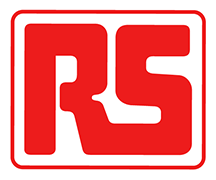
A Practical Guide to CHEMICAL SAFETY
INTRODUCTION TO CHEMICAL SAFETY
Basic handling guidelines
Most jobs today involve some level of chemical exposure, whether you’re working with hazardous pesticides on a farm, dyeing someone’s hair, mixing compounds in a lab, or cleaning a food preparation area.
This guide provides a broad overview of approaches to various issues concerning chemical safety at work. The key goal of all workplace chemical awareness information is to reduce exposure to hazardous chemicals and help prevent illnesses, injuries and accidents on the job.
As a worker in an environment where chemical use is an issue, there are some basic health and safety guidelines that should almost always be followed, regardless of the specific task at hand:
- Read the relevant Safety Data Sheet (SDS) before working with a chemical product
- Follow all workplace hazard control plans for hazardous or extremely hazardous chemicals
- Pay close attention to control measures for chemicals that are known to be particularly high hazard or chemical carcinogens
- Never underestimate risk – assume that any mixture will be more hazardous than its most toxic component, and that all substances of unknown toxicity are highly toxic
- Never hold loose items in your mouth, pipette by mouth, or allow lids or soiled protective wear to come into direct contact with skin
- Never smell chemicals to identify them
- Do not eat, drink, store food, smoke, or apply cosmetics in areas where chemicals are in use
- Wash your hands frequently and immediately after any chemical use
- Keep loose hair tied back and avoid baggy clothing
Toxicity and DTLs
The perceived threat to safety – both of employees and the public – involved in workplace chemical use focuses primarily on issues around their potential toxicity.
For the purposes of health and safety legislation and enforcement, a hazardous chemical’s toxicity rating is often defined in terms of its Dangerous Toxic Load (DTL) value.
A DTL value expresses the airborne concentration level vs. required exposure time, after which a given chemical causes the Specified Level of Toxicity (SLOT) or Significant Likelihood of Death (SLOD) in the exposed population.
SLOD is defined as a 50% mortality rate among an exposed population. The HSE has defined the SLOT as any scenario causing:- Severe distress to almost everyone exposed
- A substantial fraction of the exposed population to need medical attention
- Some incidents of severe injury requiring prolonged treatment
- The potential for highly susceptible people to be killed
- There is likely to be considerable variability in the responses of different individuals affected by a major accident
- There may be pockets of high and low concentrations of a toxic substance in any cloud chemical release, and thus not everyone will suffer the exact same degree of exposure
- The available toxicity data is not usually adequate for predicting precise dose-response effects
- They should be straightforward for non-scientists to understand in terms of overall health impact
AWARENESS OF RISKS AT WORK
Chemical exposure at work can occur in many different scenarios, both direct and indirect. There will often be very different risks – and levels of risk – for different employees associated with various processes involving chemicals.
These might include:- Manufacture of chemicals
- Transport of chemicals
- Mixing of chemicals
- Agitation of chemicals
- Different uses of chemicals in various work tasks
- Disposal of chemicals
Classification, Labelling and Packaging (CLP)
Classification, labelling and packaging are often key to understanding the severity and type of risk in different applications, processes or environments. As a baseline requirement for all workplaces conducting responsible chemical handling, general knowledge among management and workers should include- Which areas of chemical legislation apply to the business practice and premises
- An up-to-date inventory of chemicals used or stored on site
- Classification of the substances and mixtures being handled, and how these affect other legislative obligations
- Comprehensive risk assessment processes that ensure all reasonable steps are taken to protect staff and the environment, including a focus on securing reliable classification and labelling protocols
- Regular monitoring of changes in classification, and evaluation of the impact of any changes on compliance status
Classification
Chemicals are classified according to their hazardous properties. These classifications enable people who work with certain substances to quickly identify risks, typically in terms of the potential health impacts associated with exposure or mishandling.
