- Published 13 Sept 2024
- Last Modified 13 Sept 2024
- 7 min
Seamless Machining with End Mill Cutters
End mills are cutting tools that give a great finish to milling work. Find out all about them, how they work and tips on finding the best type in this article.

Introduction to End Mills
Reviewed by Osman Hafeji, Technical Support Engineer (August, 2024)
End mills are a type of cutting tool used in industrial milling applications. They are distinct from drill bits in that they are designed to cut in multiple directions, not just axially. End mills typically have cutting edges on the sides as well as the end of the tool, allowing them to perform a variety of tasks such as profiling, contouring, slotting, and counterboring. They come in a wide range of shapes, sizes, and materials, making them highly versatile for different machining operations.
What Is its Importance in Machining?
End mills play a crucial role in modern machining processes, enabling the creation of complex parts and components with high precision and efficiency. Their ability to remove material in intricate ways allows for the production of detailed features and complex geometries that would be difficult or impossible to achieve with other cutting tools. This versatility makes end mills indispensable in industries such as aerospace, automotive, medical device manufacturing, and mold making.
Types of End Mill Cutters
Unlike a drill bit, which cuts only in the axial direction, an end mill cutter is designed to cut in multiple directions, including radially. This versatility allows end mill cutters to perform various tasks such as profiling, contouring, slotting, and counterboring. The cutting edges on the end mill cutter are typically located on both the end and sides of the tool, enabling it to remove material from the workpiece in a highly efficient manner.
End mill cutters come in a variety of shapes and sizes, each tailored to specific machining needs. Here are some common types:
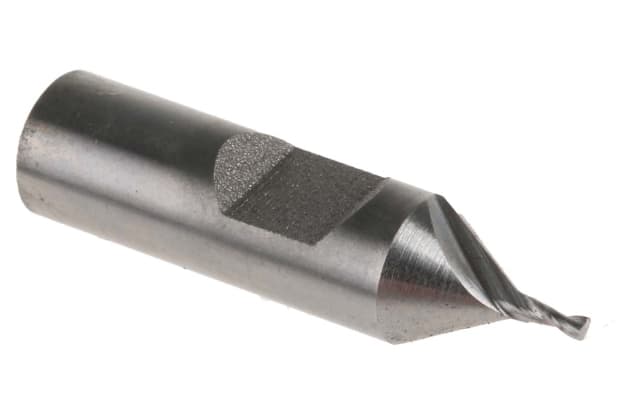
- Roughing End Mills: These are designed for rapid material removal. They have serrated cutting edges, which reduce the cutting forces and break up the chips, making them ideal for removing large amounts of material quickly.
- Finishing End Mills: These provide a smooth surface finish and are used for final machining passes. They have a more refined cutting edge compared to roughing end mills and are used to achieve high precision and excellent surface quality.
- Center-Cutting End Mills: These end mills have cutting edges at the tip of the tool, allowing them to plunge directly into the material. They are versatile and can be used for a variety of operations, including drilling, slotting, and contouring.
- Non-Center Cutting End Mills: Unlike center-cutting end mills, these do not have cutting edges at the tip and cannot be used for plunging. They are typically used for side milling operations where the tool moves laterally through the material.
- Ball End Mills: Characterised by their spherical cutting tips, ball end mills are used for milling contoured surfaces, slotting, and pocketing. They are particularly useful in 3D milling applications and mold making.
- Corner Radius End Mills: These end mills have a rounded edge at the corner, which reduces chipping and extends the tool’s life. They are used to produce rounded edges on the workpiece, improving its durability.
Material Considerations for End Mills
When selecting end mills, the cutter material plays a crucial role in performance and durability. Understanding the differences between HSS, carbide, and other materials helps in choosing the best tool for specific machining needs.
- High-Speed Steel (HSS):
- Overview: Durable and wear-resistant, HSS is ideal for general-purpose milling.
- Applications: Best for softer materials like aluminium, mild steel, and plastics.
- Advantages: Cost-effective, easy to re-sharpen, good for low-speed operations.
- Carbide:
- Overview: Extremely hard and heat-resistant, carbide milling bits are made from tungsten carbide.
