- Published 16 Jun 2023
- Last Modified 9 Aug 2023
- 8 min
Hydraulics and Pneumatics Guide
Hydraulics and pneumatics are systems that use air and liquid to convert force into usable energy for machinery.

From industrial machinery to entertainment and road vehicles, both hydraulic and pneumatic systems feature in everyday life. In this guide, we will outline the differences between the two, their advantages, how they work, and some examples of where these systems can be found.
What is the Difference Between Hydraulics and Pneumatics?
Whilst both hydraulic and pneumatic systems feature heavily in day-to-day life, there are fundamental differences between the two systems.
The most obvious difference between the two is the fluid they use to operate their systems. Whilst hydraulics rely on creating energy from pressurised liquid, pneumatics use filtered and pressurised air to make their systems work. Most pneumatics use pressurised air, dry or lubricated.
Other differences include the applications where these systems are utilised. Pneumatics are more commonly used for lower pressure needs, as gas is more compressible than liquid. Pneumatics are primarily used for shock absorption. This is partially because air is easy to compress and works effectively within a pneumatic system to absorb shock. Most of the time, pneumatic systems operate with a pressure of around 100 psi. This is generally quite low but works well for the various applications and tools that use it. Hydraulic systems are better for heavy-duty tasks as they are more robust and operate at higher psi.
Also, hydraulic systems are more costly to install and maintain, due to their complexity. This is mainly because the fluid is contained in a closed system. This differs from pneumatics, as they can draw in air from outside and compress it, then release it when it is no longer needed. This makes them a more sustainable and budget-friendly option. However, some pneumatic systems contain air in a reservoir that’s compressed to a higher degree than the air outside. This makes it more of a closed system, albeit one that’s easier to re-pressurise if necessary.
Pneumatics work on end effectors which could be something as simple as a common cylinder. This is generally one of the first things people think about when it comes to pneumatics. However, it could also be something more complex and specific to different types of applications. For example, it could be air springs, vacuum systems, grippers, and more.
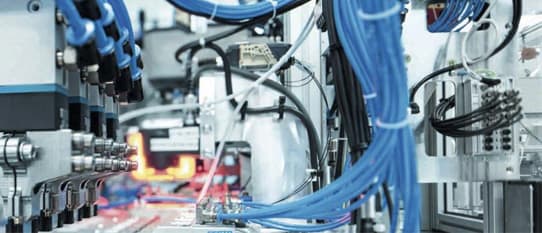
What is a Hydraulic System?
Present in multiple industries and in a wide range of applications, hydraulic systems play an active role in the function of many machines and processes. To function effectively, hydraulics use the force generated from pressurising liquids to power machinery.
Hydraulic systems are a long-standing feature in industry and date back to the 1700s. In 1795, the hydraulic press was invented by English locksmith and inventor Joseph Bramah. Hydraulics are now used in cranes, construction vehicles, pumps, and industrial applications.
Hydraulics is an area of engineering that deals with liquids, and how to use liquids to create mechanical actions of some sort. Many people consider hydraulics a liquid form of pneumatics, but it is more complicated than that. Hydraulic engineering and science can be very complicated, as fluid properties are far different from the properties of a gas, such as air. Hydraulics use more psi, typically between 3,000 and 5,000 psi. As mentioned, pneumatics only uses a fraction of this amount of psi.
How Do Hydraulics Work?
As previously mentioned, hydraulics use the movement and pressurising of liquid through valves and converting the force and pressure created from that into energy that operates the machinery.
Hydraulics work on the principle that a liquid will not change its volume if it is compressed. If it is pressurised by forcing the piston forwards, instead of losing volume (as is the case with air), the pressure will act in all directions within the system, which means it can be used to force a separate piston to move. It’s how a single push on a car’s brake pedal can force all four brakes to apply with equal force.
A hydraulic system has many parts working together, starting with a reservoir that holds hydraulic fluid, valves that allow the fluid to enter a hydraulic pump, a cylinder and a motor that powers the hydraulic pump. When functioning, the motor powers a pump which then pressurises and pushes hydraulic fluid through the valves. The energy generated from the pressure and movement of the fluid is then converted into mechanical and usable energy by the cylinder. The valves of a hydraulic pump can also release excess pressure created if needed.
