrial maintenance and repair services prevent machinery breakdown, rather than maintenance being reactive: waiting for a machine to fail and only then repairing it. A good maintenance regime reduces machinery downtime, which can be very costly to manufacturers, and unplanned maintenance. In doing so, it helps them maximise productivity and cut costs. Industrial maintenance may be preventative maintenance, where machinery is maintained according to a strict schedule determined by the machinery manufacturer, or, increasingly, predictive maintenance, where machinery is continuously monitored for signs of faults developing and repaired before problems arise.
Why is Industrial Maintenance Important?
Industrial maintenance is important because it increases plant safety and reliability, cuts costs, reduces unplanned maintenance and machinery downtime, slashes energy consumption, and extends the lifetime of equipment. Without following preventative maintenance best practice, or learning how to implement predictive maintenance, manufacturers may find their productivity suffers, costs go up, and safety is compromised.
What is ISO 55000?
ISO 55000 is a leading, comprehensive international asset management standard. The standard explains how to implement an effective asset management system. It includes:
- ISO 55000 (introduces critical concepts and terminology for asset management)
- ISO 55001 (establishes requirements for implementing, maintaining and improving an asset management system)
- ISO 55002 (guidance for application of an ISO 5000-based asset management system)
ISO 55000 helps the manufacturer build a complete asset management plan from the ‘cradle to the grave’ of equipment. An important part of this process is development of a machinery maintenance plan outlining maintenance strategies, prioritisation of maintenance tasks, and maintenance cost forecasts.
It’s important you measure if your asset management plan is working. You can do so by keeping track of a number of metrics, including mean time between failures (how long a piece of machinery functions between repairs) and mean time to repair (the average amount of time it takes to repair a piece of equipment). Both these measures enable you to understand the effectiveness of your industrial maintenance.
Another ISO standard that manufacturers use is ISO 13374, which outlines the best means of carrying out data processing in condition monitoring and machinery diagnostics.
SAE Standard JA1011
SAE JA1011 was originally developed in the aviation industry and focuses on what is known as ‘reliability-centred maintenance’. It is a systematic process for developing the best possible maintenance plan for a specific asset. SAE JA1011 helps to ensure assets do what they are intended to do in their operational context. Maintenance engineers using SAE JA1001 start by asking questions about the asset’s purpose and potential for failure, and what actions can be performed to prevent or mitigate a failure.
What is Maintenance Best Practice?
Industrial maintenance best practice should see equipment kept in good repair, maintenance operations carried out safely, and machinery maintenance logs kept up to date. Effective industrial maintenance makes machinery more reliable, and therefore safer. When equipment develops a fault, it may present additional hazards. In addition, unplanned maintenance activities may mean more contact with dangerous machinery than is desirable. It's also important – in addition to preventing breakdown – that machinery maintenance is planned carefully and carried out safely.
Total Productive Maintenance
‘Zero accidents’ is one of the key pillars of total productive maintenance (TPM), which strives for perfect production. TPM blurs the line between maintenance and manufacturing by encouraging shopfloor workers to take autonomous ownership of maintenance of the equipment they work with. It encourages predictive maintenance, continuous improvement, training, and maintaining a safe and healthy working environment.
What is 5S?
5S was initially developed as part of the Toyota Production System and is now synonymous with lean manufacturing. The 5Ss are:
- Sort. Sort what’s needed from what’s not needed.
- Set in order. Organise everything.
- Shine. Clean and inspect.
- Standardise. Develop common methods for consistency.
- Sustain. Keep going and continue to improve.
The steps should be carried out in order. When applied to maintenance, 5S reduces downtime, prevents equipment failure, and increases efficiency. 5S should have a beneficial impact on mean time between failures and mean time to repair metrics.
What is the 80/20 Rule?
The 80/20 rule represents an ideal ratio between time spent on preventative or predictive maintenance and time spent repairing machinery that has already failed. Ideally, engineers should spend 80% of their time on the former and 20% on the latter.
Maintenance Tips
These international standards, lean techniques, and tried-and-tested rules of thumb aren’t the only way of keeping your machinery in top condition. It’s also worth considering exploiting the power of industrial maintenance software such as computerised maintenance management systems, which can help automate and track many common preventative and predictive maintenance activities. Meanwhile, it’s vital that your engineers have the right tools for the job, so take the time to assess the wide range of industrial maintenance products on the market and make sure you get what you need for your maintenance activities.
RS offers a wide range of industrial maintenance solutions. Visit us today to find out more.
Related Articles
Related links
- How to Maintain Industrial Cooling Systems
- Digital Transformation in Industrial Maintenance
- A Guide to Machine Safety Standards and Equipment
- Guide to Industrial Maintenance Tools
- Lighting in the Workplace
- Robotics in Industrial Maintenance
- Making Industrial Maintenance Sustainable
- Why are Industrial Lubricants Important?