- Published 12 Jan 2023
- Last Modified 29 Aug 2023
- 12 min
A Complete Guide to Load Cells
From weighing scales to industrial machinery, load cells are essential devices that enable accurate measurement and control of forces in various applications.

Reviewed by Jay Proctor, Technical Support Team Leader (January 2022)
This guide is part of our Industrial Automation hub where you can discover more about AI, automation and control.
In this guide, we’ll look more closely at some of the various types of load cell transducers available, as well as explore some key aspects of how load cells function and which types are best suited to which sorts of industries.
What are Load Cells?
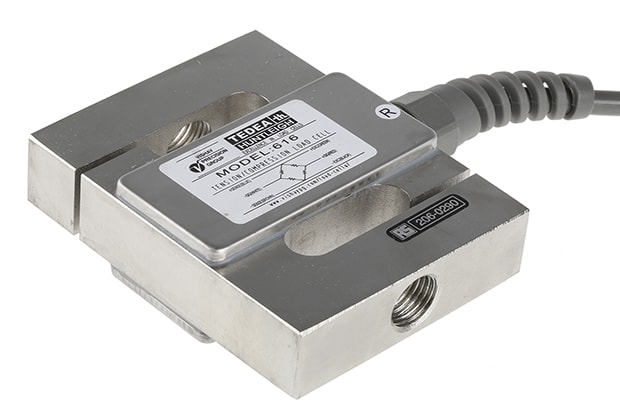
Load cells, often called load cell transducers, are crucial components in most industrial weighing systems. The most basic definition of a load cell is that they measure weight - or, more accurately, directional force - usually via a combination of spring elements and strain gauges, converted into an electrical output.
Load cells are available in many different configurations and standards, depending on the intended application and environment. Some varieties rely on calibrated proving rings to measure load displacement, although these are somewhat less common than strain gauge types.
Among the various different types of load cells available, varying models and styles can be differentiated in two key ways:
- By the specific method they use to detect weight (compression load cells, tension load cells and other measurement types)
- By the type of output signal generated (hydraulic load cells, piezoelectric load cells and various other configurations)
It should be noted that strictly speaking, a true load cell design of any type will always work (and should therefore be aligned) in the direction of gravity. However, it’s very common to encounter the term ‘load cell’ being used in reference to a wide range of force-sensing device types, many of which are explicitly designed to measure forces applied from all directions.
These terms have largely become interchangeable in many workplace environments today, so it’s sensible to clarify exactly which type of device you’ll be using for your intended application when assessing load cell prices or planning to buy load cell parts.
What are Load Cells Used for?
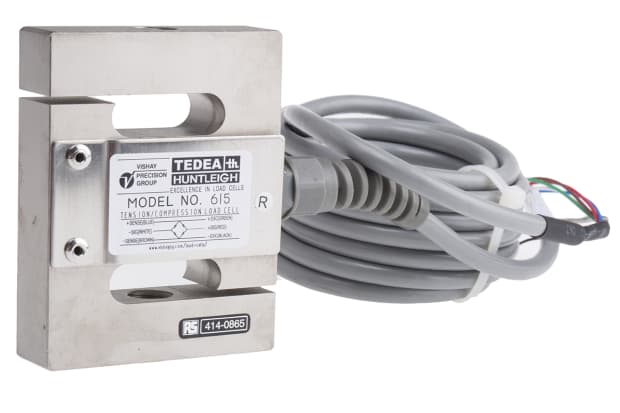
Electronic load cells are now broadly accepted as the modern standard in most of today’s heavy industries, manufacturing plants, large-scale production floors and stringent quality control environments.
The fact that such a large proportion of all global sales still rely on precise weight measurement is one reason that load cells play such a vital role in modern commerce. Industrial load cells are extremely important in maintaining precise quality control systems for manufacturing consistency and safety processes. Load cell uses also commonly include all manner of medical and laboratory settings, where they are designed to achieve optimally accurate measurements for a wide range of scientific and research purposes.
Load cells are rapidly becoming far more common across a swathe of industries that are less intrinsically reliant on critically accurate weight measurements, too - for example, in general logistics and freight calculation. Load cell transducer technologies are inherently compatible with a wide array of other digital and computer-based communications technologies, which allows companies of all types to quickly access, monitor and respond to key diagnostics information in real time.
