- Published 18 Sept 2023
- Last Modified 8 Jan 2024
- 8 min
A Guide to Predictive Maintenance Strategy
Predictive maintenance uses the latest AI and machine learning techniques to assess machinery health and alert engineers to problems before they result in costly downtime. Read this guide to discover how to implement a predictive maintenance strategy and learn about the technologies on offer.
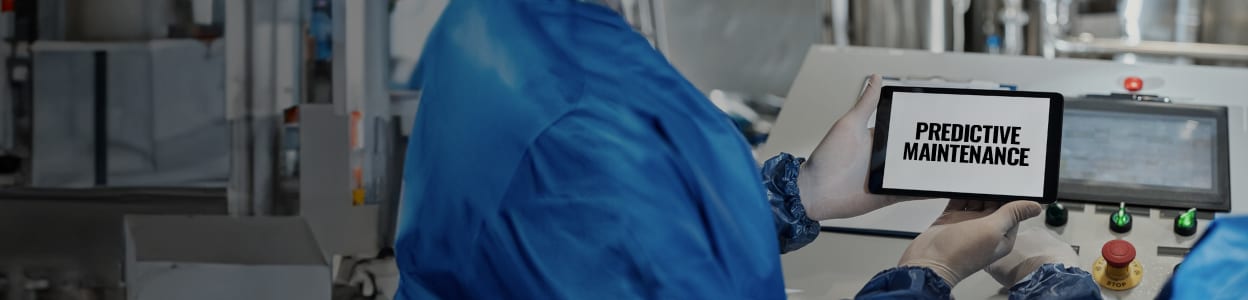
Used for everything from assessing the condition of remote offshore pipelines in oil and gas to monitoring the health of components on jumbo jets and preventing power lines from going down, there are many predictive maintenance examples.
Predictive maintenance solutions allow engineers to diagnose problems before they become critical and result in machine downtime, unplanned maintenance – and increased costs. They assess actual machine health, using sensors and other technologies to collect data and provide continuous condition monitoring of equipment. The aim is to diagnose faults before they cause machine breakdown. Understanding when and where corrective maintenance is needed is key to your predictive maintenance strategy’s success.
Read on to learn more about predictive maintenance. Explore the benefits and challenges of implementing a predictive maintenance strategy, some of the latest technologies, and how to implement a predictive maintenance solution.
Preventive Maintenance vs Predictive Maintenance
So, what’s the difference between predictive and traditional preventative maintenance? Preventative maintenance is routine maintenance of equipment to keep it running. For example, a manufacturer may specify that maintenance is carried out regularly. So, preventative maintenance is planned or scheduled according to the manufacturer’s recommendations. As with predictive maintenance, the aim is to avoid component failure and minimise downtime.
The key difference is that predictive maintenance actively monitors the condition of a machine. It alerts the engineer to any anomalies that could mean failure is on its way. By intervening and performing corrective maintenance, this outcome can be avoided. Predictive maintenance relies on many different technologies including vibration monitoring, in which sensors pick up vibrations from the machine that may indicate something is awry. This is often used on high-speed machinery with rotating parts. Cutting-edge technologies such as machine learning and artificial intelligence (AI) are also used to predict problems before they occur. Learn how RS can help you with predictive maintenance and condition monitoring.
Benefits of Predictive Maintenance
Predictive maintenance increases productivity, reduces breakdowns, and lowers maintenance costs. A good predictive maintenance strategy can eliminate machine failures altogether. Some of the benefits of predictive maintenance include:
Minimising Downtime
If machinery fails it has to be shut down for repair. Predictive maintenance solutions minimise unplanned downtime. Unplanned downtime can impact plant operations, resulting in lost productivity. Because predictive maintenance captures data relating to the actual condition of the equipment and uses analytics to determine when it may fail, it can help minimise or eliminate unplanned downtime altogether. Predictive maintenance enables engineers to implement proactive corrective maintenance actions in a convenient window, rather than relying on a preventative maintenance schedule.
Preventing Equipment Failures
Industrial machinery fails because components are subject to stress. Failures could be due to friction, vibration, or inadequate lubrication. Sometimes parts are not installed correctly or come loose during machine operation. Leading bearing manufacturer SKF estimates that 50,000,000 bearings are replaced every year due to damage or failure. SKF estimates that a third of bearings fail due to fatigue and another third due to lubrication problems. Other components that typically fail include gears, valves, seals, and belts.
Mechanical failures are a headache for your engineers. They may mean less efficiency or machinery overheating or leaking. If these problems worsen, there’s the risk of complete machine failure, which impacts production.
Predictive maintenance detects failures by analysing vibration or other parameters such as noise or temperature. It uses anomalies in these signals to predict mechanical failures and allow the engineer to perform maintenance before the worst happens.
