- Published 23 May 2024
- Last Modified 23 May 2024
- 8 min
Optimising Process Manufacturing
In this guide learn about the unique challenges faced in process manufacturing and how to optimise output and excel in that environment.
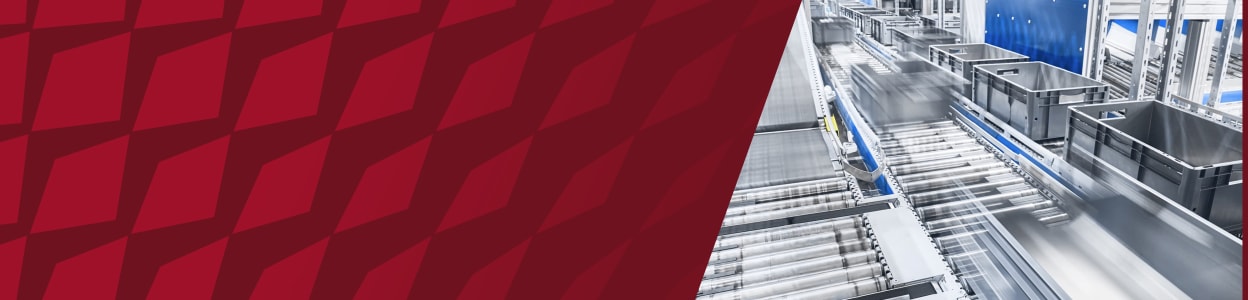
Reviewed by Stephen Bettles, Technical Support Engineer (April 2024)
Consistently having quality food, beverages, clothing, fuel, and medicine products available takes carefully optimised process manufacturing. From managing the raw material supply chain to meeting industry regulations to tailoring critical process parameters, optimising process manufacturing efficiency is a challenging but achievable goal. This guide will outline the trials that process manufacturers face and the methods and innovations they use to overcome them.
What is Process Manufacturing?
Process manufacturing produces goods by following recipes or formulas to mix and change raw materials into a new state from which they usually cannot be changed back. The key difference in process vs discrete manufacturing is that the latter involves assembling discrete parts and retaining the ability to take them apart again.
Many products begin with process manufacturing:
- Processed foods
- Beverages
- Paint
- Plastics
- Metals
- Textiles
- Petroleum fuels and lubricants
Repeatedly producing these consumer products at acceptable quality levels takes careful control of critical process parameters and raw materials. Integrating and tailoring these within a strong process control system is a starting point for optimising process manufacturing.
Challenges in Process Manufacturing
Optimising process manufacturing has unique challenges not seen in discrete manufacturing.
- Regulations: In the interests of safety, process manufacturing products must meet regulations such as food safety and hazardous material handling standards. This creates benchmarks manufacturers must hit for product quality, packaging, storage, and transportation. Distributing to multiple countries’ regulations compounds this challenge
- Quality Control: A strong quality control system helps with meeting regulations, and it applies to other challenges, such as raw material consistency. Consistently delivering the same high-quality product to consumers is difficult when at any time the raw materials could arrive in a poor-quality batch. Scheduling and seasonality also add to this uncertainty. Strict systems for sampling and inspecting batches can help assure product uniformity
- Traceability: Quality control also plays a role when product defects require recalls. Tracking what materials a batch received and where the batch was sold is essential for mitigating these issues, but it requires establishing and maintaining strong product traceability
- Perishability: Many raw materials have a limited shelf life, as do the products they’re made into. This necessitates careful materials management to prevent delivering poor or spoiled goods and to avoid business losses due to expired inventory
- Material Waste: Spoilage makes material waste losses an even greater concern in process vs discrete manufacturing. Waste minimisation is also vital in batch mixing, separating, shaping, and packaging. Additionally, material waste residue can lead to odours, equipment degradation, and health concerns, so process manufacturing can require frequent deep cleaning
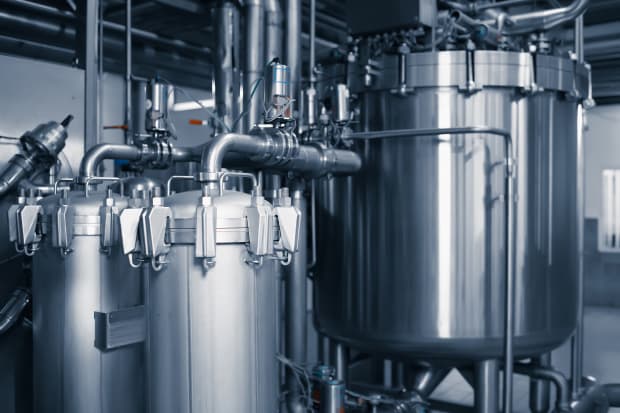
Benefits of Optimised Process Manufacturing
Surmounting these varying challenges to optimising process manufacturing efficiency unlocks equally varied business benefits:
- Reduced Risk: With a strong process control system, you can identify the risks to your operations, mitigate or eliminate them, and rest assured, with less exposure to major losses
- Reduced Costs: Improved process manufacturing efficiency means lower energy costs, less material wastage, and less storage needs
- More Consistency: With diligent quality control checks of raw materials and optimised process control of your manufacturing, you can in turn assure your customers that they’re receiving quality products consistently
- Faster Delivery: Assessing the steps, inputs, and outputs of your process manufacturing will identify suboptimal or non-value-adding operations. Trimming the fat in those areas will improve your delivery times and make you more competitive
- Better Compliance: Optimising process manufacturing should always keep your industry’s regulations front of mind. Building your process control system around them will maintain your business’ operations, reputation, and customer satisfaction
- Gained Wisdom: As you learn your critical process parameters and how to control them to suit your needs, you’ll gain more understanding of what factors affect your business and how to address problems as they come up
Ways to Improve Process Efficiency
Raw Materials Management
Along with the materials management challenges seen in discrete manufacturing (supplier relations, inventory management, supply chain, production planning, etc), process manufacturing must also consider things like shelf life, material grade, batch management, and regulatory compliance.