As this is so much more difficult to achieve using traditional mechanical platform weighing devices, load cell installation often proves to be a far more efficient and cost-effective choice for most companies in the long-run.
How Do Load Cells Work?
The spring elements attached to a strain gauge material (usually foil meshes or semiconductors) will most commonly be made from either steel or aluminium, giving them the property of being very strong but also very slightly elastic. They will therefore deform to some extent under sufficient pressure, be it a downward force from above (compression) or a pulling force from below (tension), before returning to their original form and shape.
The strain gauges are able to measure the exact extent of this deformation in the spring elements to an extremely precise degree. In a typical load cell, it’s this micro deformation analysis that is then converted electronically into a highly accurate weight readout. Directional pressure thus creates an electrical signal in a load cell transducer, and the magnitude of this signal is directly proportional to the force being measured.
In operation, load cells are generally subject to a range of outside influences that must be carefully controlled, monitored and adjusted for. These include overall temperatures - which can affect the structure (and therefore the electrical resistance) of any material - as well as a broad array of other environmental challenges, including inclement weather, moisture and dust ingress, and changes in ambient conditions from one location to another.
Another factor to consider when purchasing these components is the type of load cell housing material they’re built from, with certain varieties being better suited to specific application environments. Common load cell housing materials include:
- Aluminium load cells
- Nickel plated load cells
- Polyethylene plated load cells
- Steel
- Stainless steel load cells
How to Test a Load Cell Installation?
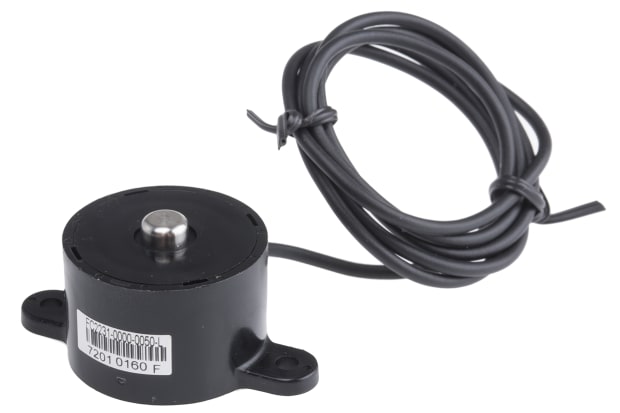
Because load cells are such a crucial and integral component in most industrial, manufacturing, production and quality control-based weighing environments, it’s vital that they’re correctly installed and maintained. In most critical application scenarios, the key to achieving consistently reliable and accurate results from a high quality load cell in regular use is proper and regular calibration.
Like any tension or strain gauge that’s regularly placed under repeated high loads - particularly if they involve dynamic forces - load cells will eventually display signs of slight drift and misalignment as they age. Industrial best practice guides (including ISO9000 standards) generally indicate that calibration procedures should ideally be performed annually, but certainly every 18-24 months as an absolute minimum, in order to guarantee continued accuracy of measurement.
Typical calibration processes usually involve taking a wide range of both linear and repeated measurements on an incremental scale, working up or down (ideally both) from very low or very high loads in gradually stepped ratios towards the minimum/maximum rated load for the cell in question.
Measuring in five predefined steps, with each reading taken three times as you move up and down through the load scale, is widely seen as an appropriate standard for most load cell calibration testing routines. In many cases, load cell calibration will also have to be independently verified at the installation location in order to meet legal certifications regarding the sale of goods by weight.
Load Cell Types
There are multiple load cell types and configurations available for industrial, manufacturing and home use in the UK and worldwide.
In the following section, we’ll give a brief outline of each of these types of gauge, and what sorts of applications they might be best suited to.
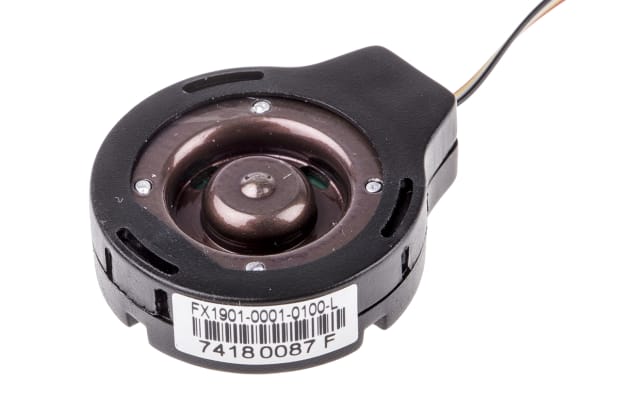
Compression Load Cells
A compression load cell is built to measure downward or lateral ‘pushing’ forces only, much like any standard weighing scale or platform. They are also sometimes referred to as ‘column load cells’, ‘pancake load cells’ or ‘donut load cells’.