Common classification types will identify whether exposure to a given substance is directly associated with specific conditions, acute health effects, long-term illnesses, environmental damage, or volatile reactions.
Occasionally, workers might encounter different classifications for the same product or chemical from different suppliers. There are a variety of possible explanations for this, which should be investigated with suppliers. These include:- The possible presence of different hazardous impurities, additives or ingredients
- Differences in certain properties such as the physical form, the pH level, or the flash point of the substance or mixture
- Different interpretations among different suppliers as a result of their own testing processes
Labelling
Hazardous substances and chemicals must carry appropriate warning labels on their packaging. This should provide product and supplier details, outline the potential hazard, and make note of any special precautions that need be taken.
Employees handling hazardous substances should always be trained to check that the information on the label is consistent with the information in the product’s Safety Data Sheet (SDS).
SDSs
All workers handling hazardous chemicals should ensure that the SDS is up to date and reflects any relevant new information that has emerged about a substance, or if the product has become subject to new authorisations or restrictions.
If a supplier has not sent a revised SDS for a few years, it’s always worth contacting them to check that the current version is still up to date
For all SDSs, handlers should check that:- The quality of the information provided is good, readable and makes sense
- The label or SDS is in the national language of the country receiving the substance
- The SDS is complete, with all 16 sections and the relevant subsections completed as appropriate
- The SDS contains all relevant information necessary for a full usage risk assessment to be conducted at the receiving workplace
- Exposure scenarios are provided with the SDS where appropriate
- The information in the SDS is consistent with the information provided in exposure scenarios
- The information provided is consistent with that given by other suppliers for the same product
Packaging
The packaging of hazardous chemicals must keep workers and the environment safe from unintended contact. Suppliers should always be contacted in any cases where this requirement is not appropriately met.
Specific packaging requirements for hazardous chemicals are detailed in the new (since 2015) CLP Regulation guidelines – they include:- Packaging being designed and manufactured to prevent the accidental escape of contents
- Packaging not being susceptible to damage from its own contents, and able stand up to the typical rigors of transport and handling
- Packaging with replaceable fastenings being constructed to allow for repeated unfastening and resealing without risk of the contents escaping
Since the transition to the new CLP guidelines, employers must ensure that all staff handling chemicals recognise and understand the new CLP labels, including safety symbols, hazard descriptions and precautionary statements.
Workplaces using chemical suppliers since before June 2015 should check whether the classification of chemicals sent, received and handled has since changed. It may be necessary to amend or update risk management strategies and compliance obligations as a result.
See our links and resources section at the end of this guide for more information on CLP.
Safe disposal of chemical waste
Risk of chemical exposure, either to workers or to the environment, does not always end when handling ends.
There are numerous basic principles that should always be observed when disposing of chemical waste or leftovers:
- Know the differences in procedures and requirements for chemical waste classified as hazardous and extremely hazardous, and be aware of the different compliance obligations
- Designate a hazardous waste disposal area – this should be clearly and prominently labelled, located close to the source of the waste, under the direct and exclusive control of workers in the immediate area, and far removed from other non-chemical activities
- Choose waste containers that are chemically compatible with the material being placed in them – as a basic rule of thumb, do not store acids or bases in metal, hydrofluoric acid in glass, or solvents in polyethylene containers
- Use only waste containers with leak-proof, screw-fit caps
- Wipe down and clearly label waste containers awaiting collection or removal
- Choose appropriately sized containers for the volume of contents being disposed of – do not underfill, but always leave 10% room for potential expansion
- Store hazardous waste containers inside a secondary container, to minimize leaking and the potential for incompatible mixes
- Segregate all incompatible chemical waste (see links and resources for a guide)
- Do not mix solid and liquid waste
- Do not combine organic solvents with toxic metal waste
- Be aware of special packaging requirements for discarded sharps (pipettes, tips, broken glass) alongside chemical waste
- Be aware of procedures for unknown or unidentified chemical waste – this should always be considered hazardous waste, and must be labelled appropriately and handled with caution
MANAGEMENT OF CHEMICAL RISKS AT WORK
Five steps to lowering risk
There are five core steps in achieving the best approach to reducing chemical hazards for employees in the workplace, listed below in order of preference and efficacy:
Step one: Elimination of exposure
This is the first and most desirable step that should be taken wherever possible. If a potentially harmful process, chemical interaction or substance isn’t absolutely essential to achieving the end result, it should be removed from the workflow sequence.
