- Published 16 Jul 2024
- Last Modified 16 Jul 2024
- 8 min
Safely Operating Industrial Conveyors
Learn about safely operating industrial conveyors - the hazards to keep in mind, safely working around them, and the regulations for conveyor safety.
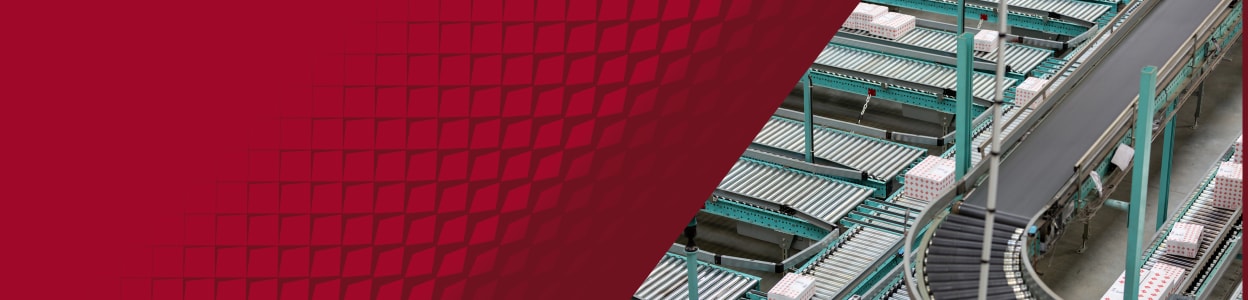
Reviewed by David Carmichael, Solution Engineer (June 2024)
Industrial conveyors have worked wonders in business efficiency since the days of the first assembly lines, but they exhibit many serious safety hazards. The heavy moving masses of conveyed material and the small gaps between high-speed conveyor components need careful guarding and avoidance to keep conveyor workers safe. Read on to learn best practices for achieving and maintaining conveyor safety.
Conveyor Safety Hazards
Nip Hazards
Conveyor hazards begin with their high-speed components that move in close proximity: conveyor rollers, belts, drums, and pulleys. All these present nip points (or pinch points) - gaps next to moving components that can easily and instantly draw a loose body part in and fiercely hold on. This can trap the person and cause horrifying injury or even death, with potential further injury through impact with conveyed material.
Conveyor belts safety in particular needs to consider entanglement hazards given the high speeds of belts, while roller conveyor safety needs to keep all the pinching gaps between rollers front of mind.
To work safely alongside these hazards:
- Maintain thorough conveyor guards and never remove them during operation
- Never wear loose or dangling clothing
- Tie back long hair
- Never place hands or arms near moving machinery
- When shovelling material onto conveyors, establish guarding and practices that prevent the shovel from contacting the belt
Crush Hazards
The object's conveyors transport can themselves be serious hazards, either through falling off the conveyor and hitting someone or by crushing or entrapping someone against something solid.
To stay safe from these heavy masses:
- Consider the weights of conveyed material and how severe an incident it would be for them to escape the conveyor
- Design conveyor guards strong enough to keep conveyed material in
- Pay extra attention to the load ratings of guarding used for overhead conveyors
- Exercise caution around all travelling objects
- Wear appropriate PPE such as safety footwear and hard hats when working around conveyors
Ergonomic Hazards
The hazards of some conveyors are manageable enough to allow workers to directly handle material on the conveyor. This presents a unique set of ergonomic hazards that, if not addressed, can cause musculoskeletal disorders (MSDs) over time.
Lifting items directly onto and off of a conveyor means frequently holding heavy loads out at a distance and rotating the body while holding that outstretched load. This can lead to MSDs if you do this work long-term in an uncomfortable position (by twisting, leaning, or stretching), the loads are too heavy for you, or you do this work repetitively without breaks.
To keep conveyors ergonomically healthy:
- Design the belt’s height and width around how high and far the operator has to lift and reach
- Give clearance for the worker’s feet under the belt
- Consider whether the worker will stand or sit
- Avoid obstructing the belt with skirting that the worker will have to lift over
- Design the speed and frequency of conveyed objects to allow workers to manage them at a comfortable pace
- Train workers to stand, sit, lift, and carry in comfortable postures, and institute regular breaks
The HSE has guidance on conveyor workstation design to help you create a safe, healthy, and comfortable environment for conveyor workers.
Other Hazards
With any conveyor motors, fans, lubricating fluids, and electrical equipment, be aware of their electrical, spillage, pinch, fire, and explosion hazards. Include these in the conveyor’s risk assessment, place appropriate warning signs, and install guarding as needed.
