- Published 3 Nov 2023
- Last Modified 26 Feb 2024
- 5 min
Condition-based Maintenance vs Time-based Maintenance
Condition-based maintenance and time-based maintenance respectively rely on monitoring of a machine’s current condition and planning and scheduling regular maintenance. They are both forms of proactive maintenance in that they aim to fix problems before they cause equipment failure. Although each approach has its advantages, combining them together is sometimes even more effective for the savvy engineer. Read our guide to find out more.
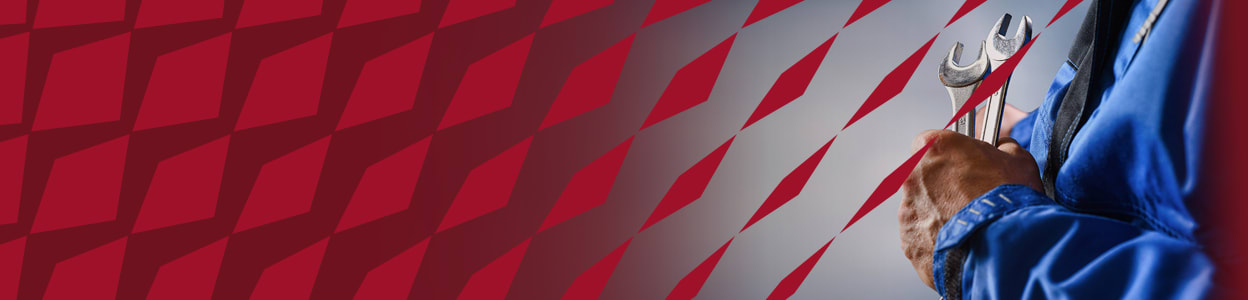
Condition-based maintenance and time-based maintenance maintenance strategies are contrasting approaches that aim for the same result: preventing machinery breaking down completely and costing manufacturers time and money. Condition-based maintenance, as the name suggests, assesses the condition of machinery while it is running and enables engineers to make interventions to keep it that way.
Time-based maintenance, on the other hand, focuses on maintaining equipment according to a regular schedule. Both condition-based and time-based maintenance provide alternatives to running machinery until it breaks down and then fixing it, sometimes known as ‘reactive maintenance’, or a ‘fix on failure’ approach.
Read on to learn more about the difference between condition and time-based maintenance – and how these maintenance solutions can also be combined to help manufacturers increase machinery uptime.
Importance of Maintaining Your Equipment
Why is it important to maintain equipment? Simply, your plant’s livelihood depends on it. Defective machinery means not only lower productivity and profitability, but also potentially faulty products and higher labour costs.
Manufacturing facilities rely heavily on the performance of physical assets, which is correlated with profitability. Extending the lifespan of machinery means a bigger ROI on that machine: your investment in it effectively goes further. Equipment that is well-maintained throughout its life will last longer. This means replacing machinery – often at very high capital expenditure – can be deferred in some cases, which also has the effect of improving productivity.
Of even greater importance, however, is the fact that factories with well-maintained machinery are safer. Fatalities and injuries in the workplace are often linked to poor maintenance.
Comparison of Condition and Time-Based Methods
Condition-based maintenance (CBM) relies on collecting data from machinery to determine maintenance needs. It is similar to predictive maintenance because it relies on collecting data from equipment to determine what maintenance activities to carry out. Time-based maintenance (TBM), also known as ‘planned maintenance’, depends on maintaining equipment at regular intervals or at times that are planned in advance.
The timing may be determined by guidelines from the machinery manufacturer, set according to the level of usage of the equipment, or even predicted based on anomalies in data collected from the machinery (time-based maintenance can be part of both a preventative maintenance and a predictive maintenance regime).
CBM means monitoring the current condition of machinery using diagnostics equipment such as sensors, measurement devices, and data collectors. Maintenance actions are determined based on the observed condition of equipment or the crossing of predetermined thresholds.
In practice, condition-based maintenance must be balanced with time-based maintenance. If time-based maintenance has already proven to be effective in preventing breakdown of machinery, then installing the networks of sensors necessary for condition-based monitoring may be unnecessary and expensive.
Condition-Based Maintenance Applications
There are a number of different types of technology that are used in condition-based maintenance applications. They include:
- Vibration analysis. Vibration analysis collects vibration data from machinery and uses the information to determine the health of the equipment. Typical problems revealed by vibration analysis include the failure of bearings, shaft distortions, imbalance, and mechanical looseness
- Ultrasonic analysis. Ultrasonic analysis uses sound to identify problems with equipment. Ultrasonic acoustic detectors detect wavelengths of sounds which are inaudible to the human ear to reveal leaks, mechanical faults in motors or gearboxes, and problems in electrical environments like arcing and corona
- Infrared thermography. Infrared thermography uses a thermal imaging camera to measure the invisible infrared radiation emitted by an object. The greater the amount of infrared radiation, the higher the temperature. Infrared thermography demonstrates when an asset is becoming overheated and can be used for checking electrical and mechanical faults on motors, inspecting bearings, and monitoring refractory insulation
- Oil analysis. Oil analysis assesses oil to check viscosity, level of additives, and contamination, allowing engineers to see if a machine is correctly lubricated. Oil analysis can also help determine if there is mechanical wear if particles of metal are found in the oil or if there is evidence of corrosion
- Motor circuit analysis. Motor circuit analysis enables engineers to determine the health of motors by revealing electrical imbalances and the degradation of insulation
- Pressure analysis. Pressure analysis continuously monitors pressure levels in real time for spikes or drops in pressure that may indicate problems with equipment
Combined Use Case
Time-based maintenance and condition-based maintenance can be used together to develop a maintenance regime more effective than either TBM maintenance or CBM maintenance alone.
For example, if you only use condition-based maintenance you may not benefit from the efficient working practices inherent in planned maintenance. On the other hand, if you only use time-based maintenance, you may still experience machinery failures because current condition is not assessed.
Time-based maintenance has several advantages. It tends to result in an organised approach to maintenance work, proper record-keeping of maintenance activities – whether in a computerised maintenance management system (CMMS) or elsewhere – and efficient use of technicians, which cuts labour costs. Other benefits include a better health and safety regime and improved productivity.
Because time-based maintenance is scheduled at an optimum time, the faults identified by a condition monitoring system can also be fixed in these windows without disrupting production. In this way, the two systems – time-based maintenance and condition-based maintenance – can complement each other.
Condition-based maintenance does not prevent failures, but helps to identify equipment that may be failing. This gives engineers the opportunity to plan a repair ahead of time before the machinery breaks down. When failure of equipment is known to be imminent thanks to condition-based maintenance technologies, there is advance warning, enabling replacement parts and anything else needed for the repair to be obtained, too.
In this way, time-based and condition-based maintenance approaches can work together. These two differing maintenance strategies have a lot to offer the engineer in combination.
Want more information on lubrication and maintenance? Look here.
Related Articles
Related links
- From condition monitoring to condition based maintenance
- Create a winning strategy for condition-based maintenance
- A Guide to Predictive Maintenance Strategy
- Condition Monitoring: What Happens & When
- Avoid disruption: planned versus unplanned rail maintenance
- Measuring maintenance
- Effective maintenance planning
- Maintenance and Automation