- Published 26 Feb 2024
- Last Modified 26 Feb 2024
- 7 min
The Industrial IoT and Smart Factories
The Industrial Internet of Things is seeing sensors on production machinery networked to computer systems to gather huge volumes of data, enabling predictive maintenance and other aspects of the smart factory like digital twins and augmented reality. Learn more in our guide.
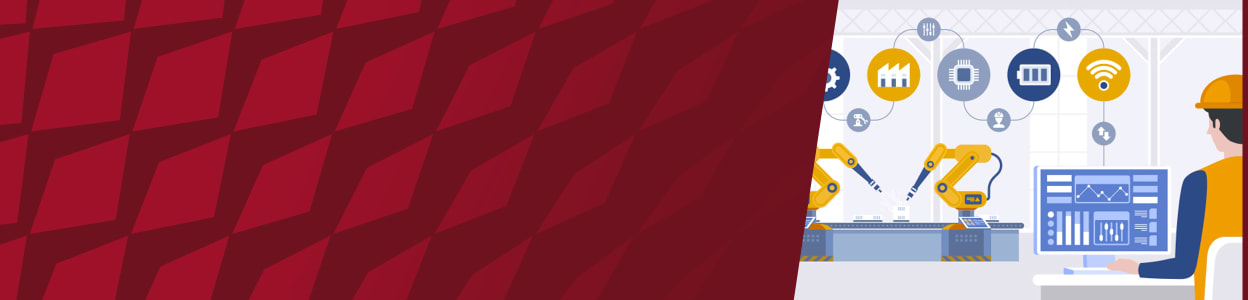
Reviewed by Stephen Bettles, Technical Support Engineer (February 2024)
The Fourth Industrial Revolution is seeing the creation of smart factories with phenomenal new data-driven capabilities. None of that would be possible without the development of the Industrial Internet of Things.
Smart Factories and Industry 4.0
The IoT and smart factory concepts are regarded as part of the Fourth Industrial Revolution (Industry 4.0), in which cyber and physical systems converge thanks to enhanced connectivity to transform manufacturing. The IIoT combines several technologies and concepts, including not just sensors and instrumentation but advanced networks, cyber-security, Big Data and data analytics, cloud and Edge computing, artificial intelligence and machine learning, and robotics and other forms of automation.
Smart Factories
Just as digital transformation changes everyday life, it’s also transforming manufacturing. But what is a smart factory? A smart factory is a heavily digital factory - a production facility in which physical systems are connected to computers to collect and share data. This includes not just production machinery but also inventory, spare parts, and finished goods. The data that is generated by connecting machinery and parts and components to the internet can be used to improve processes and make manufacturing more efficient.
Smart factory benefits also include improvements to quality control, product development, and logistics. It’s also possible to predict machinery failure before it happens as part of a predictive maintenance regime that collects data from production machinery.
Industry 4.0
If the First Industrial Revolution in the late 18th century saw steam, water, and mechanical power come to the fore, the Second Industrial Revolution had been powered by electricity, and the Third by computers, the fourth would see the convergence of cyber and physical systems.
Industry 4.0 marks a distinct phase of its own because of the speed at which it is changing the world and the possibilities of connecting billions of people with unprecedented levels of computing power. Key Fourth Industrial Revolution technologies include AI, self-driving vehicles, 3D printing, nanotechnology, biotechnology, quantum computing – and the Internet of Things.
The IIoT and Maintenance
One of the key applications of the power of the IIoT digital factory is maintenance. By collecting large volumes of data from machinery, it’s now possible to predict when it will break down. This enables engineers to intervene, whereas in the past the machinery may just have failed, causing lost production and unscheduled downtime. Industry 4.0 and maintenance works by collecting data and looking for anomalies in machinery performance that may be early warning signs of problems developing.
It’s a more sophisticated approach to maintenance than ‘fixing on fail’, or even a good preventative (scheduled) maintenance regime. And it wouldn’t be possible without the Internet of Things.