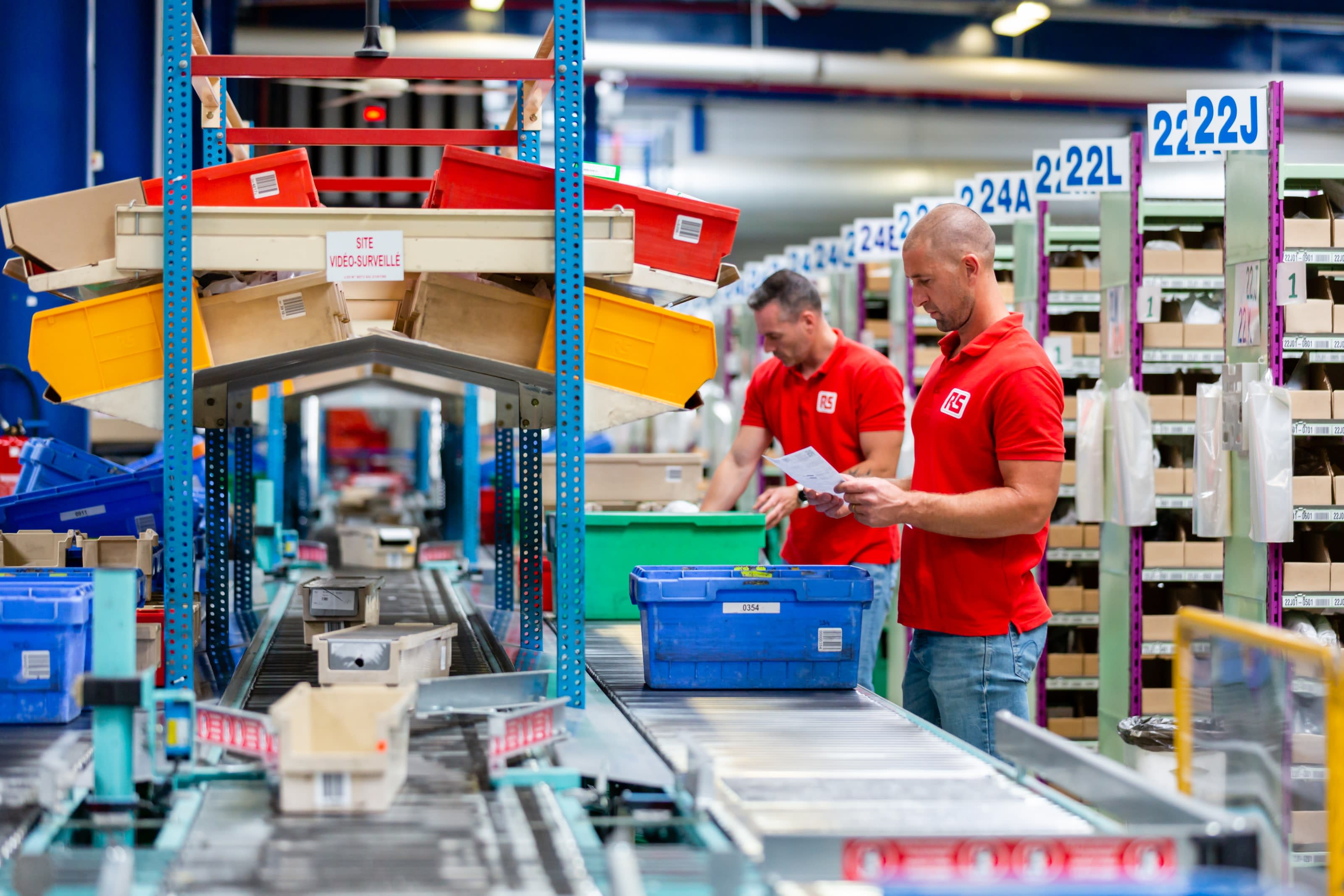
Conveyor Safety Standards
PUWER Assessment
The 1998 Provision and Use of Work Equipment Regulations place safety responsibilities on owners and operators of work equipment, such as conveyors.
