- Published 24 Jan 2023
- Last Modified 29 Aug 2023
- 8 min
A Complete Guide to Pressure Sensors
Our complete guide explains what pressure sensors are, how they work, and the best products available to buy.

What are Pressure Sensors?
Pressure sensors are measurement tools for detecting, monitoring, reading and displaying changes in applied pressure from a contained volume of liquid or gas. They can also be used with uncontained volumes, such as atmospheric pressure. There are various types of pressure sensors available for performing in specific roles, conditions and applications.
In this guide to pressure sensors, we will provide a clear definition of pressure sensors and a basic explanation of how they work. We will also look at several of the different types of pressure sensors for sale online in the UK, describing how and why they might be used.
How Do Pressure Sensors Work?
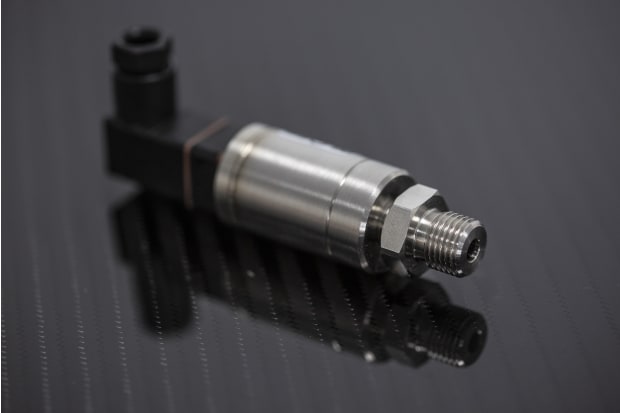
Their name offers a very simple definition of a pressure sensor - they are a type of electronic measurement device, designed for registering and recording changes in applied pressure. However, when people ask, ‘what is a pressure sensor?’, they are normally looking to find out more about how a pressure sensor works.
The basic working principle of a pressure sensor requires any proportional change in applied pressure to cause a physical reaction in the sensing element of the device.
This typically triggers the production of an output voltage, and the resulting values can then be conditioned (adjusted for environmental factors) and transmitted as analogue or digital output signals. These readings vary as further pressure changes are detected, allowing for ongoing monitoring of applied pressure over time.
There are several main types of these electronic measurement devices available to buy in the UK, including absolute pressure sensors, capacitive pressure sensors, differential pressure sensors, piezoelectric pressure sensors, and strain gauge pressure sensors.
What are Pressure Sensors Used for?
Pressure sensors are widely used in various demanding applications across a wide range of industries and sectors. Different types can incorporate many variations in core technology, features and performance levels.
Pneumatic pressure sensors measure changes in air or gas pressure, while hydraulic pressure sensors measure changes in water or fluid pressure. Different technologies for constructing these devices can result in configurations such as piezoresistive pressure sensors, capacitive pressure sensors, fibre optic pressure sensors, and strain-gauge pressure sensors.
Between them, they cover a broad array of industrial or scientific pressure measuring techniques and applications. Knowing how to use a pressure sensor will depend entirely on the type and the role you want it to perform, but some common examples of industrial pressure sensor use might include:
- Checking the applied pressure (or min/max pressure measurements) of various gases and liquids held in sealed tanks, vessels and systems. Entire tyre pressure monitoring systems, such as found in a vehicle's tyre pressure gauge, are a good everyday example of electronic pressure sensors in action
- Detecting flow rate and direction by tracking pressure changes between two or more separate locations
- Interpreting shifts in atmospheric pressure (i.e. barometric pressure) for environmental or navigational purposes
- Monitoring volumes and liquid levels via pressure exerted downward on a sensor
Transducers, Transmitters and Sensors
Before we take a closer look at the various types of pressure sensors available, we should make a quick note of the key definitions and differences between sensors, transducers, and transmitters.
Any pressure sensor device relies on changes in pressure causing a physical reaction in the sensing element. This change cannot be fed directly through to an attached circuit until it has been suitably translated and conditioned into a usable electronic signal.
The reason we need to differentiate between pressure sensors, pressure transducers and pressure transmitters is that they all incorporate a pressure sensing element, but each translates and conditions the output signal from that element in slightly different ways. Despite this, casual use of the generic term pressure sensor may refer to any of these three device types.
Pressure Sensors
A true pressure sensor works on the principle whereby a physical reaction in the sensor module produces an output voltage. Further signal conditioning - such as calibration, amplification, and temperature compensation - must be handled separately before readings are considered reliable and stable.
Pressure Transducers
The question ‘what is a pressure transducer?’ often follows from any explanation of a pressure sensor, which is understandable. Like pressure sensors, pressure transducers also produce an output voltage because of a physical reaction in the sensing element. The key difference is that some degree of signal conditioning is also handled by the transducer, allowing them to be transmitted a greater distance from the source.
Pressure Transmitters
A pressure transmitter works much like a transducer, except rather than a voltage reading, it will output a current signal across a low-impedance load (often somewhere in the 4-20mA standard industrial range).
Types of Pressure Sensors
What are the different types of pressure sensors you might need for covering a wide range of industrial or laboratory applications? The three main types of pressure sensors are absolute, differential, and gauge. The best type of sensor to buy in any given scenario will depend entirely on the specifics of your application and the types of reading you are trying to make.
