- Published 18 Apr 2024
- Last Modified 18 Apr 2024
- 6 min
How to Use Thermographic Testing for Maintenance
Thermographic cameras help us see heat conditions, which the naked eye cannot register. This is to identify when machinery needs maintenance or even major fixes to correct safety hazards.
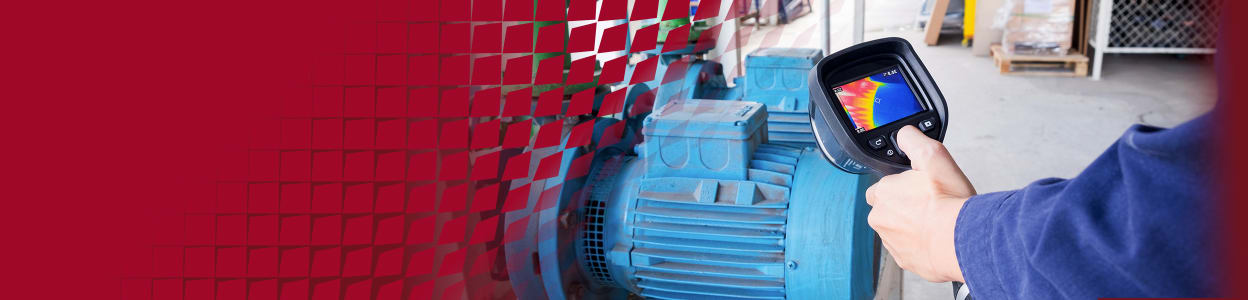
Reviewed by Karl Ralph, Technical Support Engineer (March 2024)
Heat can indicate problems that require maintenance to correct. With thermographic testing, imaging, and inspection you can uncover hot spots that might otherwise go unnoticed, letting you address them and keep your machinery cool and functional. Including this thermographic inspection in your maintenance plan can prolong equipment life, improve safety, lower equipment costs, and give you a better general understanding of your operations.
Read on to learn about how thermal imaging works and why a thermal imaging camera is a powerful addition to your maintenance instrumentation.
How Does Infrared Thermography Work?
How does thermal imaging work? Heat indicates thermal radiation, which typically occurs on the infrared spectrum and is invisible to the human eye. Thermal imaging cameras detect this infrared radiation and translate it into colours that we can see. They focus infrared energy through a lens onto an infrared sensor and then translate that information into a spectrum of visible colours. This presents hotter areas as red and cooler areas as blue, with the entire range of colours in between depicting equipment in an easily discernible temperature gradient. Since this all appears in a live video feed on a handheld device, infrared thermal imaging is a versatile, easy-to-use inspection method.
Our range of thermal imaging cameras includes dedicated handheld instruments, mountable and positionable instruments that can monitor equipment heat long-term, and even smartphone attachments that can send the infrared feed right onto your smartphone screen.

Uses of Thermal Imaging in Maintenance
Thermographic imaging is useful in maintenance, quite simply because irregular heat can indicate a problem that requires maintenance. Thermal imaging cameras can tell you much about the health of your equipment and the care it currently needs (or may need in the future).
Electrical Condition Monitoring
Resistance produces heat, and this certainly applies to electrical equipment. Rising temperatures in electrical enclosures indicate increasing electrical resistance and degrading parts. This can eventually lead to fires, and infrared thermal imaging can detect these issues before they get worse. A thermographic camera can identify parts that need replacement, detect heat escaping through insulation, and alert you to a unit that needs immediate shutdown to avoid safety incidents and costly replacements.
Electrical issues that infrared thermal imaging can identify include:
- Broken cables
- Loose, overly tight, or corroded connections
- Insufficient electrical insulation
- Failed circuit breakers
- Voltage imbalance in AC motors
- Cooling fluid issues in transformers
Bearing Monitoring
Most high-performance machinery requires bearings to keep its shafts spinning efficiently. These bearings need lubrication, attention, and eventual replacement, and thermographic inspection can help determine when.
- A lack of lubrication can cause the shaft to contact and wear against the bearing race, producing friction and heat
- Conversely, over-lubrication (an error too common in industry) can cause the lubricant to shear and heat up, which degrades bearing performance
Thermographic inspection can detect when you need preventive maintenance like adjusting bearing lubrication or even fully replacing the bearing — thus avoiding severe damage to your driveshafts, requiring costly replacements. Thermal imaging also comes up in predictive maintenance by identifying developing issues like unbalanced shafts.
Leak Detection
Any equipment leaking fluids or gases is also either releasing or letting in heat, and neither desirably so. Thermographic inspection of vessels, hoses, and pipes can detect and correct these defects in their initial stages, preventing serious incidents like fluid blowouts, fires, or hazardous gas releases. This has applications in:
- Pipelines
- Refrigerant systems
- Hydraulic machinery
- HVAC
- Engine service
- Pressure vessels
- Food and beverage manufacturing
Temperature Monitoring
Hydraulic oil does the work of the world, and it has to stay cool to maintain lubricity and prevent damaging components. Infrared thermal imaging can monitor this so you can detect overheating issues in your system and diagnose where heat is generated. This thermal detection of heat anomalies can identify issues like:
- Insufficient hose size
- Sources of oil contamination
- Damages in hydraulic motors or pumps
- Clogged hydraulic coolers
- Overly restrictive orifices
- Defective valves that are failing to divert flow
This all applies to other types of pumped process fluids as well, such as coolant, water, engine oil, and fuel.
With this map of your process fluid system’s heat profile, you can get ahead of the maintenance it needs and study your schematic to determine how to improve performance.
Benefits of Thermal Imaging in Maintenance
Using infrared thermal imaging as part of your maintenance plan brings the following benefits:
- Longer equipment life: By performing the equipment maintenance thermographic testing calls for, your machines run more efficiently and for longer, letting you maximise the return on your investment
- Better safety: Heat irregularities also present safety hazards. Detecting and addressing heat problems through thermographic inspection prevents fires, burns, and smoke. Using a thermographic camera also keeps you safely removed from unsafely hot equipment
- Lower maintenance costs: Thermography testing reveals developing problems before they get too severe, which reduces the cost of addressing these issues. This testing can also play a part in predictive maintenance, a system that aims for fewer maintenance sessions
- Fewer breakdowns: When equipment breaks and goes offline, it means high costs in repair labour, production labour waste, production material waste, overhead, and parts. The indirect costs are even worse - possible failed deliveries, loss of customers, and reputational damage. Predictive maintenance through thermal imaging lets you see issues that could cause breakdowns, and thus take steps to avoid these costly incidents
- Quicker diagnostics: If overheating or leaking systems are causing you grief, a thermographic camera can detect the source of these problems and help you determine how to resolve them
- Compare states: Thermal imaging also paints normal, steady-state pictures of equipment, so you can save and compare these baseline images against ones captured during irregular operation to get a sense of what has changed in your systems
Types of Thermal Imaging Camera
We offer various types and brands of thermal imaging cameras.
Flir thermal imaging cameras are available as:
Fluke thermal imaging camera models include:
Gun-style
Point-and-shoot-style
Mountable, positional thermal sensors, similar to levelling lasers
These options give a wide range of thermal imaging cameras to suit any maintenance application that needs heat issues diagnosed. Our own RS PRO line of thermographic cameras rounds out this lineup of instruments that can help your maintenance reap the benefits of thermographic testing.