The IIoT and Robotics
Like other production equipment, industrial robotics can be integrated into the IIoT. Monitoring the performance of robots using sensors or other instrumentation enables engineers to make improvements to manufacturing processes and carry out remote diagnostics. Online dashboards now provide insight into the performance of robots. This information can be used to make investment decisions – whether machinery needs to be replaced or upgraded, for example – or to make tweaks to performance.
Thanks to the power of cloud computing, it’s also now possible to simultaneously manage and track the performance of several industrial robotics systems. This helps to integrate different types of automation more effectively to maximise efficiency.
Advancements in robotics as part of Industry 4.0 also mean the increasing use of collaborative robots (cobots) that are sophisticated and safe enough to work alongside personnel.
AR and VR
Virtual reality (VR) and augmented reality (AR) are most popular in the gaming world, but they are also being used with the IIoT. The IIoT provides huge volumes of data about machinery. Combine all that data, and you can construct a virtual three-dimensional model of an entire factory or process - a model known as a digital twin.
This 3D visualisation of infrastructure opens up the opportunity for engineers working remotely to run operations. Experts can explain how to carry out repairs to technicians in the field without having to be on site. VR and AR can also help train workers on how to maintain a plant without having to disassemble it or assess how to make repairs without having to disrupt production.
Inventory, Logistics and the IIoT
The Internet of Things is revolutionising inventory management and logistics. It’s now possible to track the movement of parts, components, and finished goods in real-time throughout the supply chain. Manufacturers may, for example, add an RFID tag to track the location, size, manufacturer, serial number, and production line for a part. This information is transmitted continuously and stored in the cloud. Gone are the days of time-consuming manual checks on inventory to know what’s out there and entering it on a spreadsheet.
Using the IIoT to track inventory promises to make manufacturing more efficient because there is less need to hold stock that isn’t being used. Production is also streamlined.
Benefits of the Industrial Internet of Things
As with other forms of automation, one of the primary benefits of using the power of the IIoT is efficiency. Industrial robotics have been used for decades to make production more efficient, but the IIoT enhances this by making use of data to improve performance. Broadly, it is this data across the manufacturing operation that enables manufacturers to make better decisions. Some of the other principal benefits of IIoT uses include:
- Speeding up time to market: Manufacturing can be quicker and more responsive to the marketplace thanks to the IIoT. This also includes being able to identify problems in the supply chain early on. Production cycle times can also be improved, which helps manufacturers get products to market more quickly
- Predictive maintenance: Downtime caused by machinery malfunctioning is one of the biggest bugbears for manufacturers. By installing networks of condition monitoring sensors – vibration sensors on machine tools, for example – it is possible to collect data that indicates anomalies in performance long before failure occurs. This boosts machinery uptime, cuts costs, and enhances productivity
- Enabling digital representations of production processes or entire factories: Digital twins and the immersive environments of VR can assist with everything from designing new products to running plants remotely and training technicians to carry out maintenance. These types of technology also allow changes to be simulated without taking the risk of disrupting a real manufacturing line. None of this would be possible without gathering reams of data about production thanks to the IIoT
The Evolution of the IIoT
The IIoT will evolve thanks to several newer technologies. One of these is Edge computing, which processes data on a device rather than transmitting it to the cloud. This has benefits in terms of reliability, privacy, and security. Another notable industry trend is the use of AI and machine learning. These hold huge promise for more and more sophisticated and timely analysis of data generated by the IIoT. Using AI will help to improve efficiency and allow manufacturers to make better decisions.
Factories of the Future
The future of automation will combine data analytics with connected physical systems to manufacture products in increasingly innovative and flexible ways. Many of the aspects of these future factories, such as intelligent logistics, advanced robotics, and 3D printing, are here today. In the future, we may see autonomous mobile robots carrying out complex activities that require trained personnel right now. It’s also expected that additive manufacturing will be used to create finished parts rather than prototypes in demanding applications such as aerospace and defence. Augmented reality could also become a common sight on the shop floor, used by production workers to carry out operations perfectly.
The Fourth Industrial Revolution may be old hat in years to come. Many commentators are already talking about Industry 5.0, where people work alongside AI-powered robots to boost productivity and improve manufacturing. The IIoT as it stands is just the beginning!
Learn more about automation and maintenance in our guide.