- Published 25 Mar 2024
- Last Modified 25 Mar 2024
- 7 min
Fixed Wiring Electrical System Reliability
Electrical system reliability is crucial to manufacturers. Our guide explains some of the common challenges to electrical system reliability and looks at how different maintenance technologies and techniques can help.
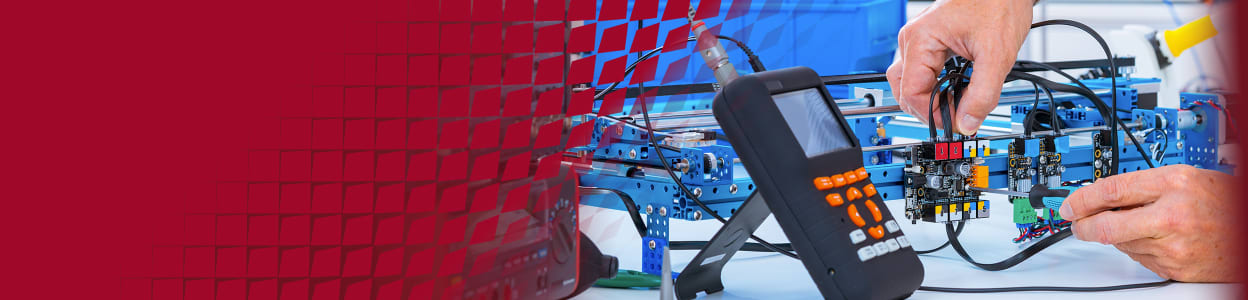
Reviewed by Karl Ralph, Technical Support Engineer (March 2024)
A reliable power supply is essential to daily life. A loss of power is not only disruptive for the public, it can damage businesses and threaten safety. For manufacturers, loss of the electrical system can halt production and cause financial losses. So for manufacturing plants, electrical reliability is crucial.
A well-maintained electrical system ensures a continuous and reliable electricity supply. Maintaining power systems correctly can also save money by improving energy efficiency. This guide examines the importance of electrical reliability and looks at some maintenance strategies to help keep the lights on.
Why is Electrical System Reliability Important?
Modern society completely relies on electricity. That means if electrical systems are unreliable, it’s a problem. For energy-intensive industries such as manufacturing, unplanned shutdowns of production can cost millions. That means the security of supply is critical.
Maintenance engineers can take steps to ensure electrical power system reliability. For example, electrical predictive maintenance and other techniques can help maintain the security of supply.
Manufacturing Electrical Systems
The picture is more complicated for manufacturing companies when it comes to electrical reliability than domestic users or most other types of businesses. Manufacturing electrical systems help to control and power a wide range of machines and equipment. Not only are these systems responsible for providing machinery with energy, but they also play an important role in equipment control and maintaining safety. Examples of control systems that rely on electricity include human-machine interfaces, industrial automation and control systems, and programmable logic controllers.
A manufacturing facility may have a bespoke electrical system set up for its needs, but all facilities will require extensive lighting. This means power quality must be good enough to light the factory correctly, which is vital for health and safety. Factories may also contain some office space.
Some factory processes may require a backup generator or uninterruptible power supply just in case there is a power outage. Specialist electrical engineers can help develop the electrical systems for production lines, conveyors, machinery, and industrial lighting.
Electrical System Challenges
Let’s look at some electrical system challenges. If electrical system reliability fails, it can be due to a number of factors:
Power Failure
A power failure is never welcome in any business, but the extent to which a company is affected varies widely by industry. For manufacturers, the loss of power can be anything from mildly disruptive to potentially life-threatening. A loss of power has the potential to shut down a production line. If machinery isn’t operating when it should be, that can entail big financial losses and have a wider impact on the supply chain. Loss of power can also have an impact on safety. For example, if lighting is lost then it may not be safe to operate machinery.
Ageing Electrical Infrastructure
Electrical system reliability can also be affected by ageing electrical infrastructure. Transformers and power networks such as wiring systems deteriorate over time if they are not maintained correctly or components are not replaced at the end of life. Engineers should consider their entire legacy of electrical infrastructure and ask if it remains fit for purpose. When there is increased demand on the system, does it struggle? Ageing infrastructure should be maintained and upgraded as necessary to avoid problems. Parts can become obsolete, which is an important factor driving upgrading, and plastics and insulation can also deteriorate over time.
Lack of Maintenance
Lack of maintenance of electrical systems can result in fire or present other hazards to workers, not to mention the economic costs of loss of production if a line shuts down. Since much of a manufacturing facility’s electrical infrastructure is hidden in walls, engineers should pay particular attention to lights that are dimmer than normal, or circuit breakers and fuses that trip repeatedly. A burning smell may indicate a problem with insulation. Engineers should also beware of equipment that is abnormally hot to the touch. All of these warning signs could indicate that urgent maintenance of the electrical system is needed. How often should fixed wiring be inspected? It's essential to get an electrical installation condition report or fixed wire test, at a minimum, every five years.
Electrical Standards
Risks to electrical system reliability can be mitigated by adhering to electrical safety standards. You should always adhere to electrical standards and work should be carried out by a suitable, qualified, competent person. British standards and codes of practice for electrical infrastructure cover everything from low-voltage switchgear to emergency lighting to fire detection and alarm systems. Current wiring regulations are encompassed by British Standard BS 7671, which came into effect in 2019. BS 7671 is the 18th edition, and the current standard used in the UK for electrical installations. BS 7671 sets the bar for electrical wiring installations at industrial facilities in the UK.
Maintenance Approaches
What is maintenance in electrical engineering? There are a number of electrical maintenance tools and techniques engineers can use to ensure electrical system reliability and conduct electrical system maintenance. One of the most prevalent is power quality monitoring. Power quality problems may cause issues such as circuit board or equipment failure. Power quality monitoring typically obtains data about voltage, electrical current, and ground quality to understand any issues impacting machinery. Engineers will use a power quality metre to measure current and voltage. Power quality problems include events such as power surges, which cause voltage to spike outside its healthy range.
Reliability testing of your electrical system by specialists can also help reveal any risks or problems that might affect power reliability or quality. For example, engineers can create a model of the electrical system for system reliability testing. They will assess any weaknesses the electrical system has, the level of redundancy built into the system, and the power system’s potential failure points.
Preventative and Predictive Maintenance
Both preventative and predictive maintenance approaches can be used to maintain electrical systems. What is electrical preventative maintenance? Preventative maintenance uses a strict maintenance schedule to ensure electrical systems are maintained on a frequent basis to help prevent problems from occurring. This maintenance regime is usually based on recommendations from the installer of the system. Electrical predictive maintenance uses technology such as thermographic testing and ultrasonic testing to diagnose when and where maintenance needs to be conducted before a system failure occurs.
Reliability-Centred Maintenance
What is reliability-centred maintenance? As the name suggests, this system’s focus is on reliable performance. Reliability-centred maintenance (RCM) is a system that can be used for electrical infrastructure, with a focus on the availability of assets. It is a methodology that helps to uncover the root causes of failure and helps engineers to take action. The aim is to prevent the sudden breakdowns manufacturers dread.
Whatever approach to maintenance you decide on, it’s important that electrical systems are tested, maintained, and upgraded as necessary. Not doing so could result in costly production problems that would be otherwise avoided.
It might not be immediately apparent where the problems, if any, lie. But a comprehensive approach to maintenance will certainly help reveal potential sources of trouble.
These maintenance concepts also factor into an even more detailed system: precision maintenance, which you can learn about with this guide.