- Published 20 Mar 2024
- Last Modified 20 Mar 2024
- 6 min
Motor Controls Explained
As electric motors play an increasingly important role in the energy transition, along with the many functions they’ve reliably performed for decades, robust motor controllers will be needed to ensure these motors efficiently output the right speeds and torques. Read our guide to learn about the types of motor controllers and the latest advances in this field.
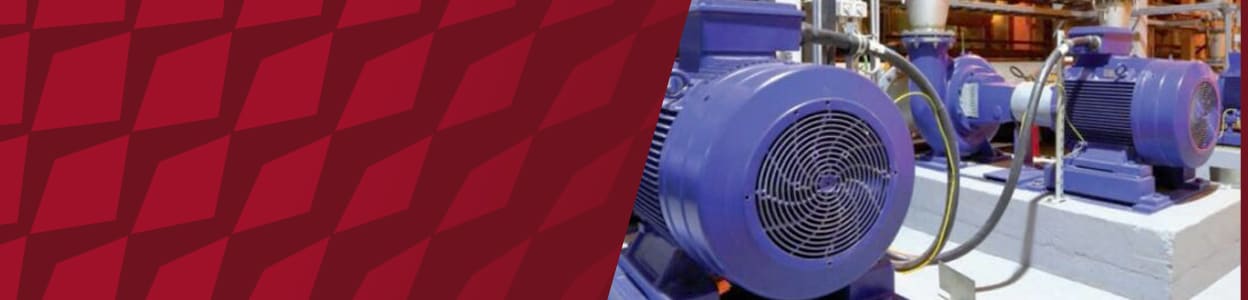
What is motor control? Though electric motors are quite simple devices in their design and function, it is a delicate process to control when and how fast they spin, as well as their efficiencies. This guide will explain the drives and controls available for using advanced motor technology to its greatest potential.
Electric Motor Controls
Electric motor controls can either be electronic or electromechanical. Electromechanical controllers are simpler devices that rely on physical contact to produce effects. These include switches, solenoids, and relays.
Electronic motor controls, however, have more adjustability, programmability, and communication capabilities with other devices, which allows widespread control system integration. These devices include variable speed drives, soft starters, and pulse width modulators. This guide will focus on electronic motor controllers.
What Do Electric Motor Controls Do?
Electric motor controls, quite simply, handle all aspects of an electric motor’s spinning shaft:
- Activation
- Deactivation (including braking and emergency stops)
- Rotational speed
- Rate of speed change
- Rotational position
- Rotational direction
- Torque produced
- Energy consumed
Different motor controller devices exist for each of these functions, and many can handle multiple ones. To configure motor controllers for your system you will first need to determine what type of performance targets your motors need to hit.
For example, if you need to control a motor’s speed in rpm, then select a speed controller that fits with the rest of your motor’s operating parameters (voltage, phase, etc.).
To precisely control a motor shaft’s position in degrees, though, look to servo motor controllers and stepper motor controllers. They are used in industries that require high-precision actuation, such as robotics.
Benefits of Electric Motor Controls
AC and DC motor controls each have their own benefits, though they naturally have different designs and features for controlling these separate motor types.
DC Motor Controls: Characteristics and Advantages
DC motor speed control is fairly simple. It essentially just involves regulating the supply voltage with a potentiometer, allowing easily setting the shaft’s speed anywhere within the motor’s full speed range. With brushed DC motors that have field control or field weakening, these DC motor controls also allow holding a consistent torque throughout these speed settings.
There are a few constraints on DC motor speed control, though:
- Any AC supply power will need conversion using a rectifier
- Braking requires a dedicated resistor in the circuit
To reverse the direction of DC motors, you’ll need a relay for switching power supply polarity and a sensor for first verifying that the motor has completely stopped.
AC Motor Controls: Characteristics and Advantages
AC motor controls are generally more complex and expensive. AC motors themselves can be more affordable, though, and connect more easily to ubiquitous AC mains power. If you need precise, on-demand braking and direction reversal, AC motor controllers are the superior choice.