According to PUWER, businesses using conveyors must:
- Configure conveyors to handle their intended loads and conditions, and only use conveyors for their intended purpose
- Inspect conveyors after installation and regularly after that to ensure their safety
- Provide training and safety information for everyone using or managing conveyors and ensure only trained people use them
- Prevent people from accessing dangerous conveyor parts, usually through either fixed or interlocked guarding
- Install and clearly identify systems for starting, controlling, and stopping conveyors, including stopping them in an emergency
- Practise thorough conveyor maintenance to keep conveyors running safely, correctly, and efficiently. This includes keeping maintenance records
The PUWER assessment requirement applies whether you’re purchasing a pre-designed conveyor system or designing and building a completely custom one. Purchased conveyors, once installed, often still lack the guarding necessary to fully satisfy PUWER. Designing new conveyor systems gives you greater control over guarding them, though this takes considerable design and manufacturing resources.
BSI Standards
The British Standards Institution also addresses conveyor safety:
- BS EN 620:2021 covers the safety and electromagnetic requirements of belt conveyors that transport loose bulk goods
- BS 4531:1986 covers dimensions for portable or mobile belt conveyors that have a containing trough above the belt
- BS EN 618:2002 covers managing hazards in mechanical equipment conveying bulk material
These standards help you maintain conveyor safety and show your due diligence for it; however, they are voluntary to adopt.
UKCA Mark
Any companies selling complete conveyors in Great Britain will need to apply the UKCA mark to them, and thus design and test the units to meet the country’s health and safety standards. It gets more complicated if you incorporate a conveyor within a larger assembly line machine that you wish to apply the UKCA mark to as a whole. This will need a detailed assessment, including documentation showing UKCA conformity for individual components in the system, like the conveyors.
Safe Conveyor Operations
Conveyor Design
The best option to deal with any hazard is to fully design it out of the system. Removing high-speed conveyor components isn’t an option in those systems, but conveyor guards can go a long way towards keeping people safe from conveyor nip hazards. Ensure you identify all nip points in the system and thoroughly guard against material escaping. Any nip guard for conveyor hazards must be strong enough for any loads it will see, including accidental human contact or moving conveyed objects coming loose.
Design emergency stop buttons or pull-cords into your conveyor system and place them within easy reach of all operator workstations. If a conveyor snags someone, they or their coworkers need to be able to shut down the conveyor quickly.
Hold-to-run controls ensure conveyors instantly stop when operators release the control switch. This reduces incident likelihood, so consider this approach if it can work with your operations.
Sensors that detect jams, malfunctions, or overloading can trigger alarms and automatically shut the system down when safety incidents happen.
Ergonomically optimise conveyor dimensions and speed to allow workers continual access without developing strain injuries.
Warning systems alerting personnel when conveyors start up help keep everyone aware when conveyor hazards are active.
Risk Assessments
Conduct a detailed risk assessment of the complete conveyor system so you can know the hazards you’re dealing with:
- Identify all the conveyor’s hazards, especially all its nip points
- Determine the ways a hazard could harm different workers. Remember that individual hazards can have multiple risks. Use a risk priority chart to plot each risk’s likelihood and severity
- Plan ways to control or mitigate each individual risk: Use a priority structure of engineering controls (guarding) over administrative controls (safe practices) over PPE (hard hats)
- Document the risk assessment’s results and put your risk controls into practice
- Regularly review the risk assessment and risk controls. A daily conveyor safety checklist can help with this
Safe Practices
Keep the following general best practices for conveyor safety in mind:
- Only allow trained and authorised people to use or maintain conveyors
- Exercise caution around all conveyed material
- Prohibit loose hair, clothing, and jewellery
- Never stand, sit, work, or ride on conveyor belts or roller tracks
- Watch for the conveyor operating incorrectly or missing guards. Include this in your daily conveyor safety checklist
- Place safety signs warning of conveyor hazards
- Set up lock-out / tag-out procedures (LOTO) when performing conveyor maintenance
- Perform conveyor maintenance regularly to ensure safe, efficient operation
Safety Training
As with any industrial equipment, proper training on its safety is essential for those operating and maintaining it. Develop detailed conveyor safety training just like you would for forklifts, etc., and ensure every individual working with conveyors receives this training:
- Stress the severity of injuries sustained from conveyors
- Show how to spot and avoid nip points
- Explain where emergency stop and LOTO devices are and how to use them
- Prohibit going under conveyors other than via designated walkways
- Encourage workers to report problems with conveyors such as operational problems or missing guards
PPE
Personal protective equipment (PPE) is your last line of defence against material escaping the conveyor. PPE for conveyor safety typically includes a hard hat, safety boots, safety glasses, and gloves, and employers must provide these to meet their safety responsibilities.
We can equip you with all the PPE you need to maximise your conveyor system safety and keep your products moving.