- Published 30 Jan 2023
- Last Modified 29 Aug 2023
- 8 min
A Complete Guide to Check Valves
Read our check valves guide to understand what they are used for, how they work, the different types and materials.

Updated April 2022
What is a Check Valve?
Let’s start with the fundamentals - what is a check valve? They are a type of valve designed to prevent or check the backflow of water, other fluids or gases within a system of pipes.
Fluid or gas that passes through a check valve can only move one way. It is important to minimise or entirely prevent backflow as it can cause contamination or damage equipment, with potentially serious consequences.
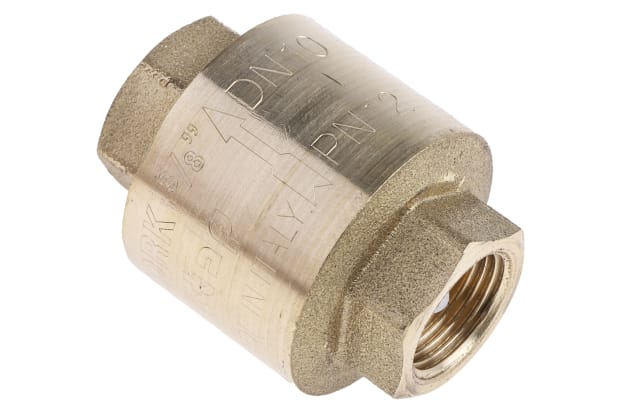
They have several alternative names, including:
- Non-return valves (although these are sometimes distinguished)
- One-way valves
- Reflux valves
- Foot valves
- Retention valves
- Stop valves
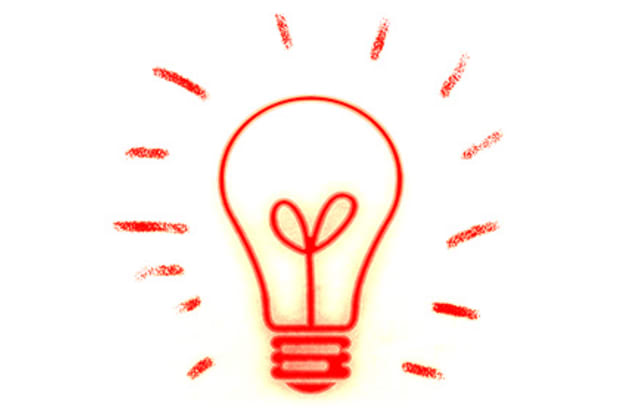
What Does a Check Valve Do?
These valves open or close in response to the flow within the pipe. These simple but robust mechanical devices require no human intervention, so there are no handles or levers, unlike other types of valve. They are built to resist the stresses and vibration inherent within plumbing and pipeline systems.
What are Check Valves Used for?
They are a standard component, used in multiple industries. They are used to prevent fluid and gas from flowing in the wrong direction. Some of the most common uses include:
- In pump outlets to keep water moving in the right direction. Centrifugal pumps, one of the most widely used types of water pump, are not self-priming (they cannot expel air from their tubes before operation) so check valves keep water moving until the air within the pump has been separated from the incoming water and expelled
- In heating, ventilation and air conditioning (HVAC) systems, especially those installed in larger buildings. These can require coolant to be pumped up multiple floors and check valves play an important role in beating gravity and ensuring that none of the coolant flows back in the wrong direction
- To protect drinking water from exposure to other types of water, or to stop the spread of possibly contaminated water back up the pipe
How Does a Check Valve Work?
This type of valve works via simple, tried and tested principles.
Spring type non-return valves respond to differences in pressure. Fluid enters via the narrow end of the cone, pushing against the ball bearing. The spring will give in that direction, allowing the fluid to flow through. However, if the water, gas or steam changes direction, the spring-loaded ball bearing will be pushed back into the narrow end of the cone, blocking the inlet and preventing backflow.
The minimum difference in pressure at which a valve will operate is called its cracking pressure. These valves can be calibrated for specific cracking pressures.
