- Published 25 Sept 2023
- Last Modified 29 Feb 2024
- 7 min
What is Planned Preventative Maintenance?
The best defence against machinery breakdown is not to let it fail in the first place, and that’s where the planned preventative maintenance inspection comes in. Regularly scheduling maintenance activity guards against unplanned failures and consequent lost productivity. Our guide explains exactly what planned preventative maintenance services are, provides some examples, and explains how to implement a planned preventative maintenance programme.
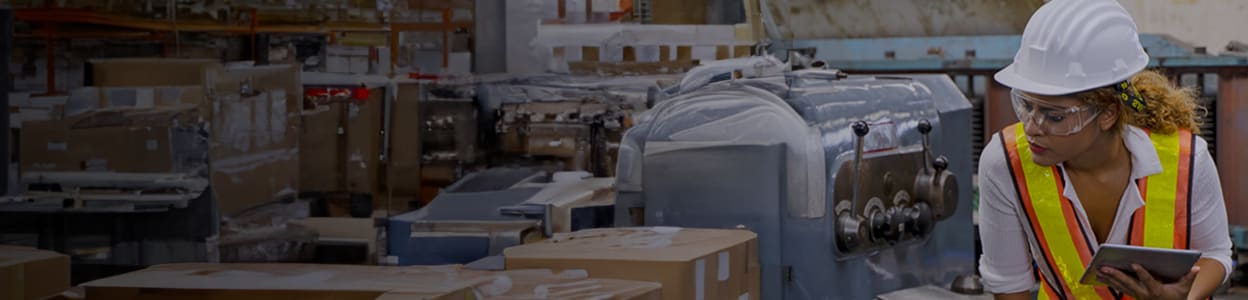
In a reactive maintenance regime, machinery is fixed when it breaks (remember the old adage, ‘If it ain’t broke, don’t fix it’?). Planned preventative maintenance (AKA PPM meaning maintenance) aims to stop the machine breaking down in the first place: ‘It’s not broken now, and we’re doing our best to keep it that way.’
The key to planned preventative maintenance is timely intervention – or more specifically, regular scheduling. Machinery is maintained according to a preventative maintenance plan with the aim of minimising risks to equipment. Engineers perform set tasks at regular intervals to keep machinery running; unplanned maintenance because of outright machine failure should be reduced (or even eliminated altogether).
Benefits of planned preventative maintenance include increased efficiency and productivity, reduced costs, improved health and safety, and fewer production line shutdowns. A good planned preventative maintenance schedule will also extend the lifespan of your machinery and capital equipment.
Planned Preventative Maintenance Examples
Types of preventative maintenance encompass many different areas. Examples of planned preventative maintenance include:
- Lubrication of rotating parts.
Lubrication reduces friction between moving parts in a machine, dissipates heat, and prevents wear. Planned preventative maintenance introduces a methodical approach to lubrication of machinery components, taking into account correct lubrication points and volume and type of lubricant, along with ensuring lubricant is applied in the right way. Planned preventative maintenance will also keep records on the lubricants used. Subsequent analysis of used lubricant (‘oil analysis’) can also help determine the health of machinery.
- Cleaning equipment regularly.
Dirt and dust are the enemy of factory machinery. They have the potential to damage it, or at least slow it down. The build-up of dirt may cause friction between components or contaminate lubricants, reducing their effectiveness and leading to increased wear and tear on mechanical systems. Dirt and grime may build up and get into products, potentially impacting customers. Regular cleaning, on the other hand, can prolong machinery life and ensure goods go to market spotless.
- Maintaining facilities.
Planned preventative maintenance can also be used to maintain your factory facilities and keep them safe for employees. This might include maintaining lighting, heating, ventilation and air conditioning, and ensuring that electrical systems are functioning correctly. This can be beneficial to the environment thanks to reduced energy consumption on heating, cooling, and lighting.
- Maintenance of automation.
