- Published 14 May 2024
- Last Modified 14 May 2024
- 8 min
How Engineering Fits into Industry 4.0
Learn how engineers can adapt to and thrive in the interconnectivity of Industry 4.0 as it increasingly becomes a part of all engineering industries.
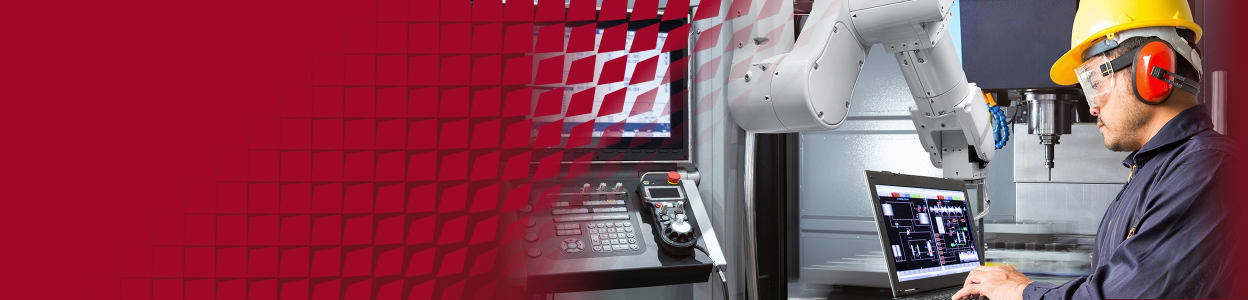
Reviewed by Allister Steel, Solution Engineer (April 2024)
As Industry 4.0 and the IIoT revolutionise how products are designed and made, engineers will need to continually adapt their skills, knowledge, and practices to fit into this space. This guide will outline the benefits of Industry 4.0 technologies and how engineers can deploy IIoT solutions to achieve competitive designs.
What is Industry 4.0?
What is Industry 4.0? It is the Fourth Industrial Revolution and all of its game-changing technologies and concepts. The previous three industrial revolutions are broadly considered to be the advents of mechanisation and steam power, electricity and assembly lines, and electronics, computers, and automation.
The fourth one is the rise of industrial applications in our data-driven, highly interconnected world. It is characterised by industrial machines connecting to the internet and each other, allowing rapid execution and optimisation in quality control, supply chain management, maintenance, and automation. Industry 4.0 also deploys cloud computing, AI, machine learning, and robotics to reduce waste and increase energy efficiency to improve operating costs.
Businesses operating in Industry 4.0 have a better understanding of their operations and can more nimbly succeed in this fast-paced revolution.
Aspects of Industry 4.0
Industry 4.0 examples are readily familiar to many people: AI, 3D printing, interconnected devices, etc. This is a key factor of this ‘revolution’. Smartphones and other online devices are used throughout our lives, and that absolutely includes engineering and manufacturing.
IIoT
The Industrial Internet of Things (IIoT) refers to industrial devices that can transmit operational information over the Internet. The IIoT is one of the principal Industry 4.0 technologies since it connects industrial machinery to the rest of the company and the broader world. The IIoT allows engineers and businesses to:
- Remotely control operations
- Monitor equipment efficiencies
- Detect issues in their early stages — well before they become costly or disastrous failures
- Know with better certainty the status of their inventory and supply chain
- Understand the business costs of machinery assets
Using IIoT devices also requires engineers to provide systems for managing this data, including through IoT gateways and edge computing devices: data hubs installed close to IIoT devices, allowing collecting, processing, and securing multiple devices’ data before sending it to the cloud, reducing latency.
3D Printing
Additive manufacturing, such as 3D printing, has been revolutionary in its ability to produce products rapidly, minimise waste, and create shapes that would be excessively expensive or even impossible to produce with traditional manufacturing. This unlocks designs and approaches previously out of reach to engineers, making more problems solvable at reasonable costs.
Industries that are reaping great benefits of Industry 4.0 through 3D printing include:
- Healthcare: 3D printing is making medical implants, prosthetics, and even surgical instruments more readily and rapidly available at reasonable costs. There are even innovations in development for 3D printing replica tissue, bone, and organs
- Aerospace: Private space exploration has become possible partly through the use of 3D printing to get aerospace products to market much more quickly. Advances in metal 3D printing technologies are also making complex aluminium and titanium designs buildable at a fraction of their previously expected costs
- Automotive: Automobile manufacturing deploys 3D printing for rapid prototyping and design iterations, custom tools and jigs for assembly lines, more doable lower-volume speciality vehicle productions, and enhanced feature customisation
Simulation and Prediction
Computer-based simulations have long been in the engineering toolbelt, and Industry 4.0 technologies are taking these simulations to new levels, such as:
- Virtual and augmented reality allowing easy visualisation of how products will fit into and interact with their environments
- Condition monitoring and predictive maintenance, which uses instrumentation to identify developing problems in machinery and automatically call for addressing them through a computerised maintenance management system (CMMS)
- ‘Digital twin’ as-builts of buildings, enabling monitoring of how well they function compared to their design
Microprocessors continue to get smaller and more powerful, allowing industrial computing to perform staggeringly broad, complex tasks to help businesses identify ways to compete on new levels.
