- Published 27 Sept 2023
- Last Modified 17 Oct 2023
- 8 min
Digital Transformation in Industrial Maintenance
The fourth industrial revolution is rapidly changing the way manufacturers work – and that includes machinery maintenance. Our guide explains how AI, the Industrial Internet of Things and digital twin technology are helping OEMs adopt predictive analytics to prevent machinery failing and improve productivity, reduce cost, and enhance health and safety.
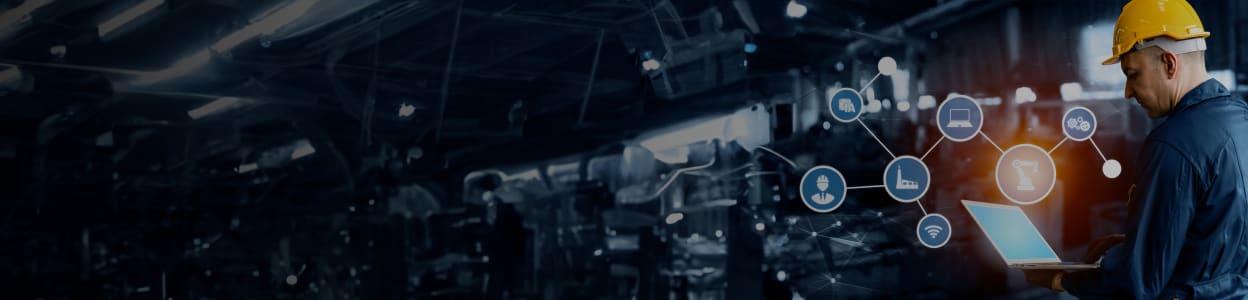
An industrial digital transformation is rapidly taking place. Industrial digitalisation now encompasses the complete industrial process, from gathering materials and resources to managing the supply chain, the design process, and the manufacturing and final delivery of goods. Maintenance in industry is just one area where digital technology is having a big impact, but it is changing fast because of the capabilities of new technologies.
Indeed, the digital transformation framework for industrial maintenance is part of the ‘fourth industrial revolution’ – in which the latest technologies such as AI, machine learning and Big Data, alongside the increasing connection of physical systems to the internet (the Industrial Internet of Things), transform the way products are manufactured. As industrial digitalisation increases, machinery maintenance can benefit from the adoption of some of these technologies.
What is Digital Maintenance?
The digital transformation in maintenance exploits advancements in technology, data and analytics to maintain machinery more effectively. For example, predictive maintenance – continuously monitors machinery to diagnose problems before they cause serious issues. Relying on networks of sensors and collecting and analysing huge volumes of digital data about equipment performance. Approaches such as this are a big step forward from ‘reactive maintenance’ – waiting for machinery to fail and then fixing it. Engineers use common maintenance performance metrics for manufacturing industry such as mean time between failure to assess the success of their digital maintenance strategy.
Many manufacturers also now use manufacturing maintenance software such as CMMS (computerised maintenance management systems) to plan, schedule and assess maintenance activities. Digital maintenance is becoming prevalent because it enables OEMs to cut maintenance costs, increase machinery uptime, and improve productivity.
The digital approach is sometimes also referred to as ‘smart maintenance’. Again, it’s part of the broader trend of Industry 4.0 and the increasing interconnectivity of physical objects and the internet. Engineers are obtaining and analysing huge volumes of data from machinery – whether by condition monitoring or other data collection methods – and using that to inform the maintenance regime.
New Maintenance Technologies
There’s a range of new digital maintenance technologies out there. Some of the more common approaches include:
Predictive Maintenance Technology
Predictive maintenance works on the basis that the best way of maintaining machinery is to stop it failing in the first place by continuously monitoring its health. It’s different to a preventative maintenance approach, which relies on regularly scheduled maintenance (although both predictive and preventative maintenance are regarded as ‘proactive’, rather than reactive, maintenance).
Instead, predictive maintenance uses condition monitoring technologies such as vibration analysis to continuously assess parameters like speed and frequency of vibration. Anomalies in this data may indicate an underlying problem with a machine before it is otherwise apparent. Engineers can then carry out planned maintenance to address the issue.
Predictive maintenance technologies include not just vibration monitoring but also infrared thermography (which detects changes in the heat emitted by components) and ultrasonics (which can help engineers detect leaks thanks to changes in sound).
An excellent non-destructive method for measuring and monitoring temperatures in your plant and machinery is Infrared thermography. This technique helps you monitor operating temperatures to ensure optimal equipment running. It also alerts you to any issues that if left unaddressed could lead to major problems later down the line.
