- Published 16 Feb 2024
- Last Modified 16 Feb 2024
- 8 min
Robotics and Process Automation for Industry
Robotics has already had a huge impact on manufacturing thanks to the range of automation now available. But that’s just the beginning as process automation is revolutionised by AI. Learn more in our guide.
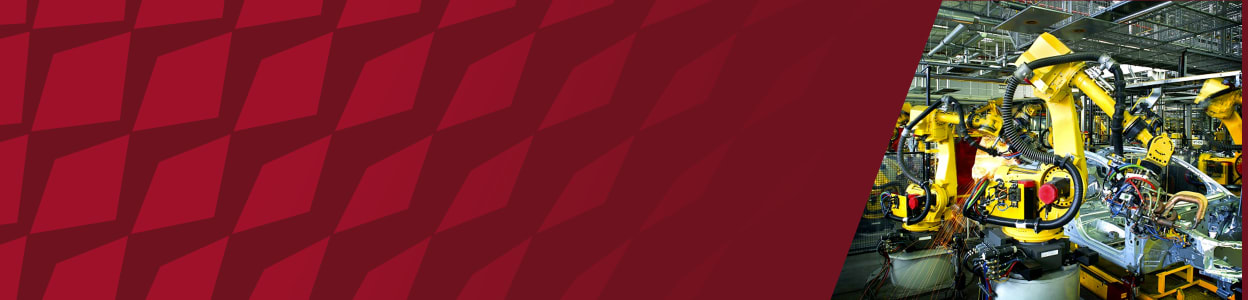
Reviewed by Stephen Bettles, Technical Support Engineer (January 2024)
Robots are used in sectors from automotive to aerospace for welding and fabrication, inventory management and logistics, and quality control. Where a task is dangerous, arduous, or repetitive for people, robots come into their own. They can also hugely boost productivity and quality because of the accuracy and speed with which they carry out tasks.
Manufacturing robots today are also being combined with the latest AI and machine learning technologies as part of the development of smart factories. Read our guide to find out how robots for industry have developed and what the future holds when it comes to robots for manufacturing.
Advanced Automation
Automation is essential to modern high-volume manufacturing. The first industrial robot was used by General Motors in 1961. Today, robotics, sensors, and other instrumentation along with AI and production software, and the power of modern cloud computing, are combining in advanced automation applications.
Advanced automation is part of the convergence of physical and digital systems known as the fourth industrial revolution (Industry 4.0). This term, coined by the World Economic Forum in 2016, describes a scenario in which the Industrial Internet of Things (IIoT), including robots networked over the internet to computers, helps to create smart factories.
The fourth industrial revolution is thought of as a distinct phase owing to the pace of current technological development, with AI and advanced robotics transforming industry and creating smart manufacturing systems.
Manufacturing Robots
Industrial robots have been used to automate manufacturing processes for many years. The first industrial robot, Unimate, was employed by GM to transport and weld die castings onto car bodies, a job that was dangerous for workers. Today there are millions of robots operating in manufacturing environments across the world, used for everything from welding and painting to assembling components. Robots can perform simpler tasks such as materials handling, but also complex automated assembly operations once programmed. Industrial robots are also widely used in pick-and-place applications in printed circuit board manufacturing.
Types of Manufacturing Robot
The most common type of robot is the automated arm fixed to a surface. Read on to learn more about the different robot types used in manufacturing and their applications.
Production Robots
Production robots include several different types. Articulated robots are what typically spring to mind when we think about robots for manufacturing. Articulated robots are very flexible and may span up to seven axes, i.e., have seven points of rotation. These types of robots are used for welding, packaging, and tending machine tools, among other tasks. They often feature suction cups to grip components. Alternatively, the robot may have a human-like hand, or be fitted with a wide range of tools including lasers, sanders, and drills. The sophistication of articulated robots means they tend to be more costly than some other types of production robots.
