- Published 24 Jan 2023
- Last Modified 25 Jan 2024
- 10 min
Condition Monitoring: What Happens & When

Published January 2022
Embracing condition-based monitoring as part of your maintenance strategy will deliver increased productivity and reduce unplanned downtime.
With the use of additional, increasingly complex machines, the reliability of condition monitoring in industrial production is becoming more and more important. Condition monitoring paves the way for effective predictive maintenance through constant, inspection-free upkeep of machines and systems. In this way, manufacturing processes can deliver high performance and the overall costs of production plants can be reduced. This article shows you how the implementation works.
What is Condition Monitoring?
Condition monitoring refers to the use of monitoring technology in industrial production. It can help to supervise machines and systems, detect errors at an early stage, and prevent production downtimes. Sensors monitor individual machine parameters, such as vibration and temperature, and report the result to an evaluation unit. This means that machines can be stopped quickly, hopefully enabling faults to be detected and corrected even before any equipment failure occurs. Condition monitoring is mainly used in processes and manufacturing plants, predominantly with machinery that has rotating or moving components typically running for long periods – even continually.
Predictive Maintenance: Always One Step Ahead
Predictive maintenance is not a new concept but it has been accelerated by Industry 4.0 and the advance of technologies such as IIoT. Preventive maintenance has previously been the common maintenance approach, striving to keep machines in a good operating condition through regular maintenance to prevent equipment failures.
The concept of predictive maintenance goes far beyond this. Predictive maintenance programs aim to carry out maintenance only when it is actually necessary. To achieve this goal, digital sensing systems are used to monitor various machine operation characteristics, such as vibration, heat, and current. Using this condition data, forecasts – or predictions – can be made on when wear and degradation of performance indicate intervention is required. Predictive maintenance measures are all actions that are initiated based on these predictions.
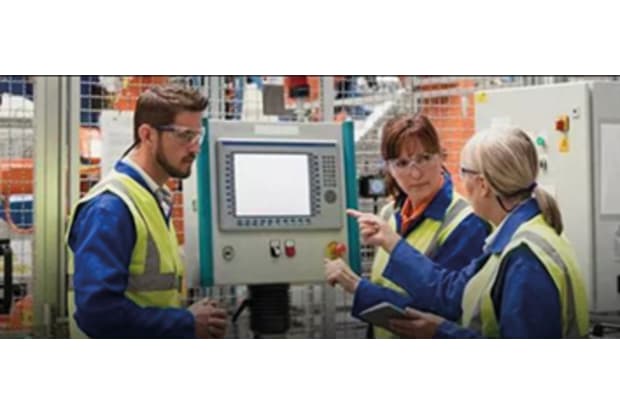
Everything You Need for Condition Monitoring
From installing cables and fixing leaks to servicing large machines, you will find everything you need to keep your operations running smoothly in the RS product range.
What Role Do Condition Monitoring & Predictive Maintenance Play Across Industry?
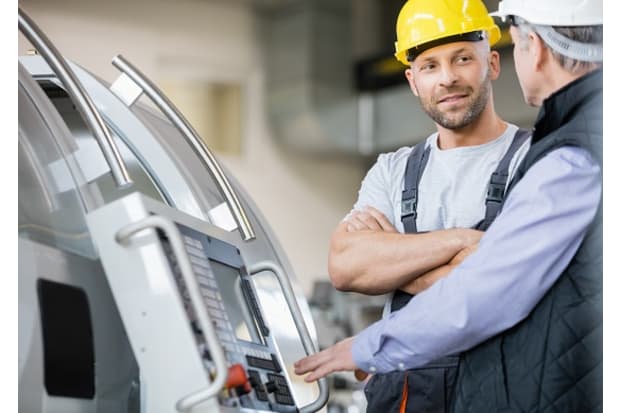
Today, many industries operate 24/7 and continually work at full or near capacity to operate cost-effectively. As capacity utilisation increases, so does the need to get smarter with the way you maintain your machinery, reduce downtime, and ensure production facilities are run smoothly and in a cost-efficient way. Condition-based monitoring is one of the most important tools in the predictive maintenance of production facilities. It replaces the classic visual maintenance inspection in a modern, digital, and often autonomous way, allowing maximum use of machines while reducing the reliance on increasingly stretched maintenance teams.
Only monitoring technology with sensors enables predictive, inspection-free maintenance based on the evaluation of process and machine data. These data collectors process real-time information, meaning that you can predict any needs-based maintenance and detect machine failures before they occur. This helps to avoid production downtime due to unforeseen faults, generating cost savings.
In addition to data collection, digitisation, and transmission, key focal points are the storage, analysis, and evaluation as well as the forecast calculation for certain failure modes and events. This is where cloud-connected solutions are perfect, as they allow this real-time data to flow continually from the sensors and monitoring gateways into analysis tools which can then instantly inform maintenance teams that action is required.