Many factories today contain large amounts of automation such as robots, conveyors, CNC machines, packaging systems, and so on. Regularly inspecting these systems for wear and tear, replacing damaged parts, and lubricating moving components is an important part of any preventative maintenance programme.
Predictive Versus Preventative Maintenance
Predictive maintenance and a preventative maintenance programme differ in that predictive maintenance is continuous monitoring of machinery in order to detect anomalies that may indicate a fault, while preventative maintenance relies on regular, scheduled maintenance activity. In practice, it’s not simply a case of just using one or the other: planned and predictive approaches are often combined to create the best possible proactive maintenance regime. Assets that require regular servicing can be serviced according to a schedule; those assets that benefit from condition monitoring can be assessed using vibration monitoring or another of the many predictive maintenance technologies.
Benefits of Planned Preventative Maintenance
There are numerous benefits to a planned preventative maintenance programme. Here are just a few:
Maximising Uptime
Uptime is a measure of the availability of a machine or machinery. Planned preventative maintenance should enable machines to be available for as much time as possible (the best way of increasing availability is minimising downtime). That doesn’t mean downtime is eliminated: some downtime is necessary to carry out maintenance work. But this activity should be planned and scheduled for convenient times that don’t impact the business. Unplanned downtime due to machine failure, on the other hand, is a headache for the maintenance engineer.
Enhancing Productivity
Productivity is high when assets are available and working as they are intended to. Introducing a planned preventative maintenance programme should make a manufacturing facility more productive because more machinery is available to do more work, more of the time. By contrast, equipment downtime is a drain on productivity. RS helps manufacturers boost their productivity – find out more here.
Improving Resilience
Preventative maintenance makes a manufacturing business more resilient because it:
- Prevents unplanned interruptions
- Extends the lifespan of equipment (and thus has the potential to reduce capital expenditure)
- Enhances productivity
- Minimises hazards to employees (the more machinery breakdowns there are, the greater the impact on health and safety)
Manufacturers that employ planned preventative maintenance are thus likely to enjoy greater levels of resilience than those who wait for equipment to fail before fixing it.
How to Create an Effective Preventative Maintenance Plan
An effective preventative maintenance plan should start by considering the assets that are critical to the business and how to maintain them on a comprehensive, regular schedule. In short, it’s important to know your equipment – which machinery is critical to the business?
It’s also important to consider the must-have tasks at the start of planning, and to prioritise actions accordingly. Naturally, anything that has an impact on employee safety has to be a matter of priority, as does anything that might result in failure of a critical asset if not addressed. Tasks that are not essential to safety, or where delaying will not impact asset performance in the short-term, can be delayed until the fundamentals of your preventative maintenance plan are in place.
Maintenance tasks can be performed on a range of frequencies, from daily to every few months or years. Devising a preventative maintenance schedule, an important part of the overall plan, means deciding on how often to carry out certain tasks. Some elements of this will be dictated to you by regulations and safety legislation. Others will be decisions based on the working practices and experience of the engineering team. The preventative maintenance plan should be put down in writing so everyone can see what it is.
Key performance indicators (commonly used metrics include mean time between failure and mean time for repair) should also be chosen. They’ll give you a good idea as to the effectiveness of your programme. If maintenance training is required for employees, carry it out, and make sure they have the right tools on hand for the job.
Having guides and lists can help ensure employees get to grips with the new maintenance plan. Preventative maintenance checklists are a great way of ensuring technicians carry out tasks correctly. There should be a set series of steps the technician needs to take in order to complete a preventative maintenance work order. Those steps should be carried out the same way every time, no matter who does them on the team. There should also be a record of the maintenance activity.
This can be stored on the asset register of a preventative maintenance software database (known as a computerised maintenance management system, or CMMS). The CMMS can also be used to schedule and prioritise maintenance work orders, allocate resources, track activity, and provide a hub for documentation, manuals and safety information.
Want industrial maintenance solutions that will help you implement an effective maintenance plan? RS has got you covered. Find out more here.