Ultrasonic monitoring enables engineers to accurately determine the location of a leak, electrical emission, or a particular sound in a machine that could indicate a problem. That’s because mechanical equipment and leakage produce a broad range of sound. These types of problems generate high-frequency short wave signals that tend to be directional and highly localised. These sounds can be separated from background noise to detect their precise origin. Ultrasound is a particularly sensitive condition monitoring technique because it picks up on subtle changes in sound that may indicate a problem with machinery before it is otherwise apparent.
Other techniques include oil analysis (where metal particles in oil or changes in oil viscosity may indicate machinery wear). For motors, there is motor condition analysis, which collects data on electric motor performance to indicate faults.
What these technologies have in common is that they all collect digital data and analyse it to predict future problems, enabling engineers to stop damage to machinery in its tracks.
Industry 4.0 and Maintenance
If the third industrial revolution was the adoption of computers and automation such as robotics in manufacturing, Industry 4.0 is its digitalisation via the Industrial Internet of Things, Big Data and artificial intelligence. Making manufacturing assets such as machinery smarter (through the incorporation of networks of sensors and other technologies that collect digital data) means they can tell you when they’re experiencing problems. This has huge implications for industrial maintenance, because it makes it possible to predict failure. And being able to predict failure prevents machine downtime.
Automation and Maintenance
Manufacturers depend on automation such as robotics, conveyor belts, computer numerically controlled machine tools and automatic process technologies in industries such as food and beverages and pharmaceuticals. Industrial automation typically relies on electronics such as programmable logic circuits, PCs and other control systems to automate tasks. PLC controllers can automate a process, machine function, or entire production line.
According to automation giant ABB, in the early days of automation, collecting information about equipment was tricky, and maintenance engineers typically had to attend in person to fix problems with automated equipment. One way in which digital technology changed things is that faults can now often be diagnosed remotely and machinery performance evaluated. Combined with the skills of technicians, this has helped manufacturers using automation move from a reactive to a proactive maintenance approach.
AI and Maintenance
Big Data is great in terms of providing much more information to the engineer, but it means nothing if they can’t interpret the information and act on it. That’s where artificial intelligence comes in. AI helps engineers collect and process very large volumes of data from machinery maintenance and make predictions about what maintenance is required, and when.
Using AI for predictive maintenance improves the reliability of machinery and avoids equipment breakdown. It can also improve manufacturing quality by minimising errors. But AI is only as good as the information it works with, which means data collection must be consistent in a vibration monitoring application, for example.
Digital twin predictive maintenance – where an entire manufacturing plant or process can be simulated, or virtual replicas of physical assets created – is also making analysis of manufacturing data for maintenance more efficient.
Data and Maintenance
Machines are capable of producing a huge amount of digital data. This information can be used to make their maintenance more efficient. Operational data provides numerous insights into machinery health, and indicates to an engineer the scope and timing of maintenance activities to prevent problems worsening – and ultimately, machine failure.
Analysing all that data swiftly manually would be impossible. So data analytics for predictive maintenance tends to require AI and associated technologies like machine learning to extract data and generate useful insights.
Internet of Things and Maintenance
The Internet of Things (IoT) and Industrial Internet of Things (IIoT) simply means a network of physical objects connected to the internet. In a maintenance context, the IoT involves the transmission of information collected by sensors and other technologies over a network. Thanks to the ability to collect and transmit data, it’s possible to carry out predictive analytics that indicate the need for maintenance.
Digital Twin Technology and Maintenance
A digital twin is a virtual representation of a physical object or manufacturing process. Once a digital twin has been created, it can be used to conduct simulations, analyse performance of assets, and provide ideas for possible improvements. These suggestions can then be applied to the physical counterpart. Using a digital twin, it’s possible to determine an optimal maintenance strategy. Developing an efficient strategy without the digital twin could be very time-consuming or costly.
Benefits of Maintenance Digital Transformation
Benefits of digital maintenance include everything from greater machinery uptime to increased productivity and an improved health and safety culture. Proactive maintenance relies on digital technology: predictive maintenance, especially, is impossible without it. Although the upfront costs of investing in predictive maintenance may seem high, manufacturing organisations report that the return on investment far outweighs the initial cost, and benefits include better safety compliance, increased asset lifespan, more efficient use of personnel, improved production capacity and productivity – the list goes on. Preventative maintenance regimes, meanwhile, are often now facilitated by digital technology such as CMMS systems.
In short, as the fourth industrial revolution continues, digital technology is proving indispensable for engineers focused on developing cutting-edge maintenance strategies. Manufacturers are embracing digital maintenance – and transforming their operations in the process.
Learn more about how RS can help you with your workplace automation.