- Published 30 Jan 2023
- Last Modified 29 Aug 2023
- 7 min
A Complete Guide to Plate Heat Exchangers
Read our plate heat exchangers guide, explaining what they are, their uses, the main types, and their advantages.

What is a Plate Heat Exchanger?
Plate heat exchangers are devices used to transfer heat from one fluid to another. The fluids do not come into direct contact - they are kept separate by metal transfer plates laid parallel to each other. In other words, these devices work via the principle of indirect heat exchange, in which heat is transferred via an intervening medium.
Plate heat exchangers are used with water, oil, refrigerant and other fluids. In larger commercial models, the plates responsible for the transfer of heat are bolted together with supporting bars and sealed by rubber gaskets. In smaller models, by contrast, the plates are normally joined directly to each other.
Hot and cold liquid flows in opposing currents - typically parallel to each other - through separate channels or tubes in the spaces between each plate, from the inlet tubes to the outlets. A lengthy, irregular channel for hot fluid runs alongside one side of each plate, and a channel for cold fluids alongside the other. Each channel creates a large surface area for the fluid to emit or absorb heat. The amount of heat transferred over an area is referred to as the heat transfer coefficient. An additional fixed plate secures the device and a flexible plate responds to pressure.
The transfer plates are typically made from stainless steel, which is noted for its strength, corrosion resistance, and ability to withstand high temperatures and pressures. It is also food-safe, so can be used with food, drink and pharmaceutical products. However, some models feature non-ferrous metals such as aluminium, copper and titanium.
Plate heat exchangers are also known as plate and frame heat exchangers.
How Does a Plate Heat Exchanger Work?
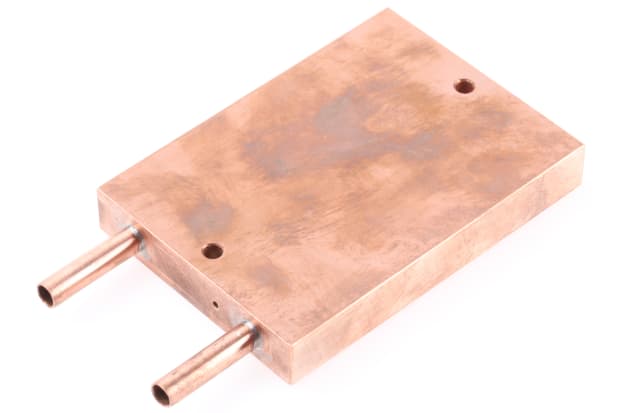
So, how do heat exchangers work? The underlying theory depends on a law of physics that states heat will always dissipate from a warm substance or material if the surrounding environment is cooler, while colder substances will absorb heat from the same environment.
For a plate heat exchanger to work, there must be a temperature difference between the liquids on each side of the device.
These are kept separate from each other in sealed channels or tubes running along the surface of the transfer plates. They feature intricate corrugated patterns and irregularly-shaped channels and troughs to create turbulence within the liquid. This encourages heat transfer and a vigorous flow of fluids while discouraging fouling, or stagnation. Corrugations also make the exchanger structurally stronger and create a large surface area within a relatively small device, maximising the heat transfer efficiency.
The heat will dissipate from the hot medium and, thanks to the tight design of the exchanger, be absorbed directly by the cold medium, which can be as little as 1°C. The amount of heat absorbed by the latter will be almost equal to the amount lost by the former, except for a small amount of heat lost in the environment.
Plate Heat Exchanger Applications
Plate heat exchangers are versatile devices with a variety of uses and applications in industry. Let’s look at some of the locations in which these devices are used:
- In heating, ventilation and cooling (HVAC) systems, to connect boilers and chillers and recover heat
- In industrial applications, to recover waste heat or cool products before packaging or bottling. In the latter case, the device will be connected to a chiller
- Evaporation and condensation of water vapour
- Process engineering (product manufacture), including laser equipment
- Connecting buildings and apartments to district-wide heating and cooling networks
- In heavy industry and oil refineries
- In water-based heat pumps
- In calorifiers (water heaters)
- In medical equipment that requires cooling - e.g. MRI scanners
Types of Plate Heat Exchanger
Plate heat exchangers are available in a variety of models. Let’s look at the principal heat exchanger designs:
Brazed Plate Heat Exchangers
Compact and with high power efficiency, brazed plate heat exchangers are a common inclusion in hot water systems, industrial and refrigeration equipment. Brazing is a process like soldering in which two pieces of metal are joined by melting a third metal onto the join and baking this into place. Brazed plate heat exchangers normally feature stainless steel brazed by copper or nickel, making them highly resistant to corrosion.
Brazed plate heat exchangers cannot be opened. Cleaning is conducted by flushing the device with a suitable cleaning agent.