All condition monitoring and predictive maintenance tasks ultimately lead to a company's cost optimisation and profit maximisation. A study conducted by the McKinsey Global Institute on IoT shows that downtimes can be reduced by up to 50% and maintenance costs by up to 40%. This corresponds to a savings potential of up to 630 billion US dollars.
Advantages of Predictive Maintenance & Condition Monitoring:
- Precise advance planning of maintenance activities
- Reduce repair work
- Avoid unexpected failures of production plants
- Increase uptime
- Increase the service life of plants
- Optimise your spare parts management
- More efficient personnel management
- Higher plant safety
- Minimise accidents
How Does Condition Monitoring Work?
Sensors can be used to monitor assets and machines in a variety of ways to identify problems and sources of error at an early stage. Key features of condition-based maintenance sensors include:
- Vibration analysis and diagnostics: Vibration sensors are used to monitor axes and bearings on rotating machines
- Detecting particles in hydraulic fluids (oil condition analysis): The composition of lubricants can be scanned with an electronic microscope. This allows you to ensure the smooth functioning of machines and order new materials in good time
- Infrared thermal monitoring (infrared thermography): Excessive heat development can be a sign of component failure, especially electrical cables and contacts. Infrared or thermographic sensors can be used to detect deviations in heat generation
- Acoustic monitoring (ultrasound and acoustic emission): Digital ultrasonic devices can measure high-frequency signals on bearings and evaluate them as acoustic signals. This makes it possible to predict friction and defects in motion bearings, which is particularly important for high-speed mechanical applications and high-pressure fluids
- Oil condition sensors: Sensors are used to perform the spectrographic oil analysis of the composition to identify critical contamination. Depending on the type of contaminating particles, it is even possible to determine the causes and initiate appropriate countermeasures
How Sensors are Used in Condition Management
Efficient condition monitoring requires the monitoring of machines and their various physical components by means of sensor data. This can include vibration, pressure, temperature, and Hall-effect sensors, as well as infrared cameras.
This results in numerous possible applications. We have listed some typical examples below:
- Forklifts and injection moulding machines: Sensors control the chemical composition of the hydraulic oil
- Centrifuges: Sensors monitor the vibration, speed, and turning speed of the rotational axis, to report possible malfunctions in the event of deviations
- Packing machines: Condition monitoring uses pressure and flow sensors to check the air consumption, the operating pressure, and the function of the axes of the servo-pneumatic drive system
- Reciprocating compressors: Acceleration and displacement sensors measure absolute vibrations at the cross and cylinder heads and any material wear, for example on the support ring
- Cooling units: Temperature sensors for liquid or gaseous media provide measurement values for controlling the temperature in the cooling circuit
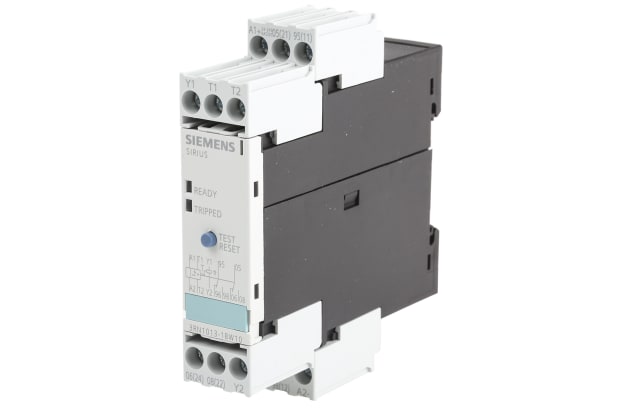
Applications for Monitoring Relays
These relays monitor machine functions and trigger a circuit breaker when they detect a fault.
The most common monitoring applications for relays include:
- Voltage monitoring
- Phase monitoring
- Temperature monitoring
- Current monitoring
- Frequency monitoring
- Speed monitoring
- RPM monitoring
- Special relay with a thermistor to cover the motor temperature
End-to-End Monitoring with Condition Monitoring Systems
Condition Monitoring Systems (CMS) not only assess machine data, but they can also centrally collect, align and retrieve data on any end device. For example, a company can provide its employees with demand-specific data on the status of individual machines (maintenance), information on the entire production process (process management), or evaluations of fault causes and damage statistics (quality management). In addition to the machine data, you can integrate building management and monitor temperatures in production rooms or the condition of security doors, with the aim of systematically optimising your entire production process.
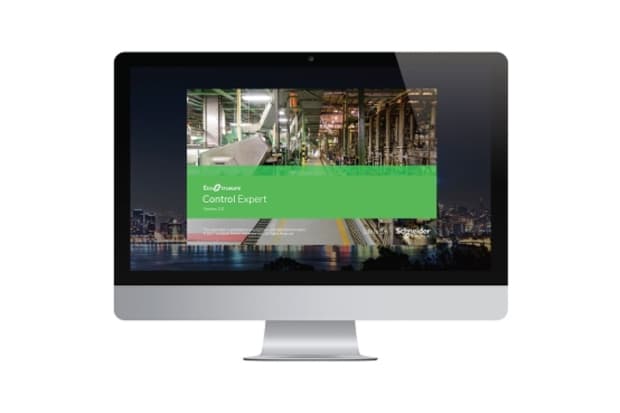
PLC Programming Software for Predictive Maintenance
Good programming software is the basis for efficiently monitoring the condition of machines and evaluating collected data delivered via a PLC interface (programmable logic controller). EcoStruxure Control™ from Schneider Electric combines IoT-enabled automation with an open plug-and-play architecture, brought together in a digital platform.
