- Published 18 Apr 2023
- Last Modified 29 Aug 2023
- 8 min
Guide to Peristaltic Pumps
What are peristaltic pumps, and how do they work?

Here’s a quick guide to peristaltic pumps. They are a precise, effective type of pump with a host of advantages for specialist applications, particularly at lower volumes.
What are Peristaltic Pumps?
There are dozens of types of pumps, but the vast majority belong to one of four families - positive displacement, impulse, velocity and gravity. Positive displacement pumps work by trapping fluids in an enclosed volume and moving it from the inlet to the outlet in a continuous motion. Peristaltic pumps belong to this type.
In theory, once a positive displacement pump is stopped, the flow will stop, in that fluid won’t be allowed to flow backwards or forwards, rather like closing a valve. In practice, there might be tiny gaps that could potentially let small amounts of fluid through, which might be necessary to prevent abrasion of moving parts. However, these narrow gaps should be so disruptive as to effectively stop flow. In many pump types, by contrast, if it is switched off, there is still a route through for the fluids, which means that flow may continue through it given a source of pressure somewhere in the system, and that could mean that flow could go backwards, which is often undesirable.
How Do Peristaltic Pumps Work?
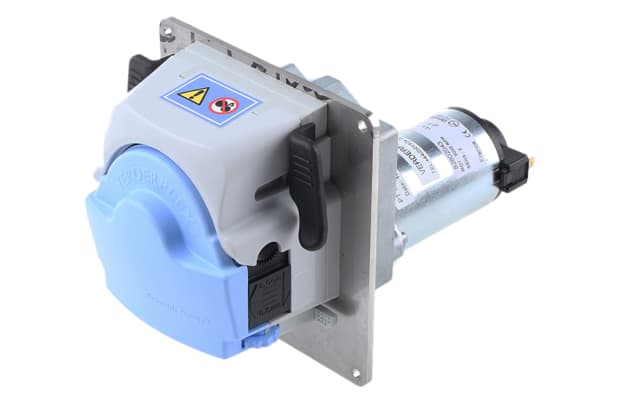
If you have ever squeezed every last drop of milkshake from a straw with your fingers, you’ll have an idea of how a peristaltic pump works. There is a flexible tube containing the fluid, and a component to compress it from the outside (just like your fingers on the straw), called a shoe or a roller. The roller moves along the tube and forces the fluid out in the direction of travel. Because it creates a vacuum on the other side of the roller, fluid behind the pump will be sucked into the system, and the process continues.
In practice, peristaltic pumps are not generally arranged in a straight line like a drinking straw, however. It is much better to have the tube arranged in a circular or semi-circular shape and to have a roller or shoe mounted on a pump at the centrepoint of the circle. The shoe progresses around on a motor, squeezing the tube from the outside, and then comes around again to continue the process.
Clearly, if there were just one roller on a tube arranged in a semicircle, that would mean there would be periods where it was not pressing on the tube, namely when it was coming around to start its next cycle. For that reason, there are multiple rollers, usually two, three or four arranged 180°, 120° or 90° apart. That will ensure there is always a section of the tube that is completely enclosed, and that the pump can always be started and stopped without the need to prime it. Multiple rollers equally spaced will also prevent stress on the pump shaft and stop it from bending away from the tube over time.
While most peristaltic pumps have the tube in a semicircular mount, they do exist with a full 360° rotation. It’s sometimes useful when the application requires a straight tube rather than one doubling back on itself, although it’s easy to curl the tube through 180° before or after the pump.
Advantages of Peristaltic Pumps
Peristaltic pumps come with a number of advantages for certain applications. Here are the key benefits of this type of pump:
- The fluid only comes into contact with the tube. In most pump designs, the fluid will touch the outer casing, blades, gears, valves, seals, diaphragms and possibly even lubricants as it passes through. Each one of these is a source of potential contamination of the fluid, which in many industrial, medical and pharmaceutical processes is unacceptable. In the peristaltic pump, the tube can run continuously from one part of the process to the other and merely passes through the pump. It also means there is no means of escape for the fluid to the outside world
- They can run very slowly. This type of pump does not require enormous amounts of energy or momentum to get the fluid moving. The shoes can move around very slowly and deliver a gentle supply of fluid, where desired
- They are good for viscous fluids. Viscous fluids that can’t be pumped by a velocity pump can often pass smoothly through a peristaltic one
- Precise measurement is possible. Because the volume within the chamber between shoes is a known quantity, precise volume measurements can be achieved simply by counting revolutions or fractions of a revolution
- They can run dry. There’s no risk of damage if the tube runs dry as the system doesn’t rely on the fluid for cooling or preventing the motor from overspeeding
- They are reversible. The process is exactly the same in whatever direction the shoes are moving, so it can be reversed, which might be useful in some applications, but is also good for flushing and clearing blockages
- No need for external valves. Although valves can be incorporated into the tubing to ensure flow is stopped, stopping the motion automatically stops the flow, rather like a diaphragm valve
- Tubing can be transparent. Although they are often opaque, tubes can be transparent to keep an eye on the flow and colour of the fluid
Drawbacks of Peristaltic Pumps
The system is not without its drawbacks, which can rule it out of some applications:
- The tube can fatigue. After hundreds of thousands of compression and release cycles, the walls of the tube can perish and potentially split. In mitigation, however, they do tend to run relatively slowly, and modern tubing materials have phenomenal durability. With a well-observed inspection and maintenance regime, this downside can be discounted
- The flow tends to be pulsed rather than smooth. The constant injection of single batches of fluid, and the inevitable gap where the shoe or roller is, tends to cause a pulsating flow. This is sometimes desirable, however
- The tubing needs to be unreactive with the fluid. Certain fluids will react with certain tubing materials, so the material has to be chosen carefully to avoid contamination or corrosion
Types of Peristaltic Pumps
Within peristaltic pumps, there are a few main types.
