- Published 19 Jun 2023
- Last Modified 25 Jan 2024
- 5 min
Maintenance Using Vibration Analysis and Condition Monitoring
Learn about vibration analysis equipment and how to use vibration measurements to monitor the condition of machinery to predict failures before they happen.

Condition monitoring vibration analysis assesses a machine or equipment using vibration measurements. Vibrations generated during machine use indicate its operational health. You can detect when something is going wrong by understanding the equipment’s normal vibration readings. For example, a deviation in the vibration signature could mean a component is failing.
So, analysis of vibrations allows you to detect problems before they occur, enabling you to intervene before equipment fails. This is known as predictive maintenance.
Why is Condition Monitoring and Vibration Analysis for Predictive Maintenance Important?
Predictive maintenance detects problems before they cause unscheduled and expensive machine downtime. It allows engineers to perform preventive maintenance work to stop equipment failure and enable machine protection. Of the various condition monitoring techniques available, vibrational analysis is an ideal way of monitoring equipment with moving parts, specifically motors.
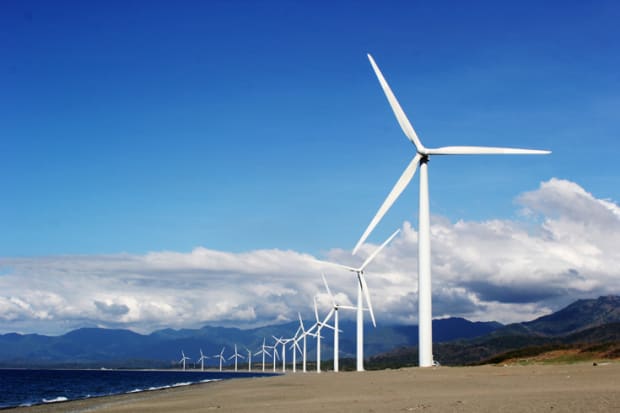
Condition monitoring vibration analysis equipment is useful in many industries. For example, it can be used anywhere where heating, ventilation, and air conditioning equipment (HVAC) is deployed to prevent fan and compressor failure. Condition monitoring equipment is also used in sectors where pipework must be monitored, such as oil and gas production, the water sector, and power generation.
Offshore wind operators use vibrational analysis to monitor the health of wind turbines and components such as rotating machinery. Condition monitoring has also been used in the rail industry to monitor train control systems, and in aerospace by connecting a data acquisition unit and sensors to aircraft components.
How Do I Interpret Condition Monitoring Vibrations?
Vibration data will help you make informed maintenance decisions. However, you need to know how a machine typically vibrates, so it’s wise to start with an understanding of its vibration spectrum. The vibration spectrum shows expected vibration behaviour. Understanding how vibration should behave enables you to identify anomalies that may indicate a machinery problem. The typical vibration characteristics are known as the baseline.
Typically, vibrations are assessed by acceleration, displacement, and velocity. Measuring displacement, velocity, and acceleration shows the vibration severity, sometimes known as its amplitude. The amplitude is the first indicator of the machine’s condition. Larger vibration amplitudes tend to indicate higher defect levels.
These parameters target different characteristics of machine vibration and allow the engineer to uncover potential problems. For instance, displacement analysis looks at vibrations at low frequencies measuring the back-and-forth movement of a part usually read in micrometres. Irregularities in the rhythm of the displacement are indicators of problems with the part's motion. Meanwhile, acceleration and velocity measurements are used to analyse machines more generally. Vibration sensors monitor overall vibration patterns during machine use.
Measuring velocity is used as a vibration measurement for most condition monitoring applications because it provides an indication of destructive force and therefore overall machinery health. To measure vibration velocity and other parameters, vibration sensors can be installed on a machine.
Vibration analysis finds many faults. Sensors might monitor the vibration, speed, and turning speed of the rotational axis of a centrifuge to reveal potential problems. Alternatively, acceleration and displacement sensors might measure absolute vibrations at the cross and cylinder heads of a reciprocating compressor and any material wear, such as on the support ring.
Velocity is the best indicator of machinery health for low and intermediate-speed components. Velocity measurements capture the frequency range of common faults such as misalignment, looseness, or imbalance. Velocity amplitude changes occur later than acceleration changes but also increase over time. This enables a better picture of the equipment's condition.
Other faults vibration analysis may reveal include:
- Bearing failures
- Faults with motor motion
- Bent shafts
- Gearbox failures
Types of Fault and Sensor
Let’s look at some of those common faults in more detail.
Bearing Failures
Bearing faults are very common, making up around half of all electric machine failures. They can result in equipment outages or breakdowns, damage, and financial loss.
Misalignment
Misalignment occurs when the shafts of two directly mating components meet at angles or are offset from each other. This typically results in high vibration levels. Misalignment reduces bearing, shaft, seal, and coupling lifespan.
Mechanical Looseness
Mechanical looseness may be rotating or structural. Rotating looseness is caused by clearances between rotating and stationary components, such as bearings. Sometimes rotating looseness is down to poor machine design, but it is often driven by component wear. Structural looseness is usually caused by looseness in the machine foundation. Improperly tightened bolts, corrosion, or cracking can be the culprit.
Imbalance
Rotating imbalance occurs when mass is unevenly distributed around the axis of rotation. Left uncorrected, it can shorten bearing life, increase noise, vibration and maintenance, and reduce machine life.
Adding sensors to machinery gives engineers the ability to constantly monitor its vibrational signature to pinpoint faults and make any necessary repairs or adjustments. This keeps the machinery running smoothly, thereby increasing its lifespan. Accelerometers in vibration sensors measure changes in the amplitude, frequency, and intensity of forces. When attached to the machine being monitored, the device generates a voltage signal corresponding to the frequency of the machine’s vibrations. This is usually how often the vibration occurs.
Piezoelectric accelerometers use the piezoelectric effect to measure acceleration changes. They have dominated vibration condition monitoring applications for years.
To recap, for conditioning monitoring, you should install vibration sensors measuring parameters targeting different characteristics of machine vibration. Measuring displacement, velocity, and acceleration shows the vibration severity, known as its amplitude. The amplitude is the first indicator of machine condition. Larger vibration amplitudes tend to indicate higher levels of defects in a piece of equipment.
Displacement provides a general picture of machine health using low frequencies, while acceleration deals with high frequencies. Velocity is used as a vibration measurement for most condition monitoring applications because it indicates destructive force - and therefore overall machinery health.
Machine failures account for almost $1 trillion in manufacturer losses per year. Maintaining the health of our equipment through constant conditioning monitoring will help mitigate inefficiencies in machine operation, costly repairs, and machine downtime.
Are you looking to implement vibration analysis predictive maintenance for a proactive approach to maintenance? RS can help - find out more here.
Further Reading
Related links
- SICK Production Monitoring System MPB10 Vibration Monitoring...
- Condition Monitoring and Predictive Maintenance
- Condition Monitoring: What Happens & When
- From condition monitoring to condition based maintenance
- RS Condition Monitoring Solutions
- Condition Monitoring Grinds Real Results For Coffee Manufacturer
- Hauber Elektronik Production Monitoring System HE200 Vibration Monitoring
- Hauber Elektronik Production Monitoring System HE101 Vibration Monitoring