- Published 21 Sept 2023
- Last Modified 18 Apr 2024
- 8 min
Maintaining Energy Efficiency in Industry
The UK, China and the US are among the biggest emitters of carbon dioxide globally, with manufacturing contributing about a quarter of those emissions. Introducing industrial energy efficiency measures at your plant will cut energy usage and help combat climate change. Not only that, the bottom line of your business will benefit too.
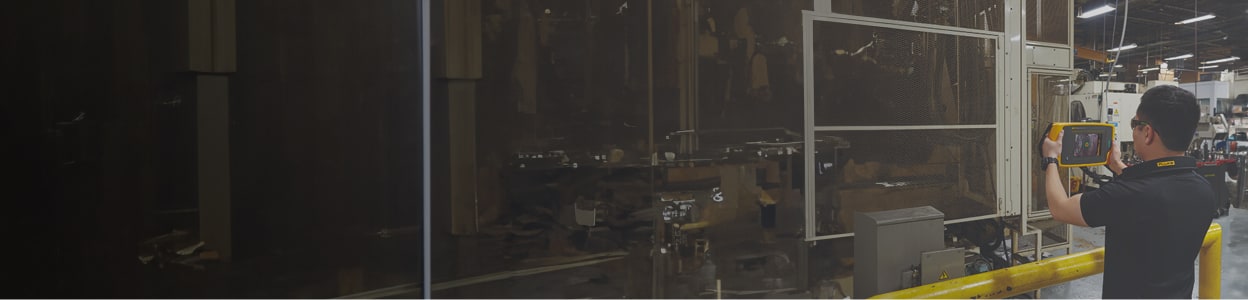
Carbon dioxide (CO2) emissions are one of the leading causes of global warming. Carbon dioxide is emitted when fossil fuels such as coal, oil and natural gas are burnt to generate electricity, fuel industrial processes, keep cars and trucks on the road and aircraft in the air, and heat our homes.
If catastrophic global warming is to be avoided, emissions need to be drastically reduced from all parts of the economy. That’s why manufacturers are making their operations more energy efficient. Read on to find out how the industrial energy efficiency accelerator is cutting emissions.
CO2 Emissions by Industry
Who are the big carbon dioxide emitters? By country, it’s the most industrialised nations that are the culprits: China, the US and countries in Europe. That means manufacturers in those places (and elsewhere) have an enormously important role to play in combating climate change, with industry worldwide responsible for about 24.2% of global greenhouse gas emissions. The most polluting industrial sectors are:
- Chemical and petrochemical
- Iron and steel
- Food and tobacco production
- Non-ferrous metals (e.g. aluminium) production
- Paper and pulp
- Machinery manufacturing
- Other industry (including mining, construction, textiles and wood production)
Manufacturers are already taking huge steps to significantly reduce greenhouse gases. For example, in the UK, manufacturing now produces about 40% less emissions than it did back in 1990. But there’s a lot more work to be done. Britain has a target of reaching net zero emissions by 2050, which will require more cuts from industry, and a level of energy efficiency industrial companies have seldom seen. That’s along with the ongoing decarbonisation of electricity generation, transport and heat.
Reducing emissions from energy-intensive sectors
Particularly energy-intensive sectors include cement production, oil and gas, and iron and steel and fertiliser production. The fact that these industries are especially energy-intensive makes their decarbonisation challenging. However, there’s a range of technologies out there that can help. These include energy efficiency heating and cooling, renewable electricity and renewable fuels such as biomass or hydrogen, as well as electrification of processes that formerly relied on oil or natural gas, not to mention other technologies that are at a relatively early stage of deployment such as carbon capture and storage.
But another key means of reducing CO2 emissions is energy efficiency. Just as many consumers are saving money on their bills by using less electricity and gas, industrial companies can do the same. Energy efficiency has the advantage of requiring common sense ways of decarbonising an industrial business that also save money.
For example, introducing an LED lighting energy efficiency system has the potential to dramatically reduce energy consumption. Improved thermal insulation of steam and hot water networks, or leak control and pressure optimisation of systems running on compressed air, may also be quick energy efficiency heating wins. Manufacturers can also look at changing employee behaviour to reduce energy demand. These types of projects tend to not only cut emissions but also represent a good return on investment, because schemes such as encouraging workers to turn off lights or computers cost very little to implement.
Improving Industrial Energy Efficiency
Maintenance professionals and engineers can improve the energy efficiency of their plant via the adoption of a number of technologies. Let’s take a look at some of the more common energy-efficient systems:
Energy Efficient Electric Motors
According to industrial giant ABB, electric motors consume about 45% of the world’s electricity. Adoption of energy-efficient electric motors has the potential to cut global electricity consumption by about 10%, it says. So one of the ways maintenance engineers can help combat climate change is by adopting these newer energy-efficient motor designs (energy efficient motors produce more mechanical power relative to electrical power consumed).