AI
As Industry 4.0 technologies collect and store reams of data, artificial intelligence can sort through it. AI and machine learning can be deployed industrially in the following ways:
- Performing predictive maintenance by monitoring machine vibrations and other conditions to determine when maintenance shutdowns are required
- Quickly visually inspecting products to both reduce manual inspections and detect costly defects more reliably
- Making human-machine interfaces (HMIs) more intuitive, adaptive, and accessible based on the individual user
- Interfacing with manufacturing robotics and improving their output quality and efficiency
- Optimising supply chain management by forecasting demand and managing inventory
Using AI in engineering enables many of the benefits of Industry 4.0, but it must be used carefully, ethically, and responsibly, as with all AI applications.
Engineering 4.0
Industry 4.0 was built by adaptable engineers rising to the design challenges of the modern world. Engineers continuing to innovate in this space will need to keep their skills sharp and stay abreast of how Industry 4.0 technologies apply to their practices.
Ongoing Training
As with all professional practices, and even life in general, continuous learning and development are essential for growth and improvement. This is especially true in Industry 4.0, which is characterised by its rapid rate of change and frequency of innovation. Engineers designing Industry 4.0 technologies will need to stay informed and knowledgeable about technological trends to ensure the products they deliver are relevant and useful.
Designing for Data
Any devices operating in Industry 4.0 and the IIoT need to transmit data. Engineers operating in these environments in turn need to design products around:
- Sending and receiving data
- Storing data (extremely large amounts of it), often on cloud computing servers
- Proper internet connection and security protocols
- Speed of data transmission
- Automatically adjusting operations based on conditions
To achieve these designs, RS offers sensors, multi-band antennas, and Bluetooth modules, as well as network cables for connecting all of them.
These data-enabling features are just the groundwork of Industry 4.0, though. The greatest Industry 4.0 challenges are what to do with all this information.
Making Sense of Data
Placing sensors everywhere and then filling up cloud computing drives with data points is one thing. Interpreting the data and acting on it to make your business win is a better thing. As Industry 4.0 technologies collect and share data, engineers will need to learn to interpret it and recognise things such as:
- Indicators of potential or imminent equipment failure
- Operating conditions that optimise efficiency
- Design flaws and how to resolve them before full production
- How interconnected Industry 4.0 devices affect and relate to each other’s operations
The use of AI in engineering can supercharge this data analysis and determine useful conclusions engineers would be otherwise unable to achieve.
Rapid Prototyping
Rapid prototyping is a well-established capability of engineering with CAD and CNC. Industry 4.0 technologies unlock new aspects of it, primarily with 3D printing. 3D printing allows realising design concepts in tangible form much faster than before. It also lets engineers skilled in 3D printing quickly produce prototypes within their teams, saving skilled machinists’ time and their equipment until designs are ready for full production. This speed of printing concepts means engineering teams can quickly propose and compare design ideas, perhaps arriving at innovations that wouldn’t otherwise be considered.
AI in engineering software is also improving prototyping by running more efficient simulations with more useful results, detecting flaws in models before they go to print, and optimising 3D printing performance as it happens.
These innovations to rapid prototyping can speed up a business’ time to market for new products, letting them stay ahead of the game.
Embracing Interconnectivity
All the data connections of IIoT-enabled machines allow more than just plotted charts and filled hard drives. They give engineers more abilities in their design tool belts for resolving challenges. With Industry 4.0 technologies at your disposal, always be open to creative ways to deploy them, such as:
- Conditions to newly monitor that could yield useful operating data
- Ways for machines to automatically communicate and adjust their operations
- Factory constraints and issues that could be resolved through reduced human inputs
- Using cloud computing and IIoT-linked ERP for teams to seamlessly work together across long distances
Of the many benefits of Industry 4.0, perhaps the greatest is the engineer’s newly unrestrained imagination!
Opportunities of Industry 4.0
As engineers rise to overcome Industry 4.0 challenges, they will also come to seize the business benefits of Industry 4.0:
- Abundant data to use in design calculations and decisions
- Easy synchronisation with other teams’ work
- Reduced time for design iterations
- Quicker addressing of customer requests and complaints
- Nonstop professional development
- Increased efficiency
- Enhanced productivity
- Cost reduction
- Quality improvement
- Flexibility and customisation
- Innovation and product development
- Supply chain optimisation
- Safety and compliance
- Sustainability
Along with its various lines of Industry 4.0 technologies, RS can bring the benefits of Industry 4.0 to you through its maintenance solutions and the RS Industria condition-based monitoring platform.