- Published 16 Oct 2023
- Last Modified 12 Feb 2024
- 6 min
Introducing Lockout/Tagout
Machinery safety is paramount at an industrial plant. Lockouts and tagouts provide a way of isolating machinery from power – whether electrical, mechanical, hydraulic or pneumatic. Doing so helps protect workers from injury. Read our guide to find out more about what lockout/tagout is, its benefits, and the correct procedures to follow.
Reviewed by David Carmichael, Solution Engineer (October 2023)
Maintaining industrial equipment and machinery, sadly, can be very dangerous. Maintenance is necessary but carrying out maintenance without the proper procedures in place is potentially lethal. Accidents sometimes occur as a result of machinery starting up or releasing energy while it is being worked on. Regulations in the UK, Europe and the US therefore require that all energy sources are isolated while maintenance is going on.
That’s where lockout/tagout comes in. Lockout/tagout prevents accidents by isolating machinery from an energy source. Doing so prevents the machinery starting up unexpectedly and injuring workers carrying out maintenance.
What is Lockout/Tagout?
A lockout/tagout procedure is designed to prevent machinery restarting and endangering personnel. Lockout isolates an electrical, mechanical, thermal, hydraulic (or any other) type of energy source from the machine, system or process that uses it. Lockout/tagout devices can be types of padlocks, or devices designed for specific purposes, such as isolating circuit breakers or valves.
A tagout is a physical warning system – literally a tag or label placed on the energy-isolating device that lets everyone know equipment is being worked on. This prevents it from being started up unexpectedly and injuring someone. Securely fastened, the tag functions as a prominent warning device indicating the machine may not be operated until the tagout device is removed.
Why is Lockout/Tagout Important?
It’s possible that technicians or engineers performing maintenance on equipment are exposed to injury from it starting up unexpectedly or the release of residual energy by the machinery. This stored energy may come from air or water pressure, or steam, for example. Lockout/tagout is so important because it reduces the chances of harm to engineers and technicians because of incidents of this type.
Contact with moving machinery was one of the causes of deaths in manufacturing over the last year, according to the UK HSE. Simply, lockout/tagout helps prevent these kinds of accidents. Lockout/tagout procedures in Britain fall under the HSE Provision and use of Work Equipment Regulations 1998. These regulations help ensure work equipment doesn’t cause health and safety incidents. They are vital and apply to all workplaces, not just manufacturing facilities.
In short, for many sectors, servicing and maintaining equipment presents the biggest hazard to employees. By protecting workers from injury, lockout/tagout is a potential lifesaver.
Lockout/Tagout Procedures
There is a defined process for implementing lockout/tagout. It’s important that all the elements of this process are followed. If a technician fails to disconnect all energy sources or doesn’t tag a machine correctly, this can mean equipment starting unexpectedly, leading to injury. An example might include a technician who is servicing a press when another worker starts it up, causing crushing, or technicians who are injured because someone opens a valve further up a pipeline they are repairing.
The Correct Lockout/Tagout Process
Prepare for Shutdown
Preparation for shutting down machinery should take place in advance as far as is possible. However, this may not be the case if a machine suddenly fails, or emergency repairs are required. The planned shutdown should consider why the machinery needs to be taken offline, such as improving safety or reducing unplanned downtime.
You can use a computerised maintenance management system (CMMS) to record the details, such as the technicians who will be doing the work, what the job involves, how long it will take, and who will need to access the machinery.
Notify Employees
Employees must be informed that equipment is to be shut down and locked out before maintenance takes place. All workers who are affected need to be kept in the loop, either face to face in a meeting, or with a prominent notice in the location where the maintenance is due.
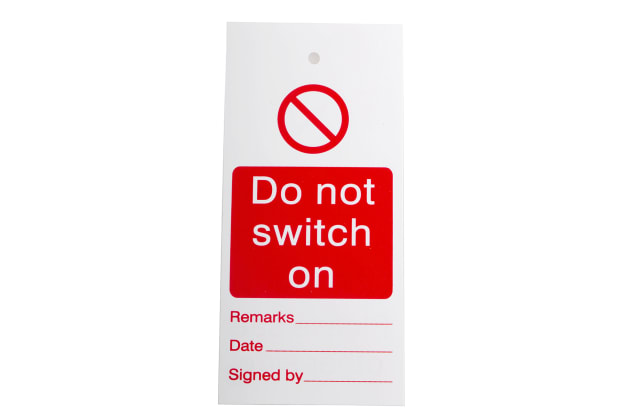
Shutdown Machinery
It’s important that machinery is turned off by a technician who is authorised to do so and understands any hazards involved. There should be an established procedure for shutdown that minimises risk.
Isolate Equipment
Equipment should be isolated from the energy source. This can take place using devices such as circuit breakers, line valves, or blocks. There may be special valves or disconnects, safety blocks on moveable parts, or pipeline blank flanges which help to isolate equipment.
Dissipate Residual Energy
Stored energy (also known as residual or ‘potential’ energy) is energy that remains in a system or machinery even when it’s turned off. When stored energy is released in an uncontrolled way, individuals may be crushed or struck by objects, moving machinery, equipment, or other items.
Residual energy is therefore a big hazard. It can be stored in many forms, such as steam, gas or water pressure, or in springs, hydraulic systems, or capacitors. It’s crucial that all residual energy is drained from equipment as part of the lockout/tagout procedure.
Apply Lockout/Tagout Devices
Now lockout/tagout devices can be applied. A lockout device will lock the energy isolating device, such as a circuit breaker, in the ‘safe’ or ‘off’ position. Safety padlocks prevent the removal of the device and energy flowing into the machinery.
Tagouts are visually prominent warning devices, Typically, a tag is securely fastened to an energy-isolating device to indicate that the machine may not be operated until the tag is removed. The lockout and tagout processes are performed at the same time. Placing a tag on a machine that is still capable of being locked out is incorrect, as is locking out a machine and not highlighting it with a tag.
Ensure Equipment is Isolated
Finally, it’s absolutely crucial that equipment is tested to check it is disconnected from the energy source. An engineer will determine no one is exposed to an energy hazard and then test the equipment by pushing an on-off button or switch to check it will not operate. Completing this step ensures machinery is ready to be serviced safely.
There are numerous benefits to following lockout/tagout procedures. The number one advantage of lockout/tagout safety is a reduction in potential harm to employees. Everyone has the right to work in an environment that is risk-free.
But there are other benefits, too. Carrying out maintenance work correctly and safely helps keep a plant productive and reduces unnecessary downtime.
In addition, enabling lockout/tagout safety avoids penalties from regulators because safety procedures haven’t been correctly followed, resulting in injury – or worse.
Check out the RS range of lockout/tagout kits here.