- Published 11 Jan 2023
- Last Modified 9 Aug 2023
- 9 min
Screws Buying Guide
Our screws guide explains everything you need to know about the different types of screws, uses and installation.

Screws are a type of fastening which work by converting rotational motion to linear motion, and rotational force (torque) to linear force. It is a simple yet highly effective process which has led to the many different types, sizes and styles of screw available today.
In this guide, we will provide an overview of screws, explaining how they work and how to install or remove them. We will explore some of the most common types of screws in use today, and provide guidance on selecting the best type of screw for different projects, materials, and requirements.
How Do Screws Work?
In the simplest terms, screws convert torque into linear force, driving the point of the screw into the material and creating an effective mechanical hold. This linear force can be used to fasten multiple materials together and can also be used alongside a nut for added security. Screws are strong and boast increasing holding power compared to nails, yet they are also beneficial as they are typically easy to remove.
Screws have four main parts – the head, shank, thread, and point. The head is typically slotted to fit the corresponding screwdriver type. The shank connects the head and the thread, and the point is the very end of the screw which is forced into the material as force is applied. Once the point enters the material, the thread is designed to catch onto the substrate and lever the screw further into the hole.
The amount of torque a screw can generate is determined by its thread. The closer together the threads are, the more torque can be generated. This also means that more turns are needed to secure the screw.
What are the Different Types of Screw?
Many screws feature slotted heads, enabling easier access for screwdrivers. However, there is an extensive variety of different types of screws available, each best suited to varying purposes, environments, and applications. Additionally, screws can be further categorised by head type, drive type, length, diameter, and material or finish. Despite this, screws are mainly distinguished by their thread type and head shape.
Some of the most common types of screw are explained in the sections below:
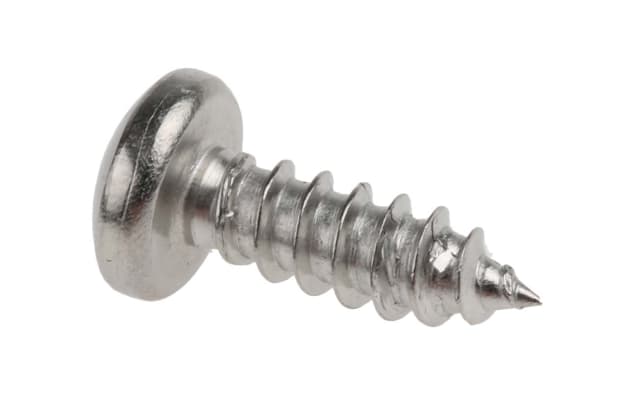
Self-Tapping Screws
Self-tapping screws are designed so that the screw itself creates the thread as it is being screwed into the material. The process of the thread cutting into the receiving material ensures a strong, tightly-fitted thread. These screws are available in various lengths to suit different project requirements.
They are primarily intended to be screwed into softer materials including wood, plastic, and sheet materials like 1mm-thick steel. As a result, self-tapping screws are best suited to lighter duties and they are frequently used in applications such as air conditioning units, where install and removal are often regular occurrences.
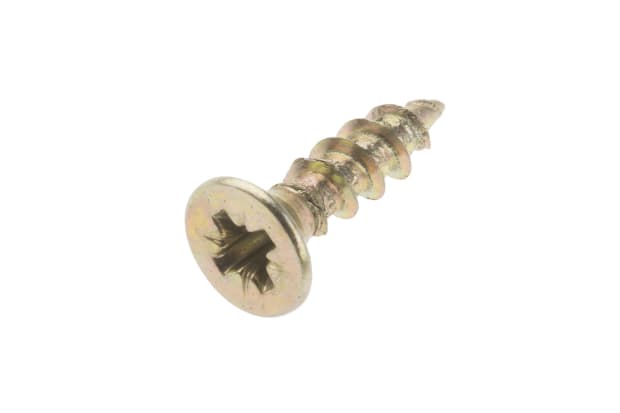
Wood Screws
Wood screws are designed to attach two pieces of wood together. They are typically made from metal and are available in various gauge sizes. Wood screws feature a tapered shank and a sharp point to dig into the wood. They are commonly available with a range of different head types including flat, pan, and oval heads.