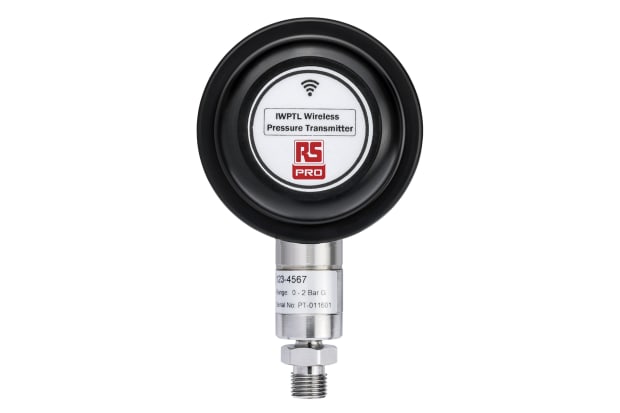
Absolute Pressure Sensors
Absolute pressure sensors are a type of vacuum pressure sensor. Their readings are always relative to zero and output values are positive, unlike others that can be positive or negative.
They are ideal for measuring air pressure in barometer-critical applications, like weather monitoring or altitude detection for navigation. Barometric pressure sensors rely on establishing a baseline value from an absolute vacuum for reliable readings.
This is vital for barometric detection as the pressure of a gas is inversely proportional to its temperature. Without a perfect vacuum as a zeroing reference, absolute pressure readings would differ with heat fluctuations.
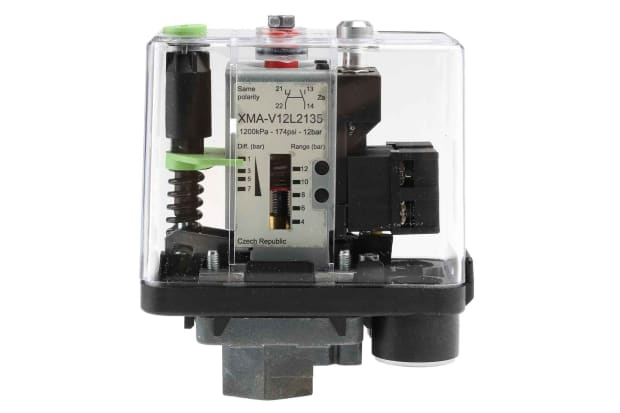
Differential Pressure Sensors
Differential pressure sensors measure pressure change between two points in a system. This is important for checking the correct functioning of various aspects of a system, such as release valves or flow rate.
Differential pressure sensor specifications vary, but most measure pressure on each side of a single diaphragm in the sensor element. The readings can either be positive or negative on either side, depending on how those pressures are deflecting the diaphragm.
Alternative setups can be created that measure pressure differential between two or more separate sensor devices, located remotely and linked via signals from their internal electronics.
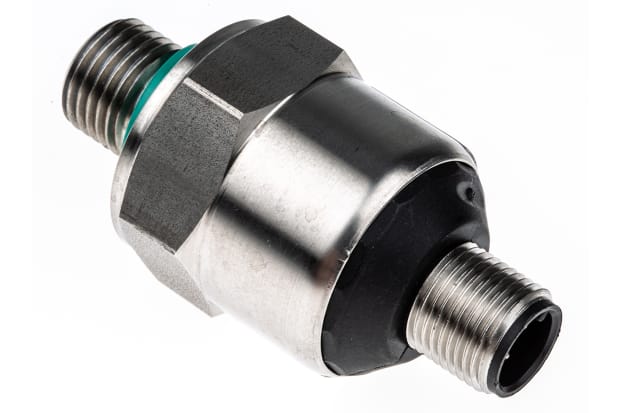
Gauge Pressure Sensors
Gauge pressure sensors are a type of relative pressure sensor. They are typically used to measure the relative difference between local atmospheric pressure, and the pressure level at a given point in another system.
Applications include checking the fluid levels of a vented tank, operating blood pressure monitors, or controlling the desired rate and power of a vacuum pump. In both cases, differences in the immediate atmospheric pressure around the system will affect the calculations and readings required.
Many gauge sensors rely on a membrane attached to a resistor or similar electronic element, which records deflection forces as a change in output value.
Pressure Sensing FAQs
What is Pressure?
Pressure is defined as the force applied to the surface of an object or medium, per unit of area across which the force is being exerted. In mathematical terms, it is a function of the formula p = F/A, where p is pressure,** F** is (perpendicular) normal force, and A is the surface contact area.
What are the Main Units of Pressure?
Since 1971, the main SI unit for pressure is the pascal, usually written as Pa. Before this, it was standard for pressure to be given in newtons per metre squared. One pascal is equivalent to one newton per square metre (N/m2). Various other non-SI ways of indicating pressure are widely used across a diverse range of applications, with common variants including bar pressure and pounds per square inch (PSI).
How Do You Test a Pressure Sensor?
There are various ways to test different functions of a pressure sensor, some of which can be quite in-depth and demanding from a technical standpoint. You will generally require access to several other tools and devices, including a pressure fluke, multifunction voltage meter with suitable probes, power supply, breadboard, and wires or jumper cables.
The core approach to any comprehensive pressure sensor test should usually involve checking for the following four key things:
- Basic function - ensuring the sensor outputs a voltage when it detects a pressure change
- Accuracy - ensuring the same sensor outputs the same reading in response to the same pressure change
- Consistency - ensuring multiple sensors all produce the identical outputs under identical conditions
- Resolution - checking that a sensor meets its minimum rated requirements for detecting very small changes in pressure