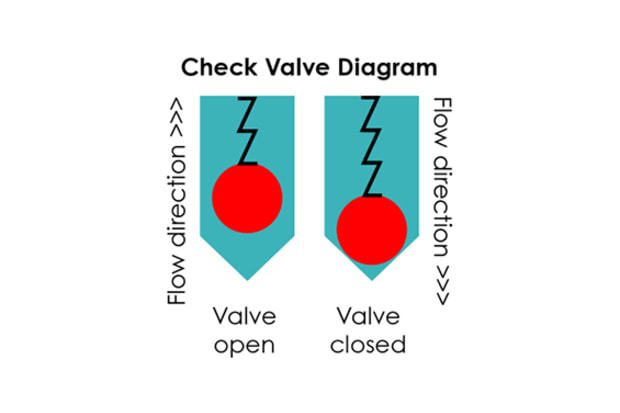
Non-Return Valve Diagram
The diagram to the right illustrates the basic operating principles of a non-return valve.
The details of each valve vary by model and intended use, but almost all are tubular in design with entry and exit points. They also rely on one key component - a ball bearing or disk on a spring, sitting within a cone-shaped housing.
Check Valve Types
Check valves are available in several different sizes and shapes, for use in everything from standard pipes to industrial pipelines. Each non-return valve type is designed for use in different applications. The principal types include:
Ball Check Valves
This standard one-way valve design features a ball bearing mounted on a spring that moves up and down in response to pressure within the valve.
Swing Check Valves
These work on the same principle as ball types but feature a disk, or flapper, instead of a ball bearing. These may be attached to a shaft. They move in response to pressure, swinging open as fluid or gas enters and then quickly falling back into place to block reverse flow and seal the valve. An effective choice for systems prone to pressure surges, these models are also known as tilting disc or flapper valves.
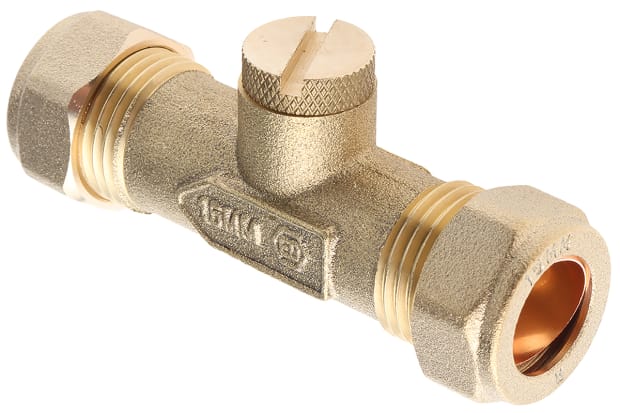
Double Check Valves
A double check valve consists of two attached units. Single check valves provide a good level of protection but they can be doubled in settings where it is essential to prevent contamination through backflow - for example, in drinking water pipes. The additional valve creates a stronger seal and can also act as an emergency backup if the first seal fails.
Lift Check Valves
These feature a disc mounted on a spring that will lift vertically from the seat of the valve in response to fluid pressure. Its cracking pressure must be sufficient to overcome gravity. Backflow will reverse this movement. The valve may need to make a 90-degree turn when moving in each direction.
A stop check valve is a variation of the lift type, incorporating a stem that can be closed to prevent the disk from moving away from the valve seat, to create a tight seal.
Clapper Valves
Clapper valves are used in firefighting systems. They feature a hinged gate that opens in the direction of the incoming liquid and closes when there is no forward pressure.
Reverse Check Valves
Reverse flow valves are used in gas lifts and similar equipment to prevent backflow and fluid mixing and to allow the circulation of pressure.
Inlet Check Valves
Inlet types are used in vehicles to prevent fuel from spitting or spilling back out - called wellback - when refuelling.
