- Published 12 Mar 2024
- Last Modified 12 Mar 2024
- 8 min
IoT Connectivity in Manufacturing
Your personal devices connect your life to the world in every which way, but is your manufacturing business similarly connected? It can be, through IoT connectivity, and this can help you succeed through reduced losses, more efficiently delivered products, and better awareness of your operations.
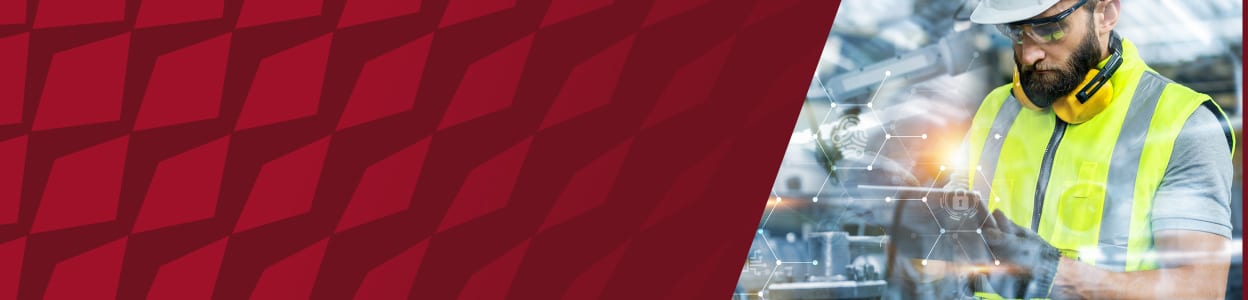
Reviewed by Stephen Bettles, Technical Support Engineer (February 2024)
We live in a connected world with a constant flow of data. That includes manufacturing industries, which are increasingly interconnecting their operations to succeed. This industrial connectivity is part of the Internet of Things (IoT) and Industry 4.0. IoT in manufacturing has great potential for improvements in inventory, quality control, maintenance, energy efficiency, supply chains, and more.
What is IoT Connectivity?
IoT connectivity refers to a device’s ability to connect to the internet for sending or receiving useful operational information. This can refer to familiar things like mobile phones and smart TVs, but also to industrial technology like assembly lines and digital warehouse management. An industrial subset of IoT is the Industrial Internet of Things (IIoT), which plays a large role in Industry 4.0 by giving companies better awareness of their machines’ operations, health, performance, and business costs.
Some key factors and concepts to consider within IoT connectivity are:
- Speed: We all demand instantaneous results from the internet, and industrial connectivity needs to be equally rapid. IIoT devices’ data transfer speed is measured in bits or gigabits per second, and these ratings affect their cost and power consumption. Consider the data packet sizes you’ll need to send when selecting equipment for industrial IoT solutions
- Range: The distance devices can transmit data over will determine their suitability for your operations and how you will lay out your connected equipment
- Costs: IIoT technologies vary in price and power consumption, so be aware of the financial commitments they represent
- Network type: IoT communication happens over various networks, such as LAN (Bluetooth and Wi-Fi), LPWAN, cellular (LTE, 5G), and mesh networks. Study the connection capabilities of IIoT devices to be sure they’ll connect with your broader system
- Machine-to-machine connectivity (M2M): M2M connectivity refers to machines connecting and automatically selecting and executing operations without human input
What are the Benefits of IoT in Manufacturing?
Introducing IIoT applications to manufacturing operations can unlock many benefits:
- Supply management: Take control of inventory by applying radio frequency identification (RFID) tags to material supplies and tracking them in digital inventory systems. Have the system automatically order materials when stocks drop below established levels, thus preventing holding up jobs due to a lack of supplies
- Tracking equipment: IoT connectivity lets you know where your vehicles are deployed and whether their operational health calls for maintenance. Similarly, RFID tags and tool management software can track who’s using individual tools and where, preventing confusion and replacement costs due to things going missing
- Quality control: Automate the measurement of produced parts and the recording of this data. This reduces the need for manual inspection and allows more immediate action on addressing defective output
- Energy efficiency: Track the real-time performance of your machines in relation to their consumed energy. This identifies areas of wasted resources and problems that need addressing
- Predictive maintenance: Monitor machine health using IIoT-connected sensors. IIoT platforms can analyse abnormal equipment behaviour (especially vibrations), model when that could lead to major failures, and schedule proactive maintenance accordingly. This reduces breakdowns and gives you control of maintenance and its costs
How are Different Industries Using Connectivity Technology?
