- Published 23 Apr 2023
- Last Modified 29 Aug 2023
- 6 min
How Many Types of Valves are there?
Valves are essential to control the flow of fluids through a system. Find out which one you need in this guide.

To keep liquids moving through any piping system safely and efficiently, the correct valves need to be selected. Choosing the incorrect type could lead to fluids moving in the wrong direction through a system and cause leaks or potentially dangerous situations.
However, there are a large number of different valves available. To find the best option, you need to consider how the system should operate, what its requirements are (such as dimensions and types of fluids flowing through it) and the level of safety or control needed.
To help you make the right decision, this valve type comparison will give you all the information you need.
How Valves Work
Though their designs and exact functions may vary, valves are essentially devices that can be put into a system to help control the flow of liquids. Mainly this involves starting, stopping or regulating the amount of fluid that’s passing from one part of a plumbing, pneumatic, hydraulic or industrial system to another.
As such, valves are essential for a variety of different operations, including:
- Throttling the flow of fluids to prevent leakages and ensure the system functions efficiently
- Stopping the flow of liquids such as oil, petrol or chemicals quickly in the case of emergencies
- Controlling the direction of fluid flow to ensure there are no backflow, leakages or blockages
- Releasing or controlling the level of pressure within a system
- Regulating the amount of fluid passing through a system, ensuring that any processes can be completed efficiently
Each valve is designed to function in specific ways, so it's important to check exactly how the different types operate alongside a valve’s specific dimensions, materials and end connection design. Matching the size of the valve to the diameter of the pipes used in a system is important to ensure it can be fitted accurately.
The material of the valve will also depend on the amount of pressure and type of liquid passing through the system. For example, if corrosive chemicals or petrol is moving through a system, then stainless steel valves will be durable and resistant enough to withstand them.
Finally, the type of end connection on the valve is important to ensure the pipe fits it correctly and will operate efficiently. Threaded, flanged and socket-welded connections are just some types that are available on valves.
Different Types of Valves
Valve types can be defined by their design or their assigned function. As such, the following valves are categorised by their designated operation:
- Safety valves - sometimes known as relief valves, these devices are put at certain points in a system to release any pressure that could potentially damage it, including back pressure
- Pressure regulating valves - to work efficiently, some systems need to be put under a specific pressure level. Pressure regulating valves help to maintain this level and prevent buildup or damage
- Check valves - in systems where the fluid flow is one way, check valves help to maintain the movement of liquid in one direction. Often they’re strategically placed to be turned on and off to protect parts of the system
- Control valves - whether its fluid flow, pressure or other parameters that need to be tightly regulated, control valves help to ensure that these levels are maintained and the system can function efficiently
- Solenoid valves - automatically operated by converting electricity into magnetic fields that then trigger mechanical movements. When a current is passed through solenoid valves, liquid can flow through it. When this current stops, the flow is stopped
In contrast, the below valves have specific designs which enable them to function in particular ways.
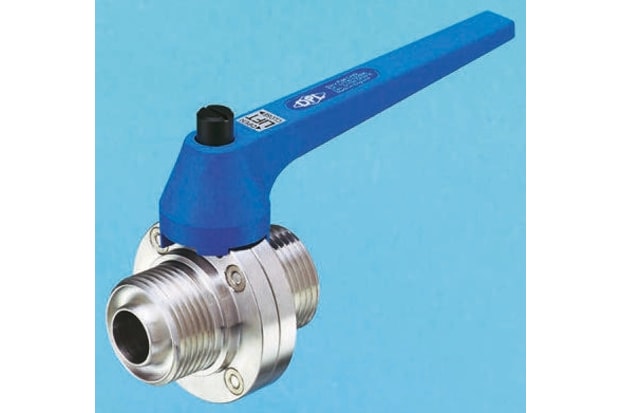
Butterfly Valves
With a quarter-turn principle of operation, butterfly valves have a body with a circular disc attached to a stem. Every time the handle is moved, the disc rotates 90 degrees and regulates the movement of fluid through the system. Seals in the valve seat and an o-ring prevents any leakages in the valve.
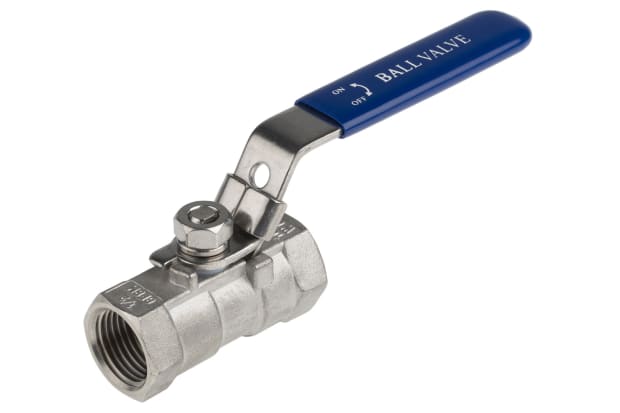
Ball Valves
So-called because of the rotary ball that’s at the centre of the valve design, this is attached to the handle on the outside of the valve. When the handle is turned, the ball moves 90 degrees to open, close or regulate the flow of fluid through the system. This reliable performance and robust design make it a popular choice in systems where a long life span is required.
