- Published 2 Sept 2024
- Last Modified 2 Sept 2024
- 8 min
What is Lean Six Sigma?
Lean Six Sigma combines the best of lean manufacturing with Six Sigma process improvement principles to help companies minimise waste and maximise quality. Want to find out more? Read our guide.
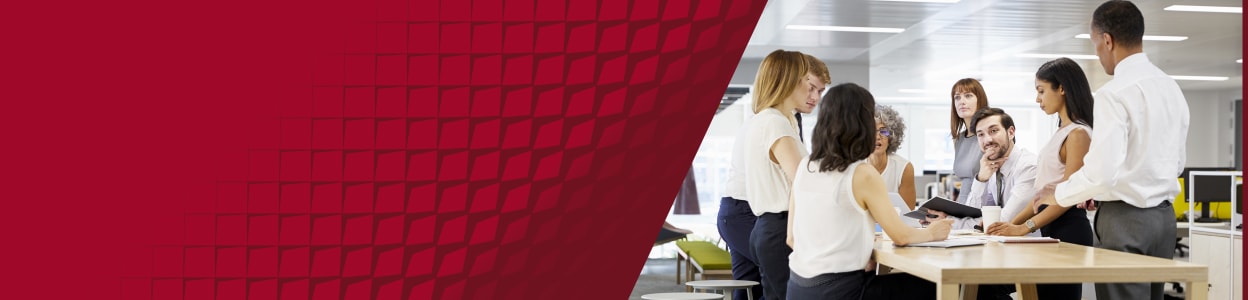
Reviewed by Karl Ralph, Technical Support Engineer (August 2024)
If you want to reduce waste in your business and make processes more efficient, Lean Six Sigma can help. This business improvement methodology combines the best of lean manufacturing with Six Sigma process improvement principles to help companies minimise waste and maximise quality. Want to find out what Lean Six Sigma is and how it works? Read on.
Lean Six Sigma Definition
What is Lean Six Sigma? We can turn to the American Society for Quality for a definition: “Lean Six Sigma is a… philosophy of improvement that values defect prevention over defect detection. It drives customer satisfaction and bottom-line results by reducing variation, waste, and cycle time, while promoting the use of work standardization and flow, thereby creating a competitive advantage. It applies anywhere variation and waste exist, and every employee should be involved.”
Simply put, Lean Six Sigma combines the focus on waste reduction that is the essence of lean manufacturing with Six Sigma’s relentless focus on reducing variation and controlling processes effectively. By improving processes, the methodology makes a business more efficient and profitable.
Six Sigma vs Lean
What’s the difference between lean and Six Sigma? Six Sigma is a data-driven method for eliminating defects in manufacturing that was developed at Motorola more than 40 years ago. The aim is to create manufacturing processes that are near perfect – or to be specific, limited to 3.4 defects per million opportunities for a defect. Six Sigma employs a framework – define, measure, analyse, improve, control (DMAIC) – that improves manufacturing processes by eliminating variation.
When it comes to Six Sigma vs lean, lean manufacturing principles focus on waste reduction and continuous improvement rather than eliminating defects. Lean and Six Sigma are nonetheless highly complementary.
Six Sigma vs Lean Six Sigma
Measurement using Six Sigma is different from Lean Six Sigma in that it focuses purely on quality (the elimination of defects in the manufacturing process). By contrast, Lean Six Sigma focuses on not only quality but also waste reduction and continuous improvement.
/IDEAS%20and%20ADVICES/Workwear/Additional%20Considerations%20For%20Work%20Clothes.jpg)
Learning Lean Six Sigma
Lean Six Sigma is fun and challenging to learn and can help drive major improvements in your business. There is a wide range of Lean Six Sigma training courses out there. Some of the key elements of these courses include:
Lean Six Sigma Principles
Training will introduce you to Lean Six Sigma principles. These include the traditional principles of Six Sigma’s DMAIC framework: define, measure, analyse, improve, and control. These principles can be understood as:
- Define. Decide what problem you want to solve.
- Measure. Determine how the process is currently performing.
- Analyse. Understand what’s causing the problem.
- Improve. Implement a plan to resolve it.
- Control. Once an improvement has been made, sustain it.
A lean and Six Sigma approach will also incorporate elements of lean manufacturing principles. While Six Sigma has a firm eye on defects, lean is about reducing waste and making processes more efficient. The engineer implementing lean hopes ultimately to be able to do much more with fewer resources, while serving customers better than ever.
Like Six Sigma, lean has five principles at its heart. These begin with ‘value’ – creating as much value for the customer as possible while also boosting profits for the manufacturer – and ‘mapping the value stream’ – analysing the entire lifecycle of the product from design through to disposal at end of life and identifying any means possible of reducing waste.
The other three key lean manufacturing principles are: ‘flow’; establishing a ‘pull system’; and ‘perfection’. Flow is about making the manufacturing process as smooth and efficient as possible, which helps to reduce time to market. Practitioners of lean recognise that disruptions to production flow are expensive, so lean aims to eliminate any disruption. Establishing a pull system, meanwhile, means manufacturing when there is demand for the product rather than manufacturing in response to a forecast, which may prove to be inaccurate. Rather than stocking a lot of unused inventory or creating products that are then just stockpiled, pull manufacturing is efficient because only resources that are needed are used.