IoT in manufacturing extends to all of its branches, including construction, mining, supply chain, and automotive.
IoT in Construction
Construction features a wide range of industrial technology, much of which is being improved with IIoT solutions.
- Fuel: Construction machines constantly burn a lot of fuel. Using fuel level sensors with IoT connectivity you can efficiently manage refuelling, monitor fuel expenses, and collect data for scheduling maintenance based on energy efficiency
- Concrete: Monitor fresh concrete’s strengthening progress using IIoT-connected sensors embedded in it as it cures. This means waiting for only as long as needed so you can better plan operations
- Digital twins: As a building is constructed, IoT connectivity lets engineers compare the building’s progress to its ‘digital twin’ model. This helps detect and diagnose issues in their early stages and produces a digital as-built of the facility
Users increasingly demand IoT connectivity built into their homes and workplaces, so this affects the infrastructure the construction industry needs to provide.
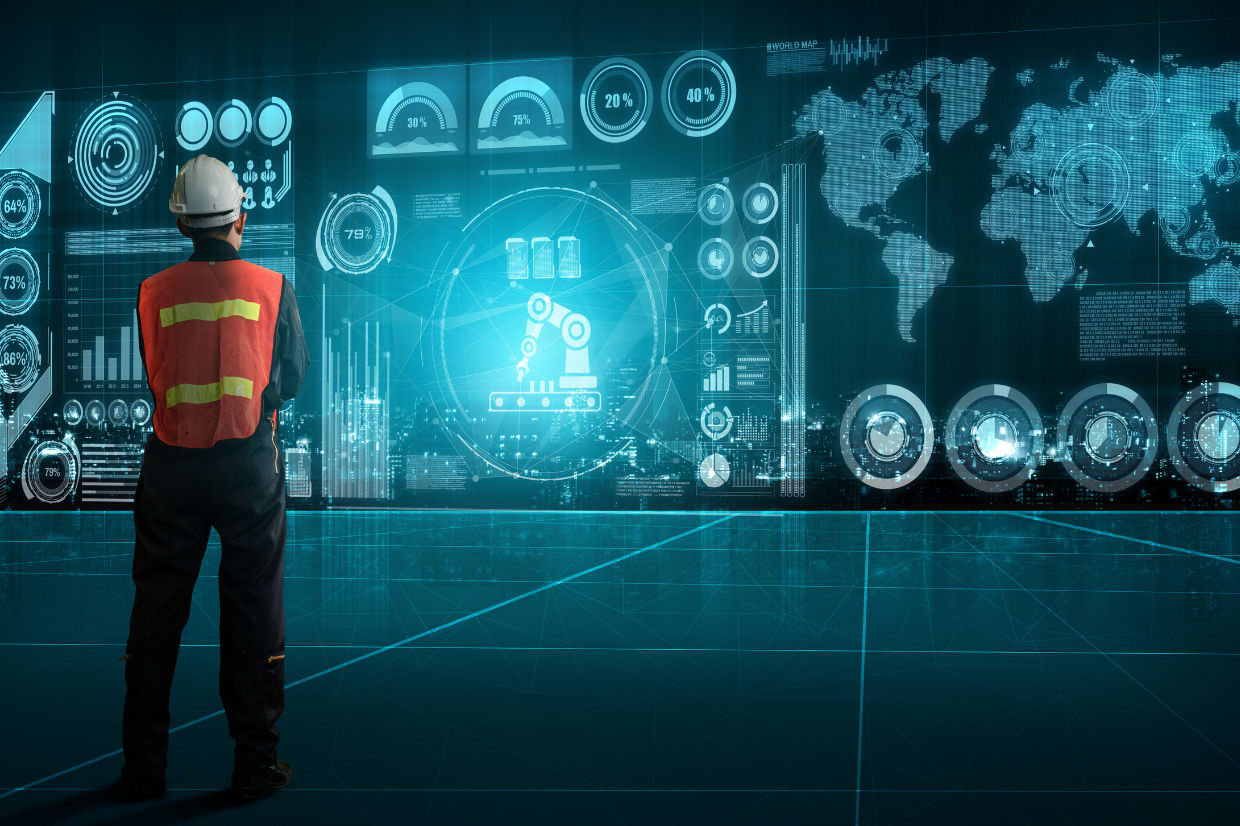
IoT in Mining
There are IIoT applications for working around the delicate, large-scale nature of the mining industry.