They often feature an integral button design, making them a relatively simple and stable type of load cell, and thus ideal for use in limited space weighing applications. They’re particularly widely seen in environments such as silo and vessel weigh stations.
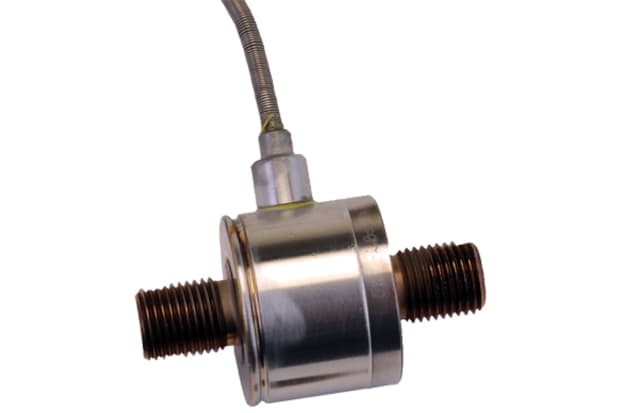
Tension Load Cells
A tension load cell measures forces ‘pulling’ on it - usually from below - similar in basic principle to the sort of configuration you might commonly encounter in a hanging digital scale at a grocery store fresh produce aisle.
On an industrial scale, tension load cell transducers (also called tensile load cells, tension links or load links) are commonly used for vessel and suspended hopper weighing, materials research and tensile testing, laboratory environment general force measurement applications, and in aerospace process monitoring.
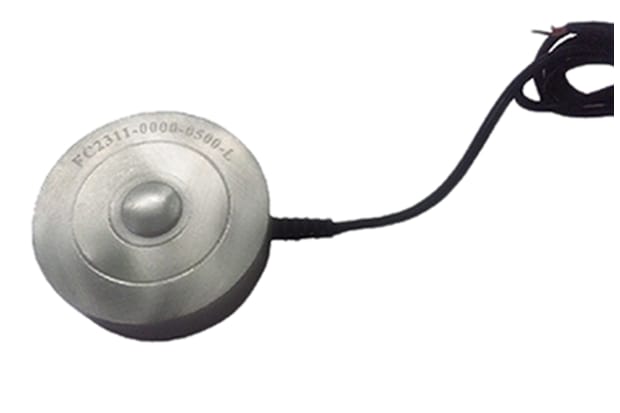
Piezoelectric Load Cells
In dynamic loading conditions, less robust strain gauge-type load cells can fail due to repeated application of sufficiently high dynamic load cycles. In essence, piezoelectric load cells work along very similar lines to regular strain gauges, using the basic load cell principles of deformation.
However, rather than using strain gauge foils, piezo cells are instead built around a special type of transducer material. This material is able to convert the measurements of dynamic and frequent force exerted on it into an electrical output, based on reading changes in resistance across the material. (‘Piezoelectric’ is derived from Greek, with the prefix ‘piezo-’ literally meaning ‘from pressure/squeezing’.)
A key disadvantage of piezoelectric sensors when compared to regular load cells is that they cannot be used for taking very static measurements of weight or strain, as these create a fixed amount of charge on the piezoelectric material. The result is that the voltage output doesn’t change under static load, and therefore the material is unable to produce a useful readout.
Hydraulic Load Cells
Hydraulic load cells are arranged around a piston and cylinder, which measure displacement under force via a diaphragm attached to the piston. This in turn registers pressure change in a tube of filling fluid, either compressing or expanding under load, which is then detected and converted to a readout by the load cell.
Hydraulic pressure load cell types are often preferred in particularly hazardous, environmentally challenging or difficult-to-access zones and application types, due to their relative robustness compared to the more sensitive electrical circuitry of many other load cell types. They’re widely used in simple industrial and agricultural weighing applications, where typical environmental challenges might include moisture, dirt or chemical exposure.
