- Published 5 Jan 2023
- Last Modified 29 Aug 2023
- 10 min
Solid State Relays: A Comprehensive Guide

What are solid state relays?
In this guide, we’ll examine various aspects of solid state relays, how they function, and what sorts of environments they’re best suited to. Firstly, in order to understand what a solid state relay (SSR) is, it’s important to know what a basic or standard electromechanical relay (EMR) is, and precisely how the two types differ.
In electrical terms, a relay is a relatively simple switching device that’s used to automatically close or open a set of contacts between two circuits. This process is triggered by an electrical input or control signal of some kind, in response to which the relay switch usually moves from an ‘off’ to an ‘on’ position.
In so doing, the relay closes (or, less commonly, opens) a specific set of contacts, thus completing (or breaking) the circuit(s). In most cases, when the electrical relay device is receiving no signal, the contacts are open and the circuit is effectively incomplete. When an electrical control signal is sent to the relay terminals, it triggers a physical response in the relay switch, typically causing it to close those contacts and complete the circuit as required.
In a standard relay, this process is electromechanical (hence these relays are referred to by the acronym EMRs). In other words, an electrical control signal triggers a mechanical response in the relay. The standard mechanical relay switch is therefore composed of key moving parts, and it’s these parts that physically change position in order to open/close the contacts and complete or break the circuit as required.
By contrast, a solid state relay has no mechanical or moving parts. As electrical components, SSRs are widely used to perform much the same on/off, open/close functions as standard relays, but a solid state switch does so entirely without any physical movement within the relay itself. (We’ll look more closely at how this works in the next section of this guide.)
Solid state relays can be designed to operate either based on AC or DC input currents, depending on the specific model and applications. Common voltages for DC input include 5V, 12V and 24V DC solid state relays, while widely available examples of AC solid state relays are often based around 120V or 240V AC input.
The term ‘solid state relay’ is actually a fairly generic one, and can, in fact, refer to all manner of different relay components and configurations used to achieve the basic on/off switching function.
Many of these configurations will be designed around specific industries or applications. Solid state relays made for automotive use, for example, tend to be optimised for plug-and-play installation methods and resilience against harsher environmental conditions (anti-vibration, over-voltage protection, polarity reversal and short circuit protection) than you’d typically encounter in, say, industrial or production applications.
What are solid state relays used for?
Solid state relays are widely used in a highly diverse range of applications, sectors and industries, including:
- Industrial controls
- Motor control
- Robotics
- Medical equipment and patient/equipment isolation
- Instrumentation
- Multiplexers
- Data acquisition
- I/O subsystems
- Meters (watt-hour, water, gas)
- IC equipment
- Home appliances
How do solid state relays work?
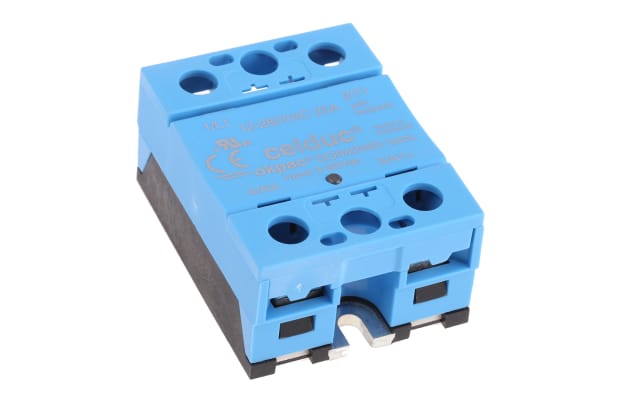
As noted above, the key characteristic of a solid state relay is that it requires no moving parts to perform the task of opening or closing contacts on a circuit.
Unlike a mechanical relay, there’s no positional change of any component within the solid state relay when it switches between on/off, open/closed states. Instead, a solid state relay works by converting the incoming electrical control signal to an optical one, often output via an infrared LED or similar (note, however, that the term ‘solid state relay’ is a generic one, and covers a variety of configurations).
This optical signal is then fired across a small gap of (permanently) open space within the module - known as an opto-isolator - to where it’s received by a photosensitive transistor, which in turn converts and sends on the signal to further electrical components. This completes the circuit and ultimately triggers the desired action, all without any contacts in the solid state relay ever coming into direct physical contact with one another.
Solid state relay mount types
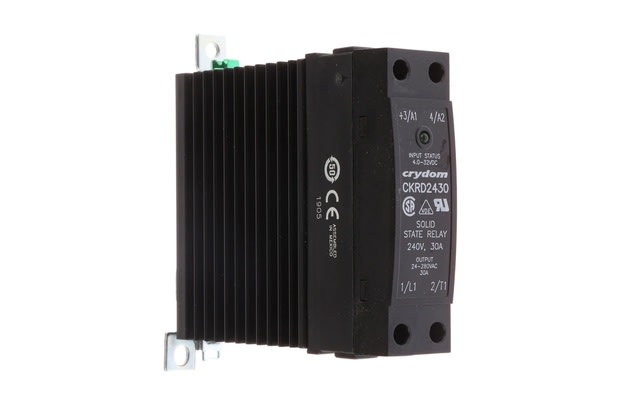
In addition to there being numerous different types of solid state relay switches sold in worldwide markets, there is also a very wide range of mounting solutions available for physically installing them to circuits or housing them as part of a wider electrical system. In this section, we’ll give a brief overview of some of the more common mounting solutions for solid state relays of various sorts.