- Shaft stability: Avoid shaft collapses by installing IIoT sensors in shafts to monitor their stability. If accidents do happen in the mine, IIoT solutions can help you quickly determine where workers were deployed and form rescue plans
- Remote control: Use IoT connectivity to remotely operate mining equipment, keeping personnel safely separated from hazardous areas. IoT connectivity even allows this remote control from anywhere in the world
- Reduce waste: Better manage consumable resources like equipment fuel and building materials using IIoT sensors and digital inventory management
- Environment: By monitoring the conditions of your site’s ground, water, and air, you can get a real-time picture of your operation’s environmental effects. This lets you adjust your mining work before developing issues become disasters
IoT in the Supply Chain
As the quintessential example of a connected industry, supply chain management has massive potential to benefit from IoT connectivity.
- Know inventories: Warehousing IIoT platforms can broadcast true, live inventory levels. Knowing with certainty what material you have and its location is a great foundation for managing where to send these items
- Track goods: With RFID tags attached to products and GPS tracking, you can precisely pinpoint the location of goods in transit. This avoids the costs of losses and the waste and delays of shipments going to the wrong place
- Predict arrival times: By knowing when materials depart and tracking their journey, you can confidently project when they’ll reach their destination. You can thus synchronise the operations that depend on these shipments, subsequent dependent operations, and so forth
- Customer satisfaction: Using this same IoT connectivity for tracking shipments, customers can have a better idea of when they’ll receive orders, which avoids the dissatisfaction of delayed material
IoT in Automotive Industry
Automotive industrial connectivity is already widespread, and industrial IoT solutions can enhance this even further.
- Tracking builds: The automotive industry has realised many improvements through industrial IoT solutions. Assembly lines need to provide a variety of vehicles with specific work, and this requires clear tracking. Handwritten tracking has significant error potential and barcodes can easily wear away, but RFID tags travelling with the vehicle omit all this. They provide instantaneous, contactless information transmission, and can carry reams of detailed information on the vehicle besides just its identifier
- Instructions for robots: For automated processes with delicate variations based on vehicles, such as welding and painting, RFID tags ensure proper inputs for the robotic devices involved. These tags can carry each vehicle’s detailed welding and painting instructions, which can be quickly read and input to the automated machines through M2M connectivity once the vehicles reach them. This omits the costly errors of doing the wrong work
- Connected cars: As with the construction industry, the automotive industry increasingly needs to include IoT connectivity in its finished products to satisfy customer wishes. This includes features such as:
- Self-driving capabilities
- GPS and mobile phone connectivity
- Driver monitoring for insurance purposes
- Predictive maintenance
These features in turn need to be manufactured and included in the vehicles’ assembly processes.
What IIoT Technology Can Manufacturers Leverage?
Many products are used to achieve IoT solutions in manufacturing:
Using these technologies, RS can help you implement IoT in manufacturing and enjoy the business benefits of industrial connectivity.