- Published 14 Feb 2025
- Last Modified 14 Feb 2025
- 6 min
Guide to Non-destructive Testing (NDT)
Non-destructive testing is used to evaluate a material, component, or structure without damaging it. This guide covers what NDT is and common techniques and applications.
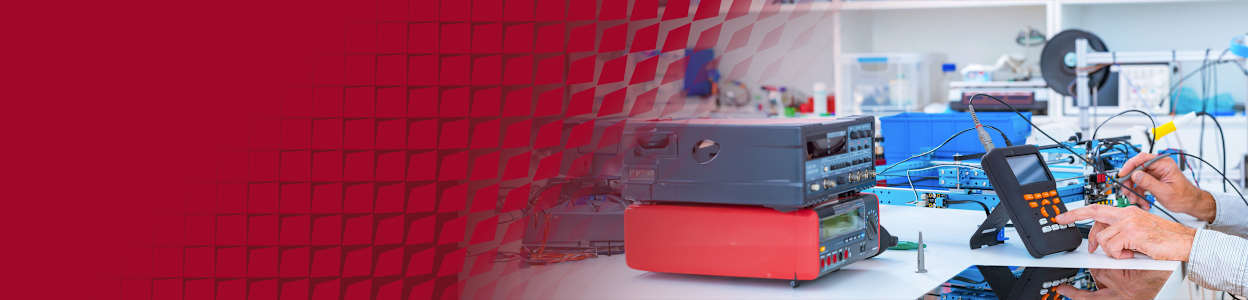
Reviewed by Osman Hafeji, Technical Support Engineer (January 2025)
If you want to assess the qualities of a material without destroying it, non-destructive testing (NDT) is the way forward. One of the main advantages of NDT is that it leaves components and materials undamaged. If repairs need to be made, the material won’t be in worse shape than the original condition. If you’ve ever wondered, “What is NDT?” or, “What is the purpose of non-destructive testing?” read on to learn more about some of the common non-destructive testing methods and applications.
What is Non-destructive Testing?
NDT is an umbrella term for a range of analysis techniques that assess the properties of a material, part, component, structure, or system. Crucially, the analysis techniques in question don’t damage the material or component that is being tested. Other names for NDT include non-destructive evaluation, non-destructive inspection, or non-destructive examination.
Eddy current testing, magnetic particle testing, radiographic testing, ultrasonic testing, dye penetrant testing and visual inspection are common NDT testing methods. NDT is widely used in mechanical engineering applications in sectors such as oil and gas, aerospace, automotive, and medicine. It is also useful in laboratory conditions for evaluating the characteristics of new products and designs and carrying out research. As well as mechanical engineering, NDT is used in both civil engineering and electrical engineering.
As well as avoiding damage to components, NDT is viewed as a safe testing method that poses few hazards to technicians (though radiographic testing requires strict conditions). NDT also helps ensure the safety of systems by making sure that machinery and structures are functioning as they should.
NDT is also:
- Accurate. Tests can be repeated many times over to check if the results are correct.
- Cost-effective. Because tests do not destroy engineering samples, the samples can be used again. NDT also detects problems before they cause breakdown or failure, helping cut costs and reduce downtime.
- Useful for testing welds. One of the most important applications of NDT is that it enables verification of welding quality.
Destructive Testing vs Non-destructive Testing
You’re probably wondering how destructive and non-destructive testing differ. Whereas NDT does not damage components, destructive testing tests the product or part to the point of complete failure. This is particularly useful for manufacturers that are introducing new products and want to know their limits prior to mass manufacture. Knowing when a product will fail makes it easier to establish maintenance regimes and operating recommendations.
During destructive testing, the test piece undergoes a level of stress that eventually deforms or completely destroys it. Examples of destructive testing methods include point bend testing and tensile testing.
Non-destructive Testing Methods
Lots of different technologies can be used for NDT. Here are some of the most commonly used NDT methods:
Ultrasonic NDT
What is ultrasonic NDT? Ultrasonic NDT uses high-frequency sound and data acquisition to examine components. Ultrasonic testing is used to measure thickness, look for defects, and monitor conditions of components and systems. Ultrasonic testing can be used to carry out tests on everything from metals and plastics to composites and ceramics. It is also widely used in medicine for diagnostic imaging and research.
Radiography NDT
Radiography NDT is another common type of NDT. What is radiography testing? In this type of test, radiation passes through the engineering specimen to detect flaws or defects. Variations in radiation strength indicate any problems. Thinner materials are analysed using X-rays, while gamma rays are required for thicker, denser materials. The results can be processed in a number of ways, including using film, computer tomography, or digital radiography.
Eddy Current NDT
An eddy current is current that flows opposite to the current introduced by a probe. What is eddy current testing? This type of NDT is widely used to inspect non-ferromagnetic surfaces and tubes. By detecting variations in these currents, eddy current testing identifies temperature-related damage, pitting, corrosion, wear, and loss of thickness in conductive materials.
Magnetic Particle NDT
What is magnetic particle testing? Magnetic particle testing detects variations on the surface of ferromagnetic materials by analysing changes to the magnetic field. This magnetic field is created with non-destructive testing equipment using permanent magnets or an electromagnet. Flux in magnetic field particles indicate problems on the surface of the component being tested.
Acoustic Emission NDT
Acoustic emissions are sometimes created by voids, cracks, or phase transformation in a metal during operation. Acoustic emission testing methods (also known as vibration testing) create vibrations in the engineering specimen and engineers then measure properties like frequency and decay time, which indicate the condition of the material. An important application of acoustic emission testing is testing cast iron structures. (Bridges are a good example.)
Visual Inspection NDT
What is visual testing in NDT? Visual inspection is a means of detecting damage, cracks, and corrosion by examining the test item by sight. Magnifying glasses or computer-aided vision systems may also be used for this purpose by test operatives.
Dye Penetrant NDT
Another example of NDT is dye penetrant testing (DPI), a method that is used to highlight surface defects such as cracks or porosity in non-porous materials. It works by applying a liquid penetrant that seeps into surface flaws due to capillary action. The process involves cleaning the surface, applying dye, removing the excess, and using a developer to reveal the defects. Visible or fluorescent dye highlights these defects under inspection.
NDT Applications
These are just some of the more common types of non-destructive testing and NDT methods. In fact, non-destructive testing equipment is used for a huge array of applications, and other techniques employ lasers, dyes, leak detection, and infrared technology, to name just a few. But the quality and performance of welding is a key NDT use case, and this can be checked with a number of technologies, including ultrasonic and magnetic particle testing, radiography NDT, and eddy current testing.
The electronics industry also uses NDT to check tiny defects in semiconductors and other electronics components, and in aerospace NDT helps to ensure aircraft safety by inspecting engines and airframes. Ultrasonic testing and radiography detect defects that could otherwise result in catastrophe. The shipping industry likewise uses NDT to assess the condition of ship hulls.
Meanwhile, OEMs use magnetic particle inspection and eddy current testing to ensure quality of materials, and in the energy industry, NDT is of vital importance in oil and gas, petrochemicals, and the nuclear sector to assess the condition of pipelines, tanks, and reactor components.
It’s true to say that without NDT, many of the products and services we rely on simply wouldn’t be possible. This versatile discipline really does help to underpin the engineering industry across many sectors.
Did you know that RS carries a range of test and measurement equipment and test leads and connector kits? Explore our range today.