To manage shelf life for orders and production batches, consider systems such as FIFO (first-in first-out), which prioritises using the oldest stock. FEFO (first-expired first-out), however, uses the stock closest to its expiration date.
Materials management in process manufacturing often requires sampling incoming product and assigning quality grades. These can be for colour, fat content, or active ingredient percentage, and they can affect the quantities of the ingredients used in individual batches.
Process manufacturers must also consider which raw materials require lot control to enable batch management and maintain traceability back through the batch’s ingredients.
Process Control
Improve your process manufacturing efficiency by identifying your critical process parameters and integrating them into your process control system. These process parameters can include:
- Temperature
- Pressure
- Flow rate
- Ingredient quantities
- Mixing time
- pH level
Set up your process control system with instrumentation and automation for controlling these parameters to your established ideal levels. Supervisory Control and Data Acquisition (SCADA) systems can manage the data collected and present it to operators for real-time analysis.
Your process control will also need fine-tuning to achieve your desired quality. A Laboratory Information Management System (LIMS) can assist with tracking samples, planning tests, and recording results to help you determine your ideal process parameters.
Batch Management
Batch management, also known as lot control, is a quality control system for tracking materials produced and delivered. For every batch of material produced, a batch management system records the process parameters (such as temperature or cooking time), ingredient quantities, ingredient traceability info (from their own batch management systems), and the recipients of the finished products. This creates traceability when recalls happen and proof that batches used established quality assurance procedures.
ERP systems with batch management functionality can optimise this by automatically recording process parameters and logging them under the batch’s identification code. These systems offer easy scaling and adjusting to ensure quality process control for varying batch sizes or brand-new products.
Proactive Maintenance
To ensure your machines reliably achieve your critical process parameters, establish a proactive maintenance plan for them rather than relying on the reactive maintenance of fixing problems when they happen.
Proactive maintenance can take a few forms:
- Preventative Maintenance: Regularly scheduled maintenance check-ups based on factors like operating hours or calendar months
- Predictive Maintenance: Using condition monitoring to detect equipment issues as they start to develop, and addressing them before they become worse
- Precision Maintenance: Training all workers to clean, operate, monitor, and maintain machines by consistently following established procedures for all tasks, and electing to perform maintenance based on the machine’s importance to the business
Tools such as Manufacturing Execution Systems (MES) and Computerised Maintenance Management Systems (CMMS) can coordinate this equipment monitoring and maintenance planning.
Regular cleaning must factor heavily into process manufacturing maintenance. Many raw materials will leave behind residue in machinery, which causes a whole host of problems including odours, health risks, corrosion, clogged machinery, and reduced performance. Schedule regular cleaning downtime for your assets and consider methods such as automatic flushing or ultrasonic cleaning.
Data Analytics
As your process control system collects ongoing data on your critical process parameters, you will need to continually evaluate how well the system is improving your process manufacturing efficiency. Assess measures implemented against things like raw materials used, energy consumed, delivery times, customer complaints, and recalls so you can see how well you are improving your systems.
One system for assisting with this is statistical process control (SPC). Statistical process control applies statistical analysis tools to process parameter data to infer the conditions for producing the best or worst quality products. This involves sampling, grouping, and plotting data within established limits, and investigating anomalous data points.
Innovations in Process Manufacturing
To stay competitive in a world of discerning consumers, manufacturers are leaning toward the innovations of Industry 4.0 to maximise process manufacturing efficiency. This includes:
- Digital Twins: These collect data from a plant’s IIoT-enabled devices to digitally recreate its operations, allowing detection of inefficiencies and developing problems. They can also predict how systems will handle early-stage, conceptual products, which lets you refine ideas and get to market quicker
- Automation: Automating control of critical process parameters means less material waste and more efficiently used energy. Automation technology can also assist with reconfiguring machinery between types of batches
- AI: Artificial intelligence can handle product quality control with greater speed and effectiveness, allowing faster output without sacrificing quality
- Blockchain Traceability: Blockchain technology is highly applicable to process manufacturing traceability needs since it allows an ongoing digital record of a product’s origin, manufacturing date, ingredient traceability, and more. This enables quickly accessed proof that products are genuine and made to expected standards
Browse RS to learn more about Industry 4.0 and how its concepts will be vital for optimising process manufacturing in the future.
Related Articles
Related links
- Maintenance Strategies in Process Manufacturing
- Five ways to tackle the challenges of food and beverage manufacturing today
- Proactive Maintenance to Optimise Machinery Lifespan
- BUSINESSES ARE EMBRACING HEALTH AND SAFETY STRATEGIES
- HOW THE HEALTH AND SAFETY SECTOR IS PREPARING FOR THE FUTURE
- Reliability-Centred Maintenance
- MRO PROCUREMENT BUSINESS PRESSURES
- Rohde & Schwarz DC Power Supply for Use with Development Labs...