Finally, much like Six Sigma, lean sets the bar very high when it comes to overall performance: the aim is continuous improvement for a ‘perfect’ process. This culture of continuous improvement in manufacturing is known as a ‘Kaizen’ approach. The aim with lean is always to eliminate waste and continue to eliminate waste – from transportation and inventory to time, quality, and human resources.
Lean Six Sigma Phases
Using the DMAIC Lean Six Sigma methodology provides the five key phases of a Lean Six Sigma project. Some companies also employ a preliminary ‘recognise’ phase to ensure that DMAIC is the right approach to the problem.
Lean Six Sigma Belts
Lean Six Sigma certification comes in the form of Lean Six Sigma belts. These are colour-coded in the manner of martial arts belts: white, yellow, green, black, and master black. White, yellow, and green belts represent beginner and intermediate levels, which focus on learning the basic Lean Six Sigma tools and then using them on a project. The black and master black levels are more time-consuming to attain and add leadership, mentoring, and coaching abilities for Lean Six Sigma programmes.
Also as in martial arts, attaining one Lean Six Sigma belt provides the foundation for the next. Where Lean Six Sigma differs is that it is also possible to start at black and move on to master black belt. This may be appropriate for people who have experience of lean manufacturing or quality and are comfortable with using statistics for quantitative analysis. Either way, there is a huge range of organisations out there providing Lean Six Sigma certification and training.
Implementing Lean Six Sigma
Implementing Lean Six Sigma can be challenging. It’s important there is buy-in from management for a Lean Six Sigma programme. It’s also important to train the employees involved in Lean Six Sigma methodology, whether that’s at white belt, green belt, yellow belt, or black belt level. Ideally, there should be awareness of the project throughout the business, and everyone should get involved.
Lean Six Sigma Examples
Lean Six Sigma principles can be applied to business in any industry, not just manufacturing. Examples of programme successes might include reducing time to market for the production of wind turbine blades, cutting downtime caused by problems with an IT system, or reducing defects in welding in an oil and gas application.
Adidas has reportedly cut manufacturing times by 30% by implementing Lean Six Sigma techniques. Lean Six Sigma is also being used in education, government, the military, healthcare, retail, hospitality, and many other sectors to improve processes, productivity, and profitability.
Benefits of Lean Six Sigma
Benefits of Lean Six Sigma include:
- Cutting costs. Less waste in the business means lower costs. For example, only producing what is needed when it is needed is more financially prudent than churning out products to meet a hypothetical forecast.
- Reducing waste. Optimising processes helps to both identify sources of waste and decrease waste within the business. That’s especially beneficial at a time when resources are under pressure and sustainability is a key goal.
- Improved productivity. Lean Six Sigma not only helps reduce waste but also helps establish more effective manufacturing processes, which in turns means better productivity.
- Elimination of errors. Because Lean Six Sigma includes Six Sigma’s focus on quality and reducing variation in manufacturing, it’s possible to entirely eradicate errors in production.
- Better quality. Improved quality of product is a fundamental aim of Lean Six Sigma, so manufacturers adopting a programme can expect to iron out any problems in production that are affecting the quality of the final product.
- Improved employee engagement. Employee engagement can also be boosted. Employees often find the quest for continuous improvement motivating.
- Enhanced profitability. Companies that successfully adopt Lean Six Sigma should make more money.
Lean and Six Sigma have come a long way from their original origins in manufacturing. Combining the benefits of both is helping companies to improve performance, cut waste, and eliminate defects.
If you haven’t considered the benefits of Lean Six Sigma for your manufacturing, now’s a great time to start.
The 5S Pillars of Lean
5S is a lean method that encourages employees to improve their working conditions by reducing waste, unplanned downtime and in-process inventory. The 5S pillars are the following:
- Sort: Focuses on separating required and unnecessary items from the workplace and removing anything that’s not needed. An example of sort is ‘red tagging’, which involves placing a red tag on any surplus items.
- Set in order: This step can only be done after unrequired objects have been removed and involves developing practical and efficient solutions to mark and arrange goods in a way that makes them easy to store and find.
- Shine: After the clutter has been removed and remaining items have been organised, the next step is to give the work area a thorough clean.
- Standardise: Once the first three steps have been implemented, now it’s all about maintaining these standards, ensuring that a consistent approach to tasks is followed.
- Sustain: The final step is to sustain. This equates to making a habit of carrying out the correct procedures on a regular basis.
Did you know RS stocks a huge range of systems for storing inventory efficiently? Explore our range here.
Related Articles
Related links
- Sustainable Industrial Waste Management
- Enhancing shopfloor excellence
- Five ways to tackle the challenges of food and beverage manufacturing today
- Shaping The Future of Waste
- Waste Utilities Services & Solutions Form Submission | RS
- Recycling
- Rubbermaid Commercial Products Slim Jim 61L Blue High-Quality...
- PCB Card Guides