- Published 30 Jan 2023
- Last Modified 29 Aug 2023
- 7 min
A Complete Guide to Compression Fittings
Our compression fittings guide explains their uses, how they work, the different types, and how to use them.

What is a Compression Fitting?
First things first: what is a compression fitting? They are couplings used by plumbers to join tubes or smaller flow diameter pipes. They are commonly made from brass, copper or even stainless steel and are used to join PVC, nylon, plastic, or copper tubing.
These versatile adapter fittings are available in a variety of designs and sizes for varying plumbing projects across domestic, commercial, and industrial applications - everything from water mains to hydraulic pumping systems.
Compression fittings are so-called because they join pipes by compressing them together. These devices have a variety of alternative names, including:
- Compression joints
- Compression nuts
- Compression pipe fittings
- Compression couplings
- Compression type fittings
- Plumbing compression fittings
What are Compression Fittings Used for?
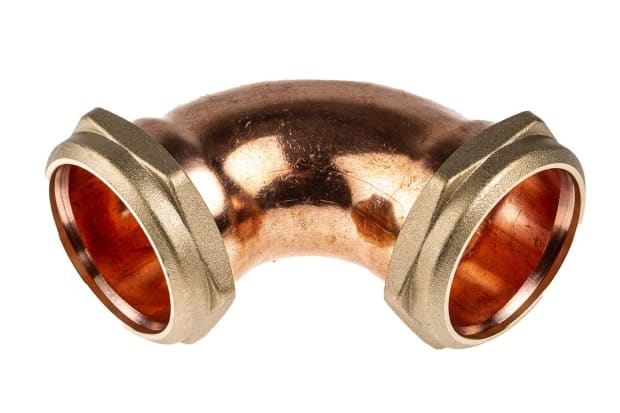
Compression fittings are used to create plumbing systems by connecting lengths of copper or plastic tubing and pipework to each other or threaded components such as valves. They are straightforward to apply and remove and a good choice for pipes laid in confined spaces that would be difficult to solder without risk of fire.
In addition to plumbing projects, these devices are used for gas installations and hydraulic equipment by industrial engineers. Although primarily designed for professional plumbing and engineering projects, compression fittings are also suitable for a variety of applications in DIY projects - for example, sink and shower unit pipes - because they do not require soldering or heat to apply.
How Does a Compression Fitting Work?
Compression fittings are relatively simple devices and are not difficult to use. They typically consist of three pieces:
- A tapered nut with threading
- A slim brass ring called an ‘olive’ or ‘ferrule’
- A tapered insert - the main body of the fitting
When the nut is tightened, the olive is compressed between the nut and the fitting. This causes the barrel-shaped olive ring to compress onto the pipe's outer diameter, creating a tight seal.
Types of Compression Fitting
Like all devices and components intended for use in different settings, these attachments are available in several sizes, from compact models to larger diameters, as well as differing designs.
Let’s look at a few of the principal types of fittings:
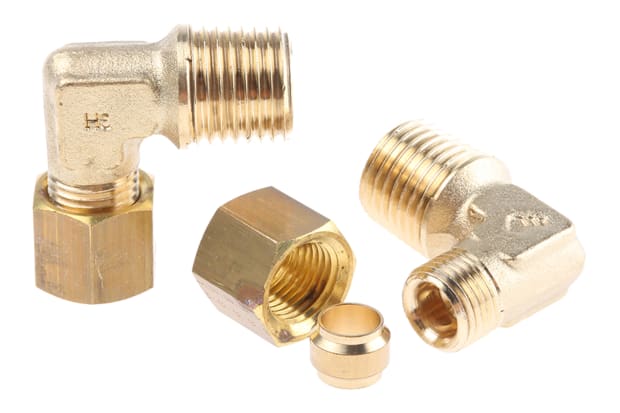
Compression Elbow Fittings
Elbow joints are angular, changing the direction of a particular pipe - most commonly by 45 or 90 degrees. As you might expect, therefore, compression elbow fittings are used to join pipes at different angles: for example, showerheads are connected to shower units by an elbow joint.