Non-Slam Check Valves
A non-slam valve is a variation of the swing type in which the disk cannot slam shut in response to backflow. Instead, a pressure-sensitive spring moves the disc in a smooth motion.
Low-Pressure Non-Return Valves
These are designed to be sensitive to low-pressure fluid or gas flow in which standard models might not function properly.
Two-Way Check Valves
These are specialist types of valve used in air braking systems. Two input circuits apply pressure to a moving component called a shuttle. The highest pressure is then directed to the output and from there to the brakes themselves.
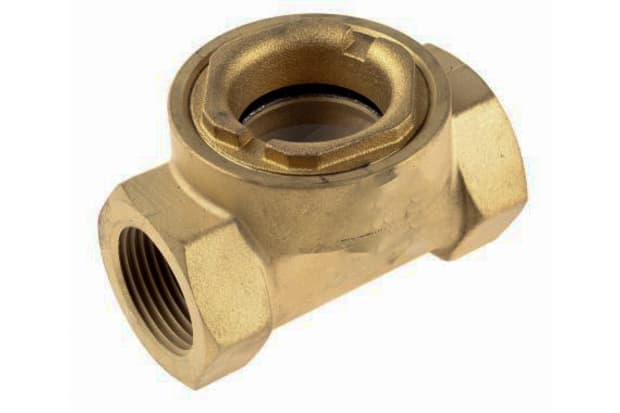
Sight Glasses
Sight glasses are pipeline components with an integrated, reinforced window to enable operators to conduct a visual inspection. They are principally used with steam boiler-based systems. Some models contain an integrated check valve.
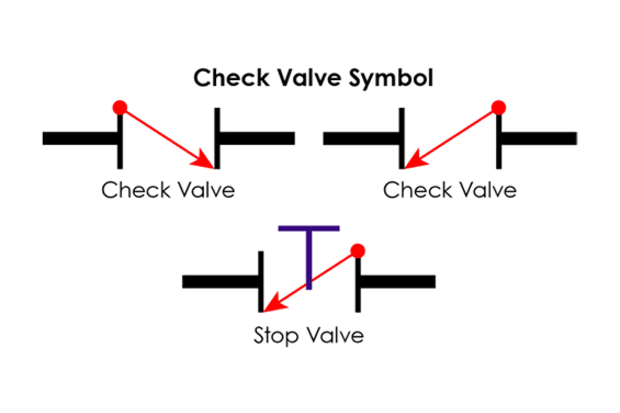
Non-Return Valve Symbols
Piping and instrumentation diagrams (P&ID) are a series of conventional symbols used to indicate valves and equipment in schematics. Symbols for one-way valves indicate the direction of flow within the device.
The P&ID symbol for the non-return valve is displayed to the left.
Thread Size
Check valves feature threads of varying sizes in either male or female format. These enable the valves to be inserted into compatible pipes. Here are some of the most common thread sizes:
- ½ inch (12.7mm)
- 0.59 inches (15mm)
- ¾ inch (19.05mm)
- 1.5 inches (38.1mm)
- 2 inches (50.8mm)
What are Check Valves Made of?
Non-return valves are made from plastics and metal, in particular:
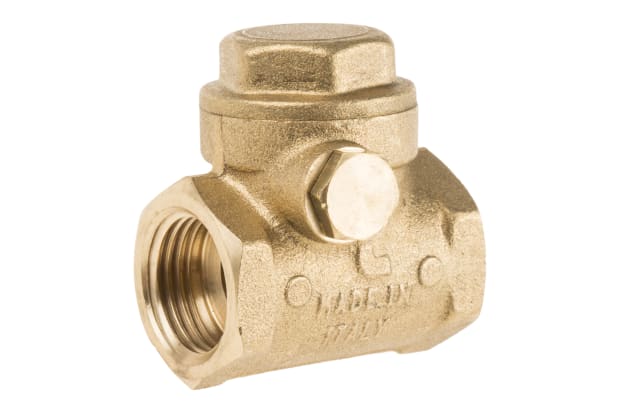
Brass
Brass check valves are a versatile choice for low-pressure piping but are not a good choice for purified water, chlorinated water or seawater. They are less resistant to heat and corrosion than stainless steel.