Solid state relay PCB mounts
PCB-mount solid state relays are, as their name suggests, intended to be mounted directly to a printed circuit board. This makes for quick and straightforward installation on motherboards and other types of PCB, either via push-in pin fittings or with a requirement for soldering directly to the PCB surface.
Solid state relay DIN rail mounts
DIN-mount solid state relays are designed to be fitted to a range of standard DIN rail setups, for easy installation and access alongside other industrial control equipment housed in a variety of PCL racks and enclosures.
Solid state relay panel and chassis mounts
Panel-mount solid state relays are among the most widely available and flexible switch types and are manufactured to be attached flush with various sorts of industrial and equipment panels, hatches or heatsinks. Chassis-mount versions offer similar functionality and convenience. Both types are typically attached via screw-fitting solid state relay mounts that allow for direct fixing through the SSR base, body, or via purpose-designed eyelets (also known as through-hole mounts).
Solid state relay heatsink mounts
Heatsink mounts for solid state relays allow for the easy attachment of a heatsink cooling solution (usually passive, but active cooling options can also be used in more extreme environments) for the switch.
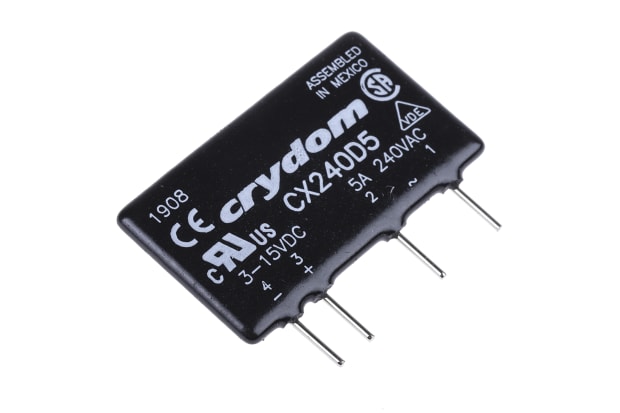
Solid state relay plug-in mounts
Various sorts of plug-in solid state relay switches are also sold that are designed around quick and convenient plug-and-play functionality - the exact type of plug attachment featured will depend on what the SSR is intended to be inserted into and where, but they’re typically intended for direct PCB insertion.
Solid state relay comparisons
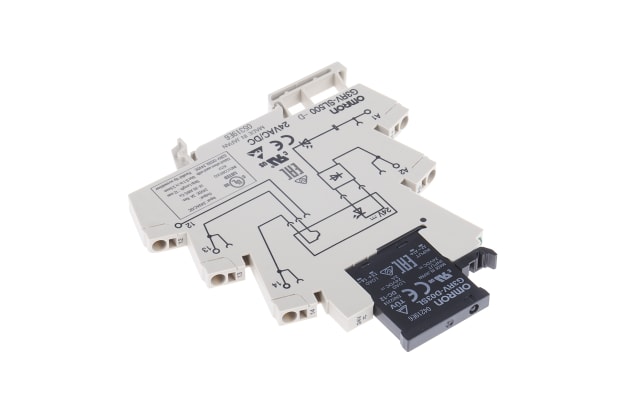
The most common comparisons made between solid state relays vs mechanical ones are broadly based on two key factors: speed of operation, and overall longevity. As we’ll see, solid state versions tend to outperform mechanical relays on both counts, because the lack of moving parts in an SSR means it can work faster and for longer without needing replacement than an equivalent mechanical version.
Despite this general rule of thumb, though, there may still be specific applications and environments in which mechanical relay switches remain a more suitable option, and are actually preferable to solid state switches in day-to-day use.
Solid state relays vs mechanical relays
Because the SSR is basically using light and/or sensors to transfer the signal, rather than physical movement, switching between on/off states can be performed orders of magnitude faster than in EMR equivalents.
This means that SSRs boast a range of abilities and characteristics that may be of potential value in many specific usage applications and industries. Application-specific advantages of solid state relay switches might include:
- Very little wear over time thus increased longevity on paper
- Electromechanical relays with moving parts will eventually need replacing
- Near-silent operation
- Ability to perform extremely fast/high-frequency switching
- Typically far lower power consumption than EMRs
- No potential for sparking caused by the rapid movement of components
- This is important in some chemically volatile or potentially explosive environments
- Reduced risk of contact failure due to physical defects or inconsistencies
- No risk of ‘bouncing’ contacts (accidental multiple contacts made, to due inaccuracy or inadequate cushioning of movement)
- Solid state relays themselves can be manufactured in far smaller and more compact form factors than mechanical versions
To complete the above actions reliably, smoothly and quickly without performing any actual mechanical action, SSRs instead rely on a number of other crucial components in order to function properly. These may include a variety of different semiconductor switching elements, such as photocouplers, diodes, transistors, thyristors and more.