Micro Load Cells
Micro load cells typically rely on semiconductor, rather than foil, strain gauges to sense and measure deformation, due to their especially compact nature. They can be bought in a wide variety of configurations and styles, including both compression and tension types, and used in an almost equally broad range of applications as larger versions (provided they will tolerate sufficient forces).
Micro or miniature load cells are most commonly used for measuring compression forces in zones where space is at a premium. They typically provide extremely accurate and precise readouts ranging anywhere between 10 g to 2000 lbs depending on the make and model.
When looking to buy micro load cell transducers, it should be noted that the vast majority of micro versions are only designed to measure force from a single direction, and so it’s advisable to be especially aware of any ‘parasitic forces’ (i.e. being exerted from another direction) which may affect the accuracy or usefulness of the measurement.
However, numerous piezoelectric applications can be adapted with accessories such as charge amplifiers to produce quasi-static measurements under the right conditions.
IP Rated Load Cells
Load cells are often supplied with an IP rating for more reliable and robust use in a wide range of industrial and manufacturing settings, outdoor applications, and improved stability in various other challenging or hazardous environments.
IP65 Rated Load Cells
IP65 load cells will be certified for full protection against dust and other particulates, including a vacuum seal tested against continuous airflow. They will also offer protection against low-pressure jets of directed water (up to 6.3 mm) from any angle, with limited ingress permitted as long as it produces no harmful effects on the proper functioning of the device.
IP66 Rated Load Cells
IP66 load cells will be rated for full protection against dust and other particulates, including a vacuum seal tested against continuous airflow. They will also offer protection against high-pressure jets of water (up to 12.5 mm) from any angle, with limited ingress permitted as long as it produces no harmful effects on the proper functioning of the device.
IP67 Rated Load Cells
IP67 load cells will be rated for full protection against dust and other particulates, including a vacuum seal tested against continuous airflow. They will also offer protection against full immersion for up to 30 minutes at depths of between 15 cm and 1 metre (again, limited water ingress is permitted provided there are no harmful effects).
IP68 Rated Load Cells
IP68 load cells will be rated for full protection against dust and other particulates, including a vacuum seal tested against continuous airflow. They will also offer protection against extended immersion under higher pressure (i.e. at greater depths).
The precise parameters of the IP68 rating test will be set and advertised by the load cell manufacturer. They may include additional factors such as temperature fluctuations and flow rates, depending on the intended application of load cell.
What is the Difference Between Load Cells and Strain Gauges?
Load cells and strain gauges are both devices used for measuring forces or loads, but they operate in different ways.
A strain gauge is a sensor that measures the strain or deformation of an object when it is subjected to an external force. It works by using a thin metallic wire or foil that is attached to the surface of the object being measured. When the object is deformed, the wire or foil is also deformed, causing a change in its resistance. This change in resistance is proportional to the amount of strain and can be measured using an electrical circuit.
On the other hand, a load cell is a device that measures the force or load applied to it by converting the force into an electrical signal. It consists of a metal structure, called the spring element, that deforms when a force is applied to it. This deformation is then detected by a strain gauge, which is attached to the spring element. The strain gauge measures the deformation and converts it into an electrical signal that can be measured and recorded.
So, in summary, a strain gauge measures the deformation of an object, while a load cell measures the force applied to it by converting the deformation into an electrical signal. A load cell usually contains one or more strain gauges as part of its structure.
Summary
Load cells are an often overlooked but crucially important component in almost every conceivable modern industrial, manufacturing, weight-based sales or quality assurance environment you could name.
As such, there is a very broad selection of configurations, brands and load cell transducer types sold on today’s markets, and some knowledge of what they are and how they work is essential when choosing the most appropriate product type for your intended application.
For any further information and advice on buying load cells, or any other aspect of sensor and transducer technology for demanding modern workplace use, you can contact a member of our expert support team at any time.
Related Articles
Related links
- Rs pro Strain Gauges
- RS PRO Load Cell Compression Measure
- RS PRO Load Cell Compression Measure
- RS PRO Load Cell Compression, Tension Measure
- Siemens SIWAREX WL Series Load Cell Compression Measure
- Variohm Group Euroamp Series Amplifier for Use with Load Cells
- Sparkfun Amplifier for Use with Load Cell
- RS PRO Load Cell Compression Measure