- Published 23 Aug 2024
- Last Modified 23 Aug 2024
- 6 min
A Complete Guide to Roller Conveyors
Roller conveyors are used in warehousing, package handling, and manufacturing applications to move materials, goods, and heavy loads safely. If you’ve ever wondered what roller conveyors are used for, and about the types of roller conveyor on the market, we’ve got you covered with this guide.
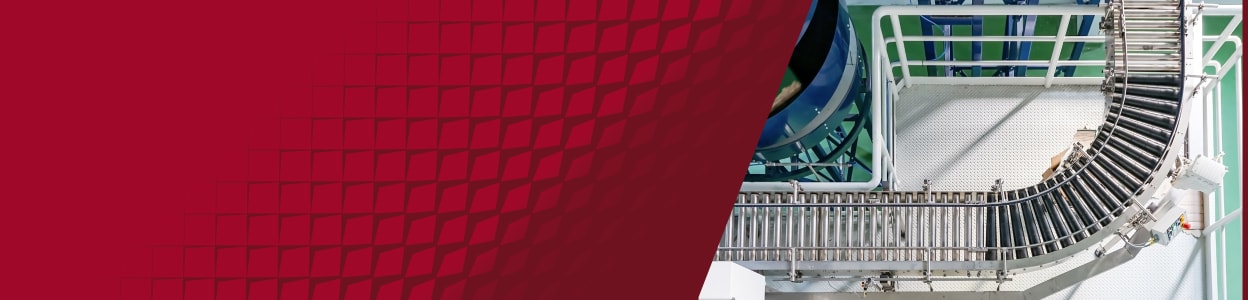
Reviewed by Osman Hafeji, Technical Support Engineer (June 2024)
Roller conveyor systems are used to move loads safely, quickly, and efficiently. They are widely used in warehousing and manufacturing. Want to learn more? Read on.
What are Roller Conveyors?
First, what is a roller conveyor? A roller conveyor consists of a series of rollers on axles mounted to a frame. Roller conveyor systems are used to move many different types of heavy and unwieldy items. One roller conveyor application we’re all familiar with is the baggage scanning system at airport security.
Roller conveyors have been a part of factory automation since the early 20th century, with the first patent awarded for a roller conveyor as far back as 1908. Roller conveyors may be made from plastic, steel, or stainless steel.
Types of Roller Conveyors
Types of roller conveyors include conveyors powered by motors (powered roller conveyors) and systems that use gravity (gravity roller conveyors). Let’s explore these roller conveyor systems and associated conveyor components further:
Gravity Roller Conveyors
What is a gravity roller conveyor? Gravity roller conveyors move loads using the natural force of gravity. The gravity roller conveyor is located on a decline. Parts or products roll down the surface to the desired location. The rollers are available in different diameters depending on the weight of the load, with larger diameter rollers generally suited to moving heavier items. Gravity roller conveyor sections come in different sizes. It’s necessary to consider the width of the gravity roller frame and whether any curved sections are needed to get the goods where you need them. Gravity roller conveyors are relatively simple types of roller conveyor technology.
Powered Roller Conveyors
Unlike their gravity roller counterparts, powered roller conveyors can be used to move products horizontally or upwards. These types of roller conveyor tend to be more expensive than gravity-based systems but more versatile, and often capable of moving heavier loads.
Powered roller conveyors typically use components such as motors, chains, belts, or rotating shafts to drive the rollers. Powered roller conveyor benefits include the ability to transport products at different speeds and cover much greater distances than gravity rollers.
Chain-Driven Roller Conveyors
The rollers on a chain-driven roller conveyor system are fitted with sprockets and driven by a chain that is powered by a motor. The chain locks in tightly to the sprockets to provide a high degree of traction. These types of roller conveyor are good for handling heavy loads, pallets, drums, tyres, and irregular shapes. Chain-driven roller conveyors can also be reversed to move goods in the opposite direction.
Chain-driven roller conveyors are just one type of powered roller conveyor. Roller conveyor belt types feature motor-driven belts driving the rollers, while other conveyors have individual motors installed in each roller. Another type of powered conveyor, the line shaft roller conveyor, is powered by a rotating shaft connected to the rollers by spools and belts.