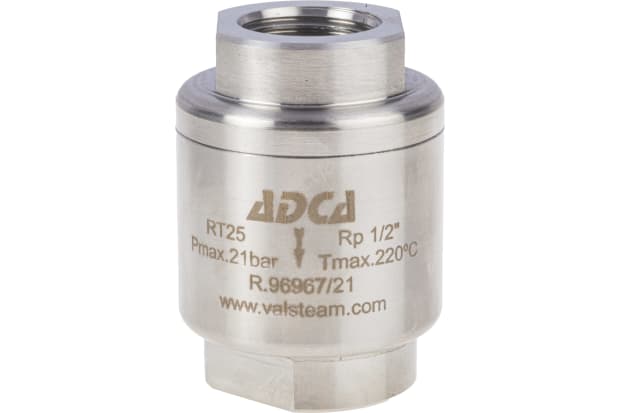
Stainless Steel
Valves made from stainless steel are highly robust and can withstand both high and low temperatures. However, they are less cost-effective than brass or plastic models.
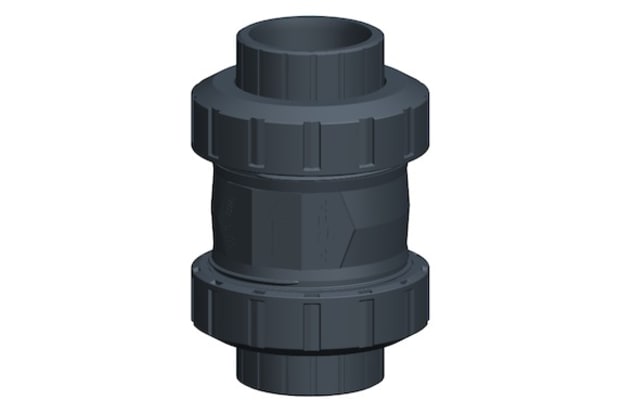
PVC
Polyvinyl chloride offers excellent resistance to corrosive substances like acid, seawater and solvents, but should not normally be used in environments above 60°C.
FAQs
What are Check Valves in Series?
When two valves are fitted together, this is known as a double check valve or a check valve in series. They are principally used in water pipelines to prevent contamination. Connecting two valves creates a redundancy so that if one fails or jams, any backflow will still be stopped. Each valve also reduces pressure on the other, creating a firmer seal.
What is the Difference Between a Check Valve and a Non-Return Valve?
Since the 1970s, a technical distinction has been made between check valves and non-return valves (NRVs). The former is a higher performance version of the latter. Non-return valves are normally used in settings where it is desirable to prevent fluids moving in the wrong direction but not crucial to do so - for example, water-based radiators. Despite this, however, the terms check valve and non-return are often used interchangeably.
Check valves in the UK are normally subject to more rigorous testing than non-return valves. In addition to being water-tight, they must also be durable and suitable for use with drinking water.
What is a Non-Return Valve on a Boiler?
Steam boilers are common heating solutions. The steam generated by the boiler is circulated around the building in pipes. Heat is emitted by radiators before the steam is eventually vented. Industrial steam boilers are also used in manufacturing processes and to generate electricity.
Non-return valves prevent steam from drifting back up into the boiler, which is potentially dangerous, especially if the boiler has failed or been shut down.
Related Guides
Related links
- Watts Check Valves
- Parker Hydraulic Check Valves
- JG Speedfit POM Double Check Valve 15mm, 12 bar
- Legris Pneumatic Non-Return Valves
- Parker Steel Non-Return Valve Check Valve 400 bar
- Parker Steel Non-Return Valve Check Valve 400 bar
- RS PRO Brass Non-Return Valve Check Valve 16 bar
- RS PRO Brass Non-Return Valve Check Valve 16 bar