- Published 6 Dec 2023
- Last Modified 6 Dec 2023
- 8 min
What is Precision Maintenance?
Precision maintenance is consistent, correct maintenance done at exactly the right time with the same method, no matter the technician. It is a system of avoiding breakdowns and maximising uptime by giving machines the maintenance they need, when they need it. Precision maintenance is knowing your team is protecting your investments correctly.
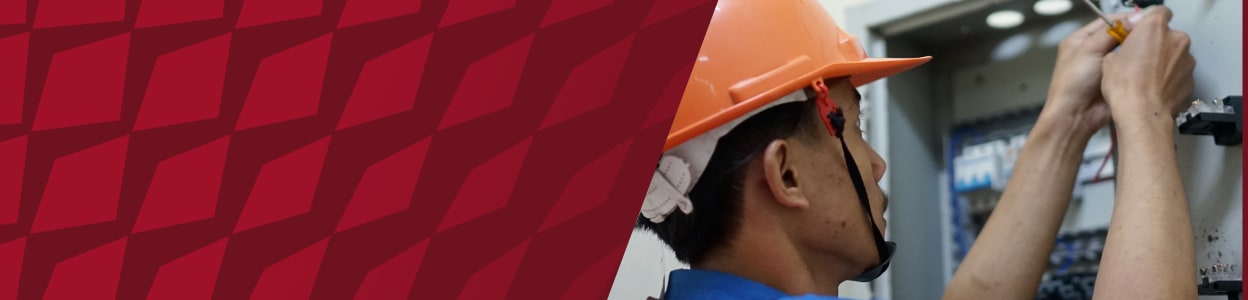
‘Precision’ refers to consistency: performing tasks in the same way over time with minimal variation.
Precision maintenance is a system of equipment maintenance techniques that are always followed in the same way. This extends to the conditions that trigger maintenance, the tools and parts used, and the technician skills and training required.
Precision maintenance isn’t necessarily a maintenance scheduling approach, such as preventative or predictive maintenance (though those can factor into it). It is a culture of making sure things are always done the same, and correct, way.
Performing high precision maintenance using common, set techniques will give you much more reliability from your assets.
Precision Maintenance Techniques
Precision maintenance techniques are as varied as the equipment they’re used on, but there are some widely applicable starting points:
- Write clear maintenance procedures and work instructions that cut out ambiguity. Keep these as controlled documents, but also make them available for the appropriate maintenance staff.
- Determine maintenance priority levels. Assess the regular maintenance costs of your assets and identify the assets your company most needs to bring in revenue. Set maintenance plans based on which machines are constraints, have a history of breakdown, are expensive to replace, or feature high vibration.
- Keep your spaces clean. A clean environment is a healthy operating one for your machines and your staff. You’ll have fewer contaminants degrading performance and less confusion about where key tools and parts are. Also mandate wide and comfortable spaces around access points to increase ease of maintenance (and keep everything well-lit).
- Regularly (or constantly) monitor all key operating conditions. Since precision maintenance isn’t necessarily a maintenance scheduling approach, continually checking on your assets’ health will be your primary way of knowing when it’s time for checkups. RS condition monitoring instruments can make this a nonstop process and cut out manual verification.
- Record and document all the maintenance you perform. Have unambiguous prompts for signing off that the work was done, recording values that are measured and set. When major breakdowns occur, despite your best efforts, thorough documentation will let you trace maintenance to find deviations from set procedures. Additionally, employ root cause analysis for diagnosing breakdowns and learn how to avoid them by tailoring your maintenance methods.
Precision Maintenance Best Practices
Here are some precision maintenance best practices that will help your system:
- Invest in the best. High-quality parts, lubricants, tools, and instruments will give you the high-precision performance you’re after and be well worth the cost.
- Establish a strong calibration system. You are going to be collecting lots and lots of data to know when it’s maintenance time. Ensuring the data is accurate requires regularly calibrated tools.
- Continuously analyse the health and performance of your assets, and how well your precision maintenance system is working. Always strive to further improve your maintenance efficiency—and this can include reducing an asset’s maintenance if you determine it can handle it. The increased uptime will be worth it.
Precision Maintenance Training
You need to ensure everyone is performing maintenance tasks in the same way.
It can be difficult to make technicians defer to your procedures rather than their deep-seated maintenance methods and ‘tricks,’ however effective they may be. Emphasise that consistency reduces confusion over breakdown causes.
Since you will be running your maintenance procedures frequently and without deviation, these are good training opportunities for new staff to shadow current workers and learn these maintenance skills.
Your biggest challenge in precision maintenance training is to change your company culture. If you want things to improve, sell the importance of continuous improvement and your commitment to it to employees. Showing your team that you’re willing to train them in this will create engagement in precision maintenance and momentum driving it forward.