It is recommended to drill a pilot hole before inserting a wood screw as this will enable easier fixing. Commonly found in a range of different settings and environments, wood screws are one of the most popular types of screw available.
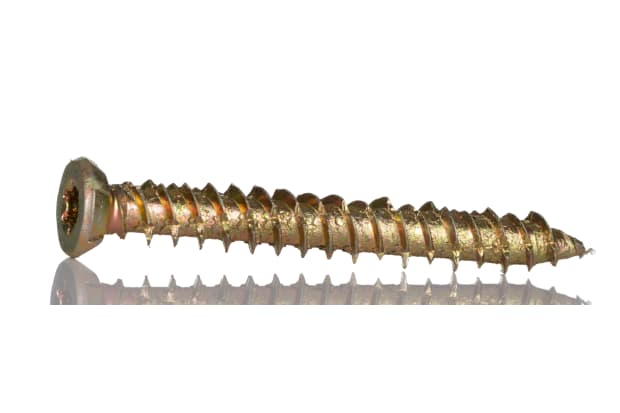
Masonry Screws
A masonry screw is a variety of self-tapping screw suitable for use with a range of materials including brick, concrete, block, mortar joints, and CMU (concrete masonry units). They are typically manufactured from carbon steel or stainless steel and many also feature a corrosion-resistant coating.
Sometimes also known as concrete screws, masonry screws are specifically designed to suit tougher materials and more heavy-duty applications. They are fully threaded and tend to feature a deeper thread than many other varieties to ensure greater resistance once installed.
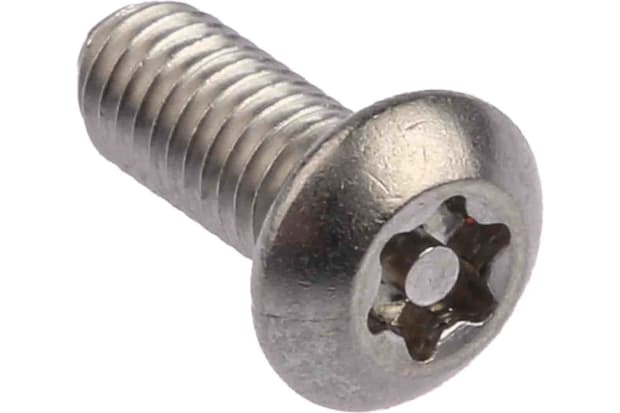
Security Screws
Sometimes also known as tamper-proof screws, security screws are similar in appearance to standard screws. However, the key difference is their unique head shape which makes security screws nearly impossible to remove with common tools.
This design ensures they are protected against removal or tampering, ideal for use in settings where this could be problematic. As a result, specialist tools such as torx keys and drivers are needed to remove security screws.
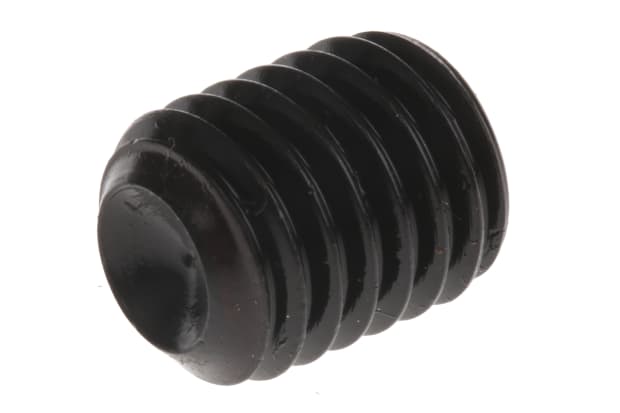
Grub Screws
Grub screws are a type of threaded fastener, typically used for securing components in place. They are usually used to fix two or more parts together, by holding one component tightly against or inside the second surface, for instance.
Sometimes also known as set screws or socket set screws, grub screws operate using a pinning action which pushes one surface against the other. This creates a compression force which holds the components tightly together. This unique approach is the primary difference between grub screws and standard screw types.
