- Published 12 Jan 2024
- Last Modified 29 Jan 2024
- 8 min
A Guide to Hydraulic System Maintenance
The components of a hydraulic system require regular attention to avoid large-scale hydraulic machinery breakdown and unplanned downtime. Predictive and preventative maintenance approaches are proving their worth as best practices for the maintenance of hydraulic systems. Read our guide to learn more about hydraulic components and how to maintain them for superior performance.
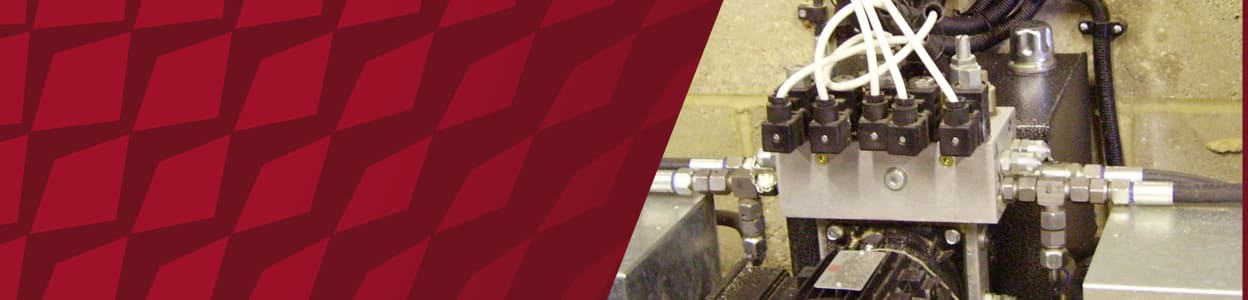
Reviewed by Osman Hafeji, Technical Support Engineer (November 2023)
Hydraulic systems are widely used in industry. They rely on transferring hydraulic fluid from one part of a hydraulic system to another to generate power. Examples of where hydraulics are used include hydraulic lifts, jacks, and brakes. Hydraulics are also widely used in construction machinery such as forklifts, cranes, and bulldozers.
Maintenance of hydraulic systems is crucial to prevent breakdown. For example, maintenance can prevent leaks of hydraulic fluid, which could cause machinery to fail. Maintenance of hydraulic systems can be reactive, preventative or predictive. Read on to learn more about how to maintain hydraulic systems and hydraulic system maintenance best practices.
Let’s start by looking at why it’s important to maintain hydraulic equipment.
Why it's Important to Maintain Hydraulic Equipment
Hydraulic equipment needs maintenance just like other industrial machinery. Maintenance helps prevent the breakdown of hydraulic equipment. If a hydraulic machine fails unexpectedly, it means lost production and productivity, and increased costs. Maintenance checks that take just a few minutes can help prevent this.
Safety is also a factor. The sudden release of pressurised hydraulic fluid from a machine can be dangerous. Hydraulic components are also often very heavy. Their unexpected or unplanned movement is capable of causing severe injury.
Industrial Hydraulic System Examples
Hydraulic machinery uses fluid power to perform tasks. Principles of hydraulics are based on a law developed by French mathematician and physicist Blaise Pascal, which states that a change in pressure anywhere in an incompressible fluid within a fixed boundary transmits that change throughout that boundary equally. Hydraulic fluid is typically pumped to hydraulic motors and cylinders to perform work. Valves control the hydraulic fluid and distribute it through pipes, tubes, or hoses.
Heavy construction machinery is an example of industrial hydraulic equipment. Loaders and forklifts use hydraulics to generate lifting power. In manufacturing, hydraulics are widely used in robot arms, conveyors, packaging equipment, lifts, and for the processing of materials. Hydraulic systems are attractive to manufacturers because of their ability to move very heavy loads, their level of control, and because they use fewer moving parts than some mechanical and electrical systems, which can make them easier to maintain.
What to Consider with the Maintenance of Hydraulic Equipment
Because hydraulic equipment relies on fluids rather than mechanical or electrical parts, it can be tempting to think it can run forever, or with very little need for maintenance. This notion is erroneous. For example, dirt can cause big problems with hydraulic systems and lead to failure. Major expenses can thus be avoided by keeping hydraulic systems clean.
Dirt degrades hydraulic fluid and the components of a hydraulic system. Abrasive dirt particles can damage the parts within a piece of hydraulic machinery. Dirt can also cause internal leakage, lower the efficiency of pumps, motors and cylinders, and lead to corrosion and components sticking. Keeping hydraulic systems clean can prevent the majority of these faults.
Many hydraulic parts need to be replaced from time to time due to general wear and tear. It is better to replace these promptly (preventative maintenance) than to wait for a hydraulic system to fail completely and then replace a component (reactive maintenance). Oil is an important part of hydraulic systems. Running unclean oil in a hydraulic system can damage it. By contrast, maintaining oil correctly extends the lifespan of hydraulic pumps, valves and cylinders.