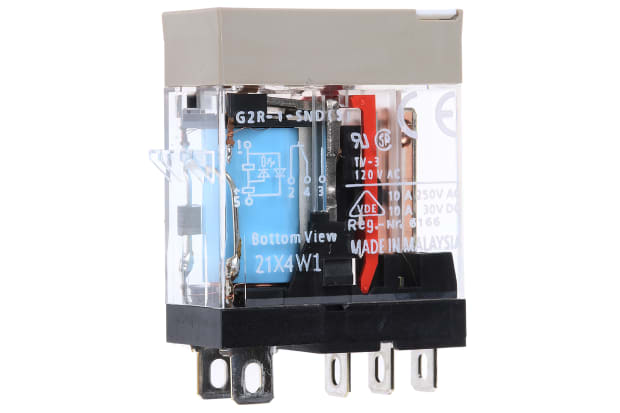
However, while technically impressive and extremely useful in a range of different scenarios, the added complexity of SSRs means that they do also have their perceived drawbacks when compared to EMRs in certain uses or environments. These might include:
- Reduced overall efficiency in terms of effective voltage-transfer compared to EMRs (there will always be a fixed drop-off on the output side)
- This might make very little difference at higher voltages, as it’s fixed rather than proportional - but at lower voltages, it will be comparatively much more significant
- This can make a noticeable difference to equipment on the output side, impacting its ability to run at full power
- There is almost always some form of ‘leakage’ current when an SSR is supposedly in an open position
- This makes them unsuitable for use in many types of safety disconnect, as they can still transfer current (and deliver a shock) at high voltages even when ‘off’
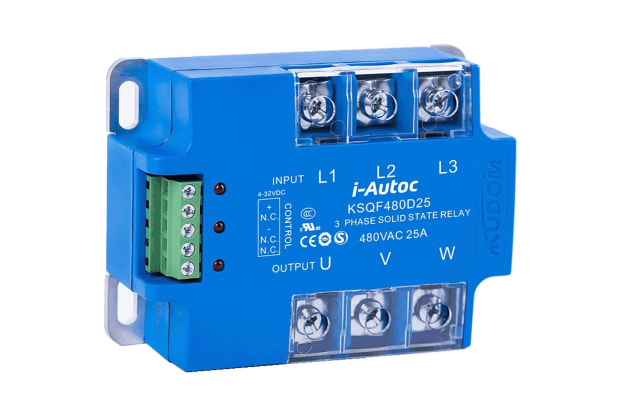
- Vulnerability to being triggered by very brief voltage spikes and surges, which a less responsive EMR would typically ‘ignore’
- Greater potential for SSRs to overheat when components are crowded, or when switching large loads
- Some configurations of solid state relays may require external cooling
- Although longevity is commonly cited as a major reason to opt for SSRs over mechanical relays, many of the potential failure points in either type of relay don’t involve the moving parts themselves
- Some argue this makes the difference in perceived durability something of a ‘theoretical’ advantage, rather than a very practical one
- Solid state relays tend to be considerably more expensive than mechanical ones
Summary
While electromechanical and solid state relays both enjoy very wide-ranging potential applications in terms of controlling power delivery for heating, lighting, motion-based equipment and much more besides, there are distinct advantages offered by each in specific scenarios.
Whether you decide to opt for the older or newer technology - and its associated price tag! - will first and foremost be a decision based on what you want the relay switch to do, how often, how fast, and how reliably. On top of this, though, there are a number of other factors worth considering when looking to buy relay switches from suppliers and manufacturers.
Not least of these is the important balance between short-term versus long-term economy. Solid state relays do offer significant performance gains in some key areas as compared to standard electromechanical relays, but of course, there’s a very noticeable cost increase involved too. That can be off-putting at first; however, the potentially increased reliability and longevity or SSRs can often mean they could work out costing less in the long-run than EMRs.
Sticking with the older versions, meanwhile, means you’ll inevitably need to budget for servicing and replacement as well - any moving parts in a standard, non-solid-state relay will eventually wear out, even if the rest of the device retains consistent performance across all other areas of the specific application you’re putting it to work in. Clearly, there’s a reasonably predictable longer-term ‘cost curve’ to be charted in that case, and buyers should also factor in the likelihood of additional expenses stemming from any productivity downtime, servicing call-outs, and so on.
Related links
- Gavazzi Solid State Relays
- Relay Heatsinks
- Infineon Solid State Relay
- RS PRO Solid State Relay Panel Mount 240 V rms Load
- i-Autoc KSQ Series Solid State Relay Panel Mount 32 V dc Control
- IXYS Solid State Relay Surface Mount
- RS PRO Solid State Relay Panel Mount, 200 V ac/dc Load
- Sensata Crydom Solid State Relay Panel Mount 32 V Control