Examples of Hydraulic Systems
Whilst all hydraulic systems work in the same way and contain similar components, there are different types of hydraulic systems, depending on their intended purpose. The first type of system and the arguably most commonly known system is the hydraulic pump.
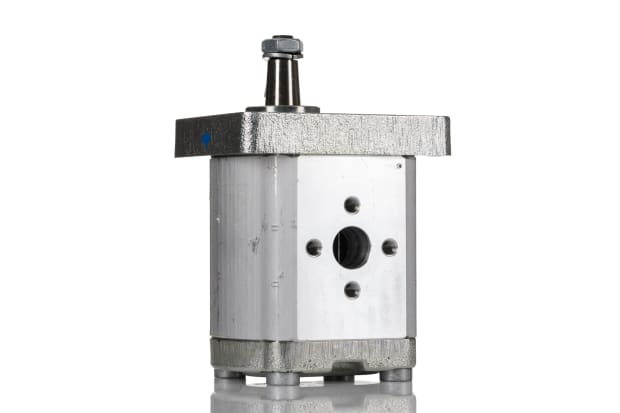
Hydraulic Pumps
These pumps come in the form of variable displacement pumps and fixed displacement pumps. Fixed displacement pumps are usually operated by gears and are referred to as fixed because they produce the same amount of energy every time they are used. This contrasts a variable displacement pump as the amount of liquid pumped and energy produced can be amended whilst the pump is running.
Hydraulic Motors
The second type of hydraulic system used is a hydraulic motor. These are systems that use the energy created from the fluid to create movement in a specific direction. Specifically, they turn the energy created from the pressurised liquid into torque.
An open-centre hydraulic system is another example and uses directional valves to control the movement of liquid to create usable energy. There is less heat generated from this system, and the air bubbles created from the liquid are released when the liquid returns to the reservoir.
Closed-Loop System
A final example of a hydraulic system is a closed-loop system. The main difference with this system is that it contains an extra pump to control the direction and displacement of the liquid. Because two pumps are involved to control the energy generated from the liquid in a hydraulic system, the energy and power created from the system can be very precise.
What is a Pneumatic System?
In a pneumatic system, it is the air that is used to create energy through movement and power machinery. Pneumatic systems are used in a huge range of applications and industries. Systems can be found in musical instruments such as pipe organs, jackhammers, nail guns and buses. They can also be found in heating systems and air conditioning systems.
Over the past few years, users have had far more control over pneumatic systems. By coupling better components, better tools, and electronics with pneumatic systems, technology has improved. Pneumatic systems and tools today are comparable to many high-end electronic automation systems.
How Do Pneumatic Systems Work?