Other common types of industrial robots for production include:
-
Selective compliance articulated robotic arm (SCARA) robots. High-speed SCARA robots feature four-axis motion in the X, Y and Z axes, along with rotational motion about the Z axis. They are great for non-complex assembly, materials handling, and pick-and-place applications where the speed of the cycle is of prime importance
-
Delta ‘spider robots’. These lightweight robots consist of three arms connected to joints at the base. Delta robots were developed in the early 1980s for food manufacturing applications where there was a requirement to place very small, light items at high speed. These robots are widely used in the packaging sector
-
Cartesian robots. Cartesian robots travel forwards and backwards, up and down, and side to side on the X, Y and Z (Cartesian coordinate) axes. They are extremely accurate and relatively simple to use. Typical applications include materials handling, drilling, and packaging
Supply Chain Robots
Autonomous robots (including automated guided vehicles and drones) are proving their worth in the supply chain for repetitive or potentially hazardous tasks like selecting items from hard-to-reach or high-up areas. These types of robots are already commonly used in warehousing to reduce risk and speed up operations. By automating certain low-value operations in the supply chain using robots, manufacturers can reduce manual inventory checks, optimise component selection or distribution of goods, and reduce cost and human error.
Collaborative Robots
Throughout their use in manufacturing, robots have typically been isolated from personnel. Collaborative robots – co-bots – are changing that. Unlike their articulated arm counterparts, co-bots are designed to work alongside people. For example, they could be used to help move heavy items or help feed a machine with components. Co-bots were developed in the mid-1990s in a desire to make robots safe enough to work directly with engineers and shop floor workers at manufacturing facilities.
The original applications of co-bots were for materials handling and automotive assembly operations. Today, many of the leading robotics companies are developing co-bots.
Types of Process Automation
Types of process automation include repetitive, fixed types, where a process is repeated over and over again for maximum efficiency (as in the case of many types of manufacturing automation). Manufacturing processes can also be automated where there is a need for flexibility by programming and reprogramming automation as required (for example, in pharmaceutical or food and drink manufacturing). Here, products are typically produced in batches. Reprogramming the system or machine tool allows a new type of product to be quickly introduced with minimal disruption.
In today’s digitalised economy, processes are also being automated using software. For example, by using digital technology, it is possible to automate tasks that are time-consuming to do manually. An example might be using a computerised maintenance management system to collect and analyse data from production machinery (learn more about robotics for maintenance). The software will store the data, generate automatic requests for maintenance to be carried out, and schedule the resources for the work.
Regarding software, there’s also RPA robotic process automation to consider. What is robotic process automation? It’s a type of automation where software ‘robots’ are used to mimic human actions to automate tasks in a digital environment. A robotic process automation example in the supply chain is processing large volumes of purchase orders, invoices, and consignments automatically.
Much like physical robotics, this robotic automation process is suited to applications where there is a lot of arduous and time-consuming work to be carried out. As many of these activities can be automated, it frees up people to focus on tasks that are more complex or add greater value to the business. Robotic process automation tools include software that helps automate digital tasks and execute business processes. A common example is a chatbot that interacts with a customer visiting a website.
Advantages of Automation
From manufacturing robots welding car bodies to software robots helping sell products, automation has many advantages. Manufacturing automation and factory robotics can reduce hazards to personnel by carrying out work in environments that are difficult or dangerous for humans, such as high-voltage installations or nuclear reactors. Robotics have also been widely used in manufacturing because they are great at performing highly repetitive tasks quickly and efficiently. The benefits of automation thus include making a plant much more productive. With the advent of robotic process automation, code-based robots are also helping to take the legwork out of a lot of electronic processes, too.
Robots and AI
Advanced robots are already using AI. The fact that some robots can ‘see’ is one way in which AI is used with robotics, deciphering information from video data. This could be so robots can navigate warehouses, where their use has helped reduce costs, enable more accurate inventory management, and improve customer service. These types of vision technologies are improving with advancements in AI such as generative AI. The integration of robots on production lines with people is also dependent on intelligent machines.
Ultimately, AI and robotics are expected to lead to more flexible, autonomous robots that are capable of making their own decisions – rather than being workhorses that repetitively weld parts or pick and place components on production lines.
The Future of Robotics
The future of automation and robots will see them used even more widely in manufacturing, logistics, and sectors such as energy and healthcare to automate tasks that are difficult, hazardous, or just plain dull for people to do. Robotic process automation will also continue to make inroads as software robot assistants make their impact felt in business.
Artificial intelligence, machine learning and robotics are expected to make smart factory robots much smarter, too. Automation using deep learning, neural networks (forms of network that mimic the human brain) and natural language processing, all of which are parts of AI, is expected to be a reality by the end of the decade. This opens up the possibility of shop floor robots that can comprehend written or verbal language and respond appropriately.
When it comes to robots and manufacturing, the sky’s the limit. We’ve only just skirted the edges of what’s possible.
Want to know more about automation? Explore our automation and control gear range.