The International Electrotechnical Commission has made the process simpler by creating four efficiency classes for single speed electric motors from 120W to 1,000kW: IE1, IE2, IE3 and IE4 (standard efficiency, high efficiency, premium efficiency and super-premium efficiency).
Maintenance techs and engineers specifying an IE3 electric motor can achieve approximately 96% efficiency, and about 97% efficiency with an IE4 design. In fact, by specifying IE4 energy-efficient motors, engineers can cut power consumption to produce the same amount of work as a less efficient motor and thereby reduce the carbon footprint of their factory.
HVAC Energy Efficiency
In maintaining the ambient temperature in a manufacturing plant, air conditioning systems use a lot of electricity, accounting for 10% of global electricity consumption and about 4% of emissions. So, making heating, ventilation and air conditioning equipment more efficient has a lot of potential.
Steps engineers and maintenance professionals can take to improve HVAC energy efficiency include checking for leaks in the system such as escaping refrigerants (which in themselves are potent greenhouse gases); scheduling regular maintenance of HVAC systems, ensuring that the system is the right size for the job (oversized HVAC units consume more power); and using variable speed fans and motors for improved energy efficiency. Are your HVAC air filters functioning properly?
Efficient Gas Turbines
Gas turbines are commonly used to provide power in industry sectors including chemicals, cement manufacturing, oil and gas, and metals and mining. The ratio of work produced by the turbine to net input energy in the form of fuel is its measure of efficiency. Efficient gas turbines produce more work for less fuel. Leading manufacturers of gas turbines are reducing emissions of a number of harmful gases in their latest technology, including not just CO2 but also carbon monoxide and nitrogen oxide. At factory scale, they are also working on gas turbine technologies for manufacturers that improve efficiency while cutting greenhouse gas emissions.
Digital emissions reduction
Digital technology consumes huge amounts of energy but also has the potential to reduce emissions. Energy efficiency in building management, where networks of sensors and software are capable of controlling HVAC systems so that they use less energy in unoccupied areas, is one example. Smart lighting – which uses sensors to optimise the level of light at certain times of day or according to weather patterns – is another. AI also has huge potential as a tool for optimising industrial processes to save energy.
Your Energy Efficiency Strategy
In a large manufacturing facility with a big footprint, production equipment and maintaining the right environmental conditions are often very large consumers of energy. Large manufacturers should consider that the upfront cost of a new machine is often very small compared to the amount of energy it will consume over its lifecycle. So selecting energy-efficient machinery when replacing equipment is a good investment.
Indeed, cutting carbon dioxide emissions and saving money go hand-in-hand for large manufacturers, even if it means upfront investment in new technology. To calculate the return on investment of an energy efficiency project, estimate the cost versus projected savings over time. Calculate the return by dividing the savings by cost and expressing the result as a percentage.
The Energy Saving Trust says that small and medium-sized engineering companies can get in on the act and save up to a quarter on their bills by implementing some straightforward energy efficiency measures. The Federation of Small Businesses recommends starting by collecting data on energy usage and introducing a range of measures including installing smart metres and LED lighting and considering fitting new insulation.
Want more ideas on how to improve energy efficiency in industry? You could try:
- Implementing an energy management standard (ISO 50001 provides a means of carbon reduction through energy efficiency)
- Maintaining equipment properly to reduce energy wastage
- Continuously improving operations
- Turning off lighting when it’s not needed
- Using timers to only heat or cool the premises when employees are present
- Replacing older heating and cooling systems with energy efficient models
Taking practical measures like these will help to improve your plant’s energy consumption, not only saving you money but also changing the world for the better. And not before time. Despite the progress made in the UK in cutting CO2 since 1990, emissions from manufacturing in Britain in 2020 still stood at 48,350,000 tonnes, according to the UK Energy Research Centre.
There’s a lot more to do as we race toward that 2050 net zero emissions target.
Did you know RS carries a full range of products to make your plant more energy efficient? Check out our LED strip lighting here.
Related Articles
Related links
- Switching to Efficient Industrial Lighting
- Energy Efficiencies of Solar Panels and Solar Cells
- Guide to the Future of UK Renewable Energy
- What is Power Factor Correction (PFC)?
- Industry 5.0: Its Meaning and Impact
- Guide to Sustainability in the Pharmaceutical Industry
- New Battery and Energy Storage Technologies
- Home Appliance Solutions from Infineon | RS