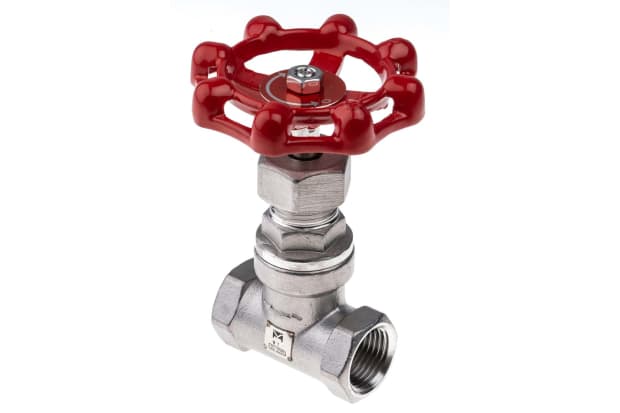
Globe Valves
Globe valves have this name due to the rounded bottom of the device. Internally they have a circular plug or disc that sits in a sealed seat when the valve is fully closed. With a screwing operation, the stem can be turned at any number of degrees to allow the flow through the valve to be tightly regulated. This makes them ideal for any throttling operations.
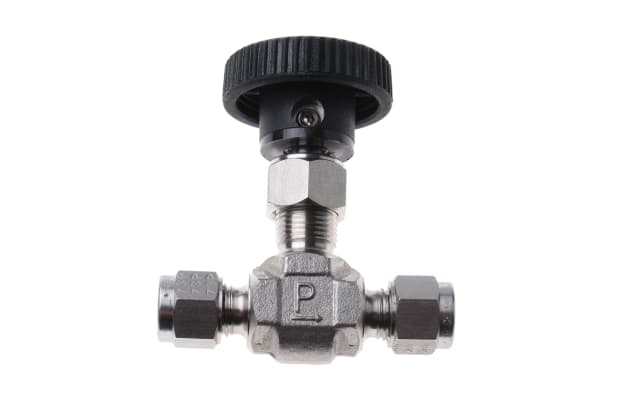
Needle Valves
A long plunger that moves up and down in the valve seat is tapered to match the end of the stem, enabling a tight seal when closed. This allows the tight control of fluid flow through the valve and the amount of pressure in a system.
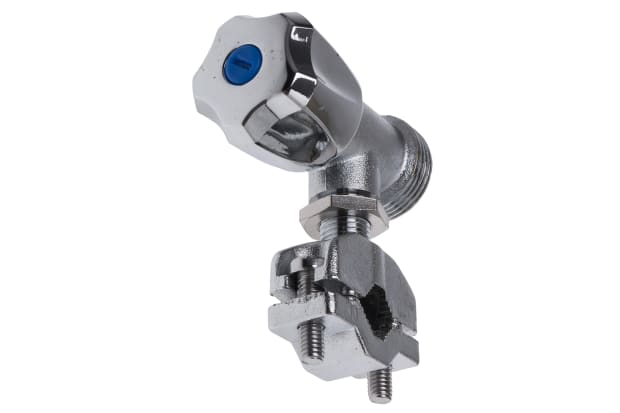
Stop Cocks Valves
Typically used in mains water systems, stop cocks look like normal taps without an opening. When the tap is turned at the top of the valve, a rubber washer is pushed up against the opening to stop the flow of fluids. This means the movement of liquids can be shut off quickly and completely, making them useful in commercial and residential buildings.
How to Check Valves are Working
It’s important to check valves are working correctly before the whole system is switched on and left to function. This will help to avoid any leaks or damage occurring when the system is switched on and prevent a drop in its efficiency. To ensure that a valve is functioning correctly, perform the following checks after you’ve installed it:
- Isolate the part of the system where the valve is so there won’t be any damage to the rest of the pipes if the device fails
- Turn the valve to its OFF position
- Gradually allow fluid to move into the part of the system where the new valve is
- Start to release the valve and turn it towards its ON position
- Move the valve a few times between fully ON and fully OFF and review its function
- If there are any faults with the functioning of the valve or problems in the system (such as leaks or buildup) then the part of the system where the valve is needs to be reisolated
By performing this check, you can ensure that the valve is operating correctly, can withstand the system’s parameters (such as pressure, flow rate and temperature) and won’t cause any problems when you switch the system on fully.