- Published 24 Jan 2023
- Last Modified 9 Aug 2023
- 6 min
A Complete Guide to Spur Gears
Our guide is designed to help you understand how spur gears work, their advantages, applications, and sizes.

What is a Spur Gear?
Spur gears are straightforward, cylindrical precision gears with straight teeth and parallel shafts. They transmit motion between parallel shafts. Commonly used in a range of mechanical power transmission applications, these versatile components feature a simplistic yet effective straight teeth design. They are the most common gear type.
Spur gear teeth are parallel to the centre axis of the gear. For this reason, the engagement is more stepped and not as seamless as that of a helical gear. They are also known as straight cut gears.
Spur Gears vs Helical Gears
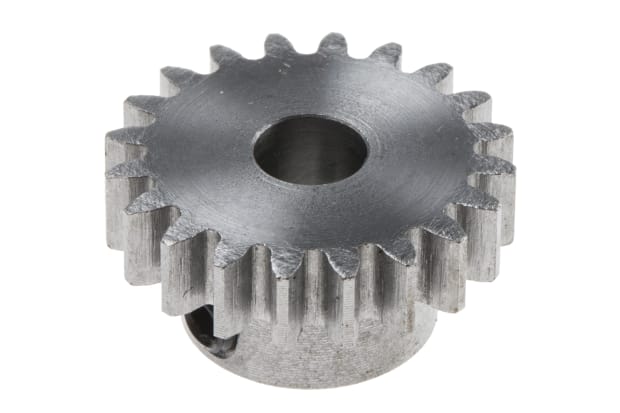
Spur gears and helical gears are both types of gears. However, there are key differences between the two types and it is important to understand how they vary.
As you can see from the image to the right, spur gears feature straight teeth mounted parallel to the gear’s axis. They can produce high levels of noise and vibration due to the way the teeth engage. They are commonly used in a range of devices, appliances and applications, and are often used in series.
Conversely, the teeth of helical gears are set on an angle to the axis. This helix angle allows the teeth to more gradually engage, resulting in a sweeping effect which creates a quieter, smoother operation. This reduced noise level is why helical gears are used in consumer vehicles instead of spur gears.
Spur Gear Applications
Spur gears can be used for a wide variety of applications. They are adaptable and versatile components, commonly used across a range of industries.
They are typically used to either increase or decrease the torque of a particular object. Spur gears can also be used for transmissions, torque multiplication, resolution, and accuracy within positioning systems.
Spur gears are commonly used in:
- Domestic appliances such as washing machines, dryers, and blenders
- Construction equipment
- Machining
- Fuel pumps
- Mills
- Mechanical transport systems
- Conveyors
- Motors and gear pumps
Although they can be used at most speeds, spur gears are usually used for lower speed applications. This is because their method of tooth meshing (one tooth at a time) is noisy and can cause high stress on the teeth.
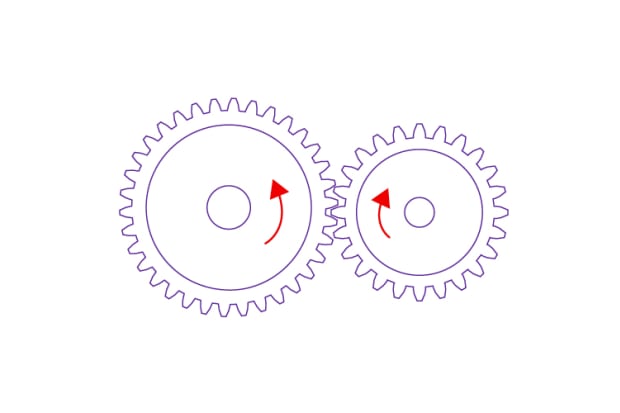
How Do Spur Gears Work?
Spur gear teeth are oriented in a straight line parallel to the shafts, which are coplanar. The teeth have an involute profile meaning that the gears only produce radial forces.
This diagram shows how the teeth on two gears mesh as they rotate. They make contact at a single point where the involutes meet. As the gears turn, this point moves along the tooth surface. The line of force is tangent to the base circles, meaning that the angular velocity ratio remains constant as the teeth mesh.
What is a Spur Gear Module?
Module size is a unit of measurement for gear tooth sizes under the International Organisation for Standardisation (ISO) guidelines. Therefore, a module is simply the unit of size that indicates how large or small a particular gear is.