Since these motor controllers offer more adjustability and are more complex, they need significant tuning when setting them up in an installation. AC controllers also often come with the features needed to readily connect to broader control systems, making them well-suited to fast-paced, highly connected environments.
Variable speed drives are the most common types of AC motor controls, and they fall into two main categories.
Variable frequency drives (VFDs) modify the frequency of the supply power, and this adjusts the motor speed. VFDs convert the supplied AC power to DC through a rectifier and then convert it back to AC at the desired frequency through an inverter. VFDs often maintain a voltage-to-frequency ratio throughout operation to give consistent torque. This allows robust motor performance across a wide range of speeds and applications, though it is not well-suited for low speeds or holding-torque (stopped) applications.
Vector control drives have more complete control ranges than VFDs. They have algorithms for separately controlling the motor’s magnetising and torque-producing currents to efficiently convert supply power to torque with minimal heat build-up, including at low speeds and holding torque.
Advanced Motor Controls
Today’s advanced motor technology has equally advanced motor controls. Drives and controls are becoming ‘smarter’ in that they employ detailed feedback, algorithms, and device communication to achieve precise control of motor speed, torque, and energy usage.
Controlling Motor Speed
Along with variable speed drives, a key component of motor speed control is soft starters, which protect motors when they start and stop spinning. They ease the motor out of its resting position to avoid the large spikes in torque, current, and heat that come from rapidly taking on large loads.
There are also advanced motor controls such as intelligent motor controllers (IMCs). These are a programmable type of integrated circuit (IC), and they can provide control commands for a motor’s speed or torque based on ongoing data collected. IMCs can work with both brushless DC motors and multi-phase AC motors, making them very versatile.
IMC speed control is very useful in heating, ventilation, and air conditioning (HVAC) applications. For example, for fans with airflow output targets, IMCs can precisely control fan speed to achieve those outputs. This is much more efficient than fans that can only be run at their maximum speed, which requires either manually throttling the airflow or periodically switching the fan on and off to meet flow rate targets.
Controlling Motor Torque
Algorithms exist for precisely calculating motor shaft position to reliably reach maximum torque for high-torque/low-speed applications but with fewer sensors involved. This allows a less expensive installation that in turn has fewer failure points.
Motor Energy Consumption
Smart motor controllers also extend to the energy electric motors expend. Advanced motor controls can set motor operation with energy usage as the input and monitor what speed and torque motors are achieving with that energy. When performance begins to degrade, these control systems can create alerts in the broader system so that operators can investigate these problems. This plays a part in predictive maintenance in that you can detect and address motor problems before they create costlier headaches for you.
The Future of Electric Motor Control
As we increasingly rely on electric motors to take the place of more carbon-intensive devices, we’ll equally need them to operate as efficiently as possible to further reduce energy usage. That will take robust, smart motor controls.
Advanced motor controls will also play a part in Industry 4.0 and maintenance strategies such as preventative, predictive, and precision maintenance. Companies will seek to maximise the returns on their equipment investments, and this will require carefully monitoring motor operating conditions and optimising their outputs with the right motor controllers. Additionally, electric motor controls that can communicate with each other and broader central control systems will be essential in reviewing system health and performance.
Browse RS’ automation and control products to achieve the performance you need in your motors’ work.
Related Articles
Related links
- Motor Controllers
- MikroElektronika PWM Driver Click Motor Controller for DMP3010LK3,...
- NIDEC ADVANCED MOTOR Gearbox 3.9 Nm Maximum Torque, 30rpm Maximum Speed
- SMC Stepper Motor Controller 3 A, Speed Controller Function
- Introduction to Motor Controllers
- Allen Bradley 5.5 kW DC Motor Controller 3 Phase Speed Controller...
- Eaton 2.2 kW Motor Controller 3 Phase Speed Controller Function, 480 V
- Siemens 0.024 kW Control Unit 1 A, 28.8 V