Plastic Roller Conveyors
Plastic rollers are often used in lightweight gravity roller conveyor systems. They are good for applications such as food processing, or where the environment is humid or acidic and metal rollers are vulnerable to corrosion (such as in handling batteries). They also require less maintenance and lubrication than their metal equivalents.
Plastic roller conveyor systems may be made from rigid ABS, PVC, or nylon. Plastic rollers often produce little noise during operation. Rollers (both plastic and metal types) may also be covered in rubber, which increases traction between the roller and the goods the system is transporting.
Steel Roller Conveyors
Steel and stainless steel rollers are stronger than plastic rollers, which makes them suitable for moving very heavy items. Although steel rollers represent a higher upfront expense, they may prove to be an economical option in the long run because they require less frequent replacement. Steel rollers may also be suitable for harsh environments (transporting hazardous chemicals, for example) in which plastic roller conveyors are damaged too easily or are difficult to clean up.
Stainless steel rollers may be resistant to chemical spills or suitable for environments that have to be kept very clean, such as in food and beverage or medical manufacturing. Generally, steel rollers are more heavy-duty than plastic types and provide better wear resistance.
Benefits of Roller Conveyors
Roller conveyors are widely used in logistics and manufacturing. Roller conveyor benefits include:
- A better health and safety regime. Roller conveyor systems may make a factory safer by reducing manual handling and heavy lifting by workers
- Simplicity. Roller conveyors are typically simple to install and operate
- Efficiency. Like conveyors generally, roller conveyors help make production more efficient by quickly transporting goods around a facility
- Ability to deal with heavy loads. Roller conveyors are durable and tough – particularly steel roller conveyors – which makes them suited to handling heavy items
- Smooth, quiet operation. Roller conveyors tend to operate quietly, which can be advantageous for personnel who are working nearby
- Limited maintenance. Compared to many other forms of automation, roller conveyors require relatively little maintenance
Roller Conveyor Applications
Roller conveyor systems are usually designed specifically for the job. The conveyor typically has to operate in a specific location and may require curved sections, mergers with other equipment, or transitions between different types of conveyor. A standalone roller conveyor is simpler to design and install than a roller conveyor application that interacts with lots of other machinery.
Roller conveyor applications include airport security and baggage handling, car production, making food and beverages, and transporting products around warehouses. Roller conveyors are also widely used in the pharmaceutical industry.
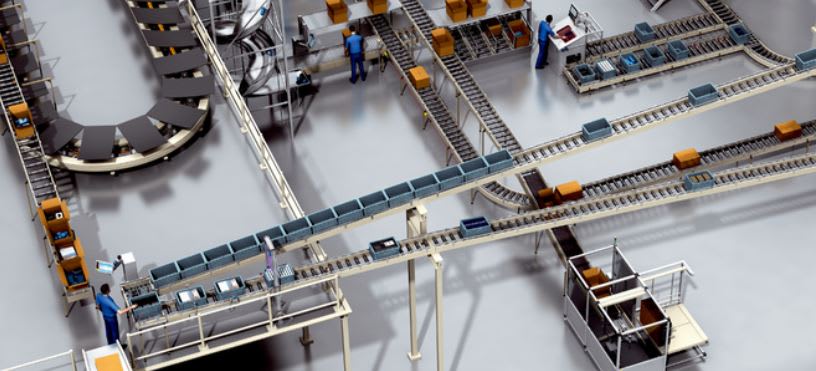
The Future of Roller Conveyors
The future of roller conveyors is bright, with the market globally forecast to be worth more than $2 billion in 2028. Materials used to manufacture rollers will evolve in the coming years, with more composites and other lightweight, strong materials employed rather than metal. In terms of motor technology, powered roller systems will benefit from energy-efficient designs that help to reduce CO2 emissions. Modular conveyor roller systems are also expected to grow in importance to make it easier to adjust roller systems to different production demands.
Finally, much like other production systems, roller conveyors are also becoming smarter through the addition of sensors that provide data that can be used for maintenance. AI will also increasingly be used to optimise conveyor performance and route items as efficiently as possible through the conveyor system.
Do you need conveyor components? We’ve got you covered. Explore our range of roller track and drive rollers.