Peristaltic Dosing Pumps
Where very precise (and often small) doses of a fluid need to be injected into another fluid, the peristaltic dosing pump is a good way of delivering controllable and measurable amounts in a short burst, rather than continuously. Low-flow peristaltic pumps are vital in medicine and many chemical processes.
Peristaltic Hose Pumps
While many peristaltic pumps can fit in the palm of your hand and connect small-volume tubing, there are some that have higher volume delivery, namely peristaltic hose pumps.
Small Peristaltic Pumps
This type of pump comes into its own at a small scale, where incredibly precise volumes can be delivered by measuring and controlling the motor’s rotation, by fractions of a rotation if necessary.
Industrial Peristaltic Pumps
There are some applications where peristaltic pumps are useful at the large industrial scale, for example when moving thick sludges and sewage with lumps of solid matter in them. Many other types of pumps simply cannot handle such fluids.
What are Peristaltic Pumps Used for?
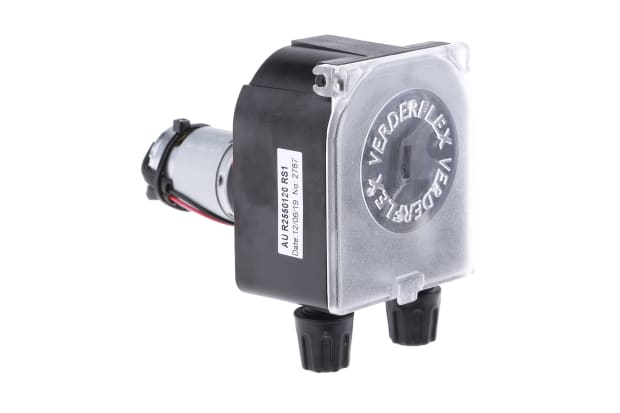
With a few notable exceptions, peristaltic pumps tend to be on a smaller scale, as they don’t excel in shifting large volumes of fluid quickly. But when controllability, precision and low volume are essential, they are perfect.
One of their most important applications is in the medical setting, where precision and predictable fluid delivery is vital. They are used to pump blood during open heart surgery and for dialysis machines. The pharmaceutical industry uses them in its manufacturing processes for certain drugs, where precise concentrations of certain molecules need to be known so that clinicians can confidently prescribe doses to patients.
The same applies to food manufacturing, particularly to mass production. Once a recipe has been finalised, it needs to be consistently applied in the factory, with precise amounts of ingredients going into the mix. Peristaltic pumps facilitate that precision. If you’ve ever had paint custom-mixed in the hardware store, there’s a good chance the individual dyes will have been injected using peristaltic pumps to ensure the exact shade you’ve ordered.
On a larger scale, some concrete pumps are peristaltic. It’s a useful way of moving wet concrete, full of aggregate, up to heights so it can be poured and produce a single, homogeneous slab, which isn’t always possible with multiple buckets. It also guarantees the heavy concrete mix will not flow back down the pipe when the flow is stopped.
Exploring Efficiency and Flow Rate
When you’re choosing a peristaltic pump, it’s essential that you know its maximum flow rate, head, pressure and operating temperature. You need to ensure any pump you choose can handle the specifications set by the engineers for its proposed use. Choosing a pump that will work near or outside its intended flow rate will adversely affect its efficiency, and could even prevent it from delivering fluid anywhere near your required levels. Always check the specifications to ensure you choose a suitable pump for your requirements.
Further Reading
Related links
- Positive Displacement Pumps
- Peristaltic Pumps
- Verderflex Peristaltic Electric Operated Positive Displacement...
- Verderflex Peristaltic Electric Operated Positive Displacement...
- ProMinent Peristaltic Electric Operated Positive Displacement...
- Verderflex Peristaltic Electric Operated Positive Displacement...
- Verderflex Peristaltic Electric Operated Positive Displacement...
- Verderflex Peristaltic Electric Operated Positive Displacement...