- Published 21 Nov 2023
- Last Modified 30 Nov 2023
- 8 min
A Guide to Emergency Shutdown Procedures
Site safety isn’t complete without thoroughly thinking through emergency shutdown procedures for the event of a fire, flood, or accident. Read our guide to find out about the importance of emergency procedures and how to implement a great emergency response plan.
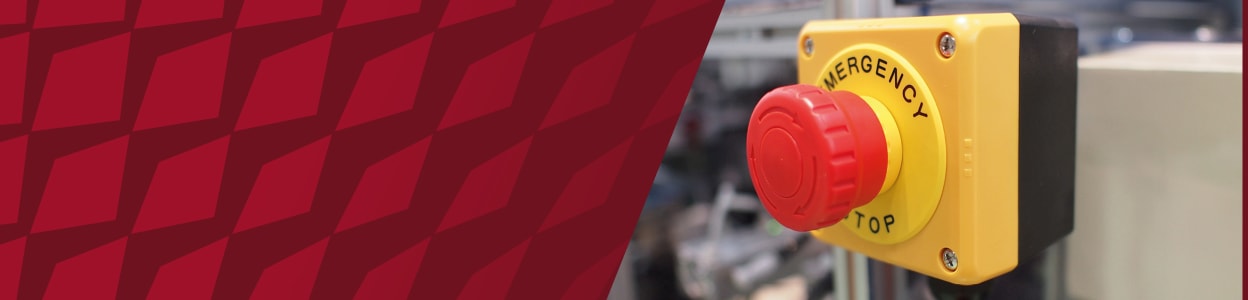
Reviewed by Peter Kendall, Technical Support Engineer (November 2023)
All workplaces must plan for what to do in the event of an emergency, and that includes manufacturing businesses. Emergencies might include fire, flooding, electrocution or other injury. Special emergency procedures should be in place in the event of injury to workers.
Are there explosion or chemical spill hazards at your plant? You should have emergency shutdown procedures in place to deal with these types of events.
This guide explains what emergency shutdown procedures are and how to implement them. But let’s start by taking a quick look at why emergency procedures are needed.
Why do you Need Emergency Procedures in the Workplace?
Every employer has a legal duty to protect its workforce. In the UK, this legal obligation falls under the Health and Safety at Work Act, which says employers are responsible for guaranteeing the safety of employees while they are working. Companies must protect the 'health, safety, and welfare' at work of not only all their employees but also casual workers, visitors, clients, and the general public.
The Management of Health and Safety at Work Regulations 1999 add that an employer must identify risks that employees, contractors, and members of the public may face and take steps to control or mitigate those risks through a formal risk assessment process.
This means workplaces must have a plan for dealing with emergencies. The Health and Safety Executive (HSE), which enforces the Health and Safety at Work Act, says companies must also plan for emergencies that present risks to the larger public, such as spills or explosions.
What are the Required Emergency Procedures?
In an emergency, there should be an emergency response plan of action that is understood by everyone involved. Drafting an emergency response plan is essential if an emergency could require rescuing an employee, present risks to the public, or require contacting and coordinating the emergency services.
Effective emergency procedures should take into account a number of crucial factors. Employees that understand and are trained in the emergency procedures are much more likely to be able to cope in a real-life emergency situation.
As the HSE mandates, your procedures must consider:
-
Plans for emergency shutdown or isolation of the plant, machinery, or processes. Shut-off valves and electrical isolators should be clearly marked.
-
Does your site have 25 tonnes or more of dangerous substances on the premises? If so, you must notify the fire and rescue service and establish appropriate warning signs.
-
Have you planned and done risk assessments for emergency scenarios? You should consider the types of emergency that might unfold and how the alarm will be sounded. It’s also important to take into account employment patterns such as night, shift, and weekend working in planning for emergencies.
-
If there is an emergency, there should be a clear plan for contacting the emergency services such as fire and rescue. You can help the emergency services by drawing a plan of hazardous substances on site.
-
Do you have enough emergency exits? They should be clearly marked and free of obstructions. There should be adequate lighting in the event of an emergency.
-
Have you considered who is in control in an emergency situation? That person or persons should have the skills and knowledge about health and safety requirements to deal with an unexpected event.
- Are there other specialists, such as first-aiders, needed during an emergency? Have they been trained? What about employees who are able to provide technical information if necessary?