Step two: Substituting hazardous chemicals or processes
If wholesale elimination isn’t practical, then substituting potentially harmful chemicals for alternatives that are less toxic or irritant is the next best option. Be aware that some substitutions may introduce new chemical hazards, and must be risk assessed accordingly.
Step three: Engineering changes
If a workplace can’t feasibly eliminate OR substitute a risk of harmful chemical exposure, then reducing threat through designed changes to the physical and mechanical procedures undertaken in completion of a task should be the next goal. Steps such as improving mechanical extraction, ventilation or disposal methods might be included in possible engineering changes.
Step four: Administrative changes can also be sought to improve hazard management – improved shift and rota systems reduce exposure, provide better supervision or improve training and guidelines publication are all examples of effective administrative changes.
Step five: PPE. Personal Protective Equipment (PPE) includes any items of clothing or worn accessories designed to protect users against potential hazards from chemical spill or exposure.
Although often covered by legal requirements in many work environments, PPE should be thought of as a last line of defence – it’s used to help guard staff against risks that can’t otherwise be eliminated, substituted, engineered or administrated to improve the way a workplace functions or lower the risk of the substances it handles.
In many specific environments, responsible and legal provision of appropriate PPE equipment is defined by law, but in all cases it should also be subject to a PPE risk assessment carried out by management in conjunction with employees.
As well as highlighting areas for improvement in provision, a comprehensive PPE risk assessment should help establish:- better protocols for understanding limitations
- repair and replacement cycles
- wearer training
- ongoing monitoring of proper PPE equipment use
Typical PPE supplied in workplaces involving exposure to chemical hazards will include eyewear, gloves, respirators and coveralls, depending on the types and toxicity values of substances present. Full training should always be provided in the correct use of any PPE supplied, as well as clear guidelines on how to safely dispose of single-use items, or clean and reuse non-disposable ones.
SOPs
Different chemicals each have their own unique set of risk and hazards associated with them, often dictated by their DTL values.
Each must be handled appropriately, but in a work environment that regularly handles a wide range of substance types, too many different rules and regulations for each separate chemical can overcomplicate things.
In the worst-case scenario, this can actually increase the overall risk of accidental exposure or mishandling. As a simplified alternative, it’s worth examining the full range of chemical stock used in a workplace to see if it’s possible to draw up a more wide-scope Standard Operating Procedure (SOP).
A typical SOP is a range of core regulations that always apply across an entire group of substances, regardless of the specific chemical being handled. SOPs of this sort tend to address general issues such as:- Correct use of PPE
- Responsible handling techniques
- Communications protocols
- Emergency procedures
- Proper disposal techniques
Once the SOP guidelines have been boiled down to their simplest and most catch-all format, they’ll be much easier for entire teams to learn and act on.
For any specific chemical hazards that require additional unique protocols, smaller signs or warnings can be placed in suitable locations around the work area.
SOPs
Good, safe chemical storage should always begin with taking a comprehensive inventory:
- Create an accurate and easy-to-reference checklist of all hazardous substances being kept on the premises or in the immediate work area
- Make sure the inventory is accessible for relevant staff to consult and amend as necessary
- Check regularly that the inventory and labelling is being kept up-to-date by all users
- Review the inventory annually; use this as an opportunity to rotate and refresh stock, and to carefully dispose of old, spoiled or unused reserves
In many workplaces, fines can be incurred by businesses who are unable to present an accurate and current COSHH inventory to certain regulatory bodies, or to emergency service responders in the event of an accident.