Like hydraulic systems, pneumatic systems have several components to make them work and produce energy, and the first of these is the valve. The valves are designed to control the direction and the force of the flow of air in the system, and they can also be used to vent the system when needed.
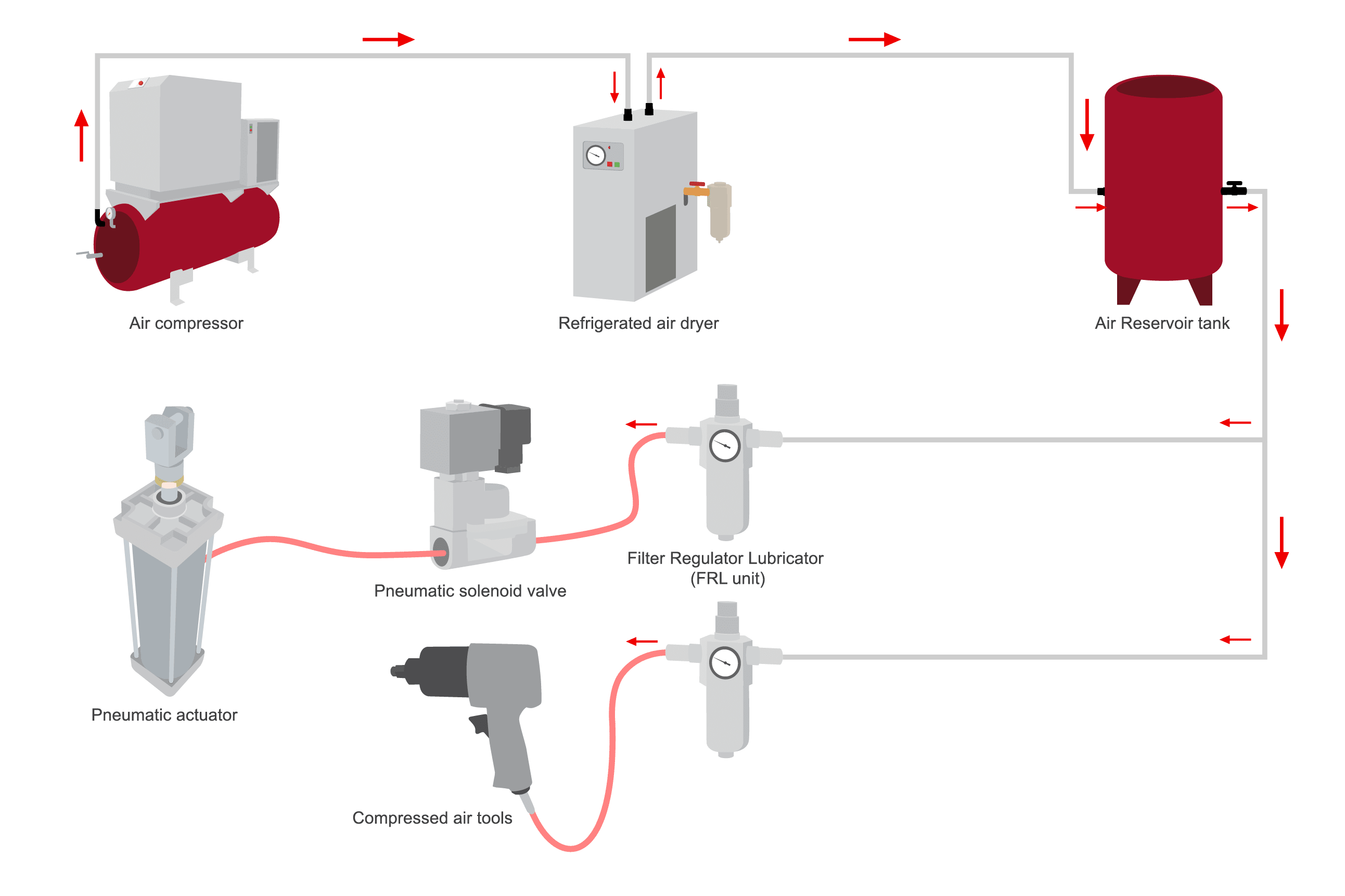
The second component of a pneumatic system is a cylinder, which is also sometimes referred to as the drive. These are the parts of the system responsible for converting the force into movement or kinetic energy.
The next part of a pneumatic system is the tubing or hose, which is where the air travels through the system. Hoses are reinforced and are used for high-pressure situations, whereas tubes are used for low-pressure situations or tasks. Both rigid and flexible tubing and hosing exist for pneumatic systems, though flexible hosing and tubing are the types more commonly used.
Ensuring the air used in the pneumatic system is clean and doesn’t damage parts of the system is of vital importance, and this is monitored and maintained with the addition of an air preparation stage. In a pneumatic system, the air preparation is responsible for filtering debris out of the air, drying and regulating the air in the system.
Another component of a pneumatics system is vacuum technology. This is the component that pressurises the air to force it through the system. The pressure of air in this type of system is significantly lower than the pressure of open air, and it is this pressure that helps create the transferable force.
Silencers are also useful in a pneumatics system. They are responsible for reducing the excessive noise made by forcing out pressurised air. The silencers reduce the sound, making the environment safe and comfortable for those close to a working pneumatics system.
Examples of Pneumatic Systems
Pneumatic systems are a staple part of all areas of life, and examples can be found in many applications. The technology is useful in material handling, robotics, medical science, entertainment, and more. Some amusement parks use pneumatic systems to control their rides, and trucks and trains contain pneumatics in their air brakes and exhausts. Pneumatic systems can also be found in automated production equipment, exercise machines, pressure regulators and sensors, vacuum pumps, pneumatic tires, power tools, and dentists' drills.