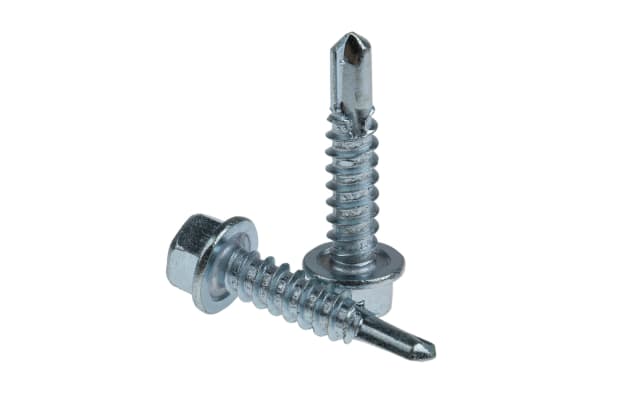
Self-Drilling Screws
Self-drilling screws are like self-tapping screws. However, the key difference is that self-drilling screws feature a sharp point at the end of the screw. This is similar in appearance to a drill’s point.
Self-drilling screws work by drilling their own hole into the material without needing a pre-drilled pilot hole. They then form the mating threads in a single operation. Ideal for use with materials including wood and metal, self-drilling screws are often used in applications such as roofing.
How to Safely Insert and Remove Screws
Screws are relatively straightforward to use, but safety is paramount and should not be overlooked. It is also important to install screws correctly to ensure the fixing is strong and reliable.
Follow these steps to safely insert a standard screw:
- Choose a screw that is the right type and length for the application
- If you are screwing two components together, place them in position
- Mark the spot on the material where you want the screw to be installed
- If your screw needs a pilot hole, use a drill and standard bit to drill the hole
- Insert the screw into the pilot hole (if applicable) and use a screwdriver to tighten
The steps below explain how to safely remove a standard screw:
- Use a screwdriver to unscrew the fixing from the material
- Make sure to choose a screwdriver which corresponds to the screw’s head shape
- Once the screw has been loosened, you should be able to pull it out by hand
- Remember to take care as removing screws may result in loose components
How to Choose the Right Type of Screw
As there are so many different types of screws, selecting the most suitable fixing for the job can be challenging. There are several important elements to consider, and knowing the specific requirements for the intended task will also help to determine the best screw type.
Material
The material you will be screwing into will play a significant role. Some types of screws are ideally suited to specific materials, such as wood screws, while others are more general-purpose. You should also consider the material’s thickness as this will dictate the required length of screw you will need.
Size
The screw you are using needs to be the right size for the material and application. Screws should not be too long, as this could result in the screw passing all the way through the material. Screws that are too short should also be avoided as this could compromise the strength of the fastening. Lastly, the diameter of the screw should be considered, as thicker screws may split more delicate materials while thinner, smaller screws could be bent out of shape by more heavy-duty components.
Drive Type
There are hundreds of different screw drive types, but the most common drives include:
- Phillips
- Torx T and TX
- Hex
- Hex socket
- Security hex socket
- One-way
Slotted drives are the most common. They simply feature a single slot in the head of the fastener and can be driven by a standard flat-bladed screwdriver.
FAQs
What is the Best Way to Remove Rusted Screws?
Rusted and corroded screws can be commonplace, especially with older screws or those which have been left outdoors in extreme conditions. There are several ways to remove rusted screws, and the effectiveness of each will depend on the severity of the rust and the condition of the screw itself.
- Use a hammer to strike the screw’s head, loosening the rust. You can then apply a lubricant or rust penetrant, leave it to work, then return and try to remove the screw again
- If you have utilised the above method but the rusted screw is at risk of being stripped, you may need to re-cut notches into the screw’s head to give the screwdriver better grip. Note that proper safety guidelines should always be followed if you choose this method
- Apply localised heat to expand the screw head, then quickly cool with water to contract, break the rust’s bond, and cause it to crack away. This may take several attempts to be successful and heat should only be used if the material surrounding the screw is non-flammable
What is the Best Way to Remove Stripped Screws?
Stripped screws occur when the screw’s head has become damaged and screwdrivers struggle to grip the head well enough to remove it from its location. As a result, they can be difficult to manage and remove.
The following methods may help remove a stripped screw:
- The simplest method is to tap a screwdriver into the screw head, helping to improve grip
- A specialist screw extractor is ideal for the task, as they are counter-threaded to screws and designed specifically for this purpose
- Use an impact driver to loosen the screw enough to then remove manually or with a screwdriver. Just be careful not to accidentally tighten it instead!
- If the screw is not countersunk, you could try to remove it by gripping the head with pliers