- Published 18 Apr 2023
- Last Modified 29 Aug 2023
- 6 min
Types of Welders
Discover everything you need to know about welder types.

In many manufacturing industries, welding is an essential process that joins metals and thermoplastics together. There are many ways that these materials can be joined together, including friction, electron beam, laser, and resistance welding. However, the most used method for joining together metals is arc welding.
These processes use electronically powered welders to generate the high levels of heat required to melt the metals and any other binding material together. This then creates a strong join when the metals have cooled. Depending on the type of materials being welded and the surrounding environment, different welding tools and methods will be required.
This guide will give an overview of the different types of welders, how they can be used, and the welding accessories required to work efficiently and safely.
MIG Welders
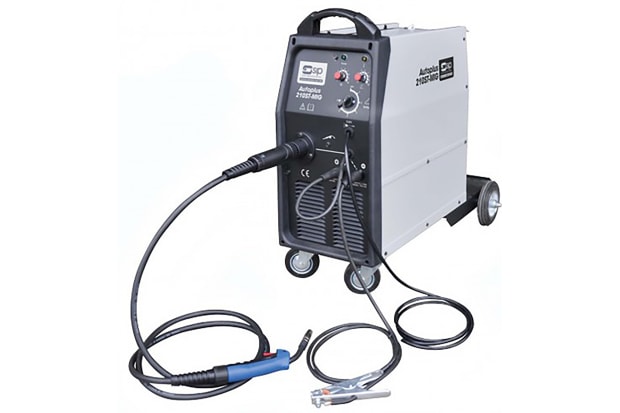
One of the most used welding methods, metal inert gas (MIG) welding generates large amounts of heat by creating a short electrical circuit between an electrode wire and the metal being welded. This wire melts onto the metal to create the weld as it cools. As the weld is made, an inert gas is released by the welder around the site to ensure no gases in the surrounding environment ignite and cause dangerous fires.
Advantages of MIG welders:
- They can be used on any type of material, including stainless steel, aluminium, and various alloys, at any thickness
- They use electrode wire, meaning welding is a more efficient process with no need to stop and start
- They can be used in any position easily with minimal mess or waste created
- They can make long weld passes, meaning less time is spent waiting for each pass (deposit of metal) to cool before work can continue
Disadvantages of MIG welders:
- They can be more expensive and less portable than other types of welders
- The gas shield needs to be protected from drafts, making outdoor welding more difficult
- Some torches can be difficult to use in restricted areas due to their size
- Some machines require more regular maintenance than others to stay efficient and safe
- Burn-through can be a problem on certain metals, particularly if they’re relatively thin
TIG Welders

Tungsten inert gas welding is also a widely used method for joining together pieces of metal. It works by using electricity to create an arc between a tungsten electrode and the welding metal. With the welding site shielded by an inert gas, the electrode isn’t consumed, though extra filler metals can be used to create the weld bead.
Benefits of TIG welders:
- They can be used on the largest range of metals and alloys
- The use of filler metal means less mess and wastage is created. Plus, the process doesn’t create any fumes or smoke
- They can be used in a variety of positions and provide high levels of precision, including in the amount of heat produced, leading to a high-quality weld
- Only one shielding gas, argon, is required for any TIG welding process
Limitations of TIG welders:
- They require specialist training and skill to be able to use, as they need greater levels of coordination and control
- They can be more expensive to operate and maintain than other welder options
- Using these can be more time-consuming and complicated than other types
- They expose the user to greater levels of light, meaning appropriate safety equipment is required
Industrial Welding
Though MIG and TIG welders are widely used for most industrial applications, shielded metal arc and flux-cored arc welding help to meet specific requirements.
Shielded Metal Arc Welding
Also known as stick welding, shielded metal arc welding works by creating an arc between the welder’s consumable electrode and the piece of welding metal. The high temperature created melts the electrode and creates the weld which then joins the pieces of metal together when cooled.
This welding method is lower in cost than other types. The welder is also smaller and more portable, making it more appropriate for welding in restricted spaces and difficult positions, and for moving from one job to another. However, more mess is created and less welding material is deposited per minute, meaning using this process can be less productive.
Flux-Cored Arc Welding
Most used outdoors or on contaminated materials, the arc in this type of welder is created between the metal being welded and the fed consumable filler wire. The core is made of materials that release shielding gases and flux, meaning the weld is protected from any contaminants or flammable gases in the air.
This feature means that flux-cored arc welding is appropriate for use outdoors or wherever wind or drafts may reduce the supply of shielding gas by other methods. Plus, the high deposition rate means this method can quickly produce high-quality welds. There are some downsides, such as the large amount of noxious fumes created, the amount of mess produced and the fact that it's not suited to all metal types.
Welding Accessories
Depending on the specific welding method being used, the types of metal being used and the area in which the welding is taking place, certain equipment and safety accessories will be required. These can include:
- Clamps or holders help to position and fix the different required materials in place so both hands can be used for welding
- Welding wire is required for certain types of methods where the electrode isn’t consumed.
- Electrodes and holders to ensure the welding point can be reached accurately
- Torch tips deliver high amounts of heat to the welding site, meaning they need to be replaced regularly
- Shielding gases such as CO2 and argon help to protect the welder from atmospheric dangers.
- Chipping hammers for removing excess splatters or messes from the welding site
- Welding helmets and curtains to keep welders, other workers or the public from sparks, heat, and light
By choosing the right welding method for your needs and ensuring you have the right equipment, you can create strong, neat, and high-quality welds quickly and efficiently.