Finally, show strong leadership commitment. Convince the maintenance team that senior management is committed to achieving precision maintenance benefits and empower the team to make suggestions for ongoing improvement—though be firm about the broader goal of reliability due to consistency.
Precision Maintenance Skills
Skills assessment is an essential part of your maintenance training.
First clearly determine what precision maintenance skills and certifications are required to perform each of your maintenance tasks. Then, assess the skillset of each of your team members. Consider which people can quickly take on some of your current tasks and who needs training.
Perhaps the most important of precision maintenance skills is willingness to follow established procedures. Maverick ‘machine whisperers’ may pull off miracles with broken-down equipment, but your primary goal is to avoid breakdowns by doing work the same way every time.
Precision Maintenance Management
The precision maintenance programme you establish will need careful management to ensure it’s generating the benefits you’re after. You’ll need to verify your inventory system has enough spare parts for your equipment and regularly check if your detailed procedures are being followed completely. This will factor into the internal and external audits of your quality assurance system.
Precision Maintenance Inventory
Precision maintenance is naturally done more frequently than corrective (reactive) maintenance, so you’ll need a steady stream of spare parts. A computerised maintenance management system (CMMS) will be indispensable for this.
A CMMS tracks machinery maintenance schedules so you can easily work around your planned downtime. A CMMS can also manage the spare parts you’ll need for this maintenance: inventorying them, setting optimal stock levels, and scheduling their purchase orders. This way, you’ll continually have the parts you need at optimal stock levels.
Also consider the storage conditions of your inventory. You’ll be investing in high-quality spare parts, and you won’t want them kept where they’ll deteriorate.
Precision maintenance can’t happen without the proper tools. Along with regular calibration, your system must track tool storage locations and current job assignments. Precision maintenance tools are high-value investments, just like the equipment they’re used for maintaining, and missing tools means frustrating replacement costs and delayed job completion.
Precision Maintenance Examples
All precision maintenance programmes are highly customised to the business’s needs, but here are a few practical examples:
Eliminating vibration is the original precision maintenance technique; precision maintenance was developed in the first place to reduce machine damage due to vibration. Monitor it, diagnose it, and stop what’s causing it to keep your machines running optimally.
When a fan belt needs replacing, have a clear step-by-step procedure for the whole process: safely shutting down equipment; removing every piece of guarding in the correct order; replacing the belt; setting and verifying tension; replacing guarding in the correct order; and testing operation. Give all these steps a clear sign-off space in the maintenance record as proof the technician followed the procedure. These will be records to fall back on if the machine experiences a breakdown that must be investigated.
For cases where you haven’t yet established instrumentation for condition monitoring, perform regular verifications instead. Check critical temperatures daily, record them, and establish protocols for what maintenance steps to take for irregular or critical readings.
And treat your maintenance programme itself as a machine that needs precision maintenance by managing and monitoring how well your procedures are being followed.
Precision Maintenance Benefits
Precision maintenance benefits take great ongoing effort, commitment, and teamwork to achieve, but those are worthy business investments.
Maximise life expectancy of machinery: Significantly reduce equipment breakdowns and downtime, and the financial and lost-time headaches that come along with them. You can also correct problems in their early stages to avoid later incidents.
Reducing downtime: Plan downtime on your own terms and control costs. You’ll also reduce expensive overtime, which is often a necessity in addressing unplanned breakdowns.
Easily meet industry standards: Quality management systems, such as ISO 9001, speak the same language as precision maintenance methods when it comes to establishing and following procedures and documenting them.
Increased safety: Any detailed maintenance procedure that you want performed successfully, frequently, and reliably by different people will naturally create good safety practices. This will further strengthen the certainty that your company is proactively avoiding disastrous problems.
Stronger company: You’ll be creating a culture of teamwork and continuous improvement since people will see their clear involvement in the company’s success.
Peace of mind: Know that you’ve cared for your investments and that they will pay off.
The Future of Precision Maintenance
High precision maintenance means running machinery more efficiently. This will become increasingly important in our world’s shift to responsible energy usage. That, combined with the benefits to company finances, safety, and culture, means precision maintenance benefits will be increasingly seen as worth the investment in years to come.
Precision maintenance techniques will employ more and more automation. Artificial intelligence and machine learning will play a greater role in the data analytics behind precision-maintenance best practices.
Browse RS maintenance solutions to realise precision maintenance benefits at your business.
Related Articles
Related links
- Confronting the downtime dilemma
- Well-oiled machines keep global food supplier moving
- What is Inventory Management?
- Condition monitoring programme helps industry leader stay on track
- Saving time and money for a telecoms service provider
- How to Clean Battery Terminals
- 3D Printing and Spare Parts Management
- RS helps ACCIONA to digitise its management processes