- Everyone on site must be trained in emergency procedures. This includes workers with disabilities or other vulnerabilities.
- Remember that it’s vital people don’t go back to work if the situation is still dangerous. If you are in doubt, consult the emergency services.
Fire Emergency Procedures
Fire evacuation procedures should be as clear as possible. Employees should be trained in the evacuation protocol. They should remain calm in the event of fire, and raise the alarm at the nearest alarm point immediately and by shouting ‘fire’. They should be trained not to open a door that has smoke coming from underneath it. The fire evacuation plan should contain details of an assembly point area where employees and any visitors or contractors on the site evacuate to. They should comply with all instructions from the fire warden in the event of a fire.
The fire warden must contact the fire brigade and begin the evacuation plan when the alarm has been sounded. The warden should send employees and any visitors to the fire assembly point. They should take a roll call of all people in the building. If anyone is missing, they should inform an officer from the fire brigade. The fire warden must also make sure no one returns to the building until the fire brigade says it is safe to do so.
Machine Emergency Procedures
In an emergency such as someone being injured by machinery, or a machine emitting smoke, it is necessary to shut it down immediately. Machinery should be equipped with at least one emergency shutdown system – an off switch or stop button, which is depressed by the employee. It may also be necessary to isolate the piece of equipment by switching off the electric power supply to the machine.
Worker Emergency Procedures
Workers should understand the importance of emergency procedures in the workplace. They should begin with raising the alarm about the emergency and informing everyone on site, including contractors, members of the public, and vulnerable people. If there is a fire, there should be employees who have been trained in how to use fire extinguishers and how to evacuate the building to the fire assembly point. There should also be a member of the team whose responsibility it is to contact the emergency services such as fire and ambulance. Trained first-aiders should be on site in the event of an injury to a worker.
What to Consider When Setting Up Emergency Shutdown Procedures
Manufacturing plants and other industrial facilities need protocols for emergency shutdown. In the event of an emergency, these procedures should be rapid, feature redundancy and failsafe mechanisms, and have clear channels of communication. Employees should have been drilled in the procedures so they can handle the emergency situation correctly.
Different Shutdown Levels
Levels and types of emergency shutdown will vary depending on the severity of the incident and the type of facility. For a manufacturing plant, an emergency shutdown (ESD) plan hierarchy might be as follows:
- Level 0 (most severe) – abandon plant
- Level 1 – shutdown overall plant
- Level 2 – shutdown section of plant
- Level 3 – shutdown single production line
- Level 4 – shutdown single machine or piece of equipment
Types of Emergency
Types of emergency range from a smoking piece of equipment to natural disasters. Severe weather is having more and more of an impact globally due to climate change. This heightens the risk of flooding. Technological breakdown may cause a fire, or hazardous materials might result in a chemical spill or an explosion. Whatever the scenario, it is important to have an emergency response plan and properly trained employees. You must ensure that they understand the importance of emergency procedures in the workplace.
Machine-Specific Procedures
Specific pieces of machinery may require specific plans in the event of an emergency. For example, if the worst happens and a worker is trapped in a piece of machinery, it’s important to know how you would go about freeing them. You would need to know if it were possible to do that with the power off in the event of an emergency shutdown, or if specialist skills or tools are needed. It’s important to plan for these scenarios so that you know what procedure to follow in the event of an accident.
Required Safety Equipment
On site safety equipment should include fire extinguishers, fire alarms, smoke detectors, fire blankets, first aid kits, emergency lighting in the event of a power failure, and clear signage showing evacuation routes and emergency exits.
How to Implement Your Emergency Shutdown Procedures
Implementing emergency shutdown procedures should be planned carefully with potential risks to the facility and your employees considered in full. That means a risk assessment is vital for preparing a comprehensive emergency response plan. The risk assessment should take into account every possible scenario and develop shutdown procedures for each one.
It should be clear among employees who has responsibility for each action in the event of an emergency. For example, in the event of a fire there should be a trained fire warden responsible for evacuating staff to the assembly point and taking a roll call of workers and visitors to the plant. Your emergency evacuation procedures should be drilled into employees so that they are 100% clear on what to do in the event of an emergency.
Follow all the steps above, and you can be confident your plant is prepared when something unexpected happens. Preventing workplace hazards requires careful planning. Get it right, and you can enjoy the peace of mind of knowing you’ve done everything possible to be ready.
Read our guide to find out how RS can help you with equipment to ensure workplace site safety.