- Applications: Suited for high-speed machining of harder materials like stainless steel and cast iron, and particularly effective as milling cutters for steel.
- Advantages: Retains sharpness longer, allows higher cutting speeds, reduces tool wear.
- Cobalt Steel Alloys:
- Overview: Enhanced HSS with higher cobalt content for improved heat and wear resistance.
- Applications: Suitable for harder materials and high-temperature operations, including milling cutters for steel.
- Advantages: More durable than standard HSS, better for demanding tasks.
- Ceramics and Diamond Coatings:
- Overview: Offer greater level of hardness and wear resistance.
- Applications: High-speed machining of abrasive materials and hard metals, especially effective for non-ferrous metals, composites, and carbon fiber.
- Advantages: Exceptional tool life, maintains sharpness under extreme conditions.
Applications of Milling Cutters
Milling cutters are versatile tools used in various machining processes to remove material from a workpiece and create precise shapes, profiles, and surface finishes. Their applications span across numerous industries, each requiring specific types of milling cutters to achieve desired results efficiently and accurately. Below are detailed applications of milling cutters in different contexts:
1. General Machining: End mill cutters are used for profile milling, slotting, and face milling, creating complex shapes, grooves, and flat surfaces. The versatility of end mill bits allows for a wide range of applications, from roughing to finishing.
-
Automotive Industry: End mill cutters machine precise engine components and transmission parts, ensuring tight tolerances and high performance. Ball end mills are often used for creating the detailed shapes required in these components.
-
Aerospace Industry: End mill cutters are essential for producing complex structural components and turbine blades with high precision. Carbide milling bits are preferred due to their durability and ability to withstand the machining of tough materials like titanium and high-temperature alloys.
-
Medical Device Manufacturing: End mill cutters produce detailed and precise parts for medical implants, prosthetics, and surgical instruments. The best end mills ensure the biocompatibility and functionality of these devices, which are crucial for patient safety.
-
Mold and Die Making: End mill cutters create cavities and cores for injection molds and die casting molds with high accuracy.
-
Tool and Die Maintenance: End mill cutters are often used in tool and die shops for maintaining, re-sharpening, and modifying existing tools to extend their lifespan and improve their performance.
-