In addition to a vigilant stock-monitoring plan, the three key steps to safe chemical storage are:
1) Making sure that all potentially hazardous substances are kept in suitable containers and conditions- All container caps and lids should be kept tightly closed at all times when not actively dispensing or topping up
- Never leave pipettes, funnels or other items of equipment in the container
- Provide drip trays for liquid chemicals in storage (check material compatibility), and provide secondary containers for all liquid chemicals in volumes above one gallon
- Use approved containers for flammable solvents
- Limit the amount of hazardous substances kept in storage to the bare minimum required
- Ensure that use-by dates are clearly marked and adhered to
- Periodically inspect all stored chemicals – look for signs of:
- Leaking
- Container damage, either physical or corrosion
- Colour changes or darkening
- Caking or crystallisation
- Pressure build-up
- Unclear or missing labels
- Ensure that all chemical storage areas, rooms and cupboards are clearly and accurately marked
- Keep storage areas well lit, but avoid direct exposure to heat or sunlight – ensure there is good ventilation with consistent and cool temperatures
- Remove all potential sources of ignition from the immediate vicinity
- Frequently check on the availability and condition of emergency equipment, wash stations and fire extinguishers
- Quickly deal with and remove any leaks or spills
- Keep doorways, aisles, walkways and work surfaces in chemical storage areas free from clutter
- Regularly check shelving and drip tray setups to maintain stability, levelness and integrity
- Use approved corrosive storage cabinets for acids and bases
- Use approved flammable storage cabinets for solvents and other combustible chemicals
- Minimise the overhead storage of hazardous substances as far as possible, and never store chemicals protruding over shelf edges
- Volumes of over one gallon should be stored a maximum of two feet from the ground
- Keep corrosive substances below non-corrosive ones
- Ensure refrigerators and freezers used for chemical storage are very clearly marked and regularly defrosted to prevent ice build-up
- Chemicals (whether solids, liquids or gases) should always be stored and segregated in accordance with their chemical family or hazard classification, the most types being:
- flammables/combustibles
- corrosive acids
- corrosive bases
- Toxics
- highly toxics
- oxidisers
- compressed gases
- Cryogens
- Pyrophorics
- water reactives
- explosives
- Separate each chemical family/hazard classification with an approved non-combustible partition or cabinet, or by a distance of at least 20 feet
- Always keep acids and bases separate
- Keep most organic acids away from oxidising mineral acids
- Keep corrosives away from any potentially reactive substances
Be aware that many chemicals will belong to more than one family or hazard class – in such cases, observe ALL storage rules for any class that substance fits into, even if it means creating an entirely new storage area for a relatively small volume of chemicals.
Remain mindful of the four basic types of potential chemical harm:- Flammability
- Health damage/toxicity
- Reactivity or instability
- Volatile incompatibility
Be aware of the differences between segregation and separation, and when each is an appropriate safety measure.