Gasketed Plate Heat Exchanger
Gasketed plate heat exchangers feature rubber gaskets between the transfer plates. These create watertight seals and control flow rates. These larger, higher capacity models are standard equipment in food and drink production and heating, process engineering and HVAC systems.
The gasket seals mean that these devices are easy to disassemble for maintenance and cleaning. Additional plates can also be added to increase the capacity and thermal flow of the device.
Plate-Fin Heat Exchanger
Plate-fin heat exchangers feature finned chambers alongside the heat transfer plates, the latter typically made from aluminium. These models are usually more compact than other plate heat exchangers but still offer a large heat transfer surface area.
Plate fin heat exchangers, also known as plate-fin and tube exchangers, are favoured in industries that require lightweight heat transfer equipment. Examples include aerospace, vehicle engineering and cryogenic chemical processing.
Welded Plate Heat Exchanger
Welded plate and frame heat exchangers feature plates that have been welded together into a single block. This makes maintenance more difficult and means that the capacity of the devices is fixed because additional transfer plates cannot be added. However, it also makes welded plate heat exchangers highly durable - they can withstand corrosive fluids, high temperatures, and pressures. As a result, they are widely used in heavy industry - you will find them in oil refineries, gas extraction plants, power stations and similar locations.
Semi-welded plate heat exchangers are a variant model, combining welded and gasketed plates. Welded plate sets are connected via gaskets to other sets. Therefore, the fluid channels through this device alternate between gasketed and welded seals. This allows hot fluid and corrosive liquids to be directed to one side while servicing is conducted on the other.
Advantages of Plate Heat Exchangers
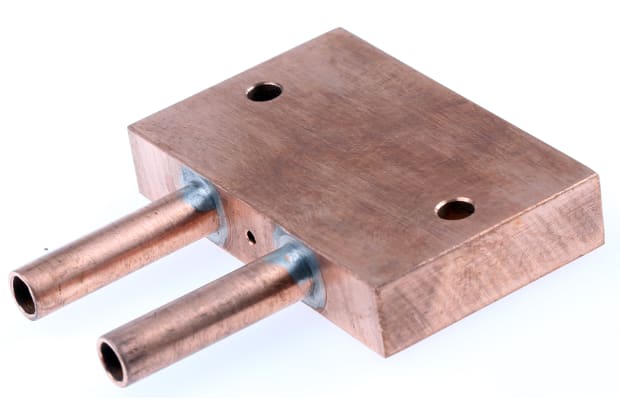
When compared to other similar equipment, exchangers offer several advantages:
- They are relatively inexpensive, both to purchase and to run on an ongoing basis as they consume low levels of energy
- Most models are easy to install and require little maintenance. Broken parts can be replaced
- They offer precise control over the rate of heat transfer
- They are less prone to wear, corrosion and waste generation than comparable heat transfer equipment
- Heat transfer plates are flexible, and some models can be expanded with the addition of extra plates, increasing the total area available for heat transfer and improving the heat transfer coefficients
However, like any other technology, plate heat exchangers do not suit every use case. Their disadvantages include:
- They can only operate in a limited range of temperatures
- Gas and liquid flow is relatively small, so plate heat exchangers are not suitable for steam-powered equipment or transfer between gases
- Exchangers produce only modest levels of pressure
- Liquid flow through larger models can be uneven, with more fluid gathering in the first channels within the device
Plate Heat Exchanger Sizing
So, what size heat exchanger might you need? Sizing depends on where and how you plan to use your exchanger.
Plate heat exchangers can vary significantly in size. Available sizes range from:
- 9.7 x 32 x 51 mm (or 0.97 x 3.2 x 5.1 cm) at the lower end
- 524.4 x 112 x 24.1 mm (or 52.44 x 11.2 x 2.41 cm) at the higher capacity end
Meanwhile, transfer plate sizes run from:
- 100 mm x 300 mm (10 cm x 30 cm) on the smaller side
- 1000 mm x 2500 mm (100 x 250 cm) on the larger side
There can be anything from ten to hundreds of transfer plates in a single model.
You should assess the amount of liquid you will need to process, pressure, and the planned location of the device, then purchase accordingly.
Related Guides
Related links
- Plate Heat Exchangers
- Xylem Brazed Plate Heat Exchanger, 309.6 x 112 x 24.1mm
- Xylem Brazed Plate Heat Exchanger, 214.5 x 80.7 x 24.1mm
- Xylem Liquid Heat Exchanger, 214.5 x 80.7 x 24.1mm
- Xylem Liquid Heat Exchanger, 309.6 x 112 x 24.1mm
- Xylem Liquid Heat Exchanger, 397.5 x 80.7 x 24.1mm
- Thermo Electric Devices Liquid Heat Exchanger, 12.7 x 89 x 64mm
- Xylem Plate Heat Exchangers