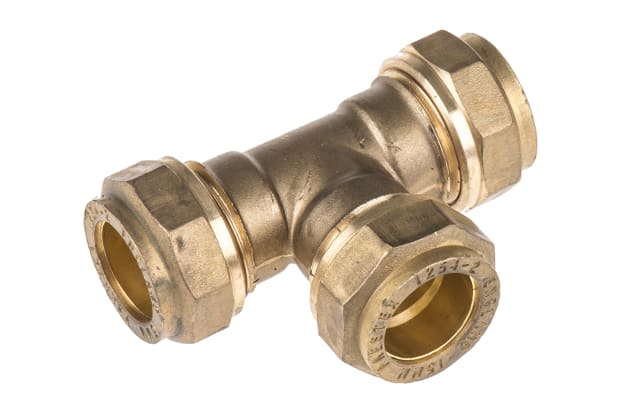
Compression Tee Fittings
Tee fittings are so-called because they have a T shape, with two inputs (or outputs) opposite each other and an output (or input) at a 90-degree angle.
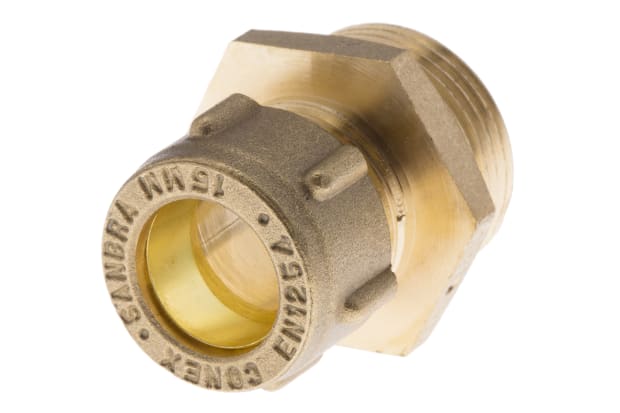
Compression Union and Coupler Fittings
This is the simplest, standard fitting. Usually short, they are used to create a simple join between two lengths of tube or pipe. Couplers - or couplings - are designed to be permanent once installed, while union fittings are more flexible and can be repositioned or moved when required.
How to Use Compression Fittings
Here’s how to install and tighten copper and brass fittings onto two lengths of pipe:
- Clean the pipes to be joined, removing any grime
- Place a pipe insert into the end of the pipe to be joined. Pipe inserts, typically made from plastic or steel, reinforce pipes and keep them in a fully circular shape, making connection easier. It should be noted that this only applies to plastic pipes and not copper or steel pipes as they are much stronger
- Screw the fitting’s tapered insert onto the end of the other length of pipe
- Slide the compression fitting olive (brass ring) over the first length of pipe, and then lay the nut over that
- Using a spanner, tighten the nut over the threaded head of the fitting, while holding the fitting with a pair of plumber’s grips. This pressure created by the tightening motion will press down on the olive, causing it to grip the pipe tightly. However, be careful not to exert too much pressure as this could damage the fitting or thread, making the device harder to remove or reposition
But how do you remove fittings or reposition olives? You should be aware that the olives cannot be easily removed once they have compressed onto a pipe. This is because they will have permanently clamped onto the outer diameter of the tube.
Compression Fitting Sizes
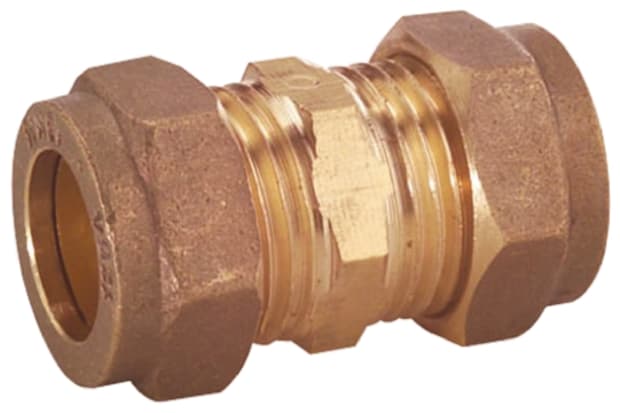
When selecting fittings for your project it is important to ensure they will be compatible with the pipes to which they will be attached. For obvious reasons you will require fittings with a broad enough diameter to enclose each length of pipe - but they also need to be sufficiently tight to ensure a watertight seal. So, the size of fittings is important.