General workplace housekeeping
- Keeping floors clean and dry, and promptly removing all forms of chemical spillage, will help prevent slip and fall injuries, as well as keeping potential exposure time to a minimum
- The provision of spill trays or absorbent mats, pads and wiper materials in spill-prone locations is key in enabling staff to clean up spills quickly
- Placing suitable receptacles for used wiping and absorbency materials near spill-prone sites also helps to minimise exposure times in the event of an accident
- Continually cleaning and decluttering work surfaces throughout the day reduces the risk of unintended spills and volatile reactions between substances that weren’t intended to be mixed
- All excess, stored or packaged chemicals should be suitably located away from busy worktops or high traffic areas, giving staff the room to perform their duties comfortably and reduce risk of spillage
- Stockrooms and storage spaces should be well-organised and clearly labelled, with volatile substances suitably segregated – having one person always in charge of stockroom organisation and inventory levels can be helpful in achieving this
- Clear guidelines and schedules should be established for all forms of chemical waste disposal, and maintained through regular checks
- Training must be provided for all relevant staff in the appropriate disposal methods for any types of chemical they’ll be working with
PROTECTIVE MEASURES AND PLANNING
HAZCOM and spill response
In the event of an accident or incident involving potentially hazardous chemical exposure, all employees should be trained to:- Enact the established Hazard Communication (HazCom) programme for the facility or premises – this will be a written and published protocol for the workplace, including clear guidelines, chemical inventories and appropriate emergency response procedures to be followed by all staff
- Locate the nearest eyewash and emergency shower stations, even in scenarios where vision is impaired – these should be available within 10 seconds of unobstructed travel from anywhere that hazardous substances are being handled
- Keep pathways between work areas and emergency wash stations clear and uncluttered at all times
- Properly use appropriate clean-up and rinsing facilities for their intended purposes only
- Operate cleaning facilities effectively in a range of circumstances – most such safety equipment is designed for simple hands-free operation with either paddles, levers, or a pull-switch
- Perform basic first aid and spill-response actions, including proper removal and disposal of exposed clothing or PPE
- Be aware of electrical hazards, and keep any mains-powered equipment or machinery well away from emergency washing stations
- Use emergency washing stations and other safety facilities for their intended purpose only
- Quickly follow protocol for clean-up around washing areas that do not have drains installed after the immediate hazard has been dealt with
Training
While all workplace environments involving potential chemical exposure will face their own unique challenges and requirements, there are a number of basic general principles that all staff at risk of hazardous exposure should be fully trained and conversant in.
These include:- How to locate and follow the workplace chemical hygiene plan and other instructional or educational literature
- Where PPE is stored, how it is selected, proper use and fitting of each piece, how to clean or dispose of it, and how to identify potential limitations, faults or maintenance requirements
- The potential hazards posed by each chemical and process used in the immediate environment
- How to handle chemicals appropriately to minimise the risk of exposure
- How to label containers properly, and how to interpret labels, symbols and other warnings
- Basic health and safety hygiene and behaviour guidelines for safe and appropriate use of the workplace
- How to handle and dispose of waste materials
Links to specific training courses, guidelines and e-learning modules for workplace chemical handling can be found in the resources section below
PPE
Personal Protective Equipment (PPE) supply and monitoring is crucial in any chemical environment:- Although equipping staff with all necessary clothing and tools for physical protection is a legal requirement in most workplaces, it’s important for employers to remember that this is always a last line of defence
- It is not a substitute for optimal practice and procedure elsewhere, and does not transfer full responsibility for safety management to the wearer
- Supply of PPE can also be significantly more expensive in the long-run than other engineered or administrative safety measures, as items will need to be repaired and replaced on a regular basis
- Any PPE supplied must be suitable for both the task and the wearer to be effective, and always paired with ongoing education and monitoring regarding its proper use
LINKS, RESOURCES AND FURTHER INFORMATION
CLP quiz for identification of hazardous chemical symbols
http://www.echa.europa.eu/chemicals-in-our-life/clp-pictograms
PDF guide to recent changes in EU chemical Classification, Labelling and Packaging Regulation (CLP)
http://ec.europa.eu/social/main.jsp?catId=738&langId=en&pubId=7639
Guide to chemical waste compatibility
https://blink.ucsd.edu/safety/research-lab/chemical/storage/compatibility.html
Guide to Safety Data Sheets (SDSs) from REACH website
http://www.hse.gov.uk/reach/resources/reachsds.pdf
HSE guide to Biocide use, exposure and disposal
http://www.hse.gov.uk/biocides/index.htm
ROSPA training for COSHH
https://www.rospa.com/safety-training/work/ra/coshh-training/
HSL training schedule 2017-18
https://www.hsl.gov.uk/training.aspx
Holchem training modules (including e-learning)
https://www.holchem.co.uk/training/on-site-training/safe-working-with-chemicals/
Chemstore training
https://www.chemstore.co.uk/services/chemical-awareness-spill-response-training/
HSE example risk assessments
http://www.hse.gov.uk/coshh/riskassess/index.htm
Chemical segregation tables and suggested storage time limits
http://www.ehso.com/ChemicalStorageGuidelines.htm