Key Features:
- All IEC 61131 languages (LD, IL, ST, SFC, FBD) and structures
- Multitasking structure for adaptable applications
- Easy import/export with XML, COM, DCOM
- Debug, online services, SPS simulator
- PL7 and concept converter
- Licence-free libraries: PLCopen, Fuzzy, AGA and more
Wireless CMS Systems
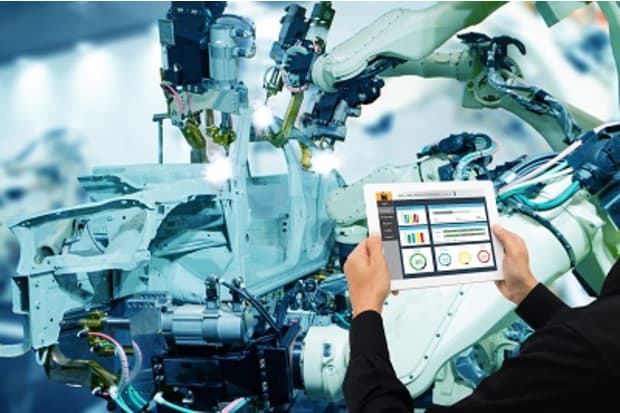
Increased networking through the Industrial Internet of Things (Industry 4.0) creates new possibilities in the process management of industrial companies, such as the end-to-end digitisation, monitoring, and evaluation of production plants (Maintenance 4.0).
Products, processes and means of production are equipped with smart sensors and transmit data wirelessly. It means that any damage to cables cannot impair data evaluation and we no longer have to install or lay additional cables in cluttered production areas. Sensors equipped with wireless technologies can be attached directly to a machine, for example, with the vibration data transmitted wirelessly to an evaluation unit.
Monitoring the Future: As Much As Necessary, As Little As Possible
The extent to which condition monitoring should be used to make an upgrade worthwhile depends on what a company wants to do with the real-time data acquisition. Full electronic control of machines and systems up to building technology is costly and should, in theory, only pay off for industrial giants. Nevertheless, small and medium-sized companies should not have to go without condition monitoring. Instead, they should implement it within a data-driven framework that suits them so they can remain competitive and future-oriented. To evaluate which machines or assets require monitoring, they are divided into different classes. Depending on the purpose, downtimes and effects, repair effort, availability of spare parts, general condition and safety aspects, we prioritise them by their importance to the production process and determine the control intensity. We can then come up with an individual, cost-effective maintenance strategy.
- Critical components: Machines that are indispensable to the production process should be constantly and proactively monitored
- Essential components: Non-critical machines that are important but without which the production process can still operate, can be condition-monitored
- Standard components: For machines and components that are commonly used and can be easily replaced or repaired, scheduled manual maintenance is sufficient
In the future, remote from-source services will play an increasingly important role. With systems becoming more and more complex, specific troubleshooting knowledge also increases. With special applications, manufacturers can directly evaluate the errors detected by the monitoring system and, if necessary, solve them remotely and automatically. This further reduces the monitoring effort but requires remote access by third parties to sensitive data. To protect from unauthorised access, additional IT security measures are a must.
Whether the implementation is actually worthwhile for a company in individual cases depends above all on the security levels.
What Does Overall Equipment Effectiveness Mean?
OEE (Overall Equipment Effectiveness) is a metric implemented by the Japan Institute of Plant Maintenance. This measures the added value of a production plant and takes into account the most common productivity problems such as downtime losses, power losses, and quality losses. The calculation of OEE, as well as its monitoring and improvement, is part of condition monitoring and is closely related to controlling. It can help to analyse relevant cost aspects such as productivity, profitability, and overall effectiveness and make them comparable at the overall company level, taking into account the entire manufacturing process. The OEE value is between 0 and 1 or 0% and 100%.
Calculating OEE
The OEE is a measure in % of the added value of a production plant. It is calculated as follows:
Degree of utilisation x degree of efficiency x degree of quality = OEE
- Degree of utilisation = operating time / planned production time
- Degree of efficiency = production quantity / planned production quantity
- Degree of quality = flawless products / production quantity
Related links
- From condition monitoring to condition based maintenance
- Reducing downtime with vendor-managed inventory
- Maintenance Using Vibration Analysis and Condition Monitoring
- Create a winning strategy for condition-based maintenance
- RS Condition Monitoring Solutions
- Condition Monitoring and Predictive Maintenance
- Hauber Elektronik Production Monitoring System HE100 Vibration Monitoring
- Hauber Elektronik Production Monitoring System HE101 Vibration Monitoring