Reducing Costs
A predictive maintenance strategy reduces manufacturing costs in many ways. Carrying out maintenance when and where it is needed can be cheaper than a traditional preventative regime, where maintenance is performed according to a schedule.
By repairing equipment at the optimum time, machinery and components can last longer. Further, maintenance can be scheduled for when it is convenient (rather than a machine failing out of the blue and having to be repaired). Since unplanned downtime is very costly, predictive maintenance can save manufacturers money. Additionally, because equipment is maintained efficiently, production capacity can be maximised.
Since predictive maintenance analyses component health in continuous, real-time detail, the need to disassemble equipment to uncover maintenance issues is reduced, which saves time and money.
Challenges of Predictive Maintenance
Despite all these advantages, predictive maintenance has a couple of drawbacks.
First, it can be expensive to set up. For example, vibration analysis requires a sensor network in your machinery (part of the industrial Internet of Things). Sensors used may include piezoelectric sensors or microelectromechanical models. The cost of installing these sensors must be factored against the potential costs of machinery failure. You may also need to invest in a specialised team for predictive maintenance. This could mean paying for training or hiring new employees who understand how to do it.
Second, if you’re collecting data you don’t understand, or the wrong type of data, it’s difficult to know what it means in terms of potential failure. A typical manufacturing plant will have so many systems that adding sensors to each and collecting all the data is costly and impractical. When looking at equipment, it’s necessary to ask what parameters need to be measured. For example, it may be necessary to monitor air leakage from a compressor using acoustic sensors or vibration monitoring to evaluate the health of a machine featuring rotating equipment. Data analytics also needs a consistent stream of data to detect anomalies. Any inconsistencies in how data is captured can make it difficult to spot problems.
Predictive Maintenance Technologies
There are several predictive maintenance tools and technologies on the market. Types of predictive maintenance include:
Vibration Analysis
This is typically done to assess mechanical components’ health. Sensors detect anomalies in vibration speed, frequency, and displacement. Vibration analysis can detect problems with a range of components, including rotors, bearings, gearboxes, and motors.
Ultrasonic Analysis
Here, instruments take high-frequency sounds picked up by a microphone and convert them into audio and digital data. Differences in the data from previous measurements help detect potential problems with machinery. Ultrasonic analysis can be used for mechanical inspection, monitoring bearing and motor wear by analysing lubrication and detecting corrosion.
Infrared Analysis
Infrared analysis uses a camera to create thermal images of components. This helps detect friction in machinery and high resistance in electrical systems, indicating possible failure.
Motor Circuit Analysis
Motor circuit analysis detects faults in motors by measuring motor voltage and operating current to detect problems with power, motor circuitry, mechanical components, and motor mechanical couplings.
Oil Analysis
This tests the viscosity, water, and metal particles in machinery oil to indicate equipment wear.
Artificial Intelligence and the Predictive Maintenance IoT (Internet of Things)
As Industry 4.0 gathers pace, new technologies such as AI can greatly enhance predictive maintenance tools. AI can assess variables, make predictions by analysing trends, and let engineers know when machinery is in danger of failing. For example, AI can compare data on vibration and noise with previous patterns to forecast failure, and schedule just-in-time maintenance. AI’s ability to analyse data in this way is dependent on networks of sensors correctly positioned on machinery (the Industrial Internet of Things) and the ability to capture and store huge amounts of current and historical information about performance.
Machine Learning
Predictive maintenance machine learning is being increasingly used in predictive maintenance regimes. Machine learning allows engineers to create models that predict failure before it happens based on current and historical equipment data. Machine learning assesses historical data from sensor networks to understand patterns that could mean components are wearing out. A number of different techniques can be applied to create a predictive maintenance machine learning model. These techniques include regression models to predict remaining useful life, classification models, and flagging anomalous behaviour.
How to Implement Predictive Maintenance Technologies
There are several steps to take when implementing predictive maintenance solutions. You need to select the technologies you intend to use and install sensor networks on the assets to be monitored. It’s also essential that engineers understand the baseline condition of equipment and what constitutes an anomaly. It’s spotting anomalies that allows them to know that maintenance should be carried out. Additionally, if you are not already using predictive maintenance software like a computerised maintenance management system, you will need one to schedule maintenance.
Implementing a predictive maintenance strategy can have major benefits for manufacturing businesses, which is why the field has become mainstream over the past few years. Of course, minimising downtime and maximising productivity while reducing costs are welcomed by manufacturers everywhere. However, by making manufacturing more efficient, predictive maintenance is also expected to help reduce industrial energy usage across the world, helping combat climate change.
If you’re ready to start your workplace maintenance journey, RS can help.