Metalworking: Specialised end mill cutters for steel, like carbide milling bits, efficiently machine hard materials, ensuring longevity and precision. These cutters are essential for high-performance metalworking applications, providing optimal results in terms of surface finish and dimensional accuracy.
-
Electronics and Micro-Machining: End mill cutters produce small, intricate parts for electronics and microelectronics with high precision. The use of fine end mill bits is crucial for achieving the necessary detail and quality in micro-machined components.
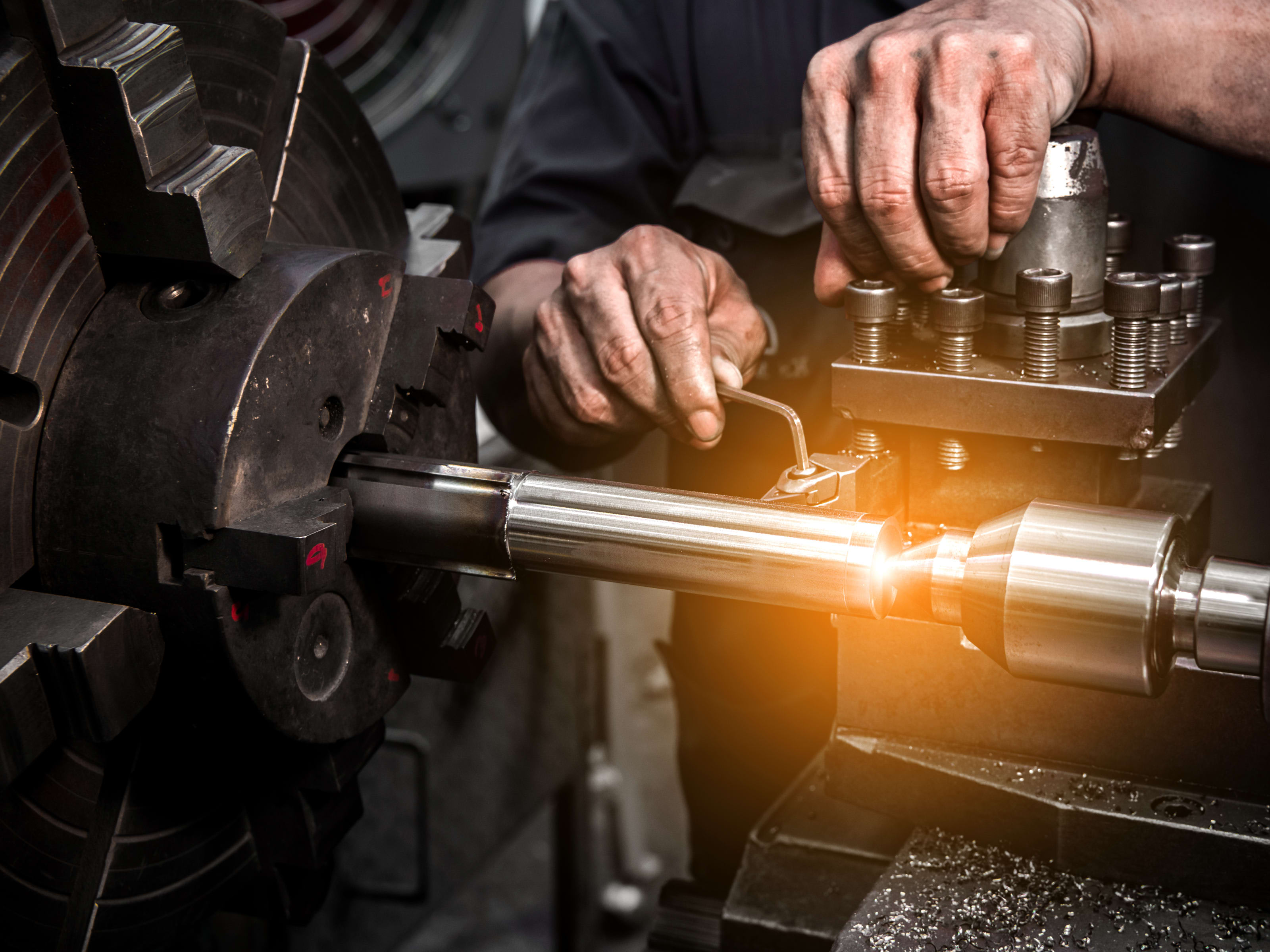
Key Considerations in Choosing the Right Milling Cutter
Selecting the appropriate milling cutter is crucial in achieving precise machining results across various industries. One fundamental decision machinists face is choosing between slot mills and end mills, each designed for specific tasks and materials.
Slot Mill vs End Mill: Slot mills are specialised tools primarily used for milling slots and keyways, characterised by their straight cutting edges and ability to plunge into the workpiece. They excel in slotting operations where a vertical cut is required without the need for drilling beforehand.
On the other hand, end mills are versatile tools with cutting edges on the tip and sides, allowing for a range of cutting operations such as profiling, contouring, and drilling. They are ideal for general milling tasks and can be used across various materials and machining scenarios.
Choosing the Right Tool:
- Application Specificity: Consider the specific machining task—whether it involves creating slots or performing complex contouring.
- Material Compatibility: Evaluate the material being machined—slot mills are often preferred for softer materials, while end mills, especially carbide end mills, excel in harder materials like steel and titanium.
- Efficiency and Precision: Select the tool that offers the required precision and efficiency for selected task, ensuring optimal performance and tool longevity.
Conclusion
Selecting the best end mill for machining needs involves careful consideration of several factors, including material compatibility, machining operations required, and tool longevity. Whether machining automotive components, aerospace parts or intricate medical devices, the choice between materials like carbide milling bits for steel or high-speed steel (HSS) can significantly impact performance and efficiency. Understanding the nuances between milling cutters, such as slot mills vs end mills, ensures selecting the right tool for the job, optimising precision and achieving high-quality surface finishes. By prioritising quality tools and informed decision-making, manufacturers can enhance productivity and maintain high standards of craftsmanship across diverse industrial applications.