Your choice of diameter ranges from around 4mm (0.16 inches) at the smaller end to a more substantial 54mm (2.13 inches) at the high end. As you might expect, compression fitting pipe diameters match the outer diameter (OD) of the tubing. The two commonest are 15mm and 22mm.
What are Compression Fittings Made of?
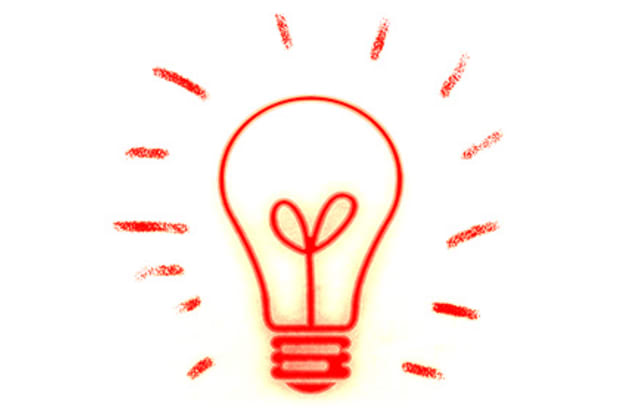
Most compression fittings are made from brass and copper because these metals combine strength and resistance to corrosion without high costs. Plastic and stainless steel models are also available.
Both brass and copper fittings make an excellent tool for joining copper pipes and plastic tubing.
They create an effective, watertight join between lengths of pipe without solder. The latter requires special tools and equipment and can be impractical when space is limited.
FAQs
How Tight Should a Compression Fitting Be?
Compression fittings should be tight enough to create a watertight seal but not so tight that the pipe warps or the thread is damaged as this could encourage leaks and make the fittings much harder to remove later. Proceed with caution.
What Should I Do if I Find a Compression Fitting Leaking?
If a compression fitting is leaking, in the first instance, try to tighten the fitting using a pair of adjustable pipe tools. These should be positioned in the opposite direction to the tightening motion. If the leak persists, disassemble the fitting, and apply sealant to the olive. Alternatively, remove the olive altogether and replace it.
How Do Compression Fittings Compare to Pipe Sweating?
The process of soldering copper pipes together is referred to as ‘sweating’. Soldering offers certain advantages: it’s a straightforward process for experienced plumbers and engineers and it creates a lasting join (in theory). However, soldering is not always a practical option - in confined spaces for example. By contrast, fittings are easy to apply even without special training, do not need the application of heat, and in most cases, they can be removed and repositioned if required.
How Many PSI Can a Compression Fitting Hold?
Pounds per square inch, or PSI, is a frequently used pressure metric. These are robust devices and stainless steel models with larger flow diameters that can withstand pressure applications above 10,000 PSI. As you might expect, smaller fittings made from other materials have lower PSI ratings.
Are Gas and Water Compression Fittings the Same?
There is no significant difference. Compression fittings designed for liquid will work fine with gas but if you use optional PTFE tape, make sure it is gas grade. In addition, ensure the fittings are accessible and not hidden behind walls or under floors.
Are Compression Fittings Reliable?
Yes, they are reliable, if you:
- Ensure that the pipe or tubing compression fittings you buy fit correctly
- Ensure they are installed correctly
Where to Next?
Related links
- A Complete Guide to PTFE Tape
- Brass Pipe Fittings
- Temperature Probe Accessories
- Norgren Brass Pipe Fitting Compression Fitting
- Legris Brass Pipe Fitting, Straight Compression Compression...
- RS PRO Brass Compression Fitting, Straight Coupler
- Legris Brass Pipe Fitting, Straight Compression Compression...
- Legris Brass Pipe Fitting, Straight Compression Compression...