Key points to consider when maintaining a hydraulic system include:
- Filter replacement: Replace filters as per manufacturer guidelines to prevent contamination and ensure clean fluid circulation
- Seal inspections: Check and replace damaged seals to prevent fluid leaks and maintain proper pressure levels
- Temperature control: Monitor system temperatures and use coolers or heaters as necessary to prevent overheating or cold-related issues
- Inspection of hoses and fittings: Regularly inspect hoses and fittings for wear, corrosion, or damage. Replace them if needed to prevent leaks
Types of Valves Used in Hydraulic Systems
Hydraulic systems need a variety of valves to function. The main types of valves are:
- Directional control valves. A directional control valve in a hydraulic system transfers the fluid in a certain direction
- Pressure control valves. A pressure-reducing valve in a hydraulic system keeps pressures at the correct level within it
- Flow control valves. A flow control valve in a hydraulic system controls the flow rate or pressure of a fluid
Types of Oils Used in Hydraulic Systems
In all hydraulic systems, pressurised hydraulic fluid is used to drive machinery. There is a wide variety of non-compressible hydraulic oils used as the fluid. These typically consist of a base oil combined with additives. For example, these chemical additives may help prevent corrosion of components of hydraulic systems.
Mineral-based hydraulic oils are the most widely used type of hydraulic oil. They are derived from crude oil, and used in applications such as mining, construction, and forestry. In damp environments, they can help guard against rust.
There are also synthetic hydraulic oils available, which are precision-engineered and more expensive but offer superior fluid stability and lubricity. Meanwhile, engineers looking to increase the sustainability of their operations may want to turn to vegetable-based hydraulic oils, which are derived from materials such as rapeseed and canola. These oils are comparable in performance to traditional mineral-based oils.
Types of Reservoirs in Hydraulic Systems
Hydraulic equipment has a reserve of fluid known as a ‘hydraulic reservoir’. Its purpose is to hold a certain volume of fluid, provide cooling to the system, and help release air or moisture. Reservoirs come in two types – pressurised and non-pressurised. Their size varies depending on the fluid level changes during the system's operation. The hydraulic reservoir functions as a radiator by dissipating heat and helps trap contaminants so they don’t damage the machinery. The hydraulic reservoir also removes entrained air from the fluid.
Hydraulic System Maintenance Best Practices
Best practices for hydraulic system maintenance include:
- Adherence to manufacturer guidelines: Follow the manufacturer's maintenance recommendations and schedules for specific components and the system as a whole
- Employee training: Train personnel in proper maintenance procedures and provide them with the knowledge to identify and address potential issues
- Record keeping: Maintain detailed records of maintenance activities, including fluid changes, component replacements, and any repairs performed
- Scheduled inspections: Implement a regular inspection schedule to proactively identify and address potential problems before they escalate
Preventative maintenance is another form of maintenance best practice for hydraulic systems. Preventative maintenance maintains hydraulic machinery according to a strict schedule and a hydraulic system risk assessment. This also includes following maintenance instructions from the manufacturer of the hydraulic equipment. Maintenance should be carried out frequently, and each maintenance task should be readily understood by all technicians.
An example of a preventative maintenance task might be cleaning the inside and outside of a hydraulic reservoir, or checking tubes, hoses and pumps for wear and tear as part of a hydraulic hose management system. Carrying out preventative maintenance effectively should be enough to eliminate the majority of failures of hydraulic systems.
Predictive maintenance is also beneficial for hydraulics and provides a way of preventing problems growing in hydraulic systems. Condition-monitoring technologies such as vibration monitoring and thermography can be used to help identify faults before they become serious. The engineer can then intervene to fix the issue. Other networks of sensors can also monitor the cleanliness of oil and the level of oil in the hydraulic machinery reservoir, along with fluid temperatures and pressures. Understanding these parameters enables maintenance teams to make changes early on and at minimum expense.
Both preventative maintenance and predictive maintenance are superior to reactive maintenance – waiting for hydraulic machinery to fail and then fixing it, often at great expense and with lost productivity and efficiency.
Some useful troubleshooting techniques for hydraulic system maintenance include:
- Identifying and addressing leaks: Trace and repair hydraulic fluid leaks promptly to prevent damage and maintain system integrity
- Noise analysis: Investigate and address unusual noises as they can indicate issues such as cavitation, air ingestion, or component wear
- Vibration analysis: Monitor vibrations to detect problems with pumps, motors, or other components. Take corrective actions if required
- Pressure and flow testing: Regularly test pressure and flow rates to ensure they align with system specifications. Make adjustments if necessary
Maintaining hydraulic fittings and tubing can often be achieved by simple actions such as cleaning or checking oil or the level of fluid in the machinery reservoir. Carry out these maintenance basics, and enjoy the benefits of improved performance and longer machinery and component lifespan.
Regular and proactive hydraulic system maintenance is crucial for longevity, reliability, and optimal performance. By adhering to preventative maintenance techniques, troubleshooting effectively, and implementing best practices, businesses can minimise downtime, reduce costs, and maximise hydraulic system lifespan.
Learn more about RS’ range of hydraulics products here.