It is calculated by dividing the ratio of the gear’s pitch or reference diameter by the number of teeth. This also means that the module is equal to the distance from the outside circle to the pitch circle.
Module is a metric unit which is equivalent to diametral pitch. Alternative units of measurement are also used, but this is the most common international unit.
Common options include:
What are the Advantages of Spur Gears?
Spur gears are simple and straightforward, yet highly versatile and suitable for use in a wide range of applications, industries and environments.
Key spur gear advantages include:
- They have high power transmission efficiency (typically between 95% and 99%)
- They are compact
- They are cost-effective and easy to install
- They offer a constant velocity ratio
- Unlike belt drives, spur gear drives will not slip
- They are highly reliable
- They can be used with high loads to transmit large amounts of power
- They are easy to produce and manufacture
- They feature a simple design
- They are suitable for use in small and constricted spaces
- They have high strength
These advantages make them highly useful components and have also contributed to their popularity and high level of usage. Straight cut gears are familiar in appearance, yet their simple design is what helps to make them so effective.
What are Spur Gears Made of?
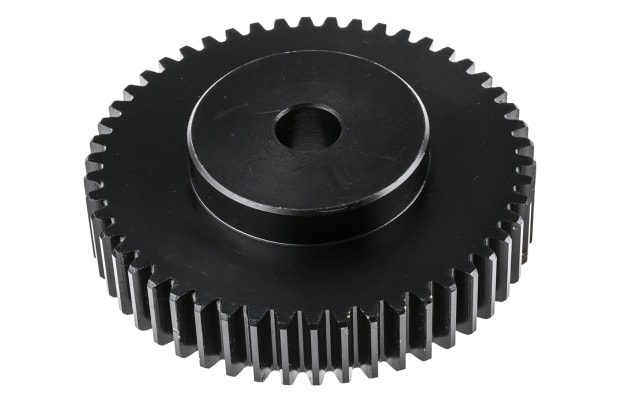
One of the main factors influencing gearing performance is its construction. Although the gear design itself is relatively straightforward, high-quality materials must be used to fabricate spur gears for maximum efficiency.
Spur gears can be made from metals such as steel or brass, or plastics and polymers like POM or acetal. Steel is typically case hardened to prevent premature wear.
Both metal and plastic gears have unique advantages. For instance, plastic gears produce less noise than their metal counterparts. However, steel and stainless steel spur gears are normally preferred as they are typically much more durable and long-lasting.
The selection of the most appropriate gear materials will ultimately depend on the torque needs to be transmitted. This is because plastic gears are not suitable for higher torque values. Plastic gears can be used for lower torques, whereas heat-treated steel gears are required for higher torque values. It is important to choose the right material to ensure the gear’s efficiency and reduce replacement or maintenance requirements.
Standard Spur Gear Sizes
Spur gear sizes are usually measured by module. This refers to the size of the tooth and a larger tooth size means more power can be transferred.
As well as this, gears can also be measured by:
- Number of teeth
- Bore diameter
- Hub diameter
- Pitch diameter
- Face width
Multiplying the module of a gear by pi will give you its pitch. This is the distance between consecutive threads and teeth.
These measurements can help you to identify the right-sized spur gear for your particular application. It is useful to accurately measure and record these sizes as this can help when working in systems where a precise size is required. Gears must be fabricated to precise dimensions in order to ensure maximum effectiveness.
Mating gears must have the same module. A spur gear of the wrong size could mean that meshing does not occur fully, or the gear could stick if it does not smoothly mesh. This could result in increased wear and tear, damage to the gear pair, increased noise levels and vibration, or it could even prevent the system from functioning correctly. Therefore, choosing the right sized gear is imperative.
Related Guides
Related links
- Spur Gears
- RS PRO Steel 12 Teeth Spur Gear 5mm Bore Diam 9mm Hub Diam
- 1 Spur Gears
- RS PRO Steel 25 Teeth Spur Gear 6mm Bore Diam 14mm Hub Diam
- RS PRO Steel 40 Teeth Spur Gear 4mm Bore Diam 9mm Hub Diam
- RS PRO Steel 60 Teeth Spur Gear 4mm Bore Diam 10mm Hub Diam
- RS PRO Steel 12 Teeth Spur Gear 8mm Bore Diam 14mm Hub Diam
- RS PRO Bronze 1 Module Worm Wheel Gear 